Beyond the Calendar: The Modern Time-Based Maintenance Playbook for 2025
Jul 17, 2025
time based maintenance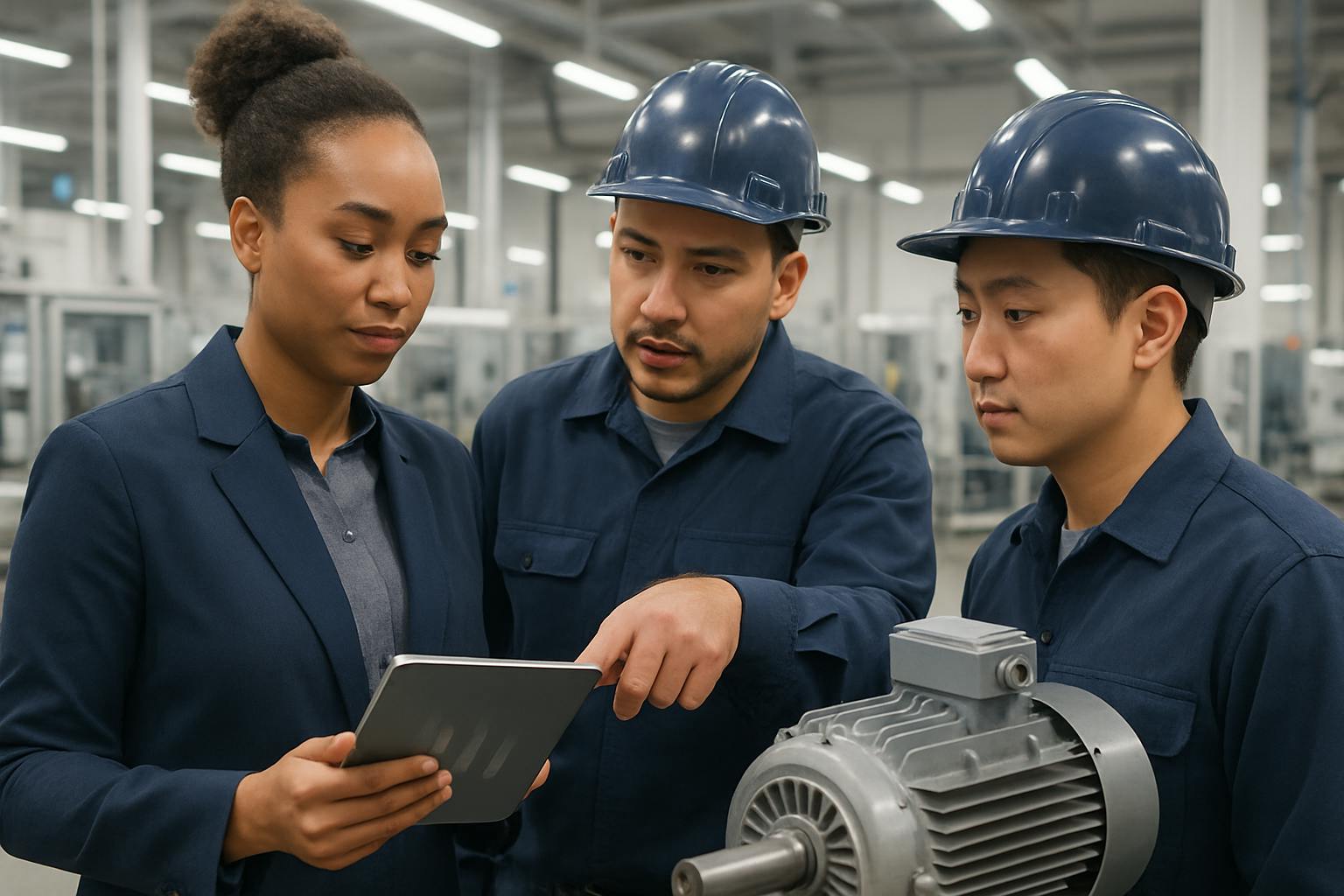
For decades, time-based maintenance (TBM) has been a cornerstone of industrial operations. The concept is simple: perform maintenance at predetermined, regular intervals. It’s the "change the oil every 5,000 miles" of the factory floor. But in an era of AI, IIoT, and advanced analytics, many maintenance leaders are asking a critical question: Is TBM an outdated relic, or is it still a relevant strategy?
The answer, for the forward-thinking organization in 2025, is a resounding "yes, but..."
TBM is not dead. Far from it. However, the old "set it and forget it" approach is. Simply following OEM recommendations from a dusty binder is a recipe for inefficiency, leading to either costly over-maintenance or catastrophic under-maintenance.
This is not another "What is TBM?" article. This is the modern playbook. This is your strategic guide to transforming time-based maintenance from a rigid, calendar-driven chore into a dynamic, data-informed, and highly effective component of a world-class asset management program. We'll move from basic theory to high-performance execution, giving you the actionable steps to build, optimize, and evolve a TBM program that drives real results.
Recalibrating Our Understanding: What TBM Really Is in 2025
Before we can build a modern TBM program, we need to shed some outdated perceptions. The TBM of 2025 is more nuanced, more data-driven, and more strategic than its predecessor.
Beyond the "Change the Oil Every 3 Months" Mentality
At its core, TBM is a form of preventive maintenance where the trigger for intervention is the passage of time or a usage counter. This could be calendar time (every 90 days), operational hours (every 1,000 run-hours), or production cycles (every 50,000 units).
The critical distinction of a modern TBM strategy is that this interval is not an arbitrary guess. It is a calculated decision based on a combination of data, analysis, and operational context. It's about proactively intervening to prevent known failure modes before they can lead to functional failure, based on the most likely timeframe for degradation.
The Core Components of a TBM Task
Every well-defined TBM work order, whether on paper or in a digital system, should contain four key elements:
- The Trigger: What initiates the work? This must be specific. Not just "quarterly," but "every 90 days from the last completion date" or "every 2,500 cycles."
- The Task List: A detailed, standardized procedure. What specific actions must the technician perform? This includes checklists, torque specs, lubricant types, and safety warnings. Vague instructions like "Check motor" are unacceptable.
- The Resources: What is needed to complete the job successfully? This includes a bill of materials (BOM) for parts, required tools, estimated labor hours, and necessary permits (like lockout/tagout).
- The Documentation: A clear record of what was done, by whom, when it was completed, any parts used, and—most importantly—any observations about the asset's condition. This feedback is the lifeblood of an optimized program.
Where TBM Still Reigns Supreme
In a world buzzing about predictive maintenance, it’s easy to think TBM should be replaced everywhere. This is a strategic error. TBM remains the most cost-effective and logical strategy for a significant portion of your assets.
- Assets with Predictable Wear Patterns: Some components are designed to wear out over a predictable lifespan. Think of filters, certain types of seals, belts, and lubricants that degrade with time and use. For these, a time-based replacement is often the most efficient approach.
- Failure Modes Not Easily Detected: Not every failure gives a clear warning sign like increased vibration or temperature. Some failures, like material fatigue or certain types of corrosion, can occur with little to no detectable precursor. In these cases, a planned TBM task is the only way to be proactive.
- Safety and Regulatory Compliance: Many safety-critical systems, like fire suppression equipment, pressure vessel inspections, or emergency lighting tests, have maintenance intervals mandated by law or code (e.g., NFPA, OSHA). Here, TBM is not just a strategy; it's a requirement.
- Low-Cost, Non-Critical Assets: Is it worth installing a $1,000 vibration sensor on a $500 non-critical exhaust fan? Probably not. For assets where the cost of failure is low and the cost of advanced monitoring is high, a simple, time-based inspection or replacement is perfectly logical.
The Foundation: Building Your TBM Program from the Ground Up
A successful TBM program isn't created overnight. It's built on a solid foundation of data, analysis, and clear processes. Rushing this stage is like building a house on sand.
Step 1: Comprehensive Asset Inventory and Criticality Analysis
You cannot effectively maintain what you don't know you have or what you don't understand the importance of. The first step is a thorough accounting of your physical assets.
- Build the Asset Hierarchy: Start by creating a logical, hierarchical list of all maintainable assets. This usually starts broad (e.g., Plant 1 -> Production Line 3 -> Packaging Area) and drills down to specific parent and child assets (e.g., Case Packer XYZ -> Main Drive Motor -> Gearbox). A robust asset management system is essential for organizing this information.
- Perform an Asset Criticality Analysis (ACA): Not all assets are created equal. An ACA is a systematic process to rank assets based on their importance to the organization. A common method is to score each asset on several factors and multiply the scores to get a criticality rating.
Example Criticality Matrix:
Factor | Score (1-5) | Description |
---|---|---|
Impact on Safety/Environment | 1 (Low) - 5 (High) | What happens if this asset fails? |
Impact on Production | 1 (Low) - 5 (High) | Does failure stop the entire line or just a small part? |
Cost of Repair | 1 (Low) - 5 (High) | How expensive is it to fix? |
Likelihood of Failure | 1 (Low) - 5 (High) | How often does this type of asset tend to fail? |
An asset with high scores across the board (e.g., the main plant air compressor) is highly critical and warrants a more intensive maintenance strategy. An asset with low scores (e.g., an office air conditioner) is less critical. This analysis tells you where to focus your TBM efforts first.
Step 2: Uncovering Failure Modes with FMEA
Once you know what assets you have and which are most critical, you need to understand how they can fail. The best tool for this is a Failure Mode and Effects Analysis (FMEA).
An FMEA is a structured process to:
- Identify potential failure modes for an asset (e.g., for a motor: "Bearing seizure," "Winding insulation failure," "Shaft fracture").
- Determine the potential effects of each failure (e.g., "Unplanned line stoppage for 8 hours," "Potential for fire").
- Identify the potential causes of the failure (e.g., "Contamination of lubricant," "Overheating," "Vibration").
- Define current controls (maintenance tasks) to prevent the cause.
The FMEA process directly informs your TBM strategy. If a primary cause of failure is "lubricant degradation over time," then a time-based task like "Replace lubricant every 1,500 run-hours" is a perfect control. If a cause is undetectable, like internal metal fatigue, a time-based component replacement might be the only viable proactive option. For a deep dive into the methodologies, engineering bodies like ASME offer standards and publications on reliability engineering.
Step 3: Setting the Right Intervals - The Science and the Art
This is the most challenging—and most important—part of creating a TBM plan. The right interval saves money and prevents failures. The wrong interval wastes resources or invites disaster.
The Science: Using Data and Formulas
Your starting point should always be data. Guesswork is not a strategy.
- Manufacturer Recommendations: Use these as your initial baseline, but with a critical eye. Manufacturers are often conservative to protect themselves from warranty claims. Their recommendations don't account for your specific operating context.
- Mean Time Between Failures (MTBF): If you have historical data on asset failures, you can calculate MTBF. It's a simple but powerful metric for reliability.
- Formula:
MTBF = Total Operational Uptime / Number of Failures
- Example: A pump ran for 8,760 hours in a year. During that time, it failed 3 times. Its MTBF is 8760 / 3 = 2,920 hours.
- Application: A common rule of thumb is to set the TBM interval at a fraction of the MTBF (e.g., 1/2 or 1/3) to intervene well before the average failure point. In this case, you might set a PM for that pump every 1,000-1,500 run-hours.
- Formula:
- Historical Work Order Data: Your best source of truth is your own history. A well-managed CMMS software contains a goldmine of information. Analyze past work orders for similar assets to see when failures occurred and what the "as-found" condition was during past PMs.
The Art: Factoring in the Real World
Data and formulas only get you so far. You must temper them with operational reality.
- Operating Environment: An identical motor running in a hot, dusty foundry will degrade faster than one in a climate-controlled cleanroom. Adjust intervals accordingly.
- Operational Intensity: An asset running 24/7/365 is under more stress than one running a single 8-hour shift, five days a week. Your TBM trigger should ideally be based on run-hours or cycles, not just the calendar.
- Asset Age: An older asset may require more frequent inspections and lubrication than a new one.
- Technician Expertise: Your veteran technicians have invaluable knowledge. Ask them. They know which machines are "problem children" and which ones "run forever." Incorporate their qualitative feedback into your interval-setting decisions.
Step 4: Developing Standardized PM Procedures
An interval is useless without a clear, repeatable task list. Standardized procedures ensure that every TBM task is performed correctly and consistently, regardless of which technician is assigned the job.
A good PM procedure should include:
- A detailed, step-by-step checklist of actions.
- All necessary safety warnings and required PPE.
- Lockout/Tagout (LOTO) procedures.
- A list of required tools and parts.
- Photos or diagrams to clarify complex steps.
- Expected tolerances and measurement standards (e.g., "Belt tension should be between 12-15 lbs").
- A section for the technician to record observations and measurements.
These procedures shouldn't live in a binder. They should be digitized and attached directly to the work order within your CMMS, accessible on a mobile device right at the asset.
The Modern TBM Playbook in Action: Execution and Optimization
With a solid foundation, it's time to execute. A modern TBM program is a living system, not a static document. It requires the right tools, a culture of feedback, and a commitment to continuous improvement.
From Spreadsheet Chaos to Streamlined Operations
Many organizations still try to manage TBM schedules on a spreadsheet or a whiteboard. This is a recipe for failure at any significant scale. It's prone to human error, has no audit trail, offers no analytics, and makes collaboration impossible.
In 2025, a Computerized Maintenance Management System (CMMS) is non-negotiable for effective TBM. Here’s how it transforms execution:
- Automation: A CMMS automatically generates and assigns TBM tasks based on the triggers you set (time, meter readings). No more manually checking a calendar. This is the core function of modern work order software.
- Centralized Information: All asset data, PM procedures, parts information, and work history are in one place, accessible to everyone.
- Scheduling and Resource Planning: Managers can see upcoming TBM workloads, balance assignments among technicians, and ensure parts and tools are ready, minimizing wrench time.
- Mobile Empowerment: Technicians can receive work orders, view procedures and asset history, record their findings, and close out work on a tablet or phone directly at the job site. This dramatically improves data accuracy and efficiency.
The Feedback Loop: The Key to Continuous Improvement
This is the single most important concept that separates a world-class TBM program from an average one. Time-based maintenance must not be a "set it and forget it" strategy. It must be a closed-loop system where the results of today's PMs inform the schedule for tomorrow's.
Here's how to build that loop:
- Capture Technician Observations: Your work order template must have mandatory fields for technicians to describe the "as-found" condition.
- Good Feedback: "Replaced belt per PM. Old belt showed significant cracking and wear. Good call to replace."
- Actionable Feedback: "Replaced filter per 3-month PM. Filter was only 25% clogged. The replaced filter from the identical machine on Line 2 last week was 90% clogged. We should investigate why."
- Valuable Feedback: "Lubricated gearbox. Found metal shavings on the magnetic drain plug. This is the first time we've seen this on this asset. Recommend taking an oil sample."
- Analyze PM Effectiveness: Regularly review your maintenance data. Ask these questions:
- Are we still having failures of a specific mode between scheduled TBM tasks? If yes, your interval is too long.
- Are we consistently replacing components that have significant useful life remaining? If yes, your interval may be too short, and you're wasting money.
- What is the ratio of planned work (like TBM) to unplanned, reactive work? A healthy ratio is around 80/20 or better. If your reactive work is high, your TBM strategy isn't working.
- Formally Review and Adjust Intervals: Based on the analysis above, make data-driven decisions to adjust your TBM intervals. This shouldn't be a random process. Schedule a formal review of TBM plans for your critical assets on a quarterly or semi-annual basis.
Case Study: Optimizing a Conveyor Gearbox TBM Schedule
Let's see this in practice. A food processing plant has a critical conveyor gearbox.
- Initial State (Year 1): The OEM manual recommends a full oil change every 2,000 run-hours. The maintenance team follows this diligently using their CMMS to track run-hours. The task requires 3 hours of downtime and $200 in synthetic lubricant.
- Implementation & Feedback (Year 2): The plant runs 24/5, hitting the 2,000-hour mark roughly every 12 weeks. Technicians are trained to take an oil sample before draining and to note the condition. For four consecutive changes, the lab reports on the samples come back "Normal," and technicians note the old oil "looks clean."
- Analysis & Optimization (Start of Year 3): The Reliability Engineer reviews the work order history and lab reports. The data clearly shows that the oil is not significantly degraded at 2,000 hours in their specific application. They hypothesize they can extend the interval.
- The Test: They decide to push the next interval to 3,000 hours, but with a control: they will take an oil sample at 2,000 and 2,500 hours to ensure the oil's health.
- Result (End of Year 3): The samples at 2,000 and 2,500 hours come back normal. The 3,000-hour change is successful. The plant has now moved from ~4.3 oil changes per year to ~2.9 per year for this asset.
- The ROI: They eliminated 1.4 PMs per year.
- Downtime Savings: 1.4 PMs * 3 hours/PM = 4.2 hours of additional production time.
- Cost Savings: 1.4 PMs * $200/PM = $280 in direct costs.
- Labor Savings: 1.4 PMs * (labor rate) = freed up technician time for other proactive work.
This is the power of an optimized, feedback-driven TBM program.
Integrating TBM into a Hybrid Maintenance Strategy
TBM does not exist in a vacuum. The most reliable and cost-effective plants use a blended or hybrid strategy, applying the right type of maintenance to the right asset at the right time.
TBM and Preventive Maintenance (PM): The Same, but Different?
These terms are often used interchangeably, but there's a subtle difference. Preventive Maintenance (PM) is the broad category of all maintenance performed to prevent failures. Time-Based Maintenance is a type of PM where the trigger is time. Other types of PM include usage-based (triggered by cycles/miles) and condition-based. Think of PM as the parent category and TBM as one of its children. This is why a strong preventive maintenance program is the overarching goal.
The P-F Curve and Finding the Sweet Spot
The P-F Curve is a fundamental concept in reliability that illustrates an asset's journey from health to failure.
- P (Potential Failure): The point in time when a failure condition first becomes detectable (e.g., a bearing starts to generate a microscopic vibration pattern).
- F (Functional Failure): The point in time when the asset can no longer perform its intended function.
The goal of maintenance is to intervene somewhere on the curve between P and F.
- Time-Based Maintenance aims to perform a task at a fixed interval that, on average, falls before point P is even reached. It's a truly "preventive" action.
- Condition-Based Maintenance (CBM) uses monitoring (like vibration analysis or thermography) to detect the symptoms of failure after point P has occurred, allowing you to plan and schedule a repair before point F.
- Predictive Maintenance (PdM) uses advanced analytics and AI to forecast when point P will occur, providing an even earlier warning.
For a great visual explanation, Reliabilityweb offers many articles on the P-F Curve and its application.
When to "Graduate" an Asset from TBM to CBM or PdM
The decision to move an asset from a simple TBM plan to a more advanced CBM or PdM strategy is a strategic, economic one.
Consider graduating an asset when:
- It's Highly Critical: For your most critical assets, the cost of an unexpected failure is so high that you need the earliest possible warning.
- TBM is Ineffective: If an asset continues to fail despite a TBM program, it means the failure mode is not age-related and requires condition monitoring to detect.
- The Cost of TBM is Too High: TBM can be wasteful. If you are performing costly component replacements on a time-based schedule, it may be cheaper in the long run to invest in monitoring technology that allows you to run those components to their full, useful life.
- Technology Becomes Affordable: The cost of sensors and monitoring technology continues to fall. A CBM program that was too expensive five years ago might offer a fantastic ROI today.
Example: A plant has a critical process pump. Their TBM strategy involves a complete rebuild every 12 months at a cost of $15,000 in parts, labor, and downtime. They invest $10,000 in a permanent vibration and temperature monitoring system. Over the next three years, the system shows the pump is healthy, and they avoid two rebuilds, saving $30,000 and only performing the maintenance when the data indicates it's necessary. This is a clear case for graduating to a predictive maintenance strategy.
Overcoming Common TBM Challenges and Pitfalls
Even with a great plan, execution can stumble. Here are some common pitfalls and how to avoid them.
The "Pencil Whipping" Problem
This is when technicians sign off on a TBM task without performing it correctly or at all, often due to time pressure. It creates a dangerous illusion of reliability.
- Solution: Foster a culture of integrity. Use a mobile CMMS with digital checklists that require photos of the completed work or specific measurements to be entered. Implement supervisor spot-checks and audits of completed TBMs.
The Static Schedule Trap
This is the "we've always done it this way" syndrome. A TBM schedule created five years ago is likely no longer optimal. Assets age, production demands change, and new data becomes available.
- Solution: Build a formal review process into your management system. Mandate a data-driven review of the TBM strategy for your top 20% most critical assets every single year.
Poor Data Discipline
Your TBM optimization efforts are only as good as the data you collect. Incomplete work orders, generic failure codes ("pump broken"), and missing parts information make meaningful analysis impossible.
- Solution: Make data entry easy with a user-friendly CMMS. Train technicians on why the data is important—show them how their accurate notes lead to better schedules and fewer middle-of-the-night call-outs. Adhering to clear data practices, as outlined by bodies like NIST in their work on maintenance data standards, is crucial for enabling advanced analytics.
Miscalculating the True Cost of TBM
Many managers only see the cost of parts and labor. They miss the hidden costs.
- Solution: Calculate the Total Cost of TBM for critical assets. This includes:
- Direct Costs (parts, labor, contractors).
- Downtime Costs (lost production/opportunity cost).
- Administrative Costs (planning, scheduling).
- Inventory Carrying Costs (cost of holding PM-specific spare parts).
Seeing this full picture provides a much stronger business case for investing in optimization or graduating to a more efficient strategy like CBM.
The Future of TBM: Smarter, More Dynamic, and AI-Enhanced
The evolution of TBM is not over. The technologies of 2025 and beyond are making it even more intelligent.
Dynamic TBM: AI-Adjusted Intervals
Imagine a TBM schedule that isn't fixed. An AI engine integrated with your CMMS can analyze not just run-hours, but also ambient temperature, production throughput, and historical failure data. It might dynamically adjust a TBM interval, recommending a filter change at 85 days during a hot, high-production summer, but extending it to 100 days during a cooler, slower winter. This is the next level of optimization.
The Role of IIoT in Supercharging TBM
The Industrial Internet of Things (IIoT) is blurring the lines. Simple, low-cost sensors can make TBM triggers far more accurate. Instead of a calendar, a TBM task can be triggered by a smart sensor that has counted exactly 100,000 cycles or measured 5,000 hours of actual operation, eliminating the guesswork from usage-based calculations.
Prescriptive Maintenance: The Next Frontier
The ultimate goal is prescriptive maintenance. This is where AI moves beyond prediction and into recommendation. A prescriptive system might detect an emerging issue and, instead of just raising an alarm, it would automatically generate a detailed work order. This work order could include a highly specific TBM task list, a list of required parts, and even suggest the optimal time to schedule the work to minimize production impact.
TBM is Not Dead, It's Evolving
Time-based maintenance is, and will remain, an indispensable tool in the maintenance and reliability arsenal. But the days of treating it as a static, fire-and-forget task are over.
The modern TBM playbook is about being strategic. It’s about using data to define your foundation, leveraging technology like a CMMS to execute flawlessly, and creating robust feedback loops to continuously optimize. It’s about knowing when TBM is the right choice, and when it’s time to graduate an asset to a more advanced strategy.
By moving beyond the calendar and embracing this dynamic, data-driven approach, you can transform your TBM program from a cost center into a powerful engine for asset reliability, operational efficiency, and a stronger bottom line.
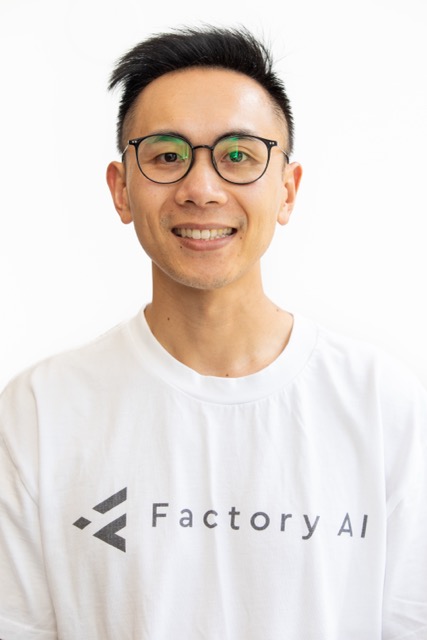