Equipment Calibration Isn't a Chore, It's Your Competitive Edge: The Strategic Guide for 2025
Jul 16, 2025
equipment calibration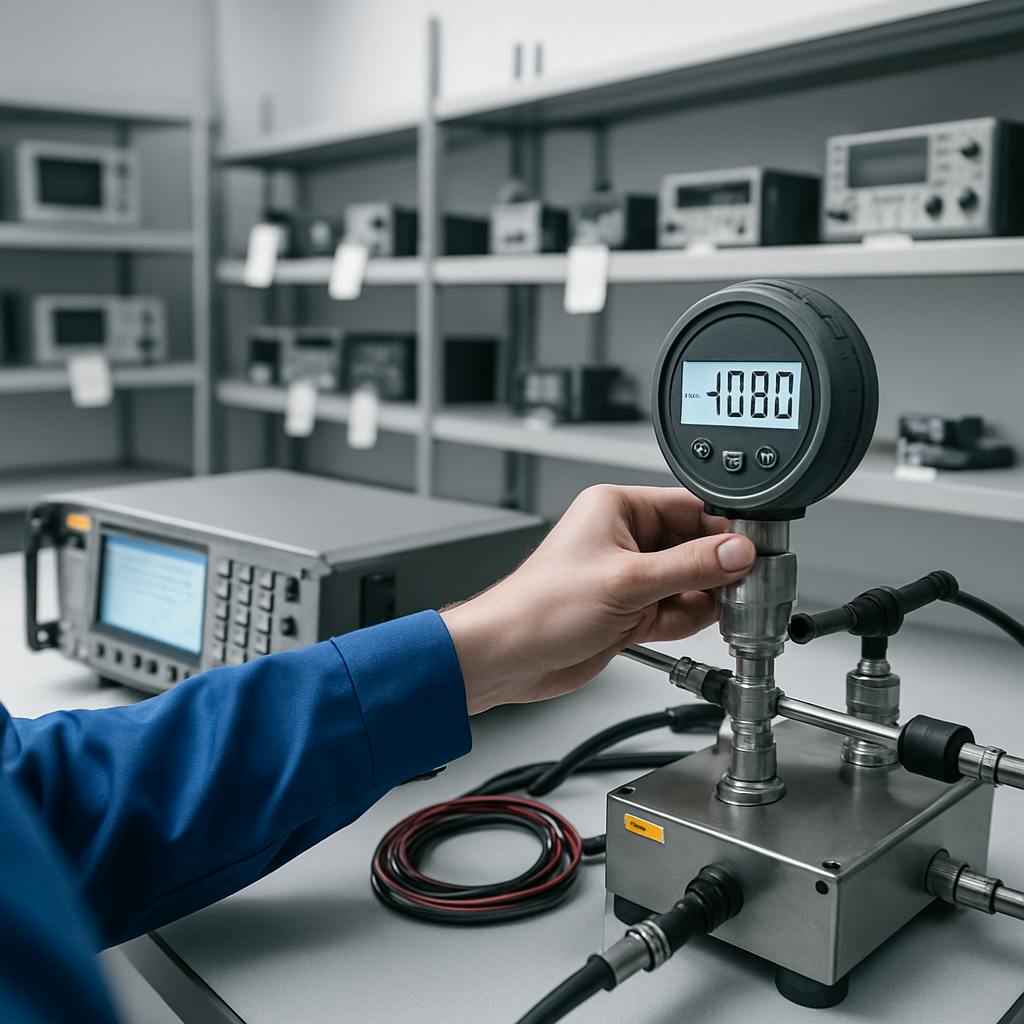
A single, out-of-tolerance pressure gauge on a reactor vessel. A barely-off temperature sensor in a curing oven. A miscalibrated torque wrench on a critical assembly line. To the untrained eye, these are minor discrepancies. To a maintenance manager, a quality engineer, or a plant operator in 2025, they are the silent signals of impending disaster. They represent scrapped product, failed audits, catastrophic safety events, and a direct hit to the bottom line.
For too long, equipment calibration has been relegated to a compliance-driven, check-the-box activity—a necessary evil performed in a dusty corner of the plant. But in today's hyper-competitive, data-driven industrial landscape, this mindset is not just outdated; it's dangerous.
A world-class calibration program is no longer a cost center. It is a strategic pillar of operational excellence, a driver of efficiency, and a powerful risk mitigation tool. It’s the foundation upon which quality control, process stability, and advanced maintenance strategies are built.
This guide moves beyond the simple "what is calibration?" We're providing a strategic playbook for maintenance managers and operational leaders. We will dissect the core components of a robust program, explore advanced strategies for optimization, and show you how to transform calibration from a reactive chore into a proactive, value-adding function.
Beyond the Basics: Why "Good Enough" Calibration Is a Ticking Time Bomb
The fundamental purpose of calibration is simple: to ensure an instrument's measurement is accurate relative to a known, verifiable standard. It's the process of comparing the reading of a device under test (DUT) with a measurement standard of known accuracy. If a deviation (or error) is found, the instrument is adjusted back into its acceptable tolerance range.
But understanding the "what" is only the first step. The real imperative lies in understanding the "why." The consequences of neglecting or poorly managing calibration ripple through every facet of an organization.
The True Cost of Inaccurate Measurements
The sticker price of a calibration service is trivial compared to the hidden—and often astronomical—costs of relying on inaccurate data.
-
Product Quality, Scrap, and Rework: This is the most immediate and visible cost. Imagine a CNC machine where a miscalibrated position sensor leads to parts being milled 0.5mm out of spec. An entire production run could be rendered useless, resulting in thousands or even millions of dollars in scrap material and wasted machine time. In the pharmaceutical or food and beverage industry, a miscalibrated pH meter or temperature sensor could ruin a multi-million dollar batch, leading to massive financial loss and product shortages.
-
Safety and Compliance Risks: This is where the stakes become life-and-death. A pressure relief valve on a boiler is set to release at 150 PSI. But what if the pressure gauge used to test and set it reads 5% low? The valve won't open until the actual pressure is nearly 158 PSI, potentially exceeding the vessel's safety limits. The result could be a catastrophic failure. On the compliance side, a failed audit due to inadequate calibration records can lead to hefty fines, forced shutdowns, and loss of critical certifications like ISO 9001 or AS9100.
-
Operational Inefficiency and Energy Waste: Inaccurate sensors feed bad data into your control systems, causing them to make poor decisions. A temperature sensor in an HVAC system that reads 2 degrees high will cause the chiller to run constantly, wasting enormous amounts of energy. A flow meter that reads low might cause a pump to work harder than necessary, leading to premature wear and increased power consumption. Maintenance teams end up chasing phantom problems, replacing perfectly good components because a faulty sensor told them something was wrong. This is the definition of inefficient, reactive maintenance.
-
Erosion of Trust and Reputation: If your out-of-spec products reach the customer, the damage extends beyond a single return. It erodes customer confidence, damages your brand's reputation for quality, and can lead to long-term loss of business. In a world of instant communication, a single major quality escape can become a public relations nightmare.
The Core Pillars of a World-Class Calibration Program
Building a program that avoids these pitfalls requires a structured approach built on four unshakeable pillars. Neglecting any one of them compromises the entire structure.
Pillar 1: Establishing Unshakeable Traceability (The NIST Connection)
Traceability is the cornerstone of all valid measurements. It is an "unbroken chain of comparisons" that links your instrument on the factory floor all the way back to a recognized national or international standard.
In the United States, the ultimate authority for these standards is the National Institute of Standards and Technology (NIST). NIST maintains the primary physical standards for the country (e.g., the standard kilogram, the atomic clock for time).
Here's how the chain of traceability works:
- NIST (Primary Standard): Holds the definitive standard with the lowest possible measurement uncertainty.
- Accredited Calibration Lab (Secondary Standard): This lab sends its primary standards to be calibrated directly against NIST's standards. These become the lab's reference standards.
- Your In-House Lab or Vendor (Working Standard): Your company's internal standards (or the standards used by your calibration vendor) are calibrated against the accredited lab's secondary standards.
- Your Instrument (Device Under Test): Your torque wrench, pressure gauge, or multimeter is calibrated using your company's working standard.
By documenting each of these steps, you create an unbroken, auditable trail proving your measurement is "NIST Traceable." When you receive a calibration certificate, it must identify the standards used to perform the calibration and confirm their own traceability. Without this, the certificate is just a piece of paper.
Pillar 2: Mastering Calibration Standards & Procedures
A traceable standard is useless without a rigorous, repeatable process for using it. This is where Standard Operating Procedures (SOPs) for calibration come in. A well-defined SOP ensures that every calibration is performed the same way, every time, regardless of which technician is doing the work.
How to Develop a Robust Instrument Calibration Procedure:
A comprehensive SOP, which can be managed and deployed through modern PM procedures software, should include the following elements at a minimum:
- Scope and Identification: Clearly define which instrument(s) the procedure applies to. Include make, model, and a unique asset ID for every device managed under your asset management program.
- Required Standards and Equipment: List the specific working standard(s) to be used (e.g., "Fluke 87V Multimeter, S/N XXXXX"). Also, list any other required equipment like test leads, pressure hoses, or environmental monitors.
- Measurement Parameters and Tolerances: State exactly what is being measured (e.g., DC Voltage, Pressure, Temperature) and define the acceptable tolerance (e.g., "±0.5% of reading," "±2°C"). This is the pass/fail criterion.
- Environmental Conditions: Specify the required environmental conditions for the calibration to be valid (e.g., "Temperature: 20°C ± 2°C," "Humidity: 40% RH ± 10%").
- Preliminary Steps: Include safety checks, cleaning the instrument, and allowing it to stabilize in the required environment.
- Step-by-Step Calibration Process: This is the core of the SOP. It should be unambiguous. For a typical 5-point calibration, it would look like this:
- Connect the standard and the DUT.
- Apply a known value at 0% of the instrument's range. Record the standard's value and the DUT's "As Found" reading.
- Repeat for 25%, 50%, 75%, and 100% of the range.
- Compare the "As Found" readings to the tolerance. If any point is out of tolerance, the instrument has failed.
- If adjustment is possible, perform the adjustment according to the manufacturer's instructions.
- Repeat the 5-point check and record the "As Left" data to verify the instrument is now within tolerance.
- Data Recording Requirements: Specify exactly what data must be recorded on the calibration record or certificate. This includes "As Found," "As Left," technician name, date, standard used, etc.
Pillar 3: Demystifying Measurement Uncertainty
Many people confuse error and uncertainty.
- Error is the difference between the instrument's reading and the true value. It's a single value we can often correct through adjustment.
- Uncertainty is the "doubt" that exists about the result of any measurement. It's a range within which the true value is believed to lie. Every measurement has uncertainty, even the measurement made by the NIST primary standard.
Think of it this way: You measure a block with a caliper and it reads 25.4 mm. The error might be +0.02 mm (it should be 25.38 mm). The uncertainty might be ±0.05 mm. This means you can only say with confidence that the true value is somewhere between 25.33 mm and 25.43 mm.
Why does it matter? A calibration is meaningless without a statement of uncertainty. The uncertainty of your measurement process must be significantly smaller than the tolerance of the device you are testing. A common rule of thumb is to have a Test Uncertainty Ratio (TUR) of at least 4:1. This means the uncertainty of your calibration process is at least four times smaller than the tolerance of the DUT.
Sources of uncertainty are numerous and include:
- The uncertainty of the reference standard itself.
- Environmental factors (temperature, humidity, vibration).
- The skill and technique of the operator (e.g., parallax error in reading an analog gauge).
- The instrument being tested (repeatability, resolution).
- The physical setup (cables, connectors, hoses).
A proper calibration process identifies all these sources and quantifies them to calculate a total "uncertainty budget."
Pillar 4: Complying with ISO 9001 and Other Regulatory Frameworks
For many organizations, calibration is a mandate driven by quality management systems like ISO 9001. Clause 7.1.5, "Monitoring and measuring resources," is the key section. It doesn't tell you how to calibrate, but it tells you what your system must achieve.
Key ISO 9001 Calibration Requirements:
- Suitability: You must determine and provide the right tools for the job.
- Maintenance: The resources must be maintained to ensure their continued fitness for purpose.
- Traceability: When traceability is a requirement (it almost always is), your equipment must be:
- Calibrated or verified at specified intervals against standards traceable to national or international standards.
- Identified with a unique ID to determine its status.
- Safeguarded from adjustments, damage, or deterioration that would invalidate its calibration status.
- Corrective Action: You must determine if previous results were adversely affected when an instrument is found to be out of tolerance, and take appropriate action. This is a critical and often-overlooked requirement.
Other industries have even more stringent requirements, such as AS9100 in aerospace or FDA 21 CFR in pharmaceuticals, which add layers for software validation and data integrity.
Strategic Decision-Making: In-House vs. Outsourced Calibration
One of the biggest strategic decisions a maintenance manager faces is whether to build an in-house calibration capability or to outsource it to a third-party lab. The answer is rarely all or nothing.
The Case for an In-House Calibration Lab
Performing calibrations internally can be a powerful option if the circumstances are right.
- Pros:
- Control & Speed: No shipping delays. Critical instruments can be calibrated and returned to service in hours, not days or weeks.
- Cost (at scale): For a high volume of common instruments (e.g., pressure gauges, calipers, multimeters), the cost per calibration can be significantly lower than outsourcing.
- Builds Expertise: Develops valuable metrology skills within your own team.
- Cons:
- High Initial Investment: The cost of primary standards, a climate-controlled environment, and training is substantial.
- Ongoing Costs: Standards must be periodically sent out for their own recalibration, which is expensive.
- Limited Scope: It's often impractical to have the in-house capability to calibrate every type of instrument you own.
- Accreditation Burden: Achieving and maintaining an ISO/IEC 17025 accreditation (the gold standard for calibration labs) is a massive undertaking.
When it makes sense: An in-house lab is ideal for companies with a large number of the same type of instruments, where turnaround time is a major operational factor, and for performing less-critical, routine verification checks.
The Case for Outsourcing to an Accredited Lab
Partnering with a professional, ISO/IEC 17025 accredited calibration lab is the most common approach.
- Pros:
- Guaranteed Traceability & Expertise: Accredited labs are rigorously audited to ensure their technical competence and traceability. You're buying peace of mind.
- Access to High-End Equipment: They have the equipment and expertise to calibrate a vast range of specialized instruments that you could never justify buying.
- Reduced Burden: No internal management of standards, environments, or technician training.
- Third-Party Validation: An accredited certificate carries more weight during an audit.
- Cons:
- Cost: The price per calibration is typically higher.
- Lead Time: Logistics and shipping can take an instrument out of service for a week or more.
- Less Control: You are dependent on the vendor's schedule and processes.
When it makes sense: Outsourcing is the best choice for your own primary/reference standards, highly complex or unique instruments, any measurement critical to safety or quality, and for satisfying strict customer or regulatory compliance requirements.
The Hybrid Model: The Best of Both Worlds
For most organizations, the optimal solution is a hybrid model. Use a risk-based approach:
- In-House: Calibrate your high-volume, low-criticality, general-purpose instruments like pressure gauges, tape measures, and basic electrical testers.
- Outsourced: Send your master standards, load cells, temperature probes for certified ovens, CMMs, and any other high-precision or compliance-critical instruments to an accredited external lab.
This strategy balances cost, control, and compliance, giving you the most efficient and effective program.
The Art and Science of Setting Calibration Intervals
"How often should we calibrate this?" is a question that plagues every maintenance department. The answer "follow the manufacturer's recommendation" is a safe starting point, but it's often inefficient. Manufacturers tend to be conservative, leading to over-calibration and unnecessary spending. A data-driven approach is far superior.
Initial Interval Determination
When you acquire a new instrument, start with a baseline interval derived from:
- Manufacturer's Recommendation: The default starting point.
- Industry Standards: Some industries have standard practices for certain instrument types.
- Criticality Assessment: How critical is this measurement? A sensor controlling a critical process needs a shorter interval than a gauge on a non-critical water line.
Advanced Methods for Optimizing Intervals
Once an instrument has been through a few calibration cycles, you can use its own history to optimize its interval.
- "As-Found" Data Analysis: This is the simplest and most powerful method. Systematically review your calibration records.
- If an instrument is consistently found to be well within its tolerance limits every time it's calibrated, you have strong evidence that the interval can be safely extended (e.g., from 6 months to 9 months).
- If an instrument is frequently found to be out of tolerance, the interval is too long and must be shortened immediately.
- Control Charting (SPC): For highly critical instruments, you can plot the "As-Left" reading from each calibration on a control chart. Over time, this will show you the instrument's drift rate, allowing you to predict when it will go out of tolerance and set the interval just before that point.
- Reliability-Based Calibration: This advanced technique, championed by resources like Reliabilityweb, analyzes the performance of a group of identical instruments in the same service. By analyzing the historical data, you can determine the optimal calibration interval for that entire class of assets, moving from an instrument-by-instrument approach to a fleet-management approach. This type of data-driven optimization is a core principle of modern maintenance, paving the way for advanced strategies like AI-powered predictive maintenance. A robust equipment maintenance software is essential for collecting and analyzing the data needed for this approach.
Leveraging Technology: The Rise of Calibration Management Software
In 2025, managing a serious calibration program with spreadsheets is like navigating a modern city with a hand-drawn map. It's slow, prone to human error, lacks visibility, and is an auditor's nightmare.
Modern CMMS software with integrated calibration management modules has become an essential tool.
Key Features of a Modern Calibration Management System
- Centralized Instrument Database: A single source of truth for every piece of test equipment, including its ID, location, status, and full calibration history.
- Automated Scheduling and Alerts: Automatically generates work orders for upcoming calibrations and sends notifications to managers and technicians, eliminating missed deadlines.
- Digital Records and Certificates: Stores all calibration certificates and records electronically, making them instantly accessible for audits or investigations.
- Full Audit Trail: Creates an unchangeable log of all activities, including who performed the calibration, when it was done, and what the results were, ensuring data integrity for compliance with standards like ISO 9001.
- Management of Standards: Tracks the calibration status of your own internal working standards, alerting you when they need to be sent out for recalibration.
- Data Analysis and Reporting: Provides tools to analyze "As-Found/As-Left" data, track instrument drift, and generate the reports needed to optimize calibration intervals.
- Mobile Access: Allows technicians to access procedures and record results directly from a tablet or phone in the field, improving accuracy and efficiency.
The ROI of implementing such a system is clear: dramatically reduced audit preparation time, elimination of compliance risks from missed calibrations, improved technician productivity, and data-driven insights that lead to direct cost savings.
Practical Guide: How to Decode a Calibration Certificate
The calibration certificate is the final product of the calibration process. Knowing how to read it and spot red flags is a critical skill.
What to Look For: The Non-Negotiables
A valid, trustworthy certificate from an accredited lab will always contain:
- Clear Identification: The lab's name and address, and the logo of their accreditation body (e.g., A2LA, NVLAP).
- Unique Certificate Number: For tracking and reference.
- Device Under Test (DUT) Info: Unambiguous identification of your instrument (Model, Serial Number, your Asset ID).
- Dates: Date of calibration and often the next calibration due date.
- Standards Used: A list of the specific reference standards used to perform the test, including their serial numbers and the expiration date of their own calibration. This is how you verify traceability.
- Environmental Conditions: The temperature and humidity at the time of calibration.
- "As Found" and "As Left" Data: This is the most critical part. "As Found" data tells you the condition of the instrument when it arrived at the lab. "As Left" data shows its condition after adjustment. Without "As Found" data, you have no idea if your processes were at risk before the calibration.
- Statement of Measurement Uncertainty: A declaration of the uncertainty associated with the measurements made by the lab. Without this, you cannot properly assess the quality of the calibration.
- Technician and Approval: The name or signature of the technician who performed the work and the quality approver.
Red Flags on a Calibration Certificate
Be wary of certificates that:
- Are missing "As Found" data. This is a major red flag.
- Lack a statement of uncertainty. This suggests the lab may not be following proper metrology principles.
- Simply state "Pass" or "Fail" without providing the actual measurement data.
- List standards that are expired or not traceable.
- Show "As Left" data that is right at the very edge of the tolerance limit. This instrument may drift out of tolerance very quickly.
Conclusion: Calibration as a Strategic Imperative
Equipment calibration is the bedrock of a data-driven, reliable, and safe operation. By moving past the "check-the-box" mentality and embracing a strategic approach, you transform a perceived cost into a powerful competitive advantage.
A world-class program for 2025 is built on a holistic understanding of its core pillars: unshakeable NIST traceability, robust procedures, a firm grasp of measurement uncertainty, and strict adherence to quality standards like ISO 9001. It involves making strategic choices about in-house versus outsourced resources and using historical data to scientifically optimize calibration intervals.
Ultimately, this foundation of accurate and reliable measurement data is what enables higher-level maintenance and reliability strategies. You cannot achieve true predictive maintenance if the sensors feeding data to your algorithms are not trustworthy. You cannot ensure quality, protect your assets, or guarantee a safe workplace without a rigorous, well-managed equipment calibration program. It’s time to give it the strategic focus it deserves.
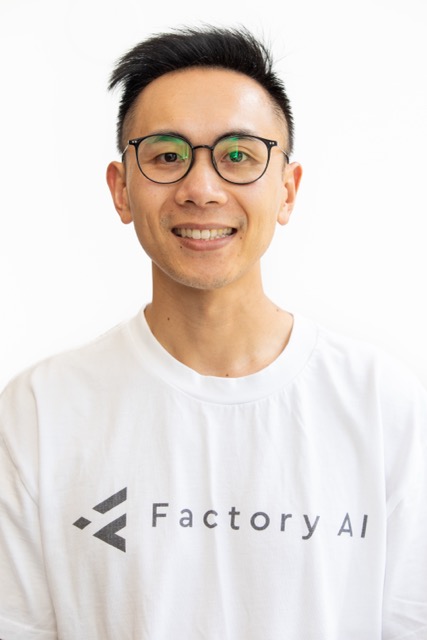