Transitioning from Preventive to Predictive Maintenance for Your HVAC Systems
Jul 16, 2025
Predictive Maintenance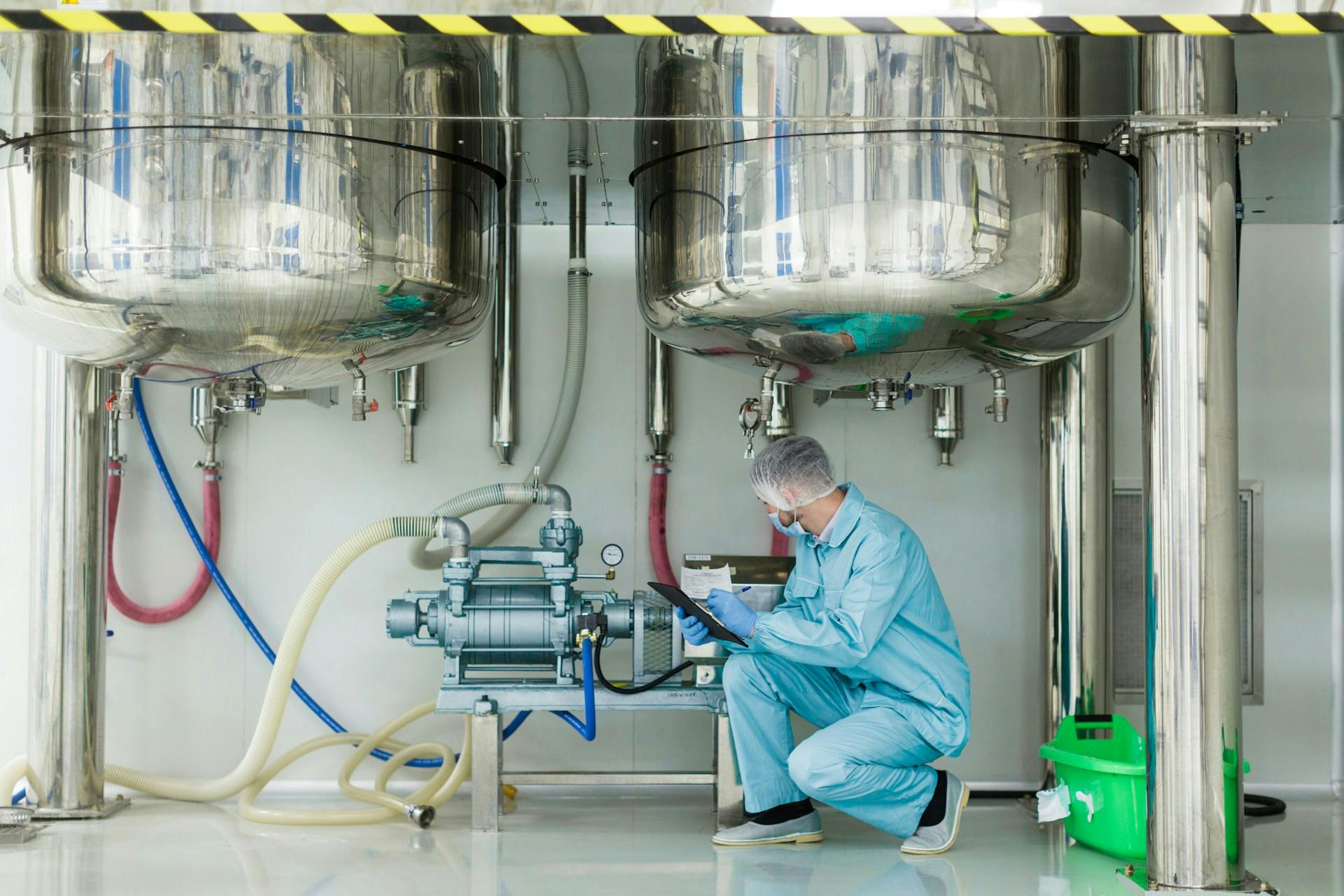
Introduction
In the intricate ecosystem of industrial manufacturing, the Heating, Ventilation, and Air Conditioning (HVAC) system is often considered a background utility – vital, yet easily overlooked until it fails. For agri-food facilities – be they dairy plants demanding precise chilling, bakeries requiring controlled humidity for dough, or seafood processing units maintaining critical cold chains and high hygiene environments – HVAC is not merely about comfort; it is a fundamental pillar of product quality, safety, regulatory compliance, and energy efficiency. While traditional preventive maintenance software has long dictated scheduled checks and routine part replacements for these complex systems, this time-based approach is increasingly proving insufficient, leading to avoidable energy waste, unexpected system failures, and costly disruptions. This article will meticulously explore the imperative of transitioning from preventive to predictive maintenance for your HVAC systems, revealing how a data-driven strategy can unlock unparalleled reliability, efficiency, and significant ROI of predictive maintenance for your operations.
The Problem: The Hidden Costs and Operational Vulnerabilities of PM-reliant HVAC
HVAC systems, comprising a complex interplay of compressors, heat exchangers, fans, blowers, and pumps, are the unsung heroes of many manufacturing processes. Their continuous operation is critical, but relying solely on preventive maintenance (PM) for these systems introduces significant vulnerabilities and hidden costs:
- Inefficient Resource Utilisation: PM schedules dictate maintenance activities based on fixed intervals (e.g., quarterly filter changes, annual pump overhauls), regardless of the actual condition of the components. This often leads to over-maintenance (replacing perfectly functional parts prematurely) or under-maintenance (missing early signs of degradation that occur rapidly between scheduled checks). Both scenarios result in wasted labour, unnecessary parts expenditure, and inefficient use of engineering resources.
- Unforeseen Failures and Costly Downtime: Despite scheduled checks, critical HVAC components can still fail unexpectedly. A sudden breakdown in a chiller's compressor can lead to massive product spoilage in a cold storage facility, or a critical air handling unit failure can compromise high hygiene environments, leading to production halts and potential regulatory non-compliance. These unplanned outages incur significant costs: lost production, wasted raw materials, idle labour, and exorbitant fees for emergency repairs and expedited spare parts.
- Energy Waste: HVAC systems are typically major energy consumers in industrial facilities. PM often fails to detect subtle, gradual declines in efficiency (e.g., a slightly fouled heat exchanger, a degrading fan bearing increasing friction). These hidden inefficiencies can silently drive up energy bills, a substantial and often overlooked operational cost.
- Compromised Product Quality and Safety: For temperature-sensitive products like dairy, baked goods, or seafood, precise environmental control is non-negotiable. HVAC system inconsistencies can lead to product spoilage, texture issues, or the growth of undesirable microorganisms. A failure to maintain air quality or pressure differentials in a sterile packaging area directly threatens HACCP and maintenance software compliance.
- Lack of Root Cause Insight: When a component fails under PM, the focus is often on replacement rather than understanding the root cause of the failure. This perpetuates recurring issues, preventing genuine long-term reliability improvements.
This pervasive reliance on scheduled maintenance frequently elicits a common objection: “We already do preventive maintenance, and it's working fine.” This perspective, while reflecting a commitment to avoiding reactive chaos, often overlooks the substantial hidden costs detailed above. It fails to recognise that "working fine" in a PM context means preventing some failures through scheduled interventions, but not optimising asset lifespan, minimising energy consumption, or proactively addressing nascent faults that could lead to significant future costs. The true "fine" for HVAC is continuous, efficient operation driven by actual condition, not just the calendar.
The Insight: Real-time Condition Data as the Master Key for HVAC Reliability
The fundamental insight underpinning the successful transition from preventive to predictive maintenance for HVAC systems is the recognition that real-time condition data is the most powerful determinant of asset health. Instead of adhering to rigid, time-based schedules that treat all components equally, PdM leverages continuous monitoring to assess the actual operational status of each individual component.
This critical shift enables organisations to:
- Anticipate Failures: Identify subtle anomalies in component behaviour that signal impending failure, often weeks or months in advance.
- Optimise Maintenance Interventions: Schedule repairs precisely when they are needed, during planned downtime, eliminating unnecessary replacements and costly emergency repairs.
- Maximise Asset Lifespan: By addressing issues early and preventing cascading damage, the useful life of expensive HVAC components is significantly extended.
- Drive Energy Efficiency: Detect and correct minor inefficiencies before they become major energy drains.
- Enhance Operational Control: Ensure consistent environmental conditions critical for product quality, safety, and compliance.
This transformation for HVAC systems is powered by advanced condition monitoring systems that combine robust sensors with intelligent analytics. It moves from merely reacting to problems or adhering to schedules to a proactive, data-driven strategy that delivers measurable improvements in efficiency, cost, and overall plant resilience. It fundamentally changes the dynamic from a guessing game to a strategic, informed approach to asset health monitoring. As Marshall Institute Blog articles consistently highlight, the move from time-based to condition-based maintenance is a hallmark of world-class reliability.
The Solution: A Phased Transition to Predictive Maintenance for HVAC Systems
The journey from a PM-centric approach to a fully integrated predictive maintenance strategy for your HVAC systems involves understanding the limitations of the old, embracing the power of new technologies, and adopting a phased roadmap. This transformation is not merely technical; it's operational and cultural.
Phase 1: Understanding the Limitations of PM for HVAC and Why PdM Excels
Traditional PM for HVAC systems typically involves a checklist approach focused on general upkeep:
- Filter Replacements: On a schedule (e.g., monthly, quarterly).
- Coil Cleaning: Annual or semi-annual washing of evaporator and condenser coils.
- Belt Tension Checks: Periodic adjustments.
- Basic Visual Inspections: Looking for obvious leaks or damage.
- Lubrication: Applying grease to fan or motor bearings.
- These tasks are typically managed using maintenance planning and scheduling software or a CMMS for manufacturing.
Why PM is Insufficient for HVAC: While these tasks are necessary, they are not sufficient for optimal HVAC reliability:
- Doesn't Detect Early Mechanical Faults: A schedule won't tell you if a fan motor's bearing is starting to degrade internally, if a compressor valve is sticking, or if a pump impeller is cavitating. These issues manifest as subtle changes in vibration, temperature, or current long before they cause a complete failure.
- Misses Gradual Efficiency Declines: PM rarely detects the slow build-up of fouling in a heat exchanger that silently drives up energy consumption, or the increasing friction in a fan motor bearing that slowly increases power draw.
- Ignores Actual Operating Conditions: PM doesn't account for variable loads, environmental factors, or sudden stress events that can accelerate wear between scheduled checks.
- Leads to Over/Under-Maintenance: Components might be replaced too soon (waste), or fail before their next scheduled check (unplanned downtime).
Addressing "We already do preventive maintenance, and it's working fine." This objection, common for HVAC, often stems from a lack of visibility into the hidden costs. While PM for HVAC prevents catastrophic failures, it does not prevent all failures, nor does it optimise performance.
- Energy Waste: A PM schedule won't reveal the significant energy wasted by a slightly misaligned fan or a partially fouled heat exchanger operating at reduced efficiency. PdM, using temperature, pressure, and power consumption monitoring, identifies these hidden energy drains.
- Unplanned Downtime (Still Occurs): PM often doesn't catch mechanical faults like compressor internal issues or motor winding degradation. A scheduled filter change won't stop a compressor from seizing due to internal wear that could have been detected by real-time vibration monitoring.
- Suboptimal Asset Lifespan: PM replaces parts based on averages. PdM ensures parts are used to their full lifespan, only replacing them when condition dictates, extending overall asset life.
- Regulatory Risk: A sudden breakdown impacting critical temperature control in a dairy cold room, for instance, could lead to product spoilage and a direct HACCP and maintenance software breach, a risk that PM can miss but PdM can mitigate.
Phase 2: Core Condition Monitoring Techniques for HVAC
Transitioning to PdM for HVAC involves deploying targeted condition monitoring techniques to gather the necessary data.
- Vibration Analysis:
- Application: Applied to virtually all rotating components in HVAC systems, including compressors, fans, blowers, and pumps, as well as their associated electric motors and gearboxes. Often involves mounting wireless condition monitoring sensors directly to bearing housings or motor casings.
- Failure Modes Detected:
- Imbalance: A common issue in fans and blowers (e.g., dirt buildup on blades) leading to excessive vibration and energy consumption.
- Misalignment: Of motors to compressors or pumps, causing undue stress on bearings and couplings, leading to premature failure.
- Bearing Wear/Degradation: The most common fault, often detected by increases in specific vibration frequencies or overall vibration levels (e.g., in fan bearings, compressor motor bearings, pump bearings).
- Looseness: Loose mounting bolts, baseplates, or internal component looseness within compressors or pumps, leading to excessive vibration.
- Gear Defects: (If applicable to a compressor or pump gearbox) Wear, cracks, or pitting in gear teeth.
- Capture Method: Real-time vibration monitoring continuously captures vibration data (acceleration, velocity, displacement). Machine learning in manufacturing then analyses changes in frequency spectra to pinpoint specific fault types and their severity, providing "pre-warning on any impending issues."
- Temperature Monitoring (Thermography & RTD/Thermocouples):
- Application: Crucial for identifying heat generation in compressors, motors (e.g., fans, blowers, pumps), heat exchangers, and electrical components. Can use thermal imaging cameras (thermography) for broad scans or permanently installed Resistance Temperature Detectors (RTDs) / thermocouples (wireless condition monitoring sensors for remote points).
- Failure Modes Detected:
- Overheating Bearings: Excessive friction from wear or insufficient lubrication in fan, blower, pump, or compressor bearings.
- Motor Winding Issues: Overload, insulation breakdown, or short circuits within electric motors.
- Electrical Faults: Loose connections, overloaded circuits, or phase imbalances in motor control centers or power distribution panels supplying HVAC units.
- Heat Exchanger Fouling/Blockage: Inefficient heat transfer indicated by abnormal temperature differentials across the exchanger (e.g., between refrigerant and water loops), leading to higher energy consumption and reduced cooling capacity.
- Refrigerant Leaks: Can manifest as abnormal temperature gradients.
- Capture Method: Thermography provides non-contact surface temperature maps. Permanently installed temperature sensors provide continuous real-time data.
- Motor Current Signature Analysis (MCSA):
- Application: Applied to the electric motors driving compressors, fans, blowers, and pumps. MCSA analyses the electrical current drawn by the motor.
- Failure Modes Detected:
- Rotor Bar Cracks/Stator Winding Issues: Direct electrical faults within the motor that impact efficiency and can lead to failure.
- Indirect Mechanical Issues: Changes in motor current can be symptomatic of mechanical problems in the driven equipment (e.g., a pump cavitating will cause load fluctuations visible in the motor current signature; a binding fan bearing will show increased current draw).
- Electrical Supply Issues: Voltage imbalance, loose connections.
- Capture Method: Non-intrusive current transformers (CTs) clip onto motor leads, providing real-time data for machine condition monitoring with AI.
- Pressure & Flow Monitoring (Process Parameters):
- Application: Crucial for assessing the performance of compressors, pumps, and heat exchangers within the HVAC system. Utilises existing process instrumentation or added predictive maintenance equipment.
- Failure Modes Detected:
- Compressor Inefficiency: Abnormal suction/discharge pressures or flow rates can indicate sticking valves, worn cylinders, or refrigerant issues.
- Pump Cavitation: Fluctuations in discharge pressure or reduced flow rate indicate a pump struggling to move fluid, often due to suction problems or internal wear.
- Heat Exchanger Fouling/Blockage: Increased pressure drop across the exchanger or reduced temperature differential indicates a build-up that impedes heat transfer, wasting energy.
- Filter Clogging: Increased pressure drop across air filters in blowers or fans indicates a need for replacement, preventing reduced airflow and increased energy use.
- Refrigerant Issues: Low pressure or abnormal temperature readings in refrigerant lines can indicate leaks or undercharging.
- Capture Method: Integration with existing PLC/SCADA systems for continuous monitoring of these parameters.
- Ultrasonics (Airborne & Structure-borne):
- Application: Highly effective for detecting leaks in pressurised systems and assessing bearing health.
- Failure Modes Detected:
- Refrigerant Leaks: Even small leaks from pipe joints, valves, or seals in compressors or heat exchangers can be pinpointed using airborne ultrasonics, preventing costly refrigerant loss and system inefficiency.
- Compressed Air Leaks: Identifies leaks in pneumatic lines and components (e.g., in blowers and associated controls) that lead to significant energy waste.
- Bearing Lubrication: Structure-borne ultrasonics can detect the distinctive sound of bearings lacking proper lubrication, allowing for timely grease application and preventing premature failure.
- Capture Method: Handheld or permanently installed ultrasonic sensors capturing high-frequency sound waves.
Phase 3: Leveraging Data with AI and Integration
The real power of these techniques is unleashed when their data is combined and intelligently analysed.
- Machine Learning in Manufacturing for Holistic HVAC Monitoring:
- ML algorithms aggregate data from multiple sensors and historical records (e.g., CMMS for food and beverage industry logs) to provide comprehensive asset health monitoring for HVAC units.
- Machine condition monitoring with AI builds a detailed "normal" profile for each specific HVAC unit, learning how its vibration, temperature, pressure, and current parameters interact under various operating loads and environmental conditions.
- This allows the AI to detect subtle, multivariate anomalies that individual threshold alarms or human inspection would miss, providing advanced "pre-warnings on any impending issues."
- Automated Anomaly Detection and Prescriptive Insights:
- The predictive maintenance software automates the complex analysis of vibration spectra, temperature trends, and MCSA signatures. This means no vibration analysis expertise required from your in-house team to understand the insights.
- The system generates clear, actionable alerts (e.g., "Compressor #2: Bearing outer race degradation, 60 days to critical failure. Recommend planned overhaul.") rather than just raw data.
- Seamless Integration with Maintenance Workflows:
- Insights from the PdM system should seamlessly feed into your existing CMMS for manufacturing or maintenance planning and scheduling software. This means an AI-triggered alert automatically creates a detailed work order, including recommended actions and necessary parts, streamlining the entire maintenance process. This ensures proactive insights lead directly to efficient action.
- Cloud-based maintenance software solutions offer remote monitoring capabilities, allowing centralised teams to monitor HVAC assets across multiple sites, a key benefit for large organisations.
- For facilities with stringent compliance, ensuring HACCP and maintenance software integration means that HVAC reliability directly supports food safety protocols.
Phase 4: The Transition Roadmap for HVAC Maintenance
Transitioning requires a systematic approach, often beginning with a pilot and scaling based on demonstrated success.
- Pilot Program for Critical HVAC Units:
- Start with a predictive maintenance pilot program on a select number of your most critical HVAC assets (e.g., the chiller compressor supporting your main cold room, a critical air handling unit for a high-hygiene area).
- Define clear KPIs for the pilot, focusing on ROI of predictive maintenance through avoided downtime, energy savings, or reduced PM costs for these specific units.
- Select assets where wireless condition monitoring sensors can be easily installed and where clear "before" data is available.
- Build Internal Buy-in with Quantifiable Results:
- Meticulously track the pilot's performance. Document every avoided breakdown, every instance of identified energy waste, and every extension of asset life.
- Quantify the downtime cost avoidance in Australian Dollars (e.g., "A$50,000 saved by averting chiller breakdown").
- Present these results clearly to all stakeholders (maintenance, operations, finance, IT, quality), demonstrating how the predictive maintenance software delivers tangible value and, for example, "Pays for Itself in 6 Months."
- Leverage Factory AI's Strengths for a Smooth Transition:
- Rapid ROI: Our focus on delivering "Predictive Maintenance That Pays for Itself in 6 Months" provides compelling financial justification for HVAC investment.
- Industry Focus: Being "Built for the Agri-Food Industry," we understand the unique demands of HVAC in your sector, from high hygiene environments to cold chain integrity.
- Simplified IT: Our ability to "Work Without Wi-Fi or IT Integration" streamlines deployment by addressing a major IT and security concern, making new predictive maintenance equipment easy to adopt.
- User-Centric Design: "No Vibration Analysis Expertise Required" and a system "Designed for the Team on the Tools" ensure rapid adoption and effective use by your existing maintenance staff for all HVAC components.
- Comprehensive Solution: As "More Than Predictive – A Full Reliability Platform," Factory AI integrates PdM for HVAC with broader CMMS capabilities and maintenance planning and scheduling software, providing a holistic approach to reliability management.
- Expert Foundation: Our solutions are "Built by Engineers Who’ve Worked on the Plant Floor," ensuring practical, real-world effectiveness for your HVAC systems.
Real-World Examples: PdM for HVAC in Agri-Food Manufacturing
Implementing predictive maintenance for HVAC systems yields substantial and diverse benefits across the agri-food sector. These predictive maintenance case studies illustrate how specific condition monitoring techniques address common HVAC failure modes.
Example 1: Cold Storage Facility – Avoiding Product Spoilage
- Problem: A major cold storage facility, crucial for frozen food distribution, relied on annual PM for its large industrial refrigeration compressors. Despite this, they experienced a costly, unexpected compressor bearing failure that led to a two-day system shutdown, resulting in significant A$50,000 in spoiled product and A$20,000 in emergency repairs.
- PdM Solution: The facility transitioned to predictive maintenance software, deploying wireless condition monitoring sensors for real-time vibration monitoring and temperature monitoring on all compressors and their associated motors. Machine learning in manufacturing analysed this data.
- Result: The system detected a subtle increase in vibration amplitude and a gradual rise in bearing temperature on a critical compressor motor, indicative of early bearing degradation. This insight, generated with no vibration analysis expertise required, allowed the maintenance team to schedule a bearing replacement during a planned 6-hour power-down. This proactive intervention averted a catastrophic failure, saving the A$70,000 in spoilage and emergency costs, and ensuring unbroken cold chain integrity for their perishable goods.
Example 2: Large Industrial Bakery – Optimising Energy and Quality
- Problem: A large industrial bakery, where precise temperature and humidity control in proofing rooms and ovens are critical for product quality, was experiencing fluctuating energy bills and occasional quality deviations related to inconsistent HVAC performance. Their existing PM involved only basic filter changes and coil cleaning, missing deeper inefficiencies.
- PdM Solution: The bakery adopted predictive maintenance for FMCG focused on its large blowers supplying conditioned air to proofing rooms and the recirculation fans in its ovens. Wireless condition monitoring sensors were installed for real-time vibration monitoring on fan and blower motors, combined with temperature sensors on bearings. Process parameter monitoring captured airflow rates and differential pressures across heat exchangers.
- Result: The machine condition monitoring with AI detected a slight imbalance in a key blower fan, which was gradually increasing energy consumption due to excess vibration. It also flagged a subtle increase in differential pressure across an oven's heat exchanger, indicating fouling. By scheduling precise blower rebalancing and heat exchanger cleaning based on these insights, the bakery achieved a 12% reduction in HVAC energy consumption for these units and significantly improved temperature and humidity consistency, leading to a 5% reduction in product rework related to dough quality.
Example 3: Dairy Processing Plant – Ensuring Hygiene and Uptime
- Problem: A dairy plant relied on its HVAC system to maintain specific air pressures and temperatures in its sterile filling areas, crucial for high hygiene environments and HACCP and maintenance software compliance. An unexpected failure of a main air handling unit's fan motor almost compromised a batch, costing A$25,000 in discarded product and an emergency repair team.
- PdM Solution: The plant implemented predictive maintenance for dairy plants for their main air handling units. This included wireless condition monitoring sensors on fan motors and bearings for real-time vibration monitoring, MCSA on the fan motors, and temperature probes. They also used ultrasonics to check for small leaks in their chilled water pump lines supplying the cooling coils.
- Result: The predictive maintenance software detected abnormal peaks in the fan motor's current signature, correlating with increasing vibration levels, indicating developing rotor bar issues. Separately, the ultrasonics revealed a small but persistent leak in a chilled water line. Both issues were addressed during a planned shutdown window. The proactive intervention averted a critical motor failure and maintained optimal sterile conditions, ensuring continuous HACCP compliance and saving the cost of batch spoilage and emergency repairs. This demonstrated substantial downtime cost avoidance.
Example 4: Pet Food Production Facility – Protecting Product and Workforce
- Problem: A pet food production facility needed to maintain specific air quality in its packaging areas to prevent airborne contaminants and ensure a safe environment for operators. Their exhaust blowers were vital. A previous unexpected breakdown of an exhaust blower led to a temporary shutdown of the packaging line due to dust accumulation, causing several hours of idle labour and a minor safety concern.
- PdM Solution: The facility installed wireless condition monitoring sensors on their critical exhaust blowers for real-time vibration monitoring and temperature sensing, and monitored motor current via MCSA.
- Result: The machine condition monitoring with AI system detected an unusual spike in vibration coupled with a minor increase in current draw for one blower motor. The predictive maintenance software alerted the team to a likely issue with the blower impeller or associated bearing. By scheduling a proactive inspection during a planned short break, they discovered and rectified a minor imbalance caused by material build-up on the impeller blades. This prevented a complete blower failure, ensuring continuous air quality, safeguarding product integrity, and maintaining a safe working environment without incurring additional "idle labour costs."
These specific examples illustrate how tailored condition monitoring techniques, integrated with intelligent analysis, provide realistic results in a predictive maintenance pilot program for HVAC systems, leading to significant operational and financial benefits for agri-food manufacturers.
Conclusion: Elevate Your HVAC Reliability with Predictive Power
The era of solely relying on reactive measures or rigid preventive maintenance software for critical HVAC systems is rapidly becoming obsolete. For agri-food manufacturers, where HVAC directly impacts product quality, safety, energy consumption, and overall operational efficiency, the transition from preventive to predictive maintenance for your HVAC systems is not merely an option; it is a strategic imperative.
By embracing predictive maintenance software and leveraging advanced condition monitoring techniques – such as real-time vibration monitoring, temperature analysis, MCSA, pressure monitoring, and ultrasonics – organisations can gain unprecedented foresight into the health of their compressors, heat exchangers, fans, blowers, and pumps. This allows for precise, condition-based interventions that eliminate costly unplanned downtime, drive significant ROI of predictive maintenance, and optimise energy usage.
Factory AI stands ready to guide your organisation through this crucial transition. Our solution:
- Delivers "Predictive Maintenance That Pays for Itself in 6 Months," providing rapid financial justification for your HVAC investment.
- Is "Built for the Agri-Food Industry," deeply understanding the unique HVAC demands of high hygiene environments and HACCP and maintenance software compliance.
- Simplifies deployment by being able to "Work Without Wi-Fi or IT Integration," addressing common IT/security concerns for predictive maintenance equipment.
- Empowers your existing team with machine condition monitoring with AI that requires no vibration analysis expertise required, making insights actionable for your technicians.
- Offers a holistic approach as "More Than Predictive – A Full Reliability Platform," integrating HVAC insights with broader CMMS capabilities and maintenance planning and scheduling software.
- Is "Designed for the Team on the Tools" and "Built by Engineers Who’ve Worked on the Plant Floor," ensuring practical effectiveness.
Don't let your HVAC systems remain a source of costly surprises or hidden inefficiencies. Embrace the power of predictive maintenance to transform them into reliable, energy-efficient assets that consistently support your core operations.
Ready to explore the realistic and transformative results of transitioning your HVAC systems to predictive maintenance?
Book a maintenance software demo with us today to begin your journey towards unparalleled HVAC reliability and operational excellence.
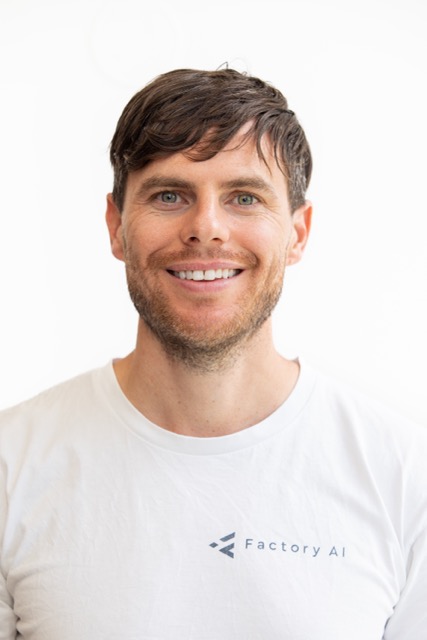