Why You Should Care About Predictive Maintenance: Beyond the Technical Jargon
Oct 24, 2023
Predictive Maintenance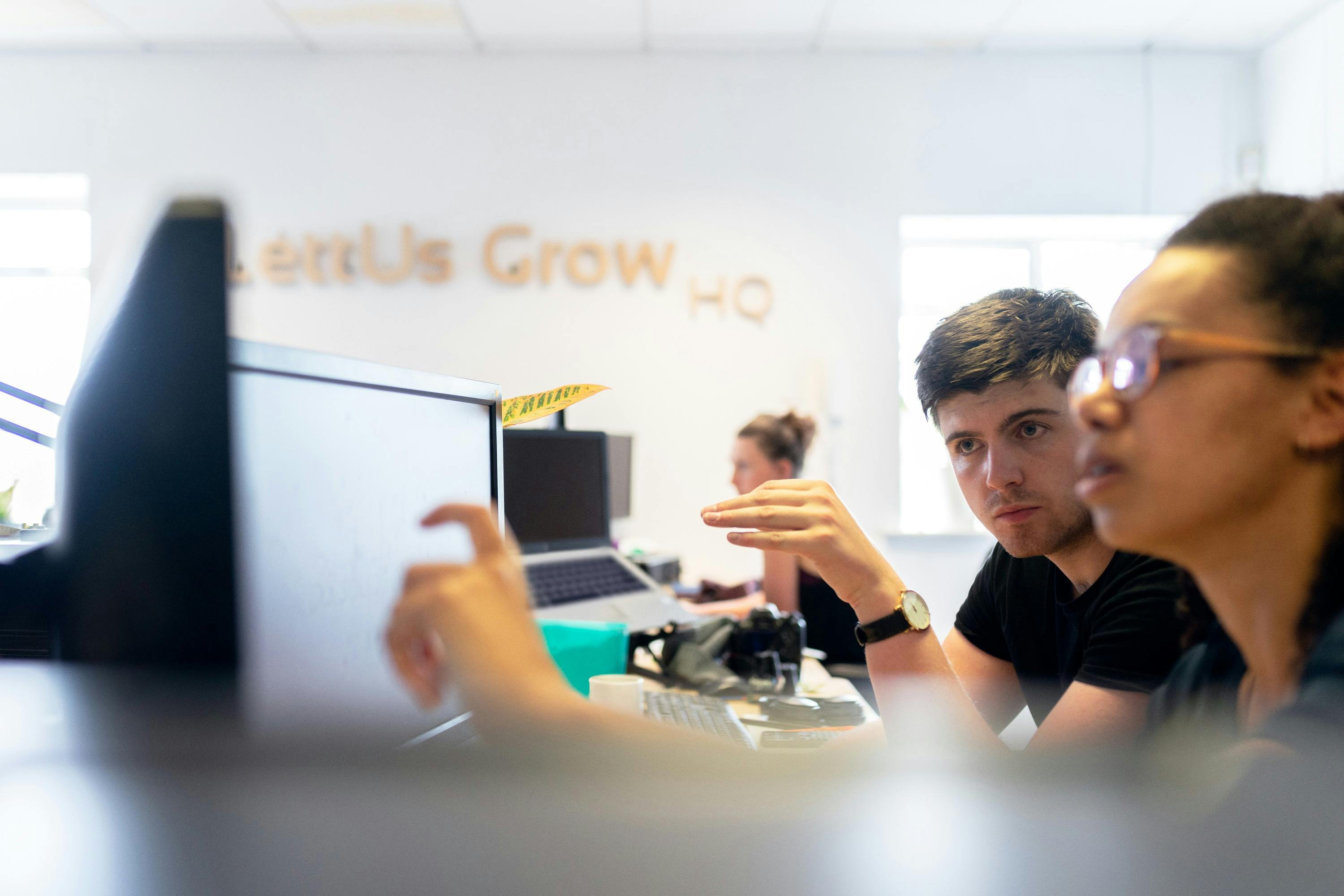
In today's manufacturing landscape, the term "Predictive Maintenance" is often misunderstood and conflated with simple predictive analytics, creating confusion for organizations looking to implement true asset health monitoring solutions. This article clarifies what Predictive Maintenance truly entails - the use of continuous monitoring data and machine learning to estimate asset conditions and enable proactive maintenance decisions well before failures occur.
Intro
AI and analytics are hot topics in manufacturing at the moment. A quick online search would have you think that almost every piece of technology in the realm of reliability and maintenance can do Predictive Maintenance. Either with their predictive analytics platform, or custom-built tools, of as a add-on capacity with their hardware.
That may not be completely false, but our experience tells us that a large part of this problem stems from the industry not being entirely aligned on a single definition of what predictive maintenance is, and what it isn’t.
This large amount of noise in the market means it makes sense that you perform a good amount of due diligence to select your partner on this journey from all those potential vendors. In order to help you do this, we will explain in this short article how we, at Factory AI, define Predictive Maintenance.
Predictive Analytics
The first thing to align on is the understanding that Predictive Analytics and Predictive Maintenance not the same thing. So let’s first distinguish the two.
Let’s first take a step back and cover the basic types of data analytics:
There are four key types of data analytics:
- Descriptive, which answers the question, “What happened?”
- Diagnostic, which answers the question, “Why did this happen?”
- Prescriptive, which answers the question, “What should we do next?”
- Predictive, which answers the question, “What might happen in the future?”
Predictive analytics is the use of data to predict future trends and events. It uses historical data to forecast potential scenarios that can help drive strategic decisions. Predictive analytics will form part of your Predictive Maintenance strategy. Only part of it. Data scientists, on their own, cannot solve your maintenance problems. If you think about it under this lens, it all seems very obvious.
Analysing machine data can be enough to identify anomalies, trends and even produce some convincing dashboards. The challenge of our customers is to adopt this to their reality, and make it useful.
Here’s a simple example; how can you tell which anomalies are part of the normal operating profile of the asset, and which ones are not? Without any maintenance understanding, you won’t be able to answer this question.
So, while data science is necessary to create models, you will need much more than big data analytics to achieve Predictive Maintenance.
A deep understanding the health of assets, and the capacity to have an in-depth discussion about maintenance strategies are necessary to reach success in Predictive Maintenance.
So, What is predictive maintenance?
Predictive Maintenance is the use of continuous monitoring data to estimate the condition of machines to enable teams to take proactive actions.
Proactive actions examples include to perform targeted maintenance before predictive failures, to cluster maintenance activities, and to adjust asset usage.
The value of Predictive Maintenance is logical, yet important: the earlier you know an asset is going to fail, the bigger the range of proactive actions you can take.
Predictive Maintenance is more than Condition Based Maintenance (CBM)
Predictive Maintenance is much more than applying condition monitoring in your maintenance strategy. Many organisations are already doing Condition Based Maintenance (CBM).
CBM considers how an asset has been and is being used to determine when servicing should occur. This will likely lead to maintenance work that is performed at the exact moment when measured parameters reach unacceptable levels. Said more simply, CBM looks at the status/health of a machine and performs maintenance when these important indicators change.
Predictive Maintenance will take this to a next level by offering the insights to plan maintenance work that is scheduled in the future based on the intelligent analysis of ML models.
A majority of reliability and maintenance leaders we speak with continue to rely on traditional periodic condition monitoring where the burden is placed on a human burden for the data collection and analysis.
Predictive Maintenance removes this dependence, hence removing barriers for the application of cost effective condition monitoring to a much wider range of asset criticality.
Understanding These Maintenance Strategies with a Runner's Analogy
Now, we’ve used quite a bit of industry jargon so far.
To simplify, let's use a straightforward analogy involving a runner to understand how different maintenance approaches work.
Imagine you're a runner gearing up for a marathon. Your coach advises that the most effective recovery strategy for you involves getting massages and doing mobility work on your legs, in addition to maintaining a balanced diet and ensuring proper sleep.
The massages and mobility work come at a cost of both time and money, just like all maintenance strategies.
Here's how different maintenance strategies align with your running needs, along with their respective benefits and drawbacks:
- Reactive / Run to Fail (Literally): In this scenario, you only opt for a massage or mobility work when you get an injury. The downside here is quite evident: you're already injured, and you'll need to halt your training until you've fully recovered. On the upside, you can be sure that every massage and mobility session is productive because they are necessary.
- Preventive or Planned Maintenance (PM): In this case, you receive a massage every week on Saturday mornings as a preventative measure. The advantage is that you're minimising the risk of injury as much as possible. However, the downside is that you might be over-investing, both in terms of time and money, on these massages and mobility sessions.
- Condition-Based Maintenance (CBM): Here, you introduce tools such as a Garmin watch, a heart rate monitor, and a Continuous Glucose Monitor (CGM) to gather condition data. You use your human intelligence to analyse this data each week after your training sessions and only schedule massages when you observe elevated readings. The benefit is that you're only investing in massages and mobility when necessary, saving both time and money. The drawback is that you must make relatively complex decisions using your own judgment on a weekly basis.
- Predictive Maintenance (PdM): Here, your coach's expertise extends further. Fortunately for you, your coach isn't just a seasoned athlete and trainer; she's also a skilled data scientist proficient in creating machine learning (ML) models. She aggregates data from various sources and inputs them into these models. As you progress in line with your training plan, the model continuously learns about your habits and performance against the plan. It automatically alerts you if you're overtraining or undertraining, and instantly notifies you when massages and mobility work are needed. Going a step further, you can program the model to schedule these sessions and add them to your calendar, making this the most efficient scenario.
Hopefully this analogy helped demystify maintenance strategies for you. Under this lens, it seems clear that while each approach has its advantages and drawbacks, predictive maintenance, with its data-driven automation, is the most efficient way to keep your running (or manufacturing) in peak condition.
What if you’re already doing some condition based maintenance?
If you already have a CBM program, then you’re in a good place. This likely means that culturally your organisation understands the benefits of monitoring machines to optimise your maintenance strategy. Adopting Predictive Maintenance will take you to the next level.
How so? Because Predictive Maintenance leverages a much higher level of data driven approaches than traditional condition monitoring given the data is from on-line, continuous sources as opposed to irregular manual readings.
The data-driven nature of Predictive Maintenance has been made possible, and continue to improve with the advancements in the domains of artificial intelligence and machine learning.
What are the benefits of Predictive Maintenance?
Returning to our earlier point, the sooner you detect an asset's potential failure, the greater your capacity for proactive measures. This naturally raises a critical question: when is the ideal moment for asset maintenance? The complexity of this question merits a dedicated article, so watch this space for more insights.
Going back to the benefits of Predictive Maintenance, whilst teams tend to immediately default to reducing unplanned downtime as the primary benefit, there’s a lot more to it. Namely:
- 10-20% Increased equipment uptime and availability (Source: Deloitte)
- 20-50% Reduction of efforts on maintenance planning time (Source: Deloitte)
- 10-20% Cost savings in operations and MRO and material spend (Source: Deloitte)
- Saving money by reducing the need for regular visual inspections
- Saving money by fine tuning and reducing the PMs
Conclusion
Going back to our statement above, the earlier you know an asset is going to fail, the bigger the range of proactive actions you can take.
This value of Predictive Maintenance is generated by helping you to make decisions that are better informed.
One consideration worth noting is that insight into the current and future state of assets can also benefit other stakeholders in the organisation, such as the production department, who might be able to subsequently reduce energy and materials usage, increase availability, reduce slowdowns and reduce quality losses.
The engineering project department can also benefit from data on remaining useful life to better plan and come up with optimisation strategies.
Hopefully, this article served the purpose of shedding some light for you on what Predictive Maintenance is.
If you’ve got any questions for us or would like to discuss further any of the claims we make, we would love to hear from you.
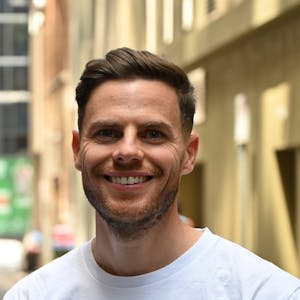
JP Picard
JP is the Co-Founder and CEO of Factory AI. Previously, he held senior sales leadership roles at Salesforce and Zipline, supporting executive teams in their digital transformation journeys. His passion for reliability and maintenance grows as Factory AI partners with clients to tackle unique challenges