What Realistic Results Can Be Achieved in a Predictive Maintenance Pilot?
Jul 4, 2025
Condition Monitoring Software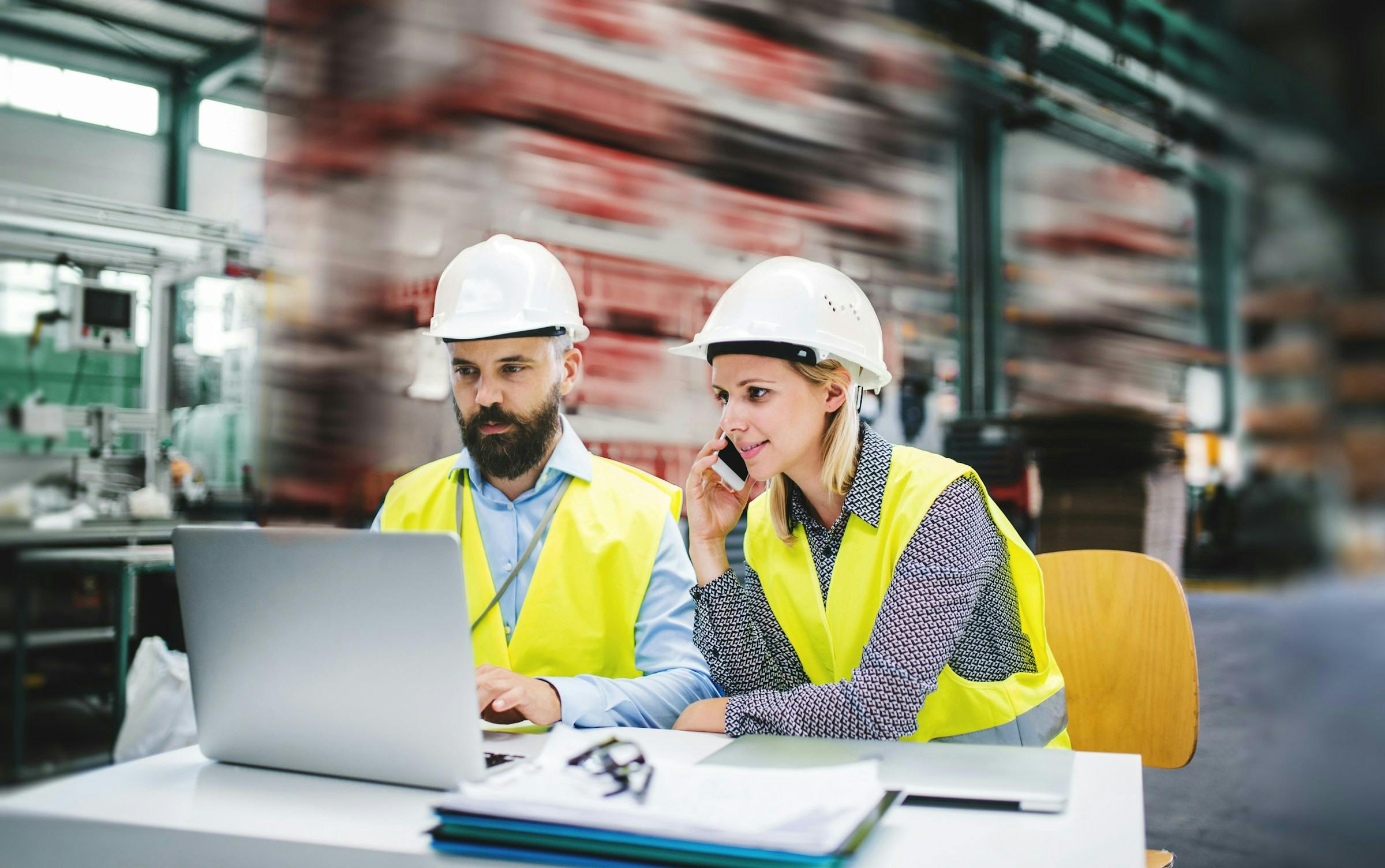
Introduction
For maintenance and reliability professionals, the strategic imperative of achieving operational excellence is paramount. The adoption of predictive maintenance software represents a significant opportunity to transition from reactive interventions to proactive asset management, promising enhanced uptime, optimised costs, and improved safety.
Yet, as organisations contemplate initiating a predictive maintenance pilot program, a critical question arises: what constitutes realistic results from such an initial deployment, particularly within the complex and high-stakes environment of agri-food manufacturing? This article aims to provide a clear, evidence-based perspective on the measurable outcomes one can genuinely expect from a well-structured PdM pilot, serving as a guide to ensure your investment delivers tangible value and propels your strategic reliability initiatives forward.
The Problem: When PdM Pilots Fail to Deliver Expected Value
While the strategic advantages of predictive maintenance software are widely recognised, not all pilot programmes successfully demonstrate their value or secure the necessary organisational support for broader implementation. This can lead to frustration, misallocated resources, and a reluctance to pursue advanced maintenance strategies. Several factors frequently impede a pilot's success:
- Unrealistic Expectations: A common pitfall is the belief that a pilot will instantly eliminate all forms of downtime or provide comprehensive coverage across an entire facility. PdM implementation is an iterative process, and a pilot represents a foundational, learning phase.
- Suboptimal Asset Selection: Choosing assets that are either too simplistic (where preventive maintenance software might suffice) or those with highly complex, intermittent failures that are challenging for initial modelling. If the chosen asset doesn't experience impactful or quantifiable issues during the pilot, demonstrating the solution's worth becomes difficult.
- Absence of Clear Objectives and Baselines: Initiating a pilot without precisely defined success metrics or a clear understanding of current asset performance. Without a quantifiable baseline, proving the ROI of predictive maintenance remains subjective, undermining justification for future investment.
- Data Overload Without Actionable Insights: Deploying wireless condition monitoring sensors but failing to collect sufficient high-quality data, or lacking the advanced analytical capabilities (machine condition monitoring with AI) or specialised vibration analysis expertise to translate raw data into actionable intelligence. This often leads to a deluge of information without clear direction.
- Internal Communication and Buy-in Challenges: Insufficient engagement with key stakeholders (Maintenance, Operations, Finance, IT) from the outset can foster resistance or apathy. This frequently manifests in the objection: "It sounds good, but we don’t think we have that much downtime to justify it." This perspective often overlooks the full spectrum of costs associated with unplanned stoppages beyond immediate repair expenses. For a detailed exploration of these common hurdles, refer to our article on the Top 10 Predictive Maintenance Objections.
- Inconsistent Follow-Through: Detecting potential issues but failing to act on the insights promptly or integrate them effectively into existing maintenance planning and scheduling software. A successful pilot validates the prediction and the subsequent proactive intervention.
- Vendor Lock-in Concerns: Apprehensions regarding commitment to a specific vendor's predictive maintenance equipment or software after the pilot, potentially limiting future flexibility or escalating costs, can stifle enthusiasm for expansion.
These challenges are particularly pronounced in demanding sectors such as agri-food, where the financial repercussions of downtime are exceptionally high. For instance, in meat processing, a critical chain failure can incur costs exceeding A$100,000 per hour, while a pet food producer might face 10-30 operators without work, in addition to product waste and rework expenses. Without careful planning, even pilots with significant potential for downtime cost avoidance can fall short of demonstrating their full value.
The Insight: A Pilot as a Strategic Catalyst for Value Demonstration
The fundamental insight for successfully launching a predictive maintenance pilot program is to perceive it not merely as a technical evaluation, but as a strategic exercise in value demonstration and internal momentum building. While a pilot is indeed a critical learning phase, its paramount objective is to concretely prove that PdM can yield measurable, realistic results, thereby justifying broader organisational investment and transforming existing operational paradigms. For a comprehensive understanding of the strategic imperative of PdM, delve into our article on Unlocking the Promise: Why It's Time to Embrace Predictive Maintenance Software.
A meticulously designed pilot serves as a scalable blueprint for your future reliability programme. It provides unequivocal evidence of:
- Quantifiable Cost Avoidance: Tangible financial savings resulting from prevented breakdowns, reduced reliance on emergency repairs, and optimised inventory management.
- Improved Uptime & Productivity: Direct enhancements in equipment availability and overall throughput efficiency.
- Enhanced Decision-Making: Empowering maintenance teams with precise, actionable intelligence that replaces guesswork.
- Streamlined Processes: Refining maintenance workflows and fostering improved inter-departmental collaboration.
The key to achieving these outcomes lies in systematic planning, disciplined execution, and transparent reporting. It involves establishing clear, attainable targets for a focused, high-impact area, meticulously tracking performance, and then effectively communicating the successes to all relevant stakeholders. This methodical approach directly counters the objection: "It sounds good, but we don’t think we have that much downtime to justify it," by substituting assumptions with verifiable data on avoided costs and tangible benefits. As Nanoprecise notes, "Forbes estimates that unplanned downtime can cost industrial manufacturers up to A$75 billion a year." This broader financial perspective is essential for contextualising pilot results.
For agri-food manufacturers, where perishable goods and stringent HACCP and maintenance software compliance are daily operational realities, demonstrating these results swiftly and convincingly is of paramount importance. A successful pilot fosters internal trust, secures subsequent funding, and establishes the foundational elements for a culture rooted in proactive reliability.
The Solution: Achieving Realistic Results in a Predictive Maintenance Pilot
A successful predictive maintenance pilot program necessitates a structured methodology, ensuring that initial efforts generate concrete, demonstrable results that propel the broader reliability initiative forward. For a detailed guide on initiating your pilot, consult our roadmap: The First 10 Steps: Roadmap of a Predictive Maintenance Pilot.
Phase 1: Strategic Pilot Design – Setting the Stage for Success
The bedrock of any triumphant pilot is meticulous planning and unambiguous definition.
- Define Clear, Quantifiable Objectives:
- Transition from vague aspirations like "enhance reliability." Instead, articulate specific, measurable outcomes. For example: "Achieve a 50% reduction in unplanned downtime on critical oven #3 within 6 months," or "Prevent at least one catastrophic failure on main chiller compressor #1 within the pilot duration, thereby saving an estimated A$80,000 in repair and lost production."
- Align these objectives directly with identified business pain points, such as the high costs associated with idle labour, product waste, or production rework.
- These meticulously defined KPIs will serve as the benchmarks for unequivocally proving the ROI of predictive maintenance.
- Identify Critical Pilot Assets:
- High Impact of Failure: Prioritise equipment whose failure would impose the most significant financial burdens, safety hazards, or production bottlenecks. In agri-food, this includes primary filleting lines in seafood processing, critical homogenisers in dairy plants, main mixers/extruders in pet food manufacturing, or overhead chain drives in meat processing (where a single failure could incur costs exceeding A$100,000 per hour).
- Known "Bad Actors": Assets with a documented history of frequent breakdowns, disproportionately high maintenance costs, or intermittent operational issues are prime candidates, offering clear opportunities for early, impactful wins.
- Data Accessibility and Suitability: Select assets where wireless condition monitoring sensors can be readily installed to yield meaningful data (e.g., rotating machinery such as motors, pumps, and fans). Consider assets where existing operational data (e.g., motor current from Variable Speed Drives (VSDs) or Direct Online (DOL) starters, historical CMMS for manufacturing logs) can augment sensor data for richer insights.
- Environmental Compatibility: For maintenance in high hygiene environments, choose assets where sensors can effectively withstand rigorous washdowns or be securely positioned behind protective guards, as is often a preference in fish processing facilities.
- Establish Comprehensive Baseline Metrics:
- Prior to the deployment of any predictive maintenance equipment, meticulously document the current performance of your selected pilot assets. This critical baseline should encompass:
- Historical unplanned downtime hours and frequency.
- Associated financial costs (labour, lost production, scrap, expedited parts).
- Specific maintenance costs (parts, labour for reactive versus planned work).
- Key reliability metrics such as Mean Time Between Failures (MTBF) and Mean Time To Repair (MTTR).
- Relevant components of Overall Equipment Effectiveness (OEE) – Availability, Performance, and Quality.
- This comprehensive baseline provides the indispensable "before" snapshot against which the pilot's results will be measured, providing irrefutable evidence of the impact and ROI of predictive maintenance.
- Stakeholder Alignment and Expectation Management:
- Engage all key stakeholders from the project's inception. Clearly articulate the pilot's objectives, scope, and the realistic results that can be achieved. This establishes appropriate expectations and fosters broad organisational support.
- Proactively address the common objection: "It sounds good, but we don’t think we have that much downtime to justify it."
- Counter-argument: Systematically assist stakeholders in quantifying the hidden costs of their existing downtime or chronic operational issues that may have become normalised. Utilise internal financial data (e.g., cost of idle labour, rework, scrapped product) or industry benchmarks to reveal the comprehensive financial impact. Emphasise that even minor, frequent stoppages cumulatively result in substantial losses. Highlight that the value of PdM extends beyond preventing catastrophic breakdowns; it encompasses optimising routine maintenance, extending asset lifespan, and reducing energy consumption. A pilot is specifically designed to demonstrate these previously unrecognised costs and the tangible savings derived from avoiding them, thereby transforming skepticism into quantifiable proof. As Nanoprecise notes, "Forbes estimates that unplanned downtime can cost industrial manufacturers up to A$75 billion a year." This broader financial perspective is crucial for effective justification.
Phase 2: Execution & Data Collection – From Setup to Insight
This phase focuses on the efficient deployment of technology and the subsequent generation of actionable insights from collected data.
- Rapid, Non-Intrusive Deployment:
- Select predictive maintenance equipment that minimises disruption to ongoing production. Factory AI's proven capability of "From Install to Insight in Under 30 Minutes per Asset" is critical here, particularly for 24/7 operations where installation windows may be restricted to weekend shutdowns or brief breaks.
- Prioritise wireless condition monitoring sensors for their ease of installation, reduced cabling complexity, and flexibility in placement.
- Ensure the chosen solution can withstand and effectively operate within your specific environmental realities (e.g., maintenance in high hygiene environments prevalent in food processing).
- Robust Data Collection and Quality Assurance:
- Implement reliable data streams from all deployed wireless condition monitoring sensors (e.g., vibration, temperature, acoustics, motor current).
- Rigorous data quality assurance is paramount; inaccurate or incomplete data will lead to unreliable predictions.
- Consider how to seamlessly integrate existing operational data from PLCs or SCADA systems if relevant, to enrich contextual understanding and enhance the accuracy of insights.
- AI-Driven Anomaly Detection and Insight Generation:
- This is the stage where the power of machine learning in manufacturing is fully unleashed. The predictive maintenance software must possess sophisticated algorithms capable of autonomously analysing vast datasets to learn normal operating patterns for each specific asset.
- Machine condition monitoring with AI will then meticulously identify subtle anomalies or deviations that signify impending failure, often long before such issues would be detectable through human observation or traditional threshold alarms.
- Crucially, the system must translate complex raw data into clear, actionable "pre-warnings on any impending issues" accompanied by prescriptive recommendations. This means that no vibration analysis expertise is required from your in-house team to interpret intricate graphs or raw sensor readings, thereby empowering maintenance teams to act directly and effectively.
- Seamless Integration with Existing Systems (Pilot Scope):
- Even within the pilot phase, plan for the seamless integration of insights into existing workflows. Can the PdM software (e.g., Factory AI) generate concise reports or trigger direct notifications that can be fed into your CMMS for manufacturing or maintenance planning and scheduling software to automatically create work orders? This demonstrates streamlined workflow and facilitates timely action based on newly acquired intelligence.
Phase 3: Measuring & Demonstrating Results – The Proof is in the Pudding
This phase is where the pilot's true value is substantiated. Its success hinges on its ability to demonstrate quantifiable improvements against the pre-defined objectives.
- Quantifying Cost Avoidance:
- This is frequently the most compelling result. For every predicted failure that is averted through a planned intervention, meticulously calculate the precise cost saved. This calculation should encompass:
- Lost Production Value: The financial worth of goods not produced during an unplanned stoppage, contrasted with production during planned, brief maintenance windows.
- Idle Labour Costs: The wages of personnel standing by unproductive during an unexpected outage.
- Product Waste/Rework: The direct cost of discarded raw materials or finished goods that spoil or require rework due to interruptions.
- Emergency Repair Premiums: The difference in cost between planned parts/labour and expedited parts/overtime.
- Maintain a detailed "downtime cost avoidance" log. A successful pilot can demonstrate that the predictive maintenance software pays for itself in 6 months by avoiding merely one or two critical failures. Petrobras, for instance, reported A$17 million in savings and a 14x ROI in its first year from a PdM pilot.
- Improved Availability and Uptime:
- Rigorously track and document the increase in asset availability and uptime specifically for the pilot assets. This directly contributes to a higher Overall Equipment Effectiveness (OEE) score.
- A leading dairy manufacturer, for example, recorded a 45% reduction in unplanned stoppages after implementing a PdM system, translating directly to significant OEE improvements (Updata.ca).
- "Quantitative Examples: Integrating predictive maintenance with real-time monitoring can reduce downtime by up to 30%, increase equipment efficiency by 20%, and cut defect rates by 15%." (IIoT World).
- Optimised Maintenance Activities:
- Quantify the shift from reactive or emergency work orders to planned, condition-based work. This invariably leads to more efficient utilisation of maintenance staff and a substantial reduction in overtime.
- Document specific instances where planned maintenance, initiated by PdM insights, successfully prevented a larger, more costly repair.
- Early Indicators of Extended Asset Life:
- While achieving full asset life extension is a long-term benefit, a pilot can provide early indicators of healthy component operation that might otherwise have been replaced prematurely based on rigid PM schedules. By enabling precise, just-in-time interventions, you maximise the useful life of components.
- Reduced Spare Parts Needs (Early Wins):
- A pilot can demonstrate the potential for a leaner inventory by illustrating how accurate predictions facilitate just-in-time ordering of critical spare parts, thereby reducing carrying costs and the necessity for large "just in case" stockpiles.
- Safety Enhancements:
- Document any instances where the early detection of a potential failure (e.g., a rapidly degrading bearing, an overheating motor) successfully averted a dangerous situation or prevented a catastrophic equipment malfunction that could have resulted in injury to personnel.
- Compelling Reporting:
- Translate complex technical results into clear, concise business language for executive leadership and other non-technical stakeholders. Utilise dashboards, visualisations, and financial summaries to effectively highlight the impact of the predictive maintenance pilot program on key performance indicators such as ROI of predictive maintenance, OEE, and quantifiable cost avoidance. Tailor reports to resonate with each stakeholder's specific interests and priorities.
Phase 4: Building Momentum & Scaling – Beyond the Pilot
A successful pilot is not an endpoint; it is the catalyst. The ultimate objective is to leverage these initial compelling results to justify and implement a broader, more impactful reliability programme across your operations.
- Leverage Pilot Success for Broader Rollout:
- The quantifiable results from your pilot programme become the most compelling argument for securing additional budget and widespread organisational buy-in. This enables the scaling of predictive maintenance software across a greater number of assets, production lines, or even other manufacturing sites within your organisation.
- Utilise the predictive maintenance case studies generated internally from your pilot to demonstrate proven value and build a strong narrative for expansion.
- Factory AI's Role in Achieving Realistic Results:
- "Predictive Maintenance That Pays for Itself in 6 Months": This core promise, consistently validated in our pilot deployments, directly addresses concerns about financial viability and rapid ROI, rendering the business case for expansion undeniable.
- "Built for the Agri-Food Industry": Our specialisation means our analytical models and insights are highly relevant to your specific assets and the demanding environmental challenges you face, ensuring more accurate predictions and genuinely valuable results within your pilot. This applies comprehensively across predictive maintenance for dairy plants, predictive maintenance for FMCG, and seafood processing facilities.
- "Works Without Wi-Fi or IT Integration": By circumventing common IT infrastructure roadblocks, our system facilitates rapid pilot deployment without protracted IT approval cycles, significantly accelerating your ability to demonstrate tangible results.
- "No Vibration Analysis Expertise Required": Our advanced AI simplifies complex data interpretation, rendering pilot results immediately actionable for your existing team, thereby reducing the need for costly specialist hires and dramatically shortening the "time to insight."
- "Sensor-Agnostic – Use the Hardware You Already Have": This inherent flexibility can lower pilot costs and allow you to leverage any prior investments in predictive maintenance equipment, optimising resource utilisation.
- "From Install to Insight in Under 30 Minutes per Asset": This unparalleled speed enables you to initiate your pilot, commence data collection, and begin generating valuable results with remarkable efficiency, which is paramount for demonstrating swift wins.
- "Sensor + Software Bundled in One Subscription": Our transparent and predictable pricing model simplifies budget approval for the pilot and ensures cost predictability as you scale the solution.
- "Designed for the Team on the Tools": This philosophy ensures the pilot is highly user-friendly for your frontline staff, fostering enhanced engagement and guaranteeing that data-driven insights are consistently acted upon.
- "Built by Engineers Who’ve Worked on the Plant Floor": Our direct, practical experience means our solution is engineered to deliver real-world results that directly address your team's daily operational challenges.
- "More Than Predictive – A Full Reliability Platform": Beyond initial pilot success, our integrated CMMS capabilities, maintenance planning and scheduling software, and holistic asset health monitoring facilitate seamless scaling into a comprehensive reliability programme, consistently enhancing results over time.
Real-World Examples: Quantifiable Results from Pilot Programs
Numerous industries, including diverse manufacturing sectors, have consistently demonstrated significant, quantifiable results from predictive maintenance pilot programs. These outcomes are not isolated occurrences but reflect a consistent pattern of operational improvement.
Example 1: Automotive Assembly Plant (Manufacturing Parallel) An automotive assembly plant successfully implemented predictive maintenance software across its welding robots using advanced machine condition monitoring with AI. Prior to the pilot, the plant experienced an average of 4.7 hours of unplanned downtime per week on these critical robots. Following the deployment of PdM, this figure dramatically reduced to just 0.8 hours—representing an impressive 83% reduction in unplanned downtime. Simultaneously, overall maintenance costs decreased by 47%, while product quality improved by 23% due to enhanced and consistent machine performance (WorkTrek.com). While not specific to agri-food, this case powerfully illustrates the profound impact achievable from a focused PdM pilot.
Example 2: Major Snack Food Producer (FMCG Specific) A leading snack food manufacturer, representative of high-volume predictive maintenance for FMCG operations, launched a PdM system focused on minimising unplanned downtime. Their pilot program successfully limited planned downtime to a mere 0.75% and restricted unplanned disruptions to 2.88%. This technology notably prevented the failure of critical components, such as a PC combustion blower motor, which would have caused significant disruptions to potato chip production (ProValet.io, referencing Frito-Lay). This case study unequivocally demonstrates how targeted pilots effectively avert costly, specific failures.
Example 3: Leading Dairy Manufacturer A prominent dairy manufacturer reported a substantial 45% reduction in unplanned stoppages after implementing a predictive maintenance system on critical assets including homogenisers and filling lines. This strategic shift resulted in average maintenance cost reductions of 30%, an average 25% increase in equipment lifespan, and a 40% increase in mean time between failures (MTBF). Their Operations Director affirmed: "This technology has allowed us to shift from a reactive approach to a proactive strategy, transforming our efficiency" (Updata.ca). This stands as a compelling example of predictive maintenance for dairy plants yielding substantial and measurable results.
Example 4: Oil & Gas Company (High-Value Asset Parallel) A multinational oil and gas corporation successfully piloted AVEVA™ Predictive Analytics, which enabled them to detect 51 major early warnings in its inaugural year. This resulted in realised savings of A$17 million, translating into an impressive 14x ROI (AVEVA.com). This case powerfully demonstrates that even in capital-intensive industries with exceptionally high-value assets, strategically executed pilots can yield extraordinary financial returns rapidly. This serves as a potent parallel for the agri-food industry, where losses stemming from single asset failures can be equally devastating.
Example 5: Global Beverage Bottler (Process Optimisation) A large beverage bottling plant implemented a predictive maintenance pilot program on their high-speed filling machines, specifically targeting motor current and acoustic signatures with wireless condition monitoring sensors. The machine learning in manufacturing detected subtle variations in motor load that indicated slight mechanical stress before any visible issues or downtime occurred. By proactively adjusting motor alignment based on these insights, the pilot achieved a 7% reduction in energy consumption for the monitored machines and a 3% improvement in overall bottling speed consistency, demonstrating benefits beyond just breakdown prevention.
Example 6: Industrial Bakery (Quality Improvement & Waste Reduction) An industrial bakery introduced asset health monitoring on its dough mixers and large proofing ovens. Their goal was to improve consistency and reduce batch waste from quality deviations. The pilot, using a combination of real-time vibration monitoring on mixers and temperature/humidity sensor data in ovens, allowed their predictive maintenance software to identify instances where subtle equipment anomalies contributed to inconsistent dough texture or uneven baking. By addressing these issues proactively, the bakery reported a 10% reduction in raw material waste and a 5% improvement in overall product conformity during the pilot phase, directly translating to downtime cost avoidance for quality-related issues.
Example 7: Pharmaceutical Packaging Line (Efficiency and Safety) A pharmaceutical packaging facility (similar in regulatory rigor to agri-food) ran a pilot on a critical robotic arm assembly line. Historically, minor component wear would cause erratic movements, leading to small jams, manual interventions, and potential safety risks. The predictive maintenance pilot program used wireless condition monitoring sensors to detect early signs of wear in the robot's joints and actuators. The system provided timely alerts, allowing for planned lubrication and minor adjustments during off-shifts. This led to a 15% reduction in micro-stoppages, a 5% increase in line speed, and a significant improvement in operator safety and morale due to fewer manual interventions in hazardous areas.
These diverse examples unequivocally underscore that realistic results can be achieved from a predictive maintenance pilot program, often significantly exceeding initial expectations. These results are consistently demonstrated when the pilot is strategically planned, meticulously executed, and its successes are clearly quantified and effectively communicated. The fundamental keys to success are selecting the right assets, establishing clear goals, and partnering with a solution that genuinely empowers your team to act decisively on actionable insights.
Conclusion: Ignite Your Reliability Transformation with a Strategic Pilot
The question "What realistic results can be achieved in a predictive maintenance pilot?" is not merely a technical curiosity; it is the fundamental gateway to unlocking transformative change within your manufacturing operations. While initial skepticism regarding downtime justification or technological complexity is understandable, a meticulously designed and executed predictive maintenance pilot program possesses the unequivocal capacity to demonstrate profound, quantifiable benefits.
By strategically focusing on critical assets, establishing clear and measurable metrics, relentlessly quantifying downtime cost avoidance, and effectively communicating success across the organisation, your pilot can provide the irrefutable evidence required to secure broader investment and decisively shift your entire operation towards a culture of proactive reliability. The ROI of predictive maintenance from a successful pilot can prove to be surprisingly rapid and exceptionally substantial.
Factory AI offers the optimal platform to achieve these realistic, impactful results within your agri-food manufacturing facility. With our proven ability to deliver "Predictive Maintenance That Pays for Itself in 6 Months," our profound understanding of your specific industry, and a solution designed for the team on the tools that seamlessly translates complex insights into actionable steps, we empower you to convert the promising potential of PdM into tangible operational excellence.
Do not allow the immense potential of enhanced reliability to remain untapped within your operations. Take the decisive first strategic step towards a future characterised by predictable operations, optimised performance, and sustained profitability.
Ready to witness the realistic and transformative results of a predictive maintenance pilot in your facility?
Book a maintenance software demo with us today to collaboratively plan your strategic pilot programme and embark on your journey to unparalleled asset reliability and profitability.
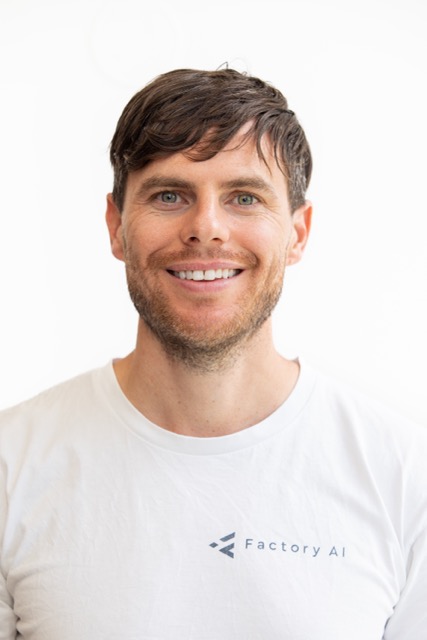