The Ultimate Guide to Forklift Maintenance: From Daily Checks to AI-Powered Reliability
Jul 17, 2025
forklift maintenance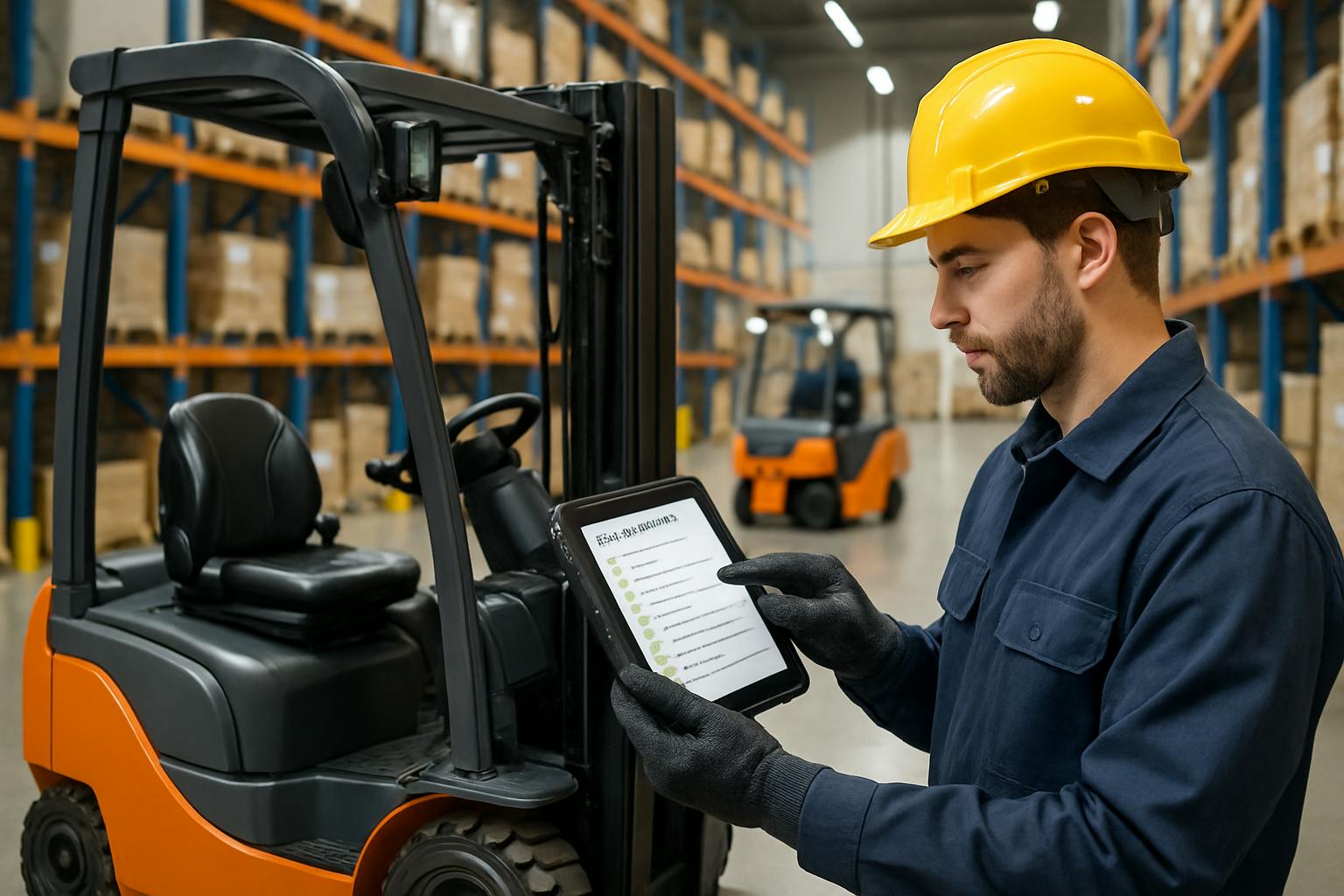
In the intricate ballet of modern logistics, manufacturing, and warehousing, the forklift is the undisputed workhorse. These powerful machines are the lifeblood of the supply chain, moving tons of material with precision and speed. Yet, this constant, demanding work takes its toll. A neglected forklift isn't just an inefficient tool; it's a ticking time bomb of catastrophic failure, a major safety hazard, and a drain on your bottom line.
In 2025, a reactive, "fix-it-when-it-breaks" approach to forklift maintenance is no longer viable. It's a relic of a less efficient, less safe, and less competitive era. A strategic, data-driven maintenance program is not a cost center—it's a powerful engine for operational excellence, safety, and profitability.
This comprehensive guide will walk you through every facet of modern forklift maintenance. We'll move beyond basic checklists to explore the tiered strategies of maintenance maturity, from essential preventive tasks to the game-changing power of AI-driven prescriptive analytics. Whether you manage a fleet of five or five hundred, this is your blueprint for building a world-class forklift maintenance program that drives results.
Why a Strategic Approach to Forklift Maintenance is Non-Negotiable in 2025
For too long, maintenance has been viewed through a narrow lens of immediate cost. However, seasoned facility operators and maintenance managers understand the truth: the cost of a well-executed maintenance program pales in comparison to the staggering costs of neglect.
Beyond the Basics: The True Costs of Neglect
The sticker price of a repair is just the tip of the iceberg. The hidden costs of poor forklift maintenance can cripple an operation.
- Crippling Downtime: When a critical forklift goes down, the entire workflow can grind to a halt. Consider a simple calculation: If a single forklift is responsible for loading trucks and its downtime halts shipments, the cost isn't just the technician's time. It's the cost of delayed orders, potential contract penalties, idle labor for drivers and loaders, and damage to customer relationships. A conservative estimate of downtime cost can be several thousand dollars per hour in a busy facility.
- Safety, Compliance, and Liability: This is the most critical factor. According to the Occupational Safety and Health Administration (OSHA), forklift accidents cause approximately 85 fatalities and 34,900 serious injuries each year. Many of these are directly attributable to mechanical failure. The OSHA standard 1910.178 explicitly mandates that forklifts be inspected daily or after each shift and that any vehicle found to be in need of repair is taken out of service. Failure to comply can result in severe fines, litigation, and irreparable damage to your company's reputation.
- Reduced Asset Lifespan: A well-maintained forklift can provide reliable service for over 20,000 hours. A neglected one might fail catastrophically at half that, forcing premature capital expenditure on a replacement. Proactive maintenance maximizes the return on your significant asset investment.
- Spiraling Repair Costs: A small, undetected hydraulic leak can eventually lead to a complete pump failure. A worn chain that isn't caught early can snap under load, destroying the mast and the cargo. Reactive maintenance is almost always more expensive than proactive maintenance because it deals with secondary damage and requires emergency parts procurement and overtime labor.
The Compelling ROI of Proactive Maintenance
Investing in a strategic maintenance program isn't an expense; it's an investment with clear, measurable returns.
- Maximized Uptime and Productivity: Reliable equipment means predictable operations. When your team can trust their forklifts to perform, you can meet production schedules, optimize labor, and maintain a smooth flow of materials through your facility.
- A Culture of Safety: A visible, robust maintenance program sends a clear message to your operators: their safety is a priority. This boosts morale, encourages operators to report minor issues before they become major hazards, and reduces the risk of life-altering accidents.
- Extended Asset Life & Lower TCO: By systematically replacing worn components, maintaining fluid integrity, and preventing catastrophic failures, you dramatically extend the useful life of your forklifts. This lowers the Total Cost of Ownership (TCO) by deferring new equipment purchases and reducing the frequency of major overhauls.
- Enhanced Operational Efficiency: A properly tuned forklift consumes less energy (whether it's fuel or battery power), operates more smoothly, and is easier for the operator to handle, leading to faster, more precise work with less product damage.
The Four Tiers of Forklift Maintenance: From Reactive to Prescriptive
Not all maintenance strategies are created equal. Understanding where your organization currently stands on the maintenance maturity curve is the first step toward improvement. In 2025, leading organizations are rapidly moving up this ladder.
Tier 1: Reactive Maintenance ("Run-to-Failure")
This is the most primitive strategy. Maintenance is only performed when the forklift breaks down.
- The Approach: No scheduled inspections, no preventive tasks, no condition monitoring. The philosophy is "if it ain't broke, don't fix it."
- The Reality: This approach is incredibly costly and dangerous for critical equipment like forklifts. It guarantees maximum downtime, highest repair costs due to secondary damage, and an unacceptably high risk of safety incidents. In the context of OSHA regulations, a purely reactive strategy is non-compliant.
- Example: A forklift's mast chain is never inspected. Over time, it stretches beyond its service limit. One day, while lifting a heavy pallet, the chain snaps. The load crashes down, destroying thousands of dollars in product, damaging the forklift's mast, and narrowly missing the operator. The facility is now facing an OSHA investigation, a costly repair, and significant downtime.
Tier 2: Preventive Maintenance (The Foundation of Reliability)
This is the essential starting point for any serious maintenance program. Maintenance tasks are performed at pre-determined intervals (based on time or usage hours) to reduce the likelihood of failure.
-
The Approach: Follow a schedule. This includes daily checks by operators and more intensive servicing by technicians at regular intervals (e.g., every 250, 500, or 1000 hours).
-
The Daily Operator Checklist (Pre-Shift Inspection): This is a non-negotiable safety and reliability practice. Before every shift, the operator must perform a walk-around inspection. A robust digital or paper checklist should include:
- Forks & Mast: Check for cracks, bends, or excessive wear. Inspect chains for broken links and proper tension. Check rollers for smooth movement.
- Tires & Wheels: Check for proper inflation (for pneumatic tires), and look for cuts, gouges, or embedded objects. For cushion tires, check for chunking or excessive wear. Ensure lug nuts are tight.
- Fluid Levels: Check engine oil, hydraulic fluid, coolant, and brake fluid. For electric forklifts, check battery water levels.
- Safety Devices: Test the horn, lights (headlights, tail lights, warning lights), and backup alarm.
- Operator Compartment: Check seatbelt for function, ensure controls are labeled and working, and check for debris on the floor plate.
- Brakes: Test service and parking brakes for proper operation.
- Leaks: Look under the forklift for any signs of oil, coolant, or hydraulic fluid leaks.
-
The Scheduled PM Plan: This is where technicians perform deeper maintenance based on the OEM's recommendations and your operating conditions.
- 250-Hour Service: Typically includes an engine oil and filter change (for IC models), chassis lubrication, mast and chain lubrication, and inspection of key systems like brakes and steering.
- 500-Hour Service: Includes all 250-hour tasks plus changing the fuel filter and air filter, and a more thorough inspection of the drive train and hydraulic system.
- 2000-Hour Service: A major service that includes all previous tasks plus changing hydraulic fluid, transmission fluid, and differential fluid. It often involves a detailed inspection and adjustment of lift chains, mast bearings, and brake systems.
Managing these schedules, ensuring compliance, and documenting work is impossible at scale without a digital system. Standardizing these tasks using a platform with features for PM procedures ensures every technician performs the job to the same high standard, every time.
Tier 3: Predictive Maintenance (The Data-Driven Leap)
Preventive maintenance is good, but it can be inefficient. You might change a part that still has 50% of its life left, or a part might fail before its scheduled replacement. Predictive Maintenance (PdM) solves this by using condition-monitoring technology to predict failures before they happen.
- The Approach: Instead of relying on a calendar, you rely on data. "Listen" to your equipment to understand its actual health.
- Key PdM Technologies for Forklifts:
- Telematics: This is the most common and powerful source of data for forklift fleets. Modern forklifts are equipped with telematics systems that track engine hours, fault codes, impact events (collisions), fuel consumption, and battery status. A sudden spike in impacts from a specific operator could indicate a need for retraining, while recurring fault codes can point to an emerging mechanical issue.
- Vibration Analysis: By placing sensors on key components like the engine, transmission, or wheel bearings, you can establish a baseline vibration signature. Deviations from this baseline can indicate problems like bearing wear, imbalance, or misalignment long before they become audible or cause a failure.
- Oil Analysis: Regularly taking small samples of engine oil, hydraulic fluid, and transmission fluid and sending them to a lab can reveal the internal health of a component. The presence of metal particles, coolant, or fuel in the oil is a clear indicator of specific types of wear or seal failure.
- Thermal Imaging: Using an infrared camera, technicians can quickly scan for hotspots in electrical panels, connectors, and motors. An abnormally hot component is a sign of high resistance or impending failure, allowing for a simple fix (like tightening a connection) to prevent a major one (like a fire).
Tier 4: Prescriptive Maintenance (The Future is Now)
This is the pinnacle of maintenance strategy, representing a true partnership between human expertise and artificial intelligence. It goes one step beyond prediction.
- The Approach: Prescriptive Maintenance (RxM) doesn't just tell you a component is going to fail; it tells you why it's failing, what the best course of action is, and how to execute that action with minimal operational impact.
- How It Works: An advanced AI predictive maintenance engine synthesizes data from all sources—telematics, vibration sensors, oil analysis, work order history from your CMMS, and even parts inventory levels. It uses machine learning models to identify complex patterns that a human analyst could miss.
- A Prescriptive Recommendation: Instead of a simple alert like "High vibration on Forklift #12's drive motor," a prescriptive system would provide a complete recommendation:
"Alert: Forklift #12's drive motor bearing shows a 95% probability of failure within the next 75 operating hours. Root cause analysis indicates chronic overloading based on recent telematics data. Recommendation: 1) Replace the bearing (Part #789-ABC). 2) Review operator logs and provide refresher training on load capacity limits. 3) Schedule this 2-hour repair during the upcoming planned maintenance window on Saturday to avoid production disruption. Part #789-ABC is in stock at the main storeroom, bin location C4."
This level of insight, delivered through prescriptive maintenance platforms, transforms the maintenance department from a reactive fire-fighting unit into a strategic business partner that proactively optimizes asset health and operational planning.
Building Your Forklift Maintenance Program: A Step-by-Step Guide
Transitioning to a proactive maintenance culture requires a structured plan. Follow these steps to build a robust and effective program.
Step 1: Asset Inventory and Criticality Analysis
You can't manage what you don't measure. The first step is to get a complete picture of your fleet.
- Create an Asset Registry: For every forklift, document key information: make, model, serial number, year of manufacture, in-service date, fuel type (electric, propane, diesel), and capacity.
- Assign a Unique Identifier: Give each forklift a clear, visible ID number (e.g., FL-01, FL-02). This is crucial for tracking work orders and costs.
- Perform a Criticality Analysis: Not all forklifts are equally important. Rank each asset based on its impact on production if it were to fail. A forklift that unloads all incoming raw materials is more critical than one used for occasional tasks. This ranking helps you prioritize PM schedules and sensor deployments.
A modern approach uses dedicated asset management software to house this information, making it accessible to everyone who needs it and linking it directly to maintenance histories and costs.
Step 2: Develop Standardized PM Checklists and Procedures
Consistency is key to quality maintenance.
- Start with the OEM Manual: The manufacturer's service manual is your primary source for recommended maintenance tasks and intervals.
- Customize for Your Environment: A forklift operating in a dusty cement plant will need its air filters changed more frequently than one in a clean food-grade facility. A forklift in a cold storage freezer will have different lubrication and battery requirements. Adjust your PMs to match your specific operating conditions.
- Create Clear, Actionable Checklists: Develop detailed, step-by-step procedures for each PM task. Use clear language and include photos or diagrams where possible. This ensures that whether your senior technician or a new hire is doing the job, it's done correctly and consistently.
Step 3: Choosing the Right Tools and Technology
Arming your team with the right tools is essential for efficiency and effectiveness.
- The Digital Foundation (CMMS): In 2025, spreadsheets and clipboards are obsolete for managing maintenance. A Computerized Maintenance Management System (CMMS) is the central nervous system of your program. It allows you to:
- Schedule and automatically assign PM work orders.
- Track all reactive maintenance work.
- Manage spare parts inventory.
- Store all asset history and documentation.
- Generate reports on key performance indicators (KPIs).
- Essential Diagnostic and Hand Tools: Your technicians need a well-stocked toolkit, including:
- A quality set of torque wrenches.
- A digital multimeter for electrical diagnostics.
- Hydraulic pressure gauges.
- A chain wear gauge.
- Grease guns and other lubrication equipment.
- A thermal imaging camera (increasingly affordable and invaluable).
Step 4: Training and Empowering Your Team
The most advanced system is useless without trained people to run it.
- Operator Training: Train every operator not just on how to drive the forklift, but on how to perform the daily inspection thoroughly. Empower them to take a forklift out of service if they find a safety issue.
- Technician Training: Invest in continuous training for your maintenance technicians. This includes OEM-specific training, as well as training on new technologies like vibration analysis or using the mobile CMMS effectively on the shop floor.
- Foster a Reliability Culture: Leadership must champion the importance of maintenance. When managers prioritize PMs over short-term production demands and celebrate proactive catches by operators and technicians, it creates a culture where everyone takes ownership of equipment reliability.
Step 5: Tracking KPIs and Continuous Improvement
A successful program is a data-driven one. Track these key metrics to measure your performance and identify areas for improvement.
- PM Compliance: What percentage of scheduled PMs are completed on time? Aim for >95%.
- Mean Time Between Failures (MTBF): The average time a forklift operates before it breaks down. Your goal is to continuously increase this number.
- Mean Time To Repair (MTTR): The average time it takes to repair a forklift after it fails. Your goal is to reduce this through better diagnostics, parts availability, and technician skill.
- Maintenance Cost per Operating Hour: This KPI helps you understand the true cost of running each asset and identify "bad actor" forklifts that may be due for replacement.
Use the reporting features in your CMMS to visualize these trends. As noted by experts at Reliabilityweb, tracking these KPIs is fundamental to shifting from a cost center to a value-adding function.
Common Forklift Problems and Troubleshooting Guide
Even with a great PM program, issues can arise. Here’s a quick guide to diagnosing common problems.
Problem: Forklift Won't Start
- Possible Causes:
- All Types: Dead or disconnected battery, faulty ignition switch, operator not seated (safety switch), neutral safety switch not engaged.
- IC Engine: No fuel, clogged fuel filter, faulty spark plugs or starter motor.
- Electric: Battery connector not seated properly, emergency disconnect activated, low battery charge.
- Troubleshooting Steps:
- Ensure the operator is seated and the gear selector is in neutral.
- Check the emergency disconnect button.
- Check battery terminals for corrosion and tightness. Test battery voltage.
- For IC engines, check the fuel level and listen for the fuel pump priming.
Problem: Mast/Lifting Issues (Won't lift, slow, or jerky)
- Possible Causes: Low hydraulic fluid, clogged hydraulic filter, air in the hydraulic lines, damaged or kinked hydraulic hoses, worn or damaged lift chains, faulty mast rollers.
- Troubleshooting Steps:
- With the forks lowered, check the hydraulic fluid level.
- Inspect all visible hoses for leaks or damage.
- Visually inspect lift chains for signs of rust, corrosion, or stretched links. Use a chain wear gauge for accurate measurement.
- Watch the mast rollers as it lifts—they should roll smoothly, not slide.
Problem: Steering is Difficult or Unresponsive
- Possible Causes: Low power steering fluid (if equipped), low tire pressure (especially on rear wheels), worn steering linkage components (tie rods, kingpins), mechanical binding in the steering column.
- Troubleshooting Steps:
- Check tire pressures and adjust as needed.
- Check the power steering fluid level.
- Safely jack up the steering axle and check for excessive play in the wheels and linkage.
Problem: Brakes are Spongy, Weak, or Not Working
- Possible Causes: Air in the brake lines, low brake fluid, worn brake shoes/pads, leaking wheel cylinder, out-of-adjustment brakes.
- Troubleshooting Steps:
- Check the brake fluid level in the master cylinder.
- Look for any signs of fluid leaks around the wheels.
- If the pedal feels spongy, the system may need to be bled to remove air.
- Listen for grinding or squealing sounds, which indicate worn brake components.
Electric vs. Internal Combustion (IC) Forklifts: Maintenance Differences
Your maintenance plan must be tailored to the type of forklift in your fleet.
Maintaining Electric Forklifts
Electric forklifts are simpler mechanically but require rigorous attention to their power source.
- The Battery is Everything: The lead-acid battery is the heart and the most expensive component of an electric forklift. Proper care is paramount.
- Watering: Check water levels after charging, not before. Use distilled or deionized water. Over- or under-watering can destroy a battery.
- Charging: Avoid "opportunity charging" (plugging it in during short breaks) unless the forklift has a battery designed for it. Complete a full charge cycle whenever possible.
- Equalization: Perform a weekly or bi-weekly equalization charge to balance the voltage across all cells.
- Cleaning: Keep the top of the battery clean and dry to prevent self-discharge and corrosion.
- Electric Motors: AC motors are virtually maintenance-free. Older DC motors require periodic inspection of brushes and commutators for wear.
- Electrical System: Keep controllers and connectors clean and dry. Regularly inspect cables for fraying or damage.
Maintaining Internal Combustion (IC) Forklifts
IC forklifts (propane, gasoline, or diesel) have maintenance needs similar to a car but in a much more demanding environment.
- Engine Systems: This is the primary focus. Regular oil and filter changes are critical to combat the heat and stress of industrial use. Air filters often need frequent replacement due to dusty warehouse conditions.
- Cooling System: The radiator, hoses, and coolant must be kept in top condition. Overheating is a common cause of major engine damage. Keep radiator fins clean of dust and debris.
- Fuel System (Propane): Regularly inspect propane tank brackets, hoses, and fittings for leaks or damage. A propane leak in an enclosed space is a severe explosion hazard.
- Exhaust & Emissions: A faulty exhaust can leak dangerous carbon monoxide into the workplace. This is a critical safety inspection point. As OSHA warns, carbon monoxide from IC forklifts is a silent and deadly hazard that proper maintenance can mitigate.
Conclusion: Elevate Your Operations Through Maintenance Excellence
Forklift maintenance in 2025 is no longer a back-office function. It is a strategic imperative that directly impacts your company's safety, productivity, and profitability. By moving away from a reactive mindset and embracing a proactive, data-driven strategy, you can transform your forklift fleet from a potential liability into a reliable, high-performing asset.
The journey from basic preventive maintenance to the predictive and prescriptive realms is a tangible path to operational excellence. It begins with building a solid foundation: detailed asset knowledge, standardized procedures, and a well-trained team. It accelerates with the adoption of modern tools like a CMMS to automate, track, and analyze every aspect of your program. And it culminates in the use of AI and condition monitoring to achieve unprecedented levels of reliability and foresight.
Don't wait for the next breakdown or safety incident to re-evaluate your approach. The tools and strategies are here. The time to build a safer, more efficient, and more profitable future through maintenance excellence is now.
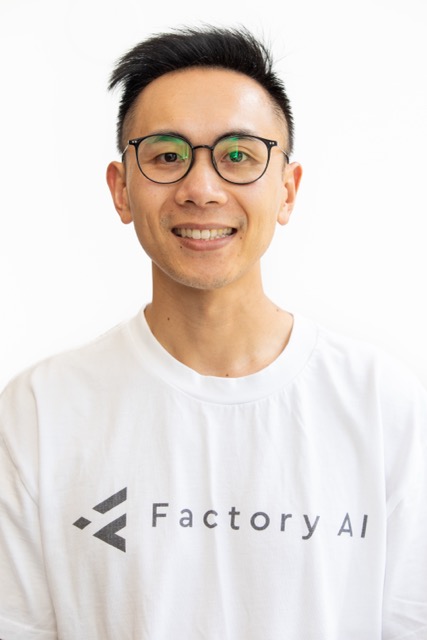