Understanding Equipment Failure Patterns and the Predictive Maintenance Advantage
Mar 13, 2025
Predictive Maintenance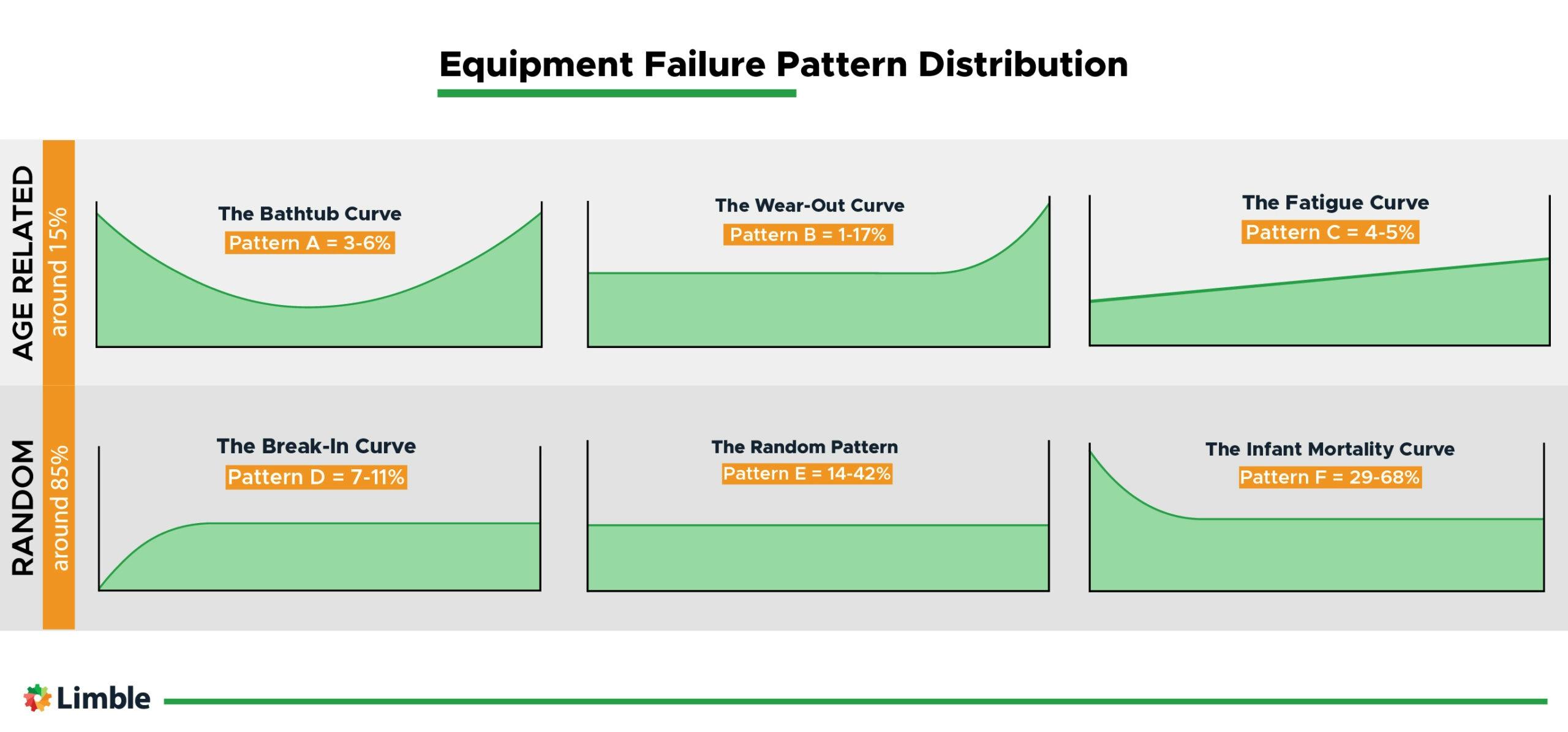
Are your manufacturing maintenance efforts heavily reliant on time-based preventive maintenance (PMs)? While easy to budget and plan, this approach often leads to unnecessary work and unexpected breakdowns because most equipment failures aren't actually age-related. This disconnect means wasted resources and a false sense of security.
The key to more efficient maintenance lies in understanding how equipment actually fails. By exploring the classic equipment failure patterns and embracing predictive maintenance, manufacturers can move beyond rigid schedules and address issues based on real-time conditions. Let's delve into these failure patterns and discover how solutions like Factory AI can transform them into opportunities for significant improvement.
Understanding Equipment Failure Patterns and the Predictive Maintenance Advantage
Most manufacturing sites today over-rely on time-based preventive maintenance (PMs). The primary reason? Time-based PMs are easy to budget for and plan. It provides a structured approach, ensuring maintenance activities are scheduled in advance. However, the reality is that most equipment failures are not age-related. This means that time-based PMs often result in unnecessary maintenance, wasted resources, and, worse—unexpected breakdowns that occur between scheduled PMs.
The fundamental challenge is that maintenance teams operate under the assumption that replacing or servicing components at fixed intervals will prevent failure. In truth, failure patterns reveal a different story. As we explore below, a significant percentage of failures follow unpredictable or non-age-related trends. This inefficiency leads to excessive costs, operational disruptions, and a false sense of security.
By understanding the patterns of equipment failure and leveraging predictive maintenance, manufacturers can break free from the inefficiencies of time-based PMs. Instead of fixing equipment on a rigid schedule, predictive maintenance focuses on actual equipment conditions, ensuring interventions happen only when necessary.
Let’s explore the six classic equipment failure patterns, how they manifest in manufacturing environments, and how predictive maintenance solutions like Factory AI’s can turn them into opportunities for improvement.
The Six Equipment Failure Patterns
Research by Nowlan and Heap (the fathers of Reliability-Centered Maintenance) identified six distinct equipment failure patterns. These patterns highlight how and when assets tend to fail—valuable insights for maintenance strategies.
Credit to Limble for this great visual. The second row is key—notice that RCM studies indicate 70–92% of failures are random, aligning with the failure patterns shown in the bottom row
1. Bathtub Curve: Infant Mortality, Useful Life, and Wear-Out (Pattern A) - 4% of Failures
The classic “bathtub curve” describes equipment with high failure rates at two points:
- Early in its lifecycle (“infant mortality” due to design flaws or poor installation).
- Late in its lifecycle (when wear and tear lead to inevitable breakdowns).
Example in Manufacturing: A newly installed conveyor system might experience teething issues from improper alignment. Over time, as it ages, motor bearings or belts may fail.
How Predictive Maintenance Helps: Our Factory AI solution identifies installation anomalies early through sensor data, ensuring reliability right from the start. As assets approach their wear-out phase, predictive models flag components nearing failure to prevent unexpected breakdowns.
2. Steady Failure Probability (Pattern B) - 5% of Failures
Some equipment maintains a constant failure probability over its lifecycle. These are often non-complex systems with predictable, uniform wear.
Example in Manufacturing: Air compressors used across production lines exhibit steady wear, with parts like filters and seals deteriorating gradually.
How Predictive Maintenance Helps: With Factory AI’s continuous monitoring, steady-state failures are predictable. Alerts guide maintenance teams to intervene just in time, avoiding unnecessary replacements and downtime.
3. Gradual Wear-Out (Pattern C) - 47% of Failures
Pattern C shows a slow increase in failure probability as equipment ages, often due to wear-and-tear mechanisms like corrosion, fatigue, or abrasion.
Example in Manufacturing: Heat exchangers in food production plants may face gradual scaling and fouling, reducing efficiency before ultimately failing.
How Predictive Maintenance Helps: Our platform analyses key performance parameters, identifying gradual efficiency losses and providing early warnings before significant wear escalates.
4. Initial Break-In Failures (Pattern D) - 7% of Failures
This pattern highlights high failure rates during initial use, stabilising as equipment "settles in."
Example in Manufacturing: Packaging machines with complex calibrations often require adjustments within the first few months of operation.
How Predictive Maintenance Helps: By monitoring equipment conditions in real-time, Factory AI ensures the right adjustments are made during break-in periods, dramatically reducing initial failure risks.
5. Sudden Failure Events (Pattern E) - 14% of Failures
Certain equipment operates flawlessly for extended periods but is prone to abrupt, catastrophic failure.
Example in Manufacturing: Gearboxes in high-load applications may operate well until a sudden misalignment or gear tooth fracture leads to complete failure.
How Predictive Maintenance Helps: Predictive analytics spots subtle indicators like vibration changes or temperature spikes, providing advanced warning before catastrophic failure occurs.
6. Random Failures (Pattern F) - 36% of Failures
Random failures occur without clear patterns or predictability, often due to external factors or manufacturing defects.
Example in Manufacturing: Electronic control systems can fail unpredictably due to surges, software glitches, or component defects.
How Predictive Maintenance Helps: While random failures are inherently difficult to predict, Factory AI mitigates their impact by ensuring spare parts availability and tracking root causes for better planning.
Since most failures are random, continuous condition monitoring makes more sense than periodic manual checks—many failures occur between scheduled rounds.
Why Understanding Failure Patterns Matters
Knowing how and when equipment is likely to fail empowers manufacturers to select the right maintenance strategy. For example:
- Pattern A assets may need rigorous commissioning processes and proactive replacements.
- Pattern C assets benefit from predictive maintenance, avoiding over-servicing.
- Pattern E assets call for advanced monitoring to detect subtle signs of impending failure.
This understanding directly impacts production reliability, cost savings, and workforce productivity.
The Predictive Maintenance Advantage
Predictive maintenance goes beyond traditional approaches by utilising real-time data and advanced analytics. Factory AI’s solution leverages IoT sensors, machine learning, and customised alerts to predict failures before they happen. Here’s how it transforms maintenance:
1. Minimising Unplanned Downtime
Unplanned downtime in the automotive industry can be up to $200K per hour, whilst in food and beverage it's more often $1K to $15K per hour. Regardless, there's now a business case in every industry given how affordable the solutions are. By predicting failures early, Factory AI helps you prevent these costly disruptions.
2. Optimising Maintenance Resources
Instead of adhering to rigid schedules, predictive maintenance focuses resources where they’re truly needed. This prevents unnecessary part replacements and reduces labour costs.
3. Extending Asset Lifespan
By catching issues early, Factory AI minimises stress on equipment, prolonging its useful life and maximising your capital investments.
4. Improving Safety and Compliance
Equipment failures can lead to unsafe conditions, especially in industries like food processing or pharmaceuticals. Predictive maintenance ensures compliance with safety standards by keeping assets in optimal condition.
Unplanned downtime on the chains in this picture can lead to massive costs. Implementing predictive maintenance in the meat industry can save a site hundreds of thousands of dollars annually.
Conclusion: Rethinking Maintenance Strategies Based on Data
The data is clear—if such a large proportion of failures are not age-related, then time-based PMs should not make up the majority of a maintenance program. Instead, the proportion of time-based PMs should align with the percentage of failures that are truly age-related. For most sites, this means a significant shift away from rigid schedules towards condition-based and predictive maintenance strategies.
Of course, some historical data is necessary to reveal when certain failure patterns emerge while others do not. However, a large portion of maintenance strategy improvement can be implemented right at the point of equipment commissioning. By ensuring that failure patterns are well understood and accounted for from the outset, manufacturers can drastically reduce inefficiencies and unplanned downtime over the asset’s lifecycle.
By adopting predictive maintenance with Factory AI, manufacturers can break free from outdated maintenance cycles, allocate resources more effectively, and ensure that interventions happen only when truly needed. This approach not only improves reliability and cost-efficiency but also positions maintenance teams as proactive problem-solvers rather than reactive firefighters.
As we like to say at Factory AI, “Better insights lead to better outcomes.” Ready to embrace predictive maintenance and take control of your operations? Let’s start the conversation today!Understanding equipment failure patterns is foundational for effective maintenance strategies. By coupling this knowledge with predictive maintenance technologies like Factory AI, manufacturers can:
- Slash unplanned downtime.
- Optimise resource allocation.
- Extend asset life.
- Ensure safety and compliance.
As we like to say at Factory AI, “Better insights lead to better outcomes.” Ready to embrace predictive maintenance and take control of your operations? Let’s start the conversation today!
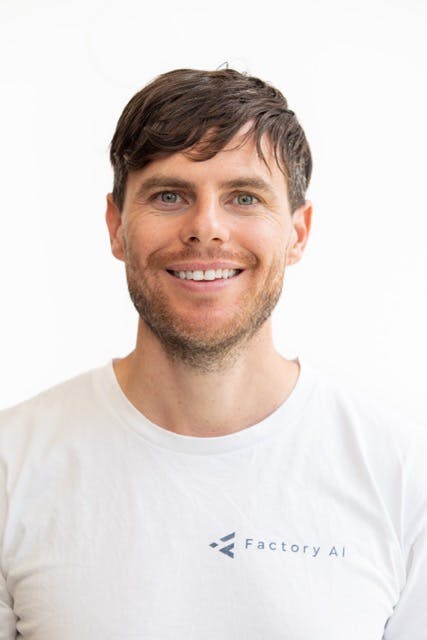
JP Picard
Jean-Philippe Picard is the CEO and Co-Founder of Factory AI. As a positive, transparent, and confident business development leader, he is passionate about helping industrial sites achieve tangible results by focusing on clean, accurate data and prioritizing quick wins. Jean-Philippe has a keen interest in how maintenance strategies evolve and believes in the importance of aligning current practices with a site’s future needs, especially with the increasing accessibility of predictive maintenance and AI. He understands the challenges of implementing new technologies, including addressing potential skills and culture gaps within organizations.