From Cost Center to Profit Engine: The Definitive 2025 Guide to Oil and Gas Asset Management
Jul 16, 2025
oil and gas asset management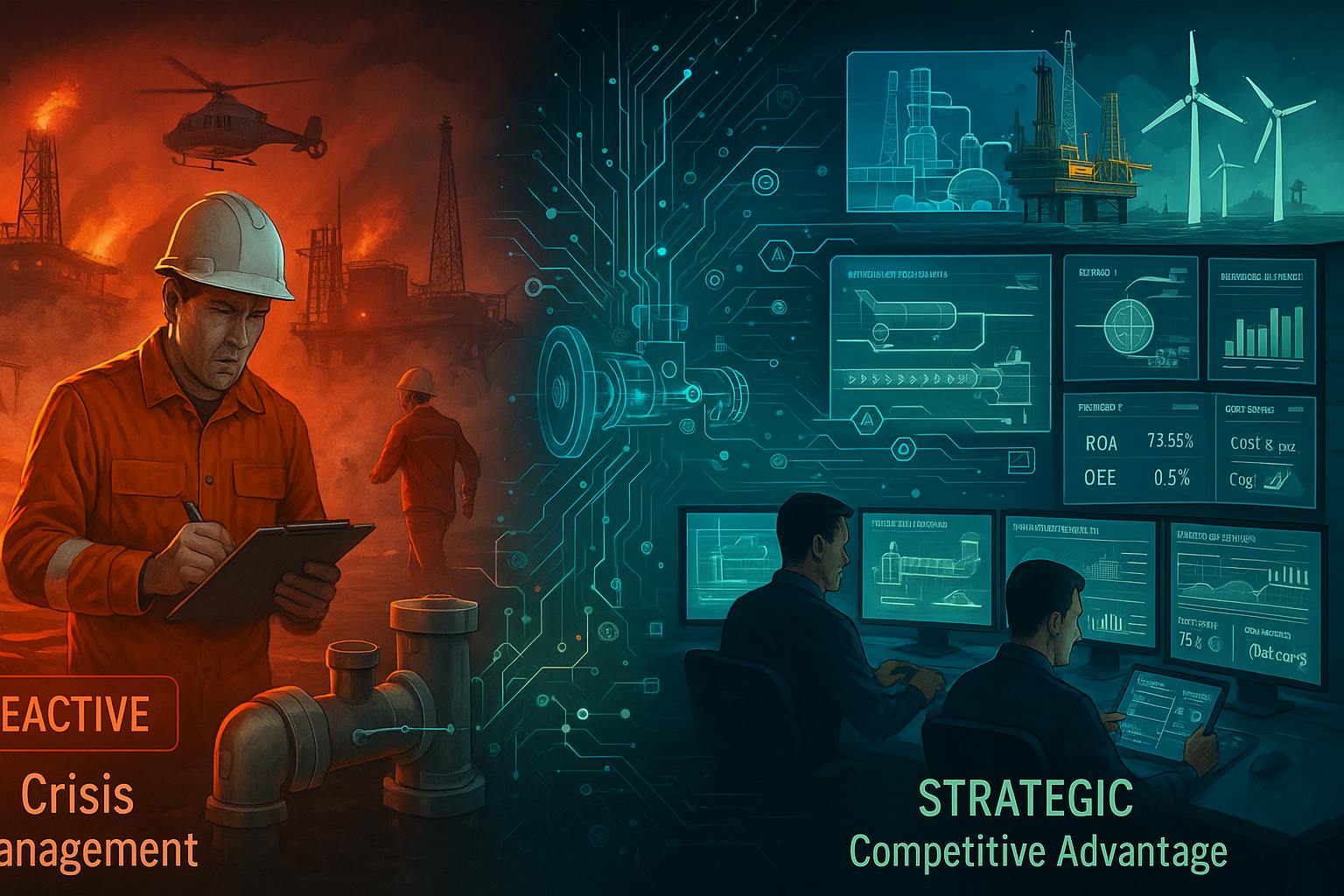
An alarm blares on an offshore platform in the North Sea. It’s not a fire; it’s a catastrophic failure of an electric submersible pump (ESP) deep below the waves. Production halts instantly. The cost isn't just the multi-million dollar replacement of the pump; it's the tens of millions in lost production, the logistical nightmare of an emergency workover, and the near-miss on a serious safety incident.
This scenario, all too familiar in the oil and gas industry, represents a failure not just of a piece of equipment, but of a philosophy. For decades, asset management was viewed as a cost of doing business—a necessary evil focused on regulatory compliance and reactive repairs.
In 2025, that paradigm is not just outdated; it's a direct threat to survival.
World-class oil and gas asset management is no longer about ticking boxes or fixing what's broken. It has evolved into a strategic, data-driven discipline that serves as a primary engine for profitability. It’s about moving beyond mere compliance to unlock competitive advantage, leveraging advanced technology to bridge the physical-digital divide, and transforming operational data into tangible financial returns.
This guide is for the maintenance managers, facility operators, and industrial decision-makers on the front lines. We will move past the generic definitions and dive deep into the strategies, technologies, and practical frameworks required to build a resilient, efficient, and highly profitable asset management program for the modern energy landscape.
Beyond the Checklist: Redefining Oil and Gas Asset Management as a Profit Center
The shift in perspective from asset management as a cost center to a profit driver is the single most important strategic evolution in the industry today. It requires a fundamental change in how we measure success, justify investment, and align maintenance activities with executive-level business objectives.
The Old Paradigm: Asset Management as a Cost of Doing Business
Historically, the maintenance department was often seen as a black box that consumed budget. The primary goals were simple:
- Keep things running: Respond to failures as they occurred (reactive maintenance).
- Prevent obvious breakdowns: Perform time-based overhauls and replacements based on OEM recommendations or simple run-hours (preventive maintenance).
- Stay compliant: Generate the necessary paperwork to satisfy regulators and pass audits.
In this model, success was measured by metrics like budget adherence and the number of PMs completed on schedule. While important, these metrics fail to capture the true value—or the value being lost—within the operation. A team could be 100% compliant with its PM schedule and still suffer from poor reliability, excessive downtime, and bloated operational expenditure (OPEX).
The New Mandate: From ISO 55000 Compliance to Competitive Advantage
The introduction of standards like ISO 55000 provided a crucial framework for a more strategic approach. However, many organizations mistakenly view achieving certification as the end goal. In reality, ISO 55000 is not the destination; it is the roadmap.
The true goal is value realization. The standard's core principles—Value, Alignment, Leadership, and Assurance—are the pillars for transforming your asset management program.
- Value: Assets exist to provide value. Every maintenance action must be justifiable in terms of its contribution to that value, whether through increased production, enhanced safety, lower costs, or extended asset life.
- Alignment: Asset management objectives must be directly aligned with the organization's overall strategic plan. The maintenance manager's goals should mirror the CEO's goals: profitability, sustainability, and growth.
- Leadership: A top-down commitment is non-negotiable. Leadership must champion the shift from a "fix-it" culture to a "reliability" culture.
- Assurance: Systems must be in place to ensure that assets will perform as required, and that risks are managed effectively. This is where compliance becomes a natural byproduct of a well-run system, not the sole focus.
Example in Practice: Consider a critical compressor at an LNG facility.
- Old Paradigm: Overhaul the compressor every 8,000 operating hours as per the manual. This is compliant and straightforward.
- New Paradigm: Continuously monitor the compressor's vibration, temperature, and energy consumption. An AI-powered model analyzes this data and determines that, based on the current operating context, the compressor can safely run for 11,500 hours before an overhaul is needed. Furthermore, it identifies a developing bearing issue that can be addressed during a minor, planned shutdown, averting a catastrophic failure.
The result?
- Reduced OPEX: The deferred overhaul saves significant labor and parts costs.
- Increased Uptime: The plant avoids an unplanned shutdown, preserving millions in revenue.
- Enhanced Safety: A potential high-energy failure is proactively prevented.
- Compliance Plus: The data-driven justification for the maintenance schedule provides a far more robust assurance case for auditors than a simple calendar entry.
Quantifying the Value: Key Metrics that Matter to the C-Suite
To drive this transformation, you must speak the language of the C-suite: finance. While MTBF (Mean Time Between Failures) and MTTR (Mean Time To Repair) are vital for maintenance teams, they don't always translate effectively to the boardroom. To demonstrate the ROI of a strategic asset management program, focus on these high-impact metrics:
-
Overall Equipment Effectiveness (OEE): The gold standard for measuring manufacturing productivity, OEE is equally powerful in oil and gas. It combines three factors:
- Availability: (Run Time / Planned Production Time) - Measures losses from downtime.
- Performance: (Ideal Cycle Time × Total Count) / Run Time - Measures losses from running below optimal speed.
- Quality: (Good Count / Total Count) - Measures losses from defects or rework. An increase in OEE from 75% to 80% on a critical production unit can translate directly to millions of dollars in additional revenue with minimal capital expenditure.
-
Return on Assets (ROA): A core financial ratio (Net Income / Total Assets), ROA shows how profitable a company is relative to its total assets. Effective asset management directly boosts ROA by:
- Increasing the numerator (Net Income) through higher uptime and lower maintenance costs.
- Optimizing the denominator (Total Assets) by extending the useful life of existing equipment, deferring capital expenditures.
-
Maintenance Cost as a Percentage of Replacement Asset Value (%RAV): This metric provides a powerful benchmark for maintenance spending. It's calculated as (Total Annual Maintenance Cost / Replacement Asset Value). A world-class %RAV is typically in the range of 1.5-3%. Tracking this metric helps you justify your budget and demonstrate efficiency improvements over time.
By framing your initiatives and results using these metrics, you transform the conversation from "How much will this cost?" to "What is the return on this investment?"
The Digital Backbone: Core Technologies Powering Modern O&G Asset Management
The strategic shift to profitability is enabled by a powerful convergence of operational technology (OT) and information technology (IT). In 2025, these digital tools are no longer experimental; they are the essential backbone of any competitive oil and gas operation.
The Foundation: Enterprise Asset Management (EAM) and CMMS
The Computerized Maintenance Management System (CMMS) or a broader Enterprise Asset Management (EAM) platform is the central nervous system of the entire operation. Modern platforms have evolved far beyond simple work order management. They are the single source of truth, providing a unified view of every asset's lifecycle.
A modern EAM/CMMS must serve as:
- The System of Record: Housing the complete asset hierarchy, maintenance history, technical specifications, warranties, and cost data.
- The Work Management Engine: Streamlining everything from work request initiation and planning to scheduling, execution, and close-out, often via mobile devices for field technicians.
- The Compliance Hub: Managing and documenting all regulatory inspections, safety procedures (like Lockout-Tagout), and audit trails.
- The Integration Core: Acting as the central hub that connects to other critical systems like ERP (for financials), SCADA (for operational data), and advanced analytics platforms.
Without a robust, modern, and well-maintained EAM, any attempt at advanced asset management will be built on a foundation of sand. It is the bedrock upon which a data-driven strategy is built, providing the structured data needed for higher-level analysis. A truly effective system provides a holistic view of your entire operation through a centralized asset management system.
The Senses: IIoT Sensors and Edge Computing
If the EAM is the brain, Industrial Internet of Things (IIoT) sensors are the nerve endings, providing a constant stream of real-time data about asset health. The cost and size of sensors have plummeted, making it economically viable to monitor a vast array of equipment that was previously unmonitored.
Key sensor types in oil and gas include:
- Vibration Analysis: Detects imbalances, misalignments, and bearing wear in rotating equipment like pumps, compressors, and turbines.
- Thermal Imaging: Identifies hot spots in electrical connections, blockages in pipes, and refractory degradation in heaters.
- Acoustic Analysis: Listens for the ultrasonic signatures of gas leaks in pipelines or valves and can detect early-stage cavitation in pumps.
- Pressure & Flow Sensors: Monitor process conditions to provide context for other sensor readings and detect operational anomalies.
- Corrosion Sensors: Provide direct measurement of wall thickness loss in pipes and vessels.
For remote assets like wellheads or midstream compressor stations, Edge Computing is critical. Instead of sending a massive, constant stream of raw data to a central cloud—which is expensive and often impractical due to limited connectivity—edge devices process data locally. They can run simplified AI models to analyze data at the source, only sending alerts or summary data back to the central system. This dramatically reduces latency and data transmission costs.
The Brain: Predictive and Prescriptive Analytics (PdM & RxM)
This is where the data from IIoT sensors is transformed into actionable intelligence.
-
Predictive Maintenance (PdM): This goes beyond simple condition monitoring ("the vibration is high"). PdM uses machine learning algorithms to analyze historical and real-time data streams, identify complex patterns, and forecast a specific future event. The output is a prediction like, "Based on the current vibration signature and operating temperature, Pump P-101 has a 90% probability of bearing failure in the next 400 operating hours." This allows maintenance to be planned and scheduled with surgical precision, minimizing both downtime and maintenance costs.
-
Prescriptive Maintenance (RxM): As the next evolution, RxM takes the prediction and answers the question, "So what should I do?" It analyzes the prediction in the context of operational plans, inventory levels, and available labor. The system might provide a recommendation like, "A failure is predicted in 400 hours. The required parts are in stock. The optimal time to perform the 3-hour repair is during the planned process shutdown in 15 days, which will have zero impact on production." This level of guidance, powered by AI-powered predictive maintenance, empowers teams to make optimal decisions consistently.
The Virtual Replica: The Rise of the Digital Twin
A Digital Twin is the pinnacle of the physical-digital convergence. It is a dynamic, virtual representation of a physical asset, process, or entire facility. It's not a static 3D model; it's a living simulation that is continuously updated with real-time data from IIoT sensors, maintenance records from the EAM, and operational data from control systems.
In the oil and gas sector, digital twins are used for:
- Scenario Simulation: "What if we increase the throughput of this pipeline by 15%? How will that affect corrosion rates and the stress on our compressor stations?" These questions can be answered in the virtual world without any physical risk.
- Maintenance Strategy Optimization: Test the effects of different maintenance strategies on the twin before deploying them in the real world.
- Remote Operations and Training: Engineers can inspect a virtual offshore platform from an onshore control center. New technicians can be trained on complex procedures in a safe, simulated environment.
- Root Cause Analysis (RCA): When a failure does occur, the digital twin's historical data can be "rewound" to precisely identify the sequence of events that led to the failure, enabling more effective prevention in the future.
A Practical Framework: Implementing a World-Class Asset Management Strategy
Technology alone is not a silver bullet. A successful program requires a structured, strategic approach to implementation. This four-step framework provides a clear path from planning to execution.
Step 1: Asset Criticality Analysis (ACA)
You cannot and should not manage every asset with the same level of intensity. An ACA is a systematic process for ranking assets based on their potential impact on the business if they were to fail. This allows you to focus your limited resources where they will have the greatest effect.
The process involves creating a risk matrix that scores each asset on two axes:
- Consequence of Failure: What is the impact? This is evaluated across multiple categories:
- Safety: Potential for injury or fatality.
- Environmental: Potential for a spill or release.
- Production: Impact on throughput and revenue.
- Cost: Cost to repair or replace.
- Likelihood of Failure: How likely is it to fail? This is based on asset age, condition, operating context, and historical failure data.
Assets that fall into the high-consequence, high-likelihood category are your most critical. These are the prime candidates for advanced monitoring and predictive maintenance. Assets in the low-consequence, low-likelihood corner may be perfectly suited for a simple run-to-failure strategy.
Step 2: Choosing the Right Maintenance Strategy
Once your assets are ranked by criticality, you can assign the most appropriate maintenance strategy to each one. A mature program uses a blend of all four strategies:
- Reactive Maintenance (Run-to-Failure): The "if it ain't broke, don't fix it" approach. Ideal for non-critical, redundant, or inexpensive assets where the cost of preventive work outweighs the cost of failure. Example: Office lighting, a non-critical utility pump with a readily available spare.
- Preventive Maintenance (PM): Time-based or usage-based tasks. Effective for assets with a known failure pattern and where the consequences of failure are moderate. Example: Replacing vehicle oil every 5,000 miles, changing out filters on an HVAC unit every 3 months.
- Condition-Based Maintenance (CBM): Triggering maintenance based on a specific condition alert. This is a step up from PM, as work is only done when needed. Example: Replacing brake pads when a wear sensor indicates they are thin, changing oil when a quality sensor shows it has degraded.
- Predictive Maintenance (PdM): The most advanced strategy, reserved for your most critical and complex assets. It uses AI and machine learning to forecast failures before they happen. This is where you deploy your most sophisticated predictive maintenance solutions. Example: Using vibration analysis to schedule a bearing replacement on a main export pump weeks in advance.
The overarching methodology to formalize this selection process is Reliability-Centered Maintenance (RCM). RCM is an intensive engineering framework that analyzes the failure modes of each asset to determine the most effective and efficient maintenance policy. For a deeper dive into the methodology, Reliabilityweb offers excellent resources.
Step 3: Data Integration and Management
A common and significant hurdle is the problem of data silos. In a typical facility, critical data is scattered across multiple, disconnected systems:
- Operational data lives in SCADA and DCS systems.
- Maintenance data is in the CMMS/EAM.
- Engineering data (P&IDs, datasheets) is in a document management system.
- Financial data is in the ERP.
- Lab data is in a LIMS.
To perform any meaningful analysis, this data must be brought together. The solution lies in a strategy of robust integration. Modern platforms are built with open APIs (Application Programming Interfaces) that allow for seamless integrations with your existing systems. Data historians, like the OSIsoft PI System, often act as a central aggregator for real-time operational data, which can then be fed into both the EAM and advanced analytics platforms. A clear data governance strategy is essential to ensure data quality, consistency, and security.
Step 4: Fostering a Culture of Reliability
You can invest in the best technology in the world, but if your people don't embrace it, the initiative will fail. Building a culture of reliability is arguably the most challenging but most important step.
This involves:
- Breaking Down Silos: Create cross-functional teams with members from maintenance, operations, engineering, and IT. When operators feel ownership over equipment health and work collaboratively with maintenance, reliability improves dramatically.
- Operator Buy-in: Empower operators as the first line of defense. Train them in basic equipment inspection (a practice known as Autonomous Maintenance) and give them easy tools (like mobile apps) to report potential issues.
- Investing in Training: Your teams need new skills. Reliability engineers need to understand data science principles. Technicians need to be trained on using new sensor technologies and mobile devices.
- Leadership and Communication: Leadership must constantly communicate the "why" behind the changes. Celebrate small wins, share success stories, and demonstrate how the new approach is making everyone's job safer and more effective.
Asset Management in Action: Upstream, Midstream, and Downstream Applications
The principles of strategic asset management apply across the entire oil and gas value chain, but their application is tailored to the unique challenges of each sector.
Upstream Asset Management: Maximizing Production and Safety
In the upstream sector (exploration and production), the environment is harsh, assets are remote, and downtime directly translates to massive revenue loss.
- Key Assets: Electric Submersible Pumps (ESPs), top drives, wellheads, rotating equipment on offshore platforms (turbines, generators, compressors).
- Strategic Application: The primary goal is maximizing uptime and ensuring safety. ESPs are a classic use case for PdM. A failure requires a costly workover rig and halts all production from that well. By deploying downhole sensors and using predictive models to forecast failure, companies can schedule workovers proactively, turning a multi-million dollar emergency into a planned, cost-effective maintenance event. On an offshore platform, the digital twin of a gas compression train can be used to optimize performance and predict maintenance needs, ensuring the platform can continue to export gas without interruption.
Midstream Pipeline Integrity Management: The Lifeline of the Industry
The midstream sector is responsible for the transportation and storage of hydrocarbons. Here, asset integrity is synonymous with public safety and environmental protection.
- Key Assets: Thousands of miles of pipelines, compressor and pump stations, storage tanks, and terminals.
- Strategic Application: The focus is on risk management and regulatory compliance, governed by strict standards like ASME B31.8S for gas pipelines. A modern pipeline integrity program combines data from multiple sources into a unified risk model:
- In-line Inspection (ILI) data from "smart pig" tools that detect corrosion or cracks.
- IIoT sensor data from acoustic sensors listening for leaks or pressure sensors detecting anomalies.
- Aerial/satellite imagery to monitor for ground movement or third-party activity near the right-of-way. This integrated data feeds a digital twin of the pipeline, allowing operators to pinpoint high-risk segments and proactively schedule targeted digs and repairs, preventing catastrophic failures.
Downstream Refinery Maintenance: Optimizing Complexity and Uptime
Downstream refining and petrochemical facilities are incredibly complex, with thousands of interconnected assets. Efficiency, safety, and optimizing the major turnaround (TAR) cycle are paramount.
- Key Assets: Distillation columns, fluid catalytic crackers (FCCs), hydrotreaters, heat exchangers, and vast networks of pumps.
- Strategic Application: The goal is to maximize the time between major TARs while ensuring reliability and safety. By applying a rigorous RCM process, refineries can challenge traditional, time-based maintenance intervals. For example, instead of opening and cleaning every heat exchanger during a TAR, real-time performance monitoring can identify only those that are truly fouled, dramatically reducing the TAR scope, duration, and cost. Applying predictive maintenance for critical pumps and other rotating equipment prevents unplanned unit shutdowns that can cost a refinery hundreds of thousands of dollars per hour.
Overcoming the Hurdles: Common Challenges and Solutions in 2025
The path to a world-class asset management program is not without its challenges. Acknowledging and planning for these hurdles is key to a successful implementation.
Challenge: The Data Deluge and "Analysis Paralysis"
With thousands of sensors generating data every second, it's easy to become overwhelmed. Teams can get stuck in "analysis paralysis," collecting data for its own sake without extracting value.
- Solution: Start small and scale. Begin with a pilot project on a single, critical asset system. Use this to prove the value and refine your processes. Leverage modern AI/ML platforms that are designed to automate the analysis, filtering out the noise and presenting clear, actionable recommendations rather than just complex dashboards of raw data.
Challenge: Integrating Legacy Systems (OT/IT Convergence)
Many facilities operate with a mix of modern and aging control systems (OT) that were never designed to communicate with IT networks. Bridging this gap is a significant technical and security challenge.
- Solution: This requires a multi-pronged approach. Use modern EAM/CMMS platforms with open APIs and dedicated integration hubs. Employ middleware and data historians as translators between old and new systems. Crucially, OT/IT convergence must be paired with a robust cybersecurity strategy. Adhering to frameworks like the NIST Cybersecurity Framework is essential to protect critical operational systems from cyber threats.
Challenge: The Skills Gap and Change Management
The technology is evolving faster than the workforce's skills. There is a shortage of professionals who are fluent in both mechanical engineering and data science. Furthermore, resistance to change from a long-serving workforce can derail projects.
- Solution: This is a human challenge that requires a human solution.
- Invest in upskilling and cross-training: Send your best reliability engineers to data analytics bootcamps. Train your technicians on the new mobile tools and sensor technologies.
- Partner with vendors: Choose technology partners who provide not just software, but comprehensive implementation support, training, and change management guidance.
- Make it intuitive: Deploy user-friendly, mobile-first software that simplifies workflows for technicians in the field, rather than adding complexity.
- Champion the change: Create cross-functional reliability teams to act as internal advocates. Continuously communicate successes and demonstrate how the new tools make everyone's job safer and more valuable.
The Final Word: Your Competitive Imperative
The landscape of the oil and gas industry is one of intense competition, stringent regulation, and relentless pressure to improve financial performance. In this environment, oil and gas asset management has completed its transformation from a back-office support function to a frontline strategic weapon.
By embracing a holistic strategy that marries a profitability-focused mindset with the power of digital technologies like IIoT, AI, and Digital Twins, organizations can move far beyond the limitations of compliance-driven maintenance. They can unlock unprecedented levels of operational efficiency, safety, and resilience.
The technologies are mature. The frameworks are proven. The financial case is undeniable. In 2025, the question is no longer if your organization should adopt a strategic, data-driven approach to asset management, but how quickly you can implement it to secure your competitive edge and redefine what's possible in your operations.
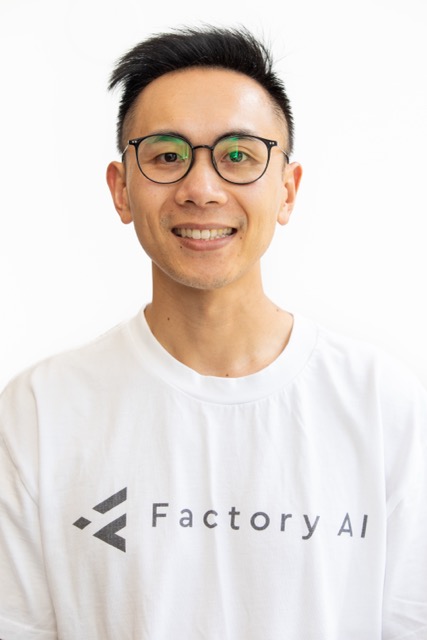