From Cost Center to Profit Driver: The Ultimate 2025 Guide to Asset Lifecycle Management
Jul 18, 2025
asset lifecycle management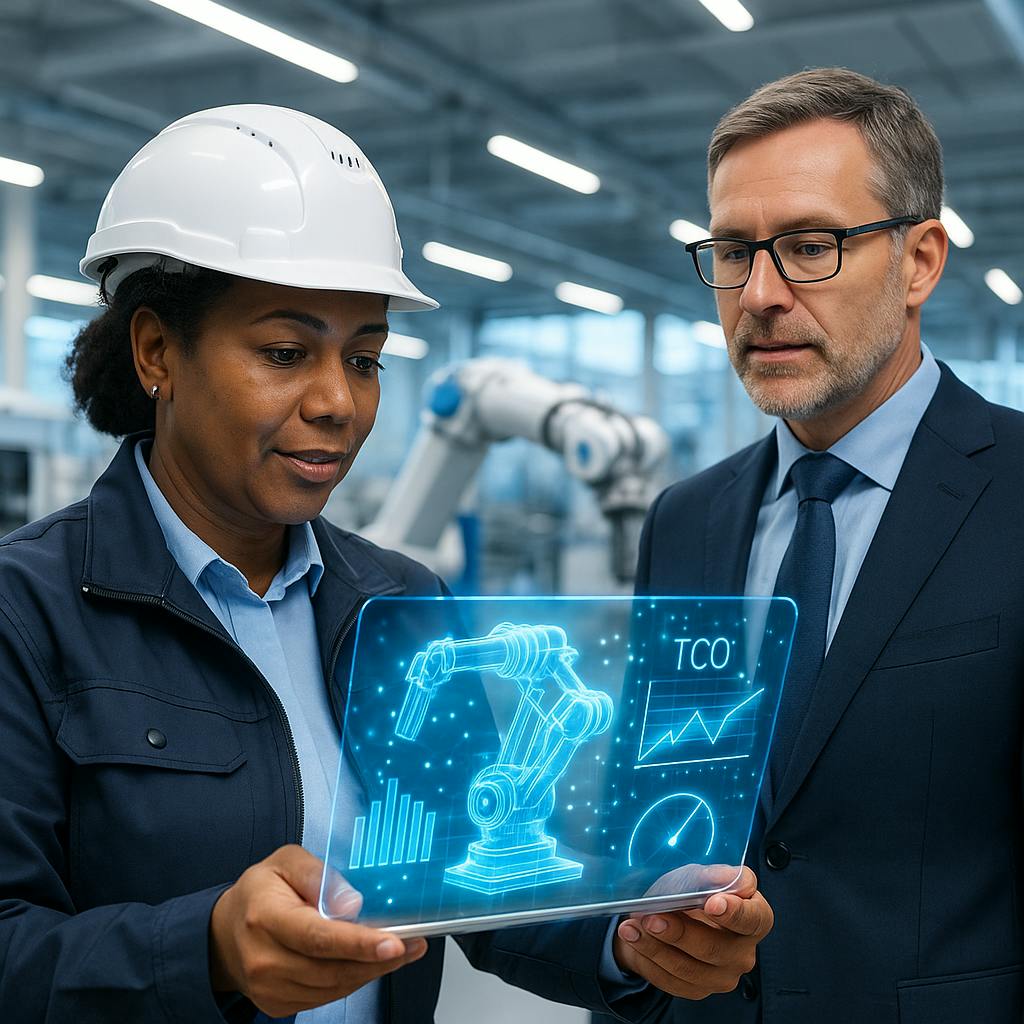
In the relentless pace of modern industry, the hum of machinery is the heartbeat of your operation. But what happens when that heartbeat falters? An unexpected breakdown isn't just an inconvenience; it's a cascade of consequences—lost production, missed deadlines, budget overruns, and frustrated teams. For decades, many organizations viewed their physical assets through a narrow lens: buy them, use them, fix them when they break, and scrap them when they die. This reactive approach is a relic of a bygone era.
Welcome to 2025, where Asset Lifecycle Management (ALM) is no longer a back-office maintenance function but a core, C-suite-level business strategy. It’s a holistic philosophy that transforms how you plan, acquire, operate, maintain, and dispose of your physical assets. It’s about shifting the conversation from "How much does it cost to fix?" to "How can this asset generate maximum value throughout its entire life?"
This isn't another generic "What is..." article. This is a comprehensive playbook for maintenance managers, operations leaders, and financial decision-makers. We'll dissect each stage of the asset lifecycle through a modern, data-driven lens, explore the technology that makes it possible, and provide a step-by-step guide to implementation. Prepare to move beyond the break-fix cycle and turn your asset management program into a powerful engine for profitability and competitive advantage.
The Strategic Imperative: Why ALM is a C-Suite Conversation in 2025
For too long, maintenance and finance have operated in different worlds, speaking different languages. Maintenance talks about MTBF (Mean Time Between Failures) and PM schedules, while Finance talks about CapEx, OpEx, and ROI. Asset Lifecycle Management is the Rosetta Stone that translates maintenance activities directly into financial outcomes, making it an essential topic in the boardroom.
Moving Beyond the "Fix-It" Mentality
The traditional view of maintenance is that of a necessary evil—a cost center focused on repairing equipment after it fails. This reactive, "run-to-failure" model is incredibly expensive. It leads to:
- Unplanned Downtime: The most expensive kind of downtime, disrupting production schedules and supply chains.
- Higher Repair Costs: Emergency repairs often involve overtime labor, expedited parts shipping, and more extensive damage than if the issue were caught early.
- Safety Risks: Catastrophic failures can create hazardous conditions for employees.
- Reduced Asset Lifespan: Constantly running assets to the point of failure shortens their useful life, forcing premature capital reinvestment.
A strategic ALM program flips this script. It reframes maintenance as a proactive, value-generating activity focused on reliability and performance. The goal isn't just to fix things; it's to prevent failures, optimize performance, and extend the economic life of every single asset.
The True Cost of Ownership: A Deep Dive into TCO
One of the most powerful concepts in ALM is the Total Cost of Ownership (TCO). The C-suite often focuses on the initial purchase price (Capital Expenditure or CapEx), but this is just the tip of the iceberg. TCO provides a complete financial picture of an asset over its entire life.
TCO = Initial Purchase Price + (Operational Costs + Maintenance Costs + Downtime Costs + Disposal Costs) - Residual Value
Let's break it down with an example. Imagine choosing between two industrial pumps:
- Pump A: Initial Cost = $20,000. It's less energy-efficient and requires more frequent, costly maintenance.
- Pump B: Initial Cost = $30,000. It's highly energy-efficient, has a longer warranty, and is designed for easier, less frequent maintenance.
A procurement team focused solely on CapEx would choose Pump A. But an ALM-focused team would calculate the TCO over a 10-year lifespan:
Cost Factor | Pump A (Lower CapEx) | Pump B (Higher CapEx) |
---|---|---|
Initial Cost | $20,000 | $30,000 |
Annual Energy Cost | $8,000 | $5,000 |
Annual Maint. Cost | $3,000 | $1,500 |
Est. Downtime Cost | $5,000 (1 major failure) | $500 (minor issues) |
Total Annual OpEx | $16,000 | $7,000 |
10-Year OpEx | $160,000 | $70,000 |
Disposal/Residual | $0 | -$1,000 (scrap value) |
10-Year TCO | $180,000 | $99,000 |
By investing more upfront in Pump B, the company saves $81,000 over the asset's life. This is the kind of data-driven insight that gets a CFO's attention. TCO analysis turns purchasing decisions from a cost-minimization exercise into a strategic investment decision.
Aligning ALM with Business Goals
Effective ALM directly impacts key business performance indicators (KPIs) that the C-suite cares about:
- Overall Equipment Effectiveness (OEE): By improving availability (less downtime), performance (running at optimal speed), and quality (fewer defects), ALM directly boosts OEE.
- Return on Investment (ROI) / Return on Net Assets (RONA): By extending the productive life of assets and increasing their output, you are squeezing more value from your capital investments, directly improving RONA.
- EBITDA (Earnings Before Interest, Taxes, Depreciation, and Amortization): Reduced maintenance costs, lower energy consumption, and increased production output all contribute positively to the bottom line.
The Role of ISO 55000: Establishing a Framework for Excellence
To formalize this strategic approach, many leading organizations are adopting the ISO 55000 family of standards. ISO 55000 isn't a prescriptive checklist; it's a management framework that provides guidance on establishing, implementing, maintaining, and improving an asset management system. It helps organizations:
- Establish a clear line of sight between organizational objectives and asset management plans.
- Manage risk and opportunities in a structured way.
- Improve financial performance without sacrificing long-term asset health.
- Foster a culture of continuous improvement.
Adopting ISO 55000 signals to stakeholders, investors, and regulators that you are serious about managing your physical assets for maximum, sustainable value.
The 5 Stages of the Asset Lifecycle: A Modern, Data-Driven Approach
While the five stages of ALM are well-known, a 2025 approach infuses each phase with data, analytics, and cross-functional collaboration. It's a continuous loop, not a linear path, where insights from the end of one asset's life directly inform the beginning of the next.
Stage 1: Strategic Planning & Acquisition
This is where value is created or destroyed. A poor decision here will have costly repercussions for years.
- Data-Informed Need Analysis: Instead of a manager saying, "I think we need a new conveyor," the process starts with data. Analysis of historical work orders, downtime logs, and TCO data from existing conveyors might reveal that a specific model consistently underperforms. This data justifies the need for a replacement and informs the specifications for the new one.
- Capital Planning & Forecasting: Modern ALM uses predictive analytics to forecast the "economic end of life" for major assets. This allows finance and operations to proactively budget for capital replacements years in advance, avoiding emergency funding requests and securing better pricing through planned procurement.
- Specifying for Reliability: The acquisition process must look beyond the price tag. The team—comprising engineering, maintenance, and procurement—develops specifications that prioritize reliability, maintainability, and energy efficiency. This includes asking for things like standardized components, easy access to service points, and comprehensive documentation. The TCO analysis from the previous section is the guiding star here.
Stage 2: Deployment, Commissioning & Integration
Bringing a new asset online correctly is critical for its long-term performance.
- Seamless Handover: A structured commissioning process ensures the asset is installed correctly and meets all performance specifications before the project team hands it over to the operations and maintenance teams.
- Establishing Baselines: From day one, performance data is captured. What is its energy consumption at idle and under load? What are its normal vibration and thermal signatures? This baseline data is the foundation for all future condition monitoring and predictive maintenance efforts.
- Digital Twin Creation: The asset is immediately entered into the central management system. This isn't just adding a name to a list. It involves uploading all relevant documentation (manuals, schematics, warranties), creating PM schedules, and linking it to spare parts inventory. A robust CMMS software acts as the asset's digital birth certificate and ongoing health record.
Stage 3: Operation & Optimization
This is the longest and most value-intensive stage. The goal is not just to use the asset but to optimize it.
- Real-Time Condition Monitoring: In 2025, critical assets are no longer black boxes. They are fitted with IoT sensors that stream real-time data on vibration, temperature, pressure, power consumption, and more. This data provides a constant, live view of asset health.
- Connecting ALM to Asset Performance Management (APM): APM uses this real-time data to drive performance. For example, if a machine's energy consumption spikes, an alert is triggered. This might not be a maintenance issue but an operational one (e.g., incorrect settings, suboptimal raw materials). ALM and APM work together to ensure the asset is not only available but also performing efficiently.
- The Power of AI: This is where the real revolution is happening. Instead of just setting simple high/low alert thresholds, AI predictive maintenance algorithms analyze complex patterns in the data to forecast failures weeks or even months in advance. For example, an AI model might detect a subtle, evolving vibration signature in a motor that indicates a bearing is beginning to wear, long before it would be noticeable to a human inspector. This allows for planned, minimally disruptive repairs.
Stage 4: Maintenance, Repair, and Overhaul (MRO)
This stage is transformed from a reactive firefight into a strategic, data-driven function. The key is implementing the right maintenance strategy for the right asset at the right time.
- Reliability-Centered Maintenance (RCM): This is the guiding philosophy. RCM is a systematic process used to determine the most effective maintenance strategy for a given piece of equipment. As explained by industry experts at Reliabilityweb, it doesn't treat all assets equally. A critical, high-cost asset will have a different strategy than a non-critical, redundant one.
- The Modern Maintenance Mix:
- Predictive Maintenance (PdM): The gold standard for critical assets. It uses condition monitoring and AI to predict failures, allowing for "just-in-time" maintenance. This is the core of a proactive strategy, and solutions for predictive maintenance are becoming increasingly sophisticated and accessible.
- Preventive Maintenance (PM): Time-based or usage-based maintenance. Still essential for many assets where failure patterns are well understood (e.g., changing oil every 500 hours of operation). Modern CMMS platforms automate the scheduling and tracking of PMs.
- Reactive Maintenance: The "break-fix" model. While the goal is to minimize it, it will always have a place for non-critical, low-cost assets where it's more economical to simply run them to failure and replace them.
- Integrated MRO Inventory: An effective maintenance strategy is useless without the right parts. ALM systems link maintenance work orders directly to inventory. When a predictive alert forecasts a bearing failure in 3 weeks, the system automatically checks if the part is in stock and, if not, generates a purchase order, ensuring the part arrives before the technician needs it.
Stage 5: Decommissioning & Disposal
The final stage is often overlooked, but it's a rich source of data and value.
- Data-Driven Replace vs. Repair Decisions: As an asset ages, its maintenance costs inevitably rise. The ALM system tracks these costs. At some point, the TCO of continuing to operate the old asset surpasses the TCO of a new one. This data-driven "economic end of life" calculation provides a clear, objective justification for decommissioning and replacement.
- Sustainable Disposal: Environmental regulations and corporate social responsibility demand responsible disposal. This stage involves planning for safe dismantling, recycling of materials, and proper disposal of hazardous components.
- Closing the Loop: This is the most crucial part. Before scrapping the asset, a final analysis is performed. Why did it fail? Did it meet its expected lifespan? What were the most common failure modes? This "asset autopsy" generates invaluable data that feeds directly back into Stage 1, influencing the specifications and selection criteria for its replacement. This closes the lifecycle loop and drives continuous improvement.
Building Your ALM Tech Stack: The Tools of the Trade for 2025
A strategic ALM program is powered by an integrated technology stack. Each component plays a vital role in capturing, analyzing, and acting on asset data.
The Central Nervous System: Your CMMS/EAM Platform
A Computerized Maintenance Management System (CMMS) or Enterprise Asset Management (EAM) platform is the foundation of your ALM strategy. A legacy, clunky system won't cut it. A modern platform for 2025 must have:
- A User-Friendly, Mobile-First Interface: Technicians need to be able to access work orders, view asset histories, and log data on a tablet or phone from the plant floor, not a desktop in an office.
- Powerful Integration Capabilities: It must seamlessly connect with other systems like IoT platforms, ERPs (for financial data), and SCADA systems (for operational data).
- Robust Reporting and Analytics: The system should make it easy to track KPIs, analyze trends, and generate reports that are meaningful to both maintenance managers and the C-suite.
- Configurable Workflows: The ability to digitize and automate key processes, from routine PMs to complex failure analysis, is essential. A system with powerful work order software capabilities is a must.
The Eyes and Ears: Asset Tracking and IoT Sensors
You can't manage what you don't monitor.
- Asset Tracking: Simple technologies like QR codes or NFC tags on every asset make it incredibly easy for a technician to scan it with their mobile device and instantly pull up its entire history, documentation, and open work orders. This eliminates guesswork and ensures work is logged against the correct asset.
- IoT Sensors: A wide array of affordable, wireless sensors are available to monitor virtually any condition:
- Vibration Sensors: Detect imbalances, misalignments, and bearing wear in rotating equipment.
- Thermal Imagers: Identify overheating in electrical panels, motors, and mechanical systems.
- Acoustic Sensors: Listen for ultrasonic signatures that can indicate gas leaks or electrical arcing.
- Oil Analysis Sensors: Monitor the condition and contamination of lubricants in real-time.
The Brain: Predictive and Prescriptive Analytics
This is where data becomes intelligence.
- Predictive Analytics: As discussed, AI and machine learning algorithms analyze sensor data to predict when an asset is likely to fail.
- Prescriptive Analytics: This is the next evolution. Prescriptive analytics goes a step further, not only predicting a failure but also recommending the optimal course of action. For example, it might not just say "Pump P-101 will fail in 2 weeks." It might say, "Pump P-101 is showing a vibration signature consistent with impeller wear. The recommended action is to schedule a replacement in 12-15 days. The required part is in stock at warehouse B. The estimated repair time is 4 hours." This level of prescriptive maintenance provides unprecedented decision support.
Integration is Key: Connecting ALM to ERP and Financial Systems
To achieve the strategic goals of ALM, the technical data must be linked to the financial data. Integrating your CMMS/EAM with your company's Enterprise Resource Planning (ERP) system creates a single source of truth. This allows for:
- Automated Financial Tracking: Maintenance costs (labor, parts) are automatically rolled up and associated with specific assets, departments, and production lines in the ERP.
- Accurate TCO Calculation: Real-time, accurate cost data makes TCO analysis dynamic and precise.
- Streamlined Procurement: The CMMS can automatically generate purchase requisitions in the ERP when spare parts inventory falls below a set level.
A Step-by-Step Guide to Implementing an Asset Lifecycle Management Strategy
Transitioning to a full-fledged ALM strategy is a journey, not an overnight switch. A phased, methodical approach is the key to success.
Step 1: Secure Executive Buy-In & Form a Cross-Functional Team
You cannot do this alone. The first step is to build a business case focused on TCO reduction, improved uptime, and risk mitigation. Present this to senior leadership to secure the necessary budget and political capital. Then, assemble a team with representatives from Maintenance, Operations, Engineering, IT, and Finance. This ensures all perspectives are considered and fosters buy-in across the organization.
Step 2: Conduct a Comprehensive Asset Audit
You need to know what you have before you can manage it. Conduct a full physical audit of your assets. What equipment do you have? Where is it located? What is its current condition? What is its criticality to the operation? This process will populate your asset hierarchy in the CMMS and form the basis of your entire program.
Step 3: Define Your ALM Goals and KPIs
What does success look like? Work with your cross-functional team to establish clear, measurable goals. These shouldn't be vague aspirations. They should be specific targets, such as:
- Reduce TCO on critical assets by 10% within 24 months.
- Increase mechanical uptime from 92% to 96% within 18 months.
- Reduce reactive maintenance work from 60% to 30% of total labor hours.
- Improve PM completion rate from 75% to 95%.
Step 4: Select and Implement Your Technology Stack
Based on your goals, select the right tools. Don't try to boil the ocean. Start with a foundational CMMS. Then, identify a pilot area—perhaps one critical production line—to deploy IoT sensors and predictive analytics. A phased rollout allows you to learn, demonstrate value, and build momentum for a wider implementation.
Step 5: Develop Standardized Processes and Workflows
Technology is only an enabler. You need robust processes. Standardize how work is requested, planned, scheduled, executed, and documented. Define your maintenance strategies (PdM, PM, etc.) for different asset classes. Create clear procedures for everything from new asset onboarding to end-of-life analysis.
Step 6: Train Your Team and Foster a Culture of Reliability
Your technicians, operators, and supervisors are the key to success. Provide comprehensive training not just on how to use the new software, but on why the company is making this shift. Explain the principles of reliability and how their actions contribute to the bigger picture. Celebrate wins and recognize individuals who embrace the new way of working.
Step 7: Measure, Analyze, and Continuously Improve
Your ALM program is a living system. Continuously track your KPIs against the goals you set in Step 3. Use the analytics in your CMMS to identify bottlenecks, recurring problems, and areas for improvement. Hold regular review meetings with your cross-functional team to discuss performance and adjust your strategy. This embodies the Plan-Do-Check-Act cycle, a cornerstone of continuous improvement methodologies as detailed by quality organizations like iSixSigma.
Overcoming Common ALM Challenges: A Troubleshooting Guide
The path to ALM excellence has its bumps. Here are some common challenges and how to navigate them.
Challenge: Poor Data Quality ("Garbage In, Garbage Out")
Your analytics are only as good as your data. Incomplete work order details, incorrectly logged parts, or inconsistent asset naming conventions will undermine your efforts. Solution: Implement data standards from day one. Use dropdown menus and required fields in your CMMS to enforce consistency. Use mobile devices with barcode/QR scanning to eliminate manual data entry errors. Conduct regular data audits to clean up inaccuracies.
Challenge: Resistance to Change from the Team
Technicians who are used to being "heroes" who swoop in to fix major breakdowns may resist a more planned, scheduled way of working. Solution: Involve them in the process early. Ask for their input on selecting software and defining workflows. Clearly communicate the "What's In It For Me?" (WIIFM)—less emergency overtime, safer working conditions, and the opportunity to develop new skills in data analysis and reliability.
Challenge: Siloed Departments
If Finance, Operations, and Maintenance don't communicate, the program will fail. Finance might cut the maintenance budget without understanding the TCO implications, or Operations might run equipment to failure to meet a quota, ignoring maintenance schedules. Solution: The cross-functional team established in Step 1 is the primary solution. Shared KPIs are also critical. When Operations and Maintenance are both measured on OEE, they are incentivized to collaborate. An integrated tech stack that provides a single source of truth also breaks down information silos.
Challenge: Proving ROI to Secure Budget
"This all sounds great, but how do I pay for it?" is a common and valid question from leadership. Solution: Start small with a high-impact pilot project. Choose a production line that is a known bottleneck or has high maintenance costs. Meticulously track the metrics before and after your intervention—downtime, repair costs, output, etc. Use this data to build an undeniable business case that shows a clear return on investment, making it much easier to secure funding for a full-scale rollout.
The Future is Proactive
Asset Lifecycle Management is more than a set of processes or a software platform. It's a fundamental shift in mindset. It's the recognition that your physical assets are not just tools to be used, but valuable investments to be strategically managed for maximum return.
By bridging the gap between the plant floor and the balance sheet, ALM turns maintenance from a reactive cost center into a proactive, data-driven profit driver. It empowers your teams to move from fighting fires to preventing them, from guessing to knowing, and from simply owning assets to truly mastering their value. The journey requires commitment, collaboration, and the right technology, but the destination—an operation that is more reliable, efficient, and profitable—is well worth the effort.
Ready to begin your journey? A great first step is understanding the capabilities of a modern asset management platform and how it can become the central hub for your entire ALM strategy.
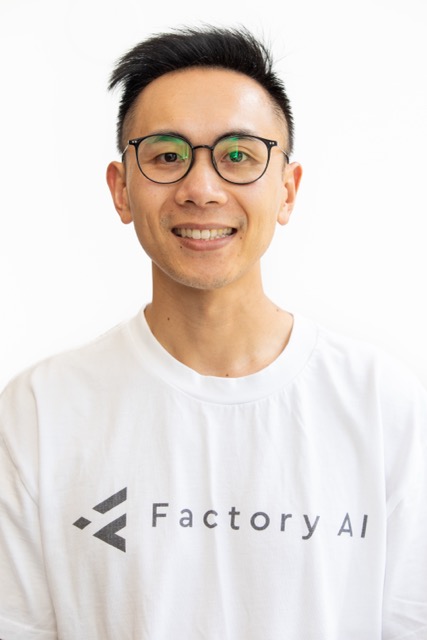