From Static Page to Strategic Asset: The 2025 Guide to Work Instructions
Jul 16, 2025
work instructions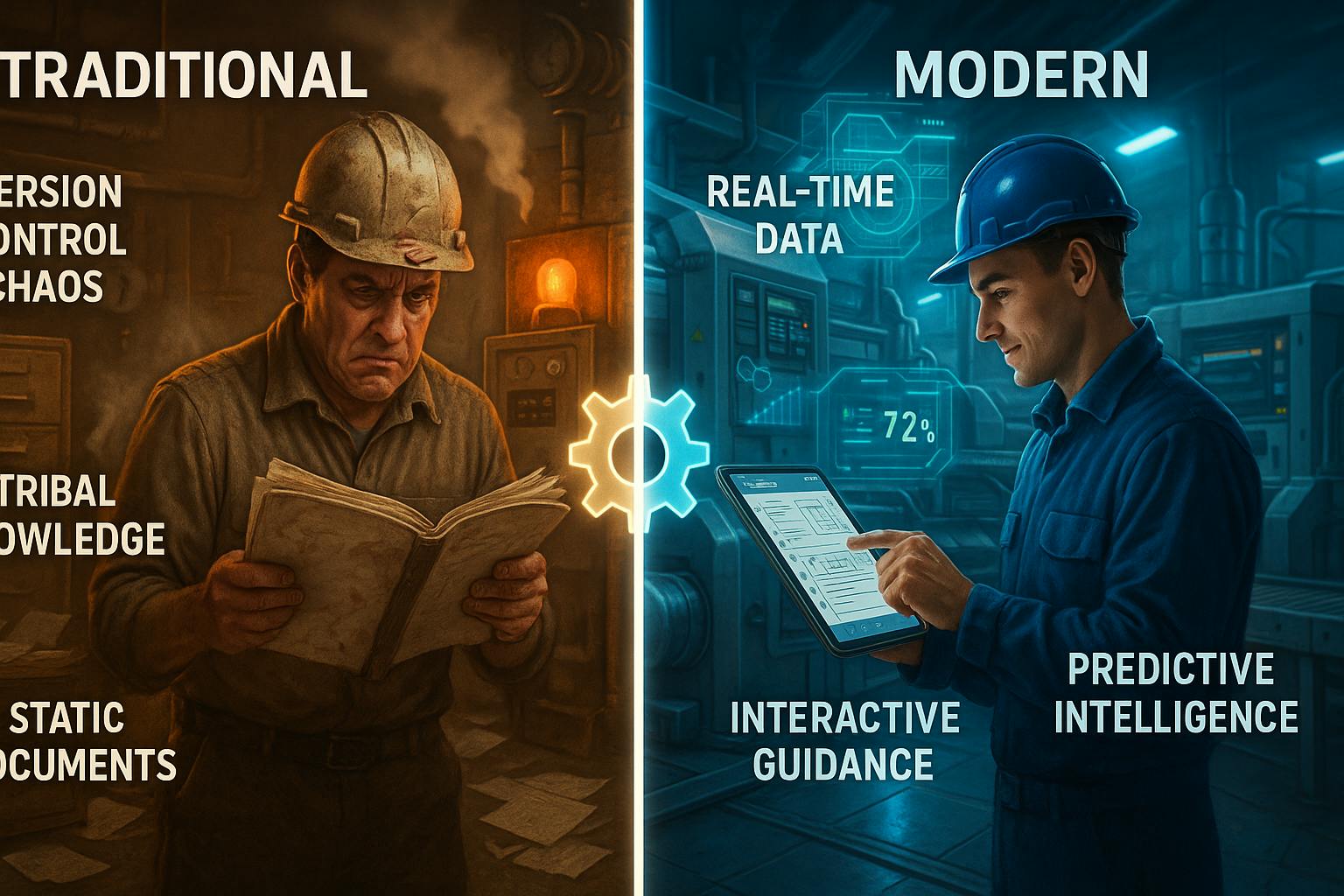
A critical production line grinds to a halt. The culprit? A failed bearing on a primary drive motor. The senior technician who knew its every quirk retired last month. A junior tech, armed with a grease-stained, laminated sheet pulled from a binder, performed the last PM. The instructions were vague—"lubricate bearing as needed"—a classic example of tribal knowledge that never made it to paper. The result is hours of unplanned downtime, lost production, and a frantic scramble to diagnose a problem that should have been prevented.
This scenario is all too common. For decades, work instructions have been treated as a necessary evil—static documents created to satisfy an audit, then filed away and forgotten. But in 2025, this mindset is not just outdated; it's a direct threat to your operational viability.
The evolution is here. Work instructions are transforming from passive documents into active, data-generating strategic assets. They are the frontline interface between your team, your equipment, and your entire maintenance strategy. This guide moves beyond the basic "how-to" and explores how to revolutionize your operations by turning your work instructions into a source of powerful, predictive intelligence.
The Foundational Flaw: Why Traditional Work Instructions Fail in Modern Industry
Before we can build the future, we must understand the failures of the past. The traditional approach to work instructions—relying on paper, static PDFs, and institutional memory—is riddled with inefficiencies and risks that modern facilities can no longer afford.
The Perils of Paper and PDFs
The three-ring binder on the shelf or the PDF buried in a shared drive is a symbol of operational drag. This static format is inherently flawed for dynamic industrial environments.
- Version Control Chaos: Is the technician using the latest procedure? A change in lubricant spec or a new safety protocol might have been issued, but the old paper copy is still in circulation. This disconnect is a direct path to equipment damage and safety incidents.
- Accessibility Issues: When a machine goes down at 3 AM, the last thing a technician needs is to hunt for a binder in a locked office or search through a confusing server directory. Instructions must be available instantly, at the point of work.
- The Tribal Knowledge Trap: The most dangerous phrase in maintenance is, "Oh, John always handled that." When John retires or leaves, his decades of experience—the subtle sounds, the specific feel of a properly tensioned belt, the non-obvious root causes—walk out the door with him. Paper instructions rarely capture this deep, nuanced expertise.
- No Feedback Loop: A technician discovers a more efficient way to perform a task or finds that a specified tool is incorrect. With a paper system, where does that feedback go? Usually, nowhere. The instruction remains flawed, and the same inefficiency is repeated by the next person.
The High Cost of Ambiguity
Vague instructions are a recipe for disaster. Phrases like "check for tightness," "listen for unusual noises," or "lubricate regularly" are subjective and unrepeatable. This ambiguity has tangible, expensive consequences.
According to research published on Reliabilityweb, human error is a contributing factor in a significant percentage of equipment failures. In maintenance, this is often rooted in unclear procedures.
Consider this real-world example: A work instruction for a gearbox PM simply says, "Top up oil."
- Technician A uses the wrong type of oil because it wasn't specified, causing premature wear on the gears.
- Technician B overfills the gearbox, causing churning, overheating, and blown seals.
- Technician C correctly identifies the right oil and fill level but doesn't note a metallic sheen in the old oil—a key indicator of impending failure—because there was no step to "Inspect drained oil for contaminants and report findings."
Each error, born from ambiguity, leads to costly unplanned downtime. The cost isn't just in parts and labor; it's in lost production, missed deadlines, and potential safety hazards.
SOP vs. Work Instruction: Clarifying the Hierarchy
To fix the problem, we must first speak the same language. The terms "Standard Operating Procedure" (SOP) and "Work Instruction" (WI) are often used interchangeably, but they represent two distinct levels of documentation. Understanding this hierarchy is the first step toward creating clarity.
Aspect | Standard Operating Procedure (SOP) | Work Instruction (WI) |
---|---|---|
Purpose | The WHAT and WHY | The HOW |
Scope | High-level, process-focused | Task-specific, detailed |
Audience | Managers, auditors, supervisors | Technicians, operators |
Content | Policies, safety regulations, process flow | Step-by-step actions, tools, specs |
Example | "Preventive Maintenance Program for HVAC Systems" | "How to Replace the Filter on Air Handler AHU-07" |
Think of it like building a house. The SOP is the blueprint—it shows the overall design, room layouts, and ensures the structure meets building codes. The Work Instruction is the detailed, step-by-step guide for the carpenter on how to frame a specific wall, including the type of lumber, nail spacing, and precise measurements. You need both, but they serve different functions. Your maintenance strategy will fail if you hand a technician a blueprint and expect them to frame a wall perfectly.
Building the Bedrock: How to Write Effective Standard Work Instructions (The Right Way)
Before you can leap to AI and augmented reality, you need a solid foundation. Creating clear, actionable, and standardized work instructions is a non-negotiable prerequisite. This is where you codify excellence and make it repeatable.
The Anatomy of a Perfect Work Instruction
A world-class work instruction is more than a checklist. It's a comprehensive guide that leaves no room for interpretation. Every effective WI should contain these core components:
- Header Information:
- Task Title: Clear and specific (e.g., "Quarterly PM for Conveyor Motor M-1138").
- Asset ID/Location: Unique identifier for the equipment.
- Estimated Duration: Sets expectations and helps with planning.
- Required Skill Level: (e.g., Electrician I, Mechanic II).
- Critical Safety Warnings: Lockout/Tagout (LOTO), arc flash, confined space, etc. This must be the first thing the user sees.
- Required Tools & Materials:
- List every single tool needed (e.g., "14mm socket wrench," "torque wrench (150 ft-lbs)," "feeler gauge").
- List all parts and consumables with specific part numbers and quantities (e.g., "2x Bearing #6204-2RS," "1 tube of Mobilgrease XHP 222"). This integrates directly with inventory management.
- Personal Protective Equipment (PPE) Checklist:
- Don't just say "standard PPE." Be explicit: "Hard hat," "ANSI Z87+ safety glasses," "cut-resistant gloves (Level A4)," "steel-toed boots."
- Step-by-Step Procedures:
- Use the Active Voice: "Torque the bolts" instead of "The bolts should be torqued."
- One Action Per Step: Keep steps simple and singular.
- Be Quantitative: Never use subjective terms.
- Bad: "Tighten the bolt."
- Good: "Using a calibrated torque wrench, tighten the six flange bolts in a star pattern to 85 ft-lbs."
- Include Verification Points: Add steps that require the technician to measure and confirm a result. "Verify belt tension is 120 Hz using a sonic tension meter."
- Visual Aids (The Power of "Show, Don't Just Tell"):
- Annotated photos showing the exact lubrication point.
- Simple diagrams illustrating a complex sequence.
- Short video clips demonstrating a specific technique.
- Completion & Sign-off:
- A final checklist to confirm all steps are complete and the area is clean.
- Fields for the technician to sign off, enter the completion date/time, and add any relevant notes.
A Step-by-Step Guide to Writing a Maintenance Work Instruction (Example: Centrifugal Pump Seal Replacement)
Let's make this practical. Here’s how you would create a robust work instruction for replacing a mechanical seal on a pump.
-
Scope the Task & Gather Information:
- Consult the OEM manual for the pump.
- Grab the specific part numbers for the mechanical seal kit and any required O-rings or gaskets.
- Bring an experienced technician who has done this job before. They are your subject matter expert (SME).
-
Perform a Job Hazard Analysis (JHA):
- Before writing a single step, analyze the risks.
- Hazard: Unexpected startup. Control: Perform LOTO on the motor breaker.
- Hazard: Chemical exposure from pumped fluid. Control: Drain and flush the pump casing; specify chemical-resistant gloves and splash goggles.
- Hazard: Musculoskeletal injury from lifting the motor. Control: Specify use of an overhead crane or a two-person lift.
-
Draft the Steps with Your SME:
- Have the technician walk you through the process, step-by-step. Document every single action.
- Initial Draft: "Remove the motor and coupling."
- Refined Draft:
- Perform LOTO on breaker P-101-B. Verify zero energy state.
- Close suction and discharge valves V-101 and V-102.
- Drain the pump casing by opening drain valve V-103.
- Disconnect the coupling guard.
- Remove the four motor mounting bolts using a 19mm wrench.
- Lift and set aside the motor using the overhead crane.
-
Incorporate Visuals:
- Take clear, well-lit photos at critical stages.
- A photo showing the correct LOTO point on the breaker.
- A close-up of the set screws on the impeller that need to be loosened.
- An annotated diagram showing the correct orientation of the new seal components. A picture here prevents a seal from being installed backward, saving a costly rework.
-
Review, Test, and Refine:
- Give the draft instruction and the parts to a technician who has never done this specific task before.
- Watch them perform the job. Where do they hesitate? What questions do they ask?
- This is your single most valuable source of feedback. Use their experience to clarify ambiguous steps, add missing information, and refine the instruction until it's foolproof.
The Digital Leap: Transitioning to Visual and Interactive Work Instructions
A perfect paper work instruction is a great start, but it's still a static artifact. The next leap in value comes from digitizing the process and making it interactive. This is where you move from simply guiding work to actively managing and learning from it.
Beyond Text: The Cognitive Power of Visual Work Instructions
The human brain is wired for visuals. The Picture Superiority Effect is a well-documented phenomenon where people remember pictures with far greater accuracy than words. In a high-stakes maintenance environment, leveraging this is not a luxury; it's a necessity for accuracy and safety.
- High-Resolution Photos: A picture of the correct dipstick marking for oil level is infinitely clearer than "fill to the correct level."
- Annotated Diagrams: Use arrows, circles, and text overlays on photos or CAD drawings to point out exact components, torque sequences, or measurement points.
- Short Video Clips: For complex or delicate actions—like seating a bearing or performing a tricky alignment—a 15-second video clip can convey more than pages of text.
- 3D Models: For highly complex equipment, allowing a technician to rotate and explode a 3D model on a tablet to see how parts fit together is a game-changer for comprehension.
By moving to a digital format on a tablet or mobile device, you can embed these rich media types directly into the workflow, ensuring the technician has the best possible information at the exact moment they need it.
Introducing Interactivity: The Game-Changer for Engagement and Data Capture
This is the critical pivot point. An interactive work instruction doesn't just present information; it demands engagement and captures data in return. This is managed best through a mobile CMMS that puts this power directly in your technicians' hands.
What makes a work instruction interactive?
- Digital Checkboxes: The technician must actively confirm the completion of each step. This creates accountability and a verifiable audit trail.
- Data Entry Fields: Instead of just "Check vibration," the instruction prompts the user to "Enter vibration reading (in/s)." This captures quantitative condition data. Other examples include entering temperature readings, pressure levels, or fluid levels.
- Photo/Video Uploads: "Take a photo of the completed repair before closing the panel." This provides visual verification of work quality and can be invaluable for troubleshooting later.
- Conditional Logic (If-Then Branching): This makes instructions dynamic.
- Step 5: "Measure bearing temperature. Is it above 180°F?"
- If NO: "Proceed to Step 6."
- If YES: "STOP. Do not proceed. Create a new work order to investigate overheating and notify the maintenance supervisor immediately."
- This simple logic prevents a technician from continuing a PM on a machine that is already exhibiting signs of failure, averting a potential catastrophe.
The shift to interactivity transforms a technician from a passive follower of instructions into an active participant in the data collection and health monitoring of an asset.
The Strategic Revolution: From Document to Data-Driven Asset
When your interactive work instructions are integrated into your core maintenance platform, they stop being mere documents. They become the primary data acquisition tool for your entire reliability program. This is where the strategic revolution happens.
Your CMMS as the Central Nervous System
Work instructions should not live in a silo. They must be an integral part of your CMMS (Computerized Maintenance Management System). This integration creates a seamless, closed-loop system for work execution and data analysis.
- Work Order Integration: When a PM is scheduled, the CMMS automatically attaches the correct, most up-to-date work instruction to the work order. No more searching, no more version confusion.
- Automated Data Logging: As the technician completes the interactive steps, all the data they enter—task duration, meter readings, parts used, notes—is automatically logged directly to the asset's history in the CMMS. The manual, error-prone process of transcribing notes from a paper form is eliminated.
- Dynamic Inventory Management: When a technician marks a step as complete that used a specific part (e.g., "Install new filter, part #AF-2556"), the CMMS can automatically deduct that part from inventory and even trigger a reorder when stock falls below a set threshold.
This integration turns every maintenance task into an opportunity to build a rich, detailed, and accurate history for every piece of equipment in your facility.
Unlocking Prescriptive Insights from Work Instruction Data
This rich data stream is the fuel for advanced analytics. This is how you move beyond reactive and even preventive maintenance into the realm of predictive and prescriptive maintenance.
The process looks like this:
- Data Capture: Hundreds of technicians complete thousands of work orders, entering quantitative data (pressures, temperatures, vibration, cycle times) as part of their standard workflow.
- Pattern Recognition: AI and machine learning algorithms within the CMMS analyze this massive dataset. The system starts to connect the dots that a human might miss.
- Predictive Alerts: The model learns that for a specific class of air compressors, a 5% increase in motor temperature, combined with a 10% increase in cycle time, is a high-confidence precursor to a valve failure within the next 15 days.
- Prescriptive Action: This is the ultimate goal. The system doesn't just send an alert saying "Failure likely." It leverages prescriptive maintenance to automatically generate a work order to prevent the failure. This work order already has the correct work instruction attached ("Air Compressor Valve Replacement"), a list of required parts, and is scheduled before the failure occurs, turning unplanned downtime into planned, efficient maintenance.
Your work instructions have now become the foundation of a system that tells you what to do, when to do it, and exactly how to do it.
Case Study in Action: A Manufacturing Plant's Conveyor Line Transformation
A large beverage bottling plant was plagued by persistent downtime on its main packaging conveyor system. Their MTTR (Mean Time to Repair) was high, and maintenance was entirely reactive.
- Before: They used laminated work instructions for basic PMs. These were rarely updated and lacked detail. Failures were frequent, especially with gearboxes and drive motors.
- The Transition: They implemented a modern equipment maintenance software platform with integrated, interactive work instructions. They invested time in creating detailed, visual WIs for all critical conveyor components.
- The "Aha!" Moment: The new work instructions prompted technicians to record vibration readings and motor amperage during every PM. This data flowed directly into the CMMS.
- The Analysis: After three months, the system's AI analyzed the data. It found a clear correlation: on the curved sections of the conveyor, motor amperage would slowly creep up for two weeks before a gearbox failure. This was an indicator of chain tension and lubrication issues that weren't obvious to the naked eye.
- The Result: The system was configured to trigger a work order for "Chain Tensioning and Lubrication" whenever motor amperage on those specific sections increased by 7% over baseline. This prescriptive work order was dispatched automatically. Unplanned gearbox failures on the conveyor line dropped by over 80% in six months. The work instruction became their most powerful diagnostic tool.
The Future is Now (2025): AI, AR, and the Connected Technician
The strategic use of data from work instructions is the current state-of-the-art. But technology continues to advance, further empowering the frontline technician and optimizing the entire maintenance workflow.
AI-Generated Work Instructions: The End of Manual Authoring?
Creating the detailed work instructions described above takes time and expertise. This is where Artificial Intelligence is becoming a powerful assistant.
Instead of starting with a blank page, a manager can prompt an AI model: "Create a preventive maintenance work instruction for a 'Goulds 3196' pump, focusing on a quarterly schedule." The AI-powered system can then:
- Scan and interpret the OEM's 200-page PDF manual.
- Analyze all historical work orders for that pump model in the CMMS.
- Incorporate safety standards and best practices.
The AI then generates a comprehensive draft work instruction, complete with steps, recommended tools, and safety warnings. A human expert still needs to review, refine, and add visuals, but this AI-assisted authoring can reduce the creation time from hours to minutes, allowing for rapid deployment of best-practice procedures across an entire facility.
Augmented Reality (AR): Overlaying Digital Information onto the Real World
Augmented Reality takes visual instructions to their logical conclusion. A technician wearing AR smart glasses (like a Microsoft HoloLens or RealWear device) can look at a piece of equipment and see the work instruction overlaid directly onto their field of view.
- Hands-Free Operation: The technician no longer needs to look down at a tablet or paper. Both hands are free to perform the work, improving safety and efficiency.
- Spatial Guidance: A glowing green arrow can point to the exact bolt that needs to be tightened. A 3D animation can play in space, showing how a component should be removed.
- Remote Expert Assistance: If the technician gets stuck, they can initiate a video call. A remote expert, sitting in an office hundreds of miles away, can see exactly what the technician sees and can draw annotations in their field of view, guiding them through the complex step in real-time.
Building a Culture of Continuous Improvement
Technology is the enabler, but culture is the driver. The most advanced system in the world will fail if the people using it aren't engaged. The final, and perhaps most important, piece of the puzzle is creating a culture of continuous improvement, or Kaizen.
Digital work instruction platforms should be designed to foster this. Every work instruction should have a simple "Suggest an Improvement" button. When a technician is on the floor and finds a better way, a wrong torque spec, or a missing tool, they can instantly submit that feedback.
This feedback shouldn't go into a black hole. It should create a notification for the maintenance planner or engineer to review. Once approved, the master work instruction is updated, and that improvement is instantly propagated to every technician for the next time the job is performed. This virtuous cycle, as detailed by methodologies like those on iSixSigma, is what separates good maintenance teams from great ones. It empowers your technicians, respects their expertise, and ensures your procedures are living documents that get better with every single use.
Conclusion: Your Instructions, Your Intelligence
We've journeyed from the dusty, forgotten binder to a future of AI-driven, augmented reality-guided tasks. The central theme is undeniable: in 2025, your work instructions are one of the most valuable assets in your entire operation.
They are no longer a cost center for documentation. They are a profit center for operational intelligence.
By treating them as such—by building a solid foundation of clear, standardized procedures, by embracing digital and interactive formats, and by integrating them into the data ecosystem of your CMMS—you can unlock unprecedented gains in efficiency, safety, and reliability. You can move from reacting to failures to predicting and preventing them.
Stop just documenting work. Start leveraging it. The time is now to transform your static pages into strategic assets and discover the intelligence hidden within your daily tasks.
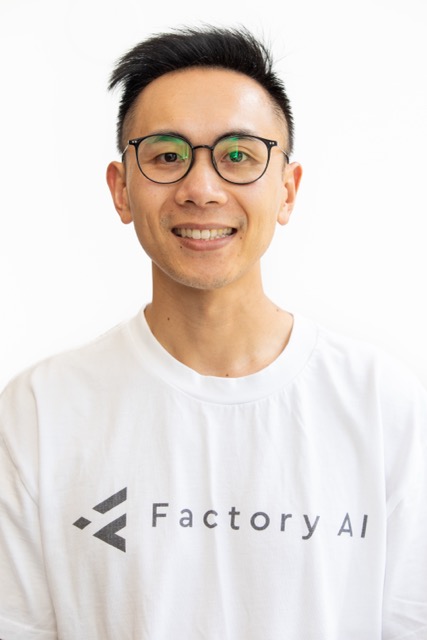