The Ultimate Guide to Writing a Maintenance Technician Job Description That Attracts Top Talent in 2025
Jul 16, 2025
maintenance technician job description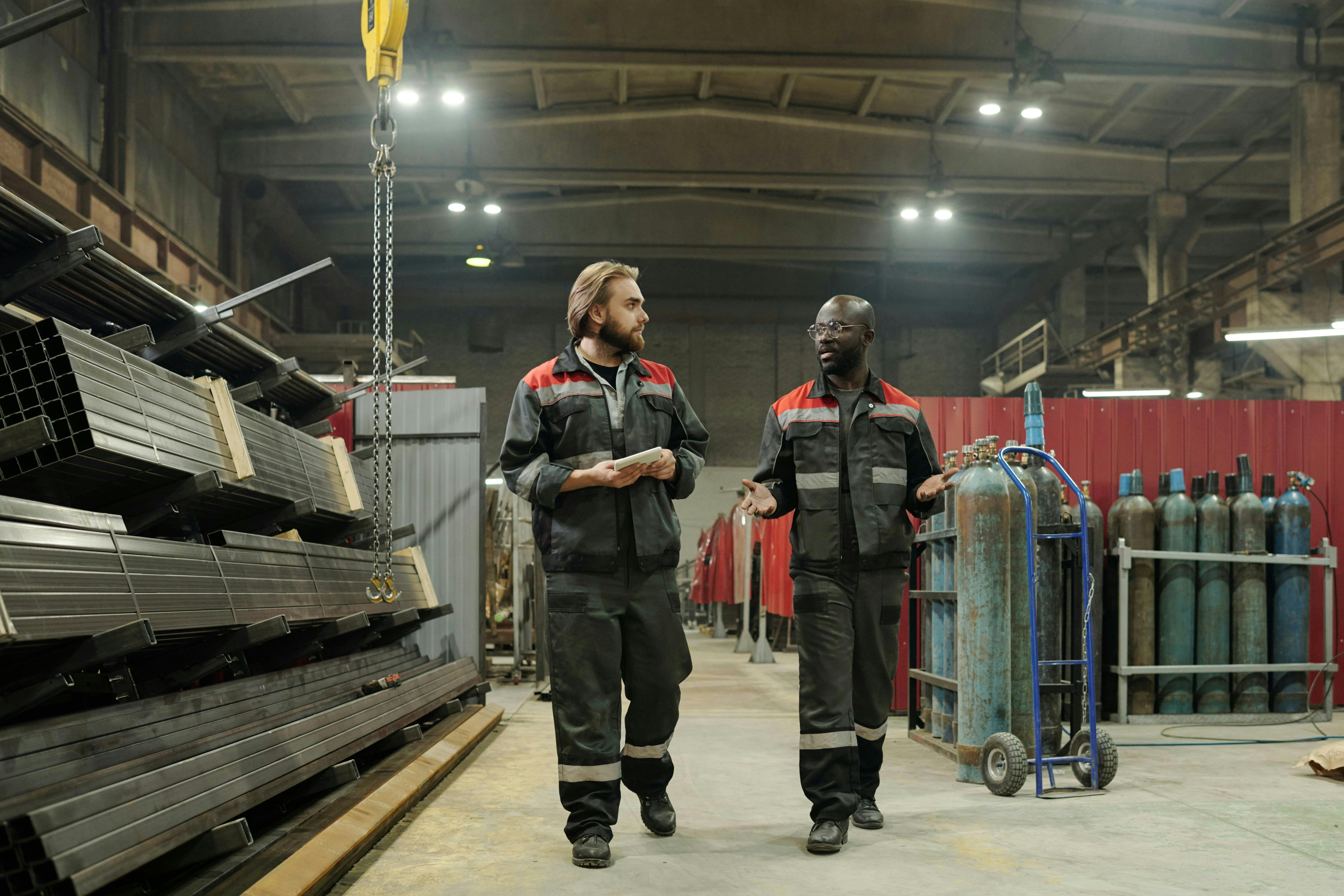
The hum of a well-oiled machine is the sound of profitability. The sudden silence that follows a breakdown is the sound of cascading costs, missed deadlines, and mounting pressure. In today's hyper-competitive industrial landscape, the line between these two realities is often drawn by a single, critical role: the Maintenance Technician.
Yet, for such a pivotal position, most job descriptions are tragically flawed. They are generic, uninspired, and rooted in a reactive maintenance mindset from a bygone era. They use vague phrases like "troubleshoot and repair equipment" and end up attracting "parts changers" instead of the proactive, data-driven "reliability champions" your facility needs to thrive in 2025 and beyond.
This isn't just another template to copy and paste. This is a strategic guide for hiring managers, operations leaders, and HR professionals. We will deconstruct the anatomy of a high-impact job description, showing you how to articulate your needs, showcase your opportunities, and attract the skilled technicians who will become the backbone of your operational excellence. It's time to stop fishing with a bare hook and start crafting the precise lure that catches the best talent in the sea.
Why Your Generic Maintenance Technician Job Description is Failing You
If your applicant pool for maintenance roles feels shallow, or if new hires aren't meeting expectations, the problem often starts with the job description itself. A generic description acts as a poor filter, letting through unqualified applicants while repelling the high-performers you desperately need. Let's diagnose the common failure points.
The Vague "Troubleshoot and Repair" Trap
Almost every maintenance job description contains the phrase "troubleshoot and repair mechanical and electrical systems." While technically true, it's strategically useless. It tells a potential candidate nothing about the complexity, the technology, or the real challenges of the role.
- A low-skilled technician reads this and thinks: "Great, I can turn a wrench and use a multimeter. I'm qualified."
- A high-skilled technician reads this and thinks: "This company doesn't know what they need. Are they dealing with 1980s conveyors or 2025 automated robotic cells? I'm not wasting my time applying to find out."
This vagueness leads to a flood of applications from individuals who can handle basic reactive tasks but lack the deeper diagnostic and analytical skills required for modern industrial environments.
Ignoring the Monumental Skills Gap
The role of a maintenance technician has evolved more in the last decade than in the previous fifty. The purely mechanical "grease monkey" is a relic. The modern technician is a hybrid professional who must be as comfortable with a tablet and diagnostic software as they are with a socket set.
Your job description fails when it doesn't reflect this new reality. It must bridge the gap between:
- Traditional Skills: Hydraulics, pneumatics, welding, fabrication, pipefitting.
- Modern Skills: PLC troubleshooting (Allen-Bradley, Siemens), VFD configuration, HMI navigation, sensor technology (vibration, thermal, ultrasonic), and critically, CMMS data entry and analysis.
A job description that only lists the traditional skills signals that your facility is technologically stagnant, scaring away ambitious technicians who want to grow their skills.
The Hidden Costs of a Mismatched Hire
Hiring the wrong technician isn't just an inconvenience; it's a significant financial drain. The consequences include:
- Increased Downtime: A technician who can only replace a failed motor but can't diagnose the root cause (e.g., voltage imbalance, bearing misalignment) guarantees the failure will repeat.
- Safety Incidents: An improperly trained or unskilled technician is a safety liability. A failure to follow LOTO procedures or correctly wire a 480V panel can have catastrophic consequences.
- Wasted MRO Inventory: "Parts changers" throw new components at a problem until it goes away, burning through expensive inventory. A skilled technician diagnoses correctly the first time.
- Damaged Team Morale: When one team member can't pull their weight, the burden falls on your high-performers, leading to burnout and turnover among your best people.
Failing to "Sell" the Role and the Company
In 2025, skilled maintenance technicians are in high demand. They have options. Your job description is not just a list of requirements; it's a marketing document. It's your first—and perhaps only—chance to convince a top-tier candidate that your company is the right place for them.
A boring, list-based description that doesn't mention company culture, training opportunities, career paths, or the quality of the work environment will be passed over for one that does. You need to sell the "why" behind the "what."
The Foundation: Defining the Role Before You Write a Single Word
Before you open a document, you must perform a strategic analysis of the role itself. A great job description is born from a deep understanding of your facility's unique needs.
Step 1: Conduct a Maintenance Needs Analysis
Ask yourself and your team these critical questions. Be brutally honest with the answers.
-
Where are you on the Maintenance Maturity Curve?
- Reactive: "We fix things when they break." Your JD should focus on strong, rapid diagnostic and repair skills across a wide range of failures.
- Preventive: "We follow a schedule to service equipment and prevent failures." Your JD must emphasize discipline, attention to detail, and experience with PM procedures and scheduling.
- Predictive/Prescriptive: "We use data and technology to predict failures before they happen." Your JD needs to attract a data-savvy technician, comfortable with sensor technology and software analysis. You should explicitly mention your goal of using technology like a predictive maintenance platform to move beyond reactive work.
-
What is your specific asset and technology stack?
- Equipment: Don't just say "production equipment." List the core systems. Is it CNC machines, robotic welding cells, high-speed packaging lines, industrial boilers, or complex HVAC systems?
- Technology: What specific PLCs (e.g., Siemens S7-1200, Allen-Bradley ControlLogix) do you use? What about your CMMS? SCADA system? Are you using any condition monitoring sensors?
-
What are your biggest maintenance pain points right now?
- Is it excessive electrical downtime? Unplanned mechanical failures on a specific asset line? Poor PM compliance? The answer to this question should directly influence the "must-have" skills in your job description.
Step 2: Differentiating Between Maintenance Roles
"Maintenance Technician" is a broad term. Be specific to attract the right expertise.
- Maintenance Technician: Often a generalist role, especially in smaller facilities. They handle a mix of mechanical, electrical, and facility-related tasks.
- Industrial Maintenance Technician/Mechanic: A more specialized role focused on production machinery. This implies a stronger emphasis on PLCs, motor controls, hydraulics, and pneumatics.
- Facilities Maintenance Technician: Focuses on the building and its supporting infrastructure: HVAC, plumbing, lighting, electrical distribution, and general building upkeep.
- Reliability Technician: A more advanced role focused on condition monitoring, root cause analysis (RCA), and using data to improve asset strategies. This role is less about "wrench time" and more about analysis.
Step 3: Defining Tiers and Career Paths
Top talent doesn't want a dead-end job. Show them a future. By defining tiers, you can attract candidates at various skill levels and demonstrate a commitment to internal growth.
- Maintenance Technician I (Entry-Level): Focus on assisting senior techs, performing basic PMs, learning systems, and demonstrating a strong work ethic and mechanical aptitude.
- Maintenance Technician II (Mid-Level): Expected to work independently on moderately complex troubleshooting and repairs, execute all standard PMs, and demonstrate proficiency with the CMMS.
- Maintenance Technician III / Lead Technician (Senior-Level): Can tackle the most complex failures, leads troubleshooting efforts, mentors junior technicians, may assist with planning/scheduling, and is an expert in key systems like PLCs or robotics.
Mentioning this career ladder directly in the job description is a powerful magnet for ambitious individuals.
Anatomy of a High-Impact Maintenance Technician Job Description
Now, let's build the job description section by section, transforming it from a bland list into a compelling recruitment tool.
The Job Title: Be Specific and Strategic
Generic titles get generic results. Infuse your title with keywords that signal the specific skills you need.
- Instead of: Maintenance Technician
- Try: Industrial Maintenance Technician (PLC & Robotics)
- Instead of: Maintenance Mechanic
- Try: 2nd Shift Maintenance Technician (Food & Beverage Manufacturing)
- Instead of: Facilities Technician
- Try: HVAC & Building Maintenance Technician
This simple change helps your job posting stand out and pre-qualifies candidates before they even click.
The Job Summary: Your 30-Second Elevator Pitch
This is your hook. It should be a 3-5 sentence paragraph that sells the mission, the impact, and the environment.
Generic (Bad) Example:
[Company Name] is seeking a Maintenance Technician to perform maintenance and repairs on our equipment. The ideal candidate will be responsible for troubleshooting issues and completing work orders.
Strategic (Good) Example:
Join the team at [Company Name] as a key player in our state-of-the-art [Type of] facility. We're looking for a skilled Industrial Maintenance Technician who is passionate about solving complex problems and ensuring the reliability of our advanced automated systems. In this role, you won't just be fixing machines; you'll be a vital part of our operations team, using your expertise in [Key Skill 1, e.g., PLC troubleshooting] and [Key Skill 2, e.g., hydraulics] to minimize downtime and drive continuous improvement. If you thrive in a fast-paced environment and want to work with a company that invests in technology and its people, we want to hear from you.
Core Responsibilities and Duties: From Vague to Action-Oriented
This is the heart of the job description. Ditch the passive, boring bullet points. Use a "Verb + Task + Purpose" framework to create a dynamic picture of the daily job. Organize responsibilities into logical categories.
Preventive & Predictive Maintenance
- Bad: - Perform PMs
- Good: - Execute detailed preventive maintenance tasks on CNC milling centers, hydraulic presses, and robotic welders according to the schedule in our CMMS software to achieve a 98% PM completion rate.
- Good: - Conduct weekly condition monitoring rounds using thermal imaging and vibration analysis tools to collect asset health data.
- Good: - Analyze data from our predictive maintenance sensors to identify and address potential equipment failures before they cause downtime, contributing to our proactive reliability strategy.
Troubleshooting & Repair
- Bad: - Troubleshoot and repair equipment.
- Good: - Diagnose and resolve complex electro-mechanical failures on high-speed packaging lines, utilizing PLC ladder logic (Allen-Bradley) and electrical schematics to pinpoint root causes.
- Good: - Repair and rebuild critical mechanical components, including gearboxes, pumps, and pneumatic cylinders, ensuring adherence to manufacturer specifications.
- Good: - Respond to urgent equipment breakdowns with a focus on safe, efficient, and sustainable repairs that prevent recurrence.
Documentation & Continuous Improvement
- Bad: - Fill out paperwork.
- Good: - Meticulously document all work performed, parts used, and failure analysis details within our mobile CMMS to ensure data integrity for reliability reporting.
- Good: - Participate in Root Cause Analysis (RCA) teams to investigate significant downtime events and help develop corrective actions.
- Good: - Identify and suggest improvements to PM procedures, equipment design, or operational practices to enhance overall equipment effectiveness (OEE).
Safety & Compliance
- Bad: - Follow safety rules.
- Good: - Champion a culture of safety by rigorously adhering to all LOTO (Lockout/Tagout), Arc Flash, and other OSHA-mandated safety protocols without exception.
- Good: - Maintain a clean, organized, and safe work area, including the maintenance shop and any on-floor project sites.
Required Skills and Qualifications: The "Must-Haves"
This section is your primary filter. Be explicit and unambiguous.
-
Education/Experience:
- High School Diploma or GED required.
- Minimum of [X] years of experience as an Industrial Maintenance Technician in a [Your Industry, e.g., manufacturing, distribution] environment.
- Associate's Degree or technical certificate in Industrial Maintenance, Mechatronics, or a related field is a plus.
-
Technical Skills (Be Specific!):
- Mechanical: Strong proficiency in troubleshooting and repairing hydraulic and pneumatic systems. Experience with precision alignment, welding (MIG/TIG), and mechanical fabrication.
- Electrical: Proven ability to troubleshoot electrical systems up to 480V/3-phase. Expertise in reading electrical schematics, diagnosing motor control circuits, and configuring VFDs.
- Automation: Must have experience troubleshooting PLC-controlled equipment. Direct experience with [Your PLC Brand, e.g., Allen-Bradley ControlLogix/CompactLogix] is required.
-
Soft Skills:
- Exceptional problem-solving and analytical skills.
- Strong communication skills and the ability to work effectively within a team.
- A proactive, self-starter attitude with a focus on continuous learning.
Preferred Qualifications: The "Nice-to-Haves"
This is where you describe your ideal, "purple squirrel" candidate. These are not deal-breakers but will make an applicant stand out.
- Experience with robotic systems (FANUC, KUKA, etc.).
- Certification such as CMRP (Certified Maintenance & Reliability Professional) or CRL (Certified Reliability Leader). You can learn more about these valuable credentials from industry leaders like Reliabilityweb.
- Experience with advanced condition monitoring techniques (vibration analysis, oil analysis, motor circuit analysis).
- Proficiency with a specific work order software or enterprise asset management system.
- Experience in a highly regulated environment (e.g., GMP, FDA).
Compensation, Benefits, and Perks: Sell the Opportunity
Don't make this an afterthought. Top candidates expect transparency and want to know what's in it for them.
- Compensation: Be transparent. Provide a competitive hourly wage range (e.g., "$35.00 - $45.00 per hour, depending on experience and skill level"). Mention shift differentials or overtime potential.
- Benefits: List your core benefits (Medical, Dental, Vision, 401(k) with company match).
- Perks (The Differentiators): This is your chance to shine.
- Annual tool allowance of $[X].
- Generous paid time off (PTO) and holiday schedule.
- Company-provided uniforms and PPE.
- A dedicated budget for ongoing training and professional development.
- Opportunities for career advancement on a defined technical ladder.
- A modern, clean, and climate-controlled work environment.
The Technology Imperative: Integrating Modern Tools into Your JD
To build a maintenance team for 2025, your job description must speak the language of modern technology. It must attract the "digital technician" who understands that data is as important as a physical tool.
Beyond the Wrench: The Rise of the "Digital" Technician
The modern technician doesn't just fix the asset; they interact with its digital twin. They use tablets and smartphones on the floor to access work orders, schematics, and asset histories. They are responsible for feeding high-quality data back into the system. Your JD should reflect this.
- Example Phrase: "Must be proficient with mobile technology (tablets, smartphones) and comfortable utilizing a mobile CMMS to manage work orders and document findings directly at the asset."
Writing for a CMMS-Driven Workflow
A CMMS is the central nervous system of a modern maintenance department. Your JD should show that you use it strategically, not just as a digital filing cabinet.
- Instead of: "Complete work orders."
- Try: "Manage and execute all assigned work orders—from creation to completion—within our CMMS, ensuring all labor hours, parts, and failure codes are accurately recorded to support our reliability analysis efforts."
Attracting Talent for a Predictive Maintenance (PdM) Program
If you are investing in PdM, you need technicians who are excited by it, not intimidated. Your JD is the perfect place to signal this forward-thinking approach.
- Mention specific PdM tasks: "Responsible for collecting and interpreting data from our condition monitoring program, including vibration analysis on critical motors and thermal imaging scans of electrical panels."
- Highlight the use of AI: "Collaborate with the reliability team to validate and act upon alerts generated by our AI predictive maintenance system, transitioning the team from reactive repairs to proactive interventions."
- Connect to broader trends: This shift towards data-driven manufacturing is a core component of modern industrial strategy, often discussed by organizations like the National Institute of Standards and Technology (NIST) in their frameworks for Smart Manufacturing. Mentioning your alignment with these principles can attract forward-thinking candidates.
Putting It All Together: A Complete, Strategic Job Description Template
Use this template as a starting point. Fill in the bracketed information with your facility's specific details.
Job Title: [Specific Title, e.g., Industrial Maintenance Technician (PLC & Automation)] Location: [City, State] Shift: [e.g., 1st Shift, Monday-Friday, 7:00 AM - 3:30 PM] Compensation: [e.g., $35.00 - $45.00 per hour, based on experience]
Job Summary:
Join the innovative team at [Company Name] as a key player in our state-of-the-art [Type of] facility. We're looking for a skilled [Job Title] who is passionate about solving complex problems and ensuring the reliability of our advanced [e.g., automated packaging lines]. In this role, you won't just be fixing machines; you'll be a vital part of our operations team, using your expertise in PLC troubleshooting and electro-mechanical systems to minimize downtime and drive our proactive maintenance strategy. If you thrive in a collaborative environment and want to work with a company that invests in cutting-edge technology and its people, we encourage you to apply.
Core Responsibilities:
- Troubleshooting & Repair:
- Diagnose and resolve complex mechanical and electrical failures on critical production assets, including [Specific Equipment 1], [Specific Equipment 2], and [Specific Equipment 3].
- Utilize PLC diagnostic tools (Allen-Bradley/Siemens) to troubleshoot machine control logic and resolve automation faults.
- Safely troubleshoot and repair electrical systems up to 480V, including motor controls, VFDs, and safety circuits.
- Repair and rebuild critical mechanical systems, including hydraulics, pneumatics, gearboxes, and conveyors.
- Preventive & Predictive Maintenance:
- Execute detailed preventive maintenance tasks according to the schedule in our CMMS to achieve a 98% PM completion rate.
- Conduct condition monitoring rounds using thermal imaging and vibration analysis tools to collect asset health data for our predictive maintenance program.
- Analyze data and alerts to identify and address potential equipment failures before they cause downtime.
- Documentation & Continuous Improvement:
- Meticulously document all work performed, parts used, and failure analysis notes within our mobile CMMS to ensure data integrity for reliability reporting.
- Participate in Root Cause Analysis (RCA) teams to investigate significant downtime events.
- Identify and suggest improvements to PM procedures, equipment design, or operational practices to enhance Overall Equipment Effectiveness (OEE).
- Safety & Compliance:
- Champion a culture of safety by rigorously adhering to all LOTO, Arc Flash, and other OSHA-mandated safety protocols without exception.
- Maintain a clean, organized, and safe work area at all times.
Required Qualifications:
- High School Diploma or GED.
- Minimum of [3-5] years of experience as an Industrial Maintenance Technician in a manufacturing environment.
- Proven expertise in troubleshooting complex electro-mechanical systems.
- Strong proficiency in reading and interpreting electrical, hydraulic, and pneumatic schematics.
- Direct experience troubleshooting PLC-controlled equipment (e.g., Allen-Bradley ControlLogix/CompactLogix).
- Proficiency with standard maintenance tools and precision instruments.
- A proactive, self-starter attitude with excellent problem-solving skills.
Preferred Qualifications:
- Associate's Degree or technical certificate in Industrial Maintenance, Mechatronics, or a related field.
- Experience with robotic systems (e.g., FANUC, KUKA).
- Experience with a modern CMMS platform.
- Welding and fabrication skills.
- CMRP or other maintenance-related certification.
Benefits & Perks:
- Competitive hourly wage and shift differential.
- Comprehensive benefits package (Medical, Dental, Vision, Life Insurance).
- 401(k) with a generous company match.
- days of Paid Time Off (PTO) plus paid holidays.
- Annual tool allowance of $[X].
- Company-provided uniforms and all necessary PPE.
- A dedicated budget for ongoing training, certifications, and professional development.
- Clear opportunities for career advancement on our technical career ladder.
Conclusion: Your Job Description is Your First Move
In the complex game of industrial operations, your maintenance team is your most valuable asset. A well-crafted job description is your opening move—a strategic action that sets the stage for victory. It's the difference between attracting a technician who simply reacts to problems and one who anticipates and prevents them.
By moving beyond generic templates and adopting a strategic approach, you articulate your needs, showcase your company's value, and appeal directly to the modern, tech-fluent professionals who will drive your facility's reliability. Empowering this top-tier talent with the right culture and the right tools, like a comprehensive proactive maintenance solution, is the ultimate key to transforming your maintenance department from a cost center into a powerful competitive advantage.
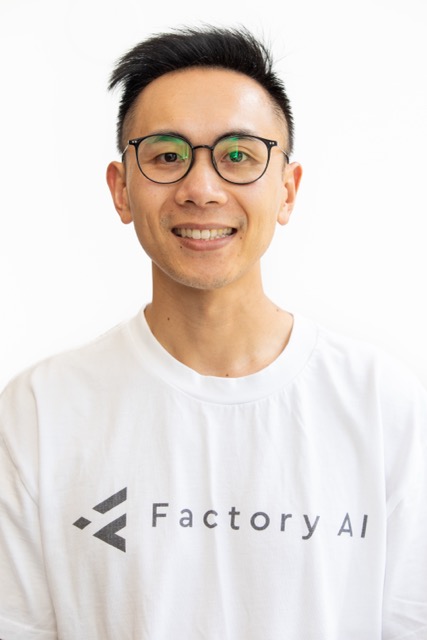