The State of Vibration Monitoring in 2025
Jul 18, 2025
Vibration Monitoring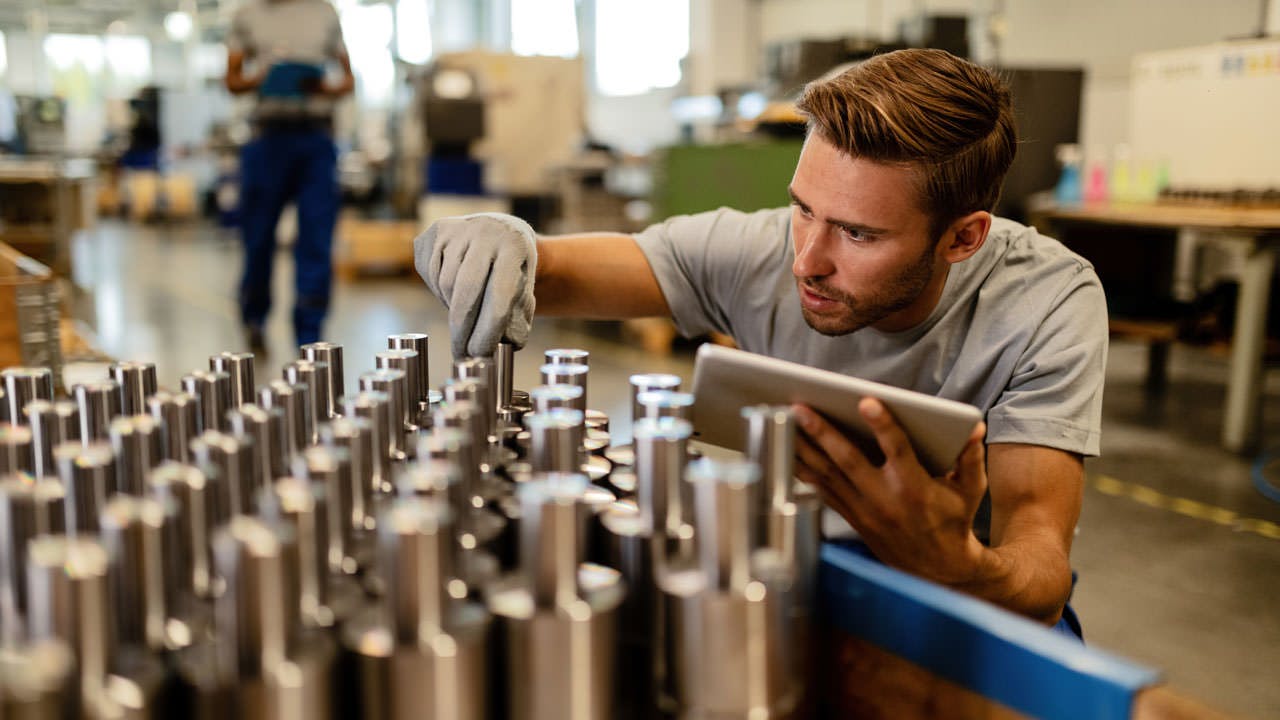
I. Executive Summary
Vibration monitoring, a fundamental pillar of industrial asset health, is undergoing a profound transformation, driven by advancements in sensor technology, sophisticated data analytics, and the pervasive integration of artificial intelligence. In 2025, the landscape is characterized by a definitive shift towards proactive, predictive maintenance strategies, moving beyond traditional reactive or time-based approaches. This evolution is not merely incremental but represents a fundamental re-evaluation of operational paradigms.
The market for vibration sensors is experiencing robust growth, with the overall global vibration sensor market projected to reach USD 7.05 billion in 2025, expanding to USD 13.25 billion by 2034 with a Compound Annual Growth Rate (CAGR) of 7.27%. Specifically, the wireless vibration sensor market is anticipated to achieve a valuation of USD 1.50 billion in 2025, with a CAGR of 5.2% from 2025 to 2034, reaching USD 2.37 billion.1 This significant growth is primarily fueled by the increasing adoption of Industrial Internet of Things (IIoT) principles and the imperative for real-time condition monitoring across diverse industrial sectors, including manufacturing, automotive, aerospace, and energy.1
Wireless vibration sensors are emerging as the dominant force in this evolving market. They are overcoming the traditional limitations of wired systems through enhanced scalability, ease of installation, and inherent cost-effectiveness, particularly for large-scale deployments.1 The seamless integration of these wireless data collection points with advanced AI-powered platforms, such as Factory AI’s Predictive Maintenance software, is revolutionizing how industries predict and prevent machinery failures. This integrated approach leads to substantial reductions in unplanned downtime, significant cost savings, and a marked improvement in overall operational efficiency and safety.6 The current trajectory indicates that the future of industrial maintenance will be increasingly intelligent, automated, and driven by comprehensive, real-time vibration data.
II. Introduction: The Evolving Landscape of Vibration Monitoring in 2025
Brief History and Fundamental Principles of Vibration Monitoring
The practice of vibration monitoring, while seemingly a modern innovation, traces its origins back to the early 1900s. The first iterations were large mechanical devices, primarily conceived for the automotive industry to measure tractive and brake effort. These rudimentary instruments relied on physical tracing pens and clockwork-driven drums to record movements, a stark contrast to the digital precision and computational power available today.8 Prior to these inventions, the only method for assessing acceleration was through simple observation, highlighting the significant leap these early mechanical monitors represented.8
The true dawn of modern vibration monitoring, however, arrived in the mid-1970s. This period was marked by the widespread adoption of minicomputers and the maturation of the Fast Fourier Transform (FFT) algorithm, along with related signal processing mathematics. These technological advancements, often borrowed from other fields, rapidly gave rise to a new class of digital closed-loop controllers. Unlike their predecessors, these systems were capable of running multiple types of tests, including sine, random, and shock analyses, offering unprecedented flexibility and superior control. This digital revolution also enhanced the presentation, retention, and communication of test results, laying the groundwork for the sophisticated analysis capabilities available today.9 This transition marked a profound shift from rudimentary observation to a scientific, data-driven approach to understanding machine health.
At its core, vibration monitoring functions on the principle that vibration is one of the most critical, yet often overlooked, indicators of machine health. From the moment a machine begins operation, it accumulates wear, which manifests as subtle, then increasingly pronounced, changes in its vibration patterns.11 The primary purpose of this monitoring is to detect common faults in rotating equipment, such as imbalance, misalignment, looseness, and bearing wear, through their characteristic vibration signatures.11 Modern monitoring systems typically measure vibrations along three axes—vertical (z) and two perpendicular horizontal (x and y) axes—to provide a comprehensive understanding of structural movement and energy propagation.12
Vibration can be measured and analyzed in three primary ways: displacement, velocity, and acceleration. Displacement refers to the distance an object moves from a reference point, best suited for measuring low frequencies, often using proximity probes.11 Velocity, representing the distance an object moves over time, is optimal for mid-frequency measurements and can be captured by velocity probes.11 Acceleration, the rate of change in velocity over time, is ideal for very high frequencies and is commonly measured using accelerometers, which are stable and have no moving parts, making them widely used.11 The real-time capability of these monitoring systems is crucial, enabling immediate assessment of vibration amplitude and dominant frequency against predefined limits. When these limits are exceeded, systems can trigger alerts via SMS, email, or visual/auditory alarms, prompting immediate action to prevent potential damage to surrounding structures or critical assets.12 This capability underscores a fundamental shift in maintenance philosophy.
Historically, maintenance was largely reactive, addressing issues only after a breakdown occurred, or preventive, based on fixed schedules regardless of actual machine condition. Early vibration monitoring, while a significant advancement, still largely supported a preventive model by identifying issues that would then be addressed during scheduled repair windows. The introduction of technologies like FFT and digital signal processing allowed for a more detailed analysis of machine behavior, pushing the industry towards condition-based monitoring. This evolution has culminated in the current embrace of predictive maintenance (PdM), where service is performed based on the actual condition of each machine and forecasts of future failure, rather than a rigid timeline.11 This represents a fundamental transformation in maintenance strategy, moving from simply reacting to failures or adhering to arbitrary schedules, to intelligently anticipating and preventing them. This paradigm shift impacts not just maintenance operations but also broader operational strategies, resource allocation, and safety protocols across industries, transforming maintenance from a perceived cost-center into a value-generating function that actively contributes to operational excellence.
The Imperative for Predictive Maintenance in Industry 4.0
The ongoing industrial revolution, often termed Industry 4.0, is defined by the seamless integration of cyber-physical systems, real-time data exchange, and intelligent automation. Within this interconnected ecosystem, Predictive Maintenance (PdM) emerges not merely as an advantageous practice but as an indispensable core pillar.1 It represents a strategic evolution from the traditional reactive "fix-it-when-it-breaks" approach or time-based preventive maintenance, which often results in unnecessary interventions or, conversely, missed critical issues.6
The fundamental aim of PdM is to optimize asset upkeep based on the actual, real-time condition of machinery, thereby minimizing unplanned downtime, substantially reducing maintenance costs, and extending the operational lifespan of critical assets.6 This is achieved by leveraging continuous data streams from sensors to anticipate equipment failures before they manifest, allowing for proactive intervention rather than costly emergency repairs.6 The benefits extend beyond mere cost avoidance; they encompass enhanced productivity, improved safety, and greater overall equipment effectiveness (OEE).16
The quantifiable impact of PdM is compelling and widely documented. Companies that have successfully implemented PdM programs have reported significant improvements, including a 10-15% reduction in downtime and a 5-20% decrease in maintenance costs.19 More comprehensive studies project even greater returns, with typical outcomes showing a 25-30% reduction in maintenance costs, a 70-75% decrease in breakdowns, and a 35-45% reduction in overall downtime.20 These figures underscore the profound economic and operational advantages that PdM offers in a competitive industrial landscape.
The effectiveness of PdM is deeply rooted in the interdependence of several key technologies: the Industrial Internet of Things (IIoT), Artificial Intelligence (AI), and Machine Learning (ML). IIoT sensors act as the "nervous system" of this ecosystem, continuously collecting vast amounts of data on critical parameters like vibration, temperature, and pressure from machines.6 This raw data, often in the billions of data points daily from large deployments, is then transmitted to central systems, frequently cloud-based platforms.19 AI and ML algorithms are then employed to process and analyze this "Big Data," transforming it into actionable intelligence. Without the continuous data flow provided by IIoT, real-time condition monitoring would be impossible. Without the analytical power of AI/ML, the sheer volume and complexity of the data would be overwhelming and largely uninterpretable, leading to data paralysis rather than proactive decision-making. Finally, without the framework of Predictive Maintenance, these technological capabilities would lack a clear application for translating insights into strategic action.
This creates a self-reinforcing cycle where each technology enhances the capabilities and value of the others. IIoT provides the data, AI/ML provides the intelligence, and PdM provides the operational framework. This convergence is what truly enables the vision of a "smart factory," where operations are not only automated but also intelligent and self-optimizing.1 The ability to predict and prevent failures with high accuracy allows organizations to transition from a reactive, unpredictable operational model to a proactive, highly efficient, and predictable one. This strategic shift is imperative for achieving operational excellence, ensuring business continuity, and gaining a competitive advantage in the rapidly evolving industrial environment of 2025.
III. The Dominance of Wireless Vibration Sensors
The landscape of industrial vibration monitoring is undeniably shifting, with wireless vibration sensors rapidly asserting their dominance. This ascendancy is not merely a preference for convenience but a strategic adoption driven by significant technological advancements and compelling economic advantages.
Technological Advancements Driving Wireless Adoption
The increasing adoption of wireless vibration sensors is directly attributable to a series of technological breakthroughs that address historical limitations and enhance their utility across diverse industrial applications. These sensors are now capable of continuous 24/7 monitoring, transmitting measurements at specified intervals, which can be as frequent as every minute, making them ideal for establishing automated alarm systems when vibration readings exceed normal levels.4
A primary driver of this momentum is the continuous refinement of the sensors themselves. Modern wireless sensors feature smaller form factors, enhanced durability, and improved integration with cloud-based platforms, facilitating seamless data analysis and remote monitoring.3 A notable advancement is the proliferation of Micro-Electro-Mechanical Systems (MEMS) based sensors. These miniature devices are gaining significant popularity due to their compact size, remarkably low power consumption, and cost-effectiveness. While widely integrated into consumer electronics like smartphones and smartwatches for motion tracking, MEMS sensors are increasingly applicable in industrial contexts where compact and economical solutions are paramount for small-scale applications and industrial IoT setups.1
Furthermore, companies are actively pushing the boundaries of wireless sensor capabilities. For instance, Broadsens has developed long-range wireless vibration and temperature sensors capable of reaching distances up to 1 kilometer in open spaces. They have also enhanced their industrial wireless sensor series with features like auto acceleration range adjustment, which provides better resolution for both minute micro-vibrations (e.g., structural health monitoring) and large acceleration events typical of heavy machinery. The addition of Over-The-Air (OTA) firmware upgrade capabilities allows for remote updates without compromising power consumption, further enhancing their long-term viability and ease of maintenance.22
The evolution of wireless sensors has directly addressed many of their historical limitations, particularly when compared to traditional wired IEPE (Integrated Electronics Piezoelectric) sensors. While IEPE sensors traditionally offered superior performance in terms of full-scale range (from 0.001 g to 20,000 g) and lower noise floors (allowing detection of micro-vibrations), wireless sensors were often limited to ranges between 10 g and 100 g and had noise floors one to two magnitudes higher.23 Similarly, the upper frequency range of wireless sensors was typically limited to around 2 kHz due to the complexity of their internal electronics and larger size.24 However, the ongoing advancements in low-power electronics, improved communication protocols, and sophisticated signal processing embedded within the sensors are steadily closing this performance gap. This means that while wired solutions may retain a niche for extremely high-fidelity or high-g shock measurements, wireless solutions are becoming increasingly viable and preferred for a much broader spectrum of "general machine applications".23 The implication of this trend is that wireless sensors are no longer merely a convenient alternative but are rapidly becoming the de facto standard for most industrial monitoring needs, enabling widespread deployment and data collection that was previously impractical or cost-prohibitive.
Wired vs. Wireless: A Comparative Analysis
The choice between wired and wireless vibration monitoring systems involves a careful consideration of their respective advantages and disadvantages, with a growing inclination towards wireless solutions in 2025.
Wired Systems
Traditional wired monitoring systems rely on physical cables to connect sensors to a central monitoring hub. Their primary advantage lies in their inherent stability and reliability. Wired connections are generally less susceptible to electromagnetic interference, ensuring robust data transfer with minimal signal loss.5 They can collect extensive and detailed data continuously, making them suitable for production-critical machines like turbine generators that require in-depth, 24/7 vibration measurements.4
However, wired systems come with significant limitations. Installation is typically complex, labor-intensive, and time-consuming, especially in facilities with existing infrastructure or hard-to-access areas. The need for extensive cabling, network switches, and control cabinets significantly drives up initial installation costs and adds complexity to the system design.4 Furthermore, expanding a wired system often necessitates running additional cables, which limits scalability. Commissioning these systems can also be costly, potentially requiring multiple return visits for troubleshooting and adjustments, prolonging deployment timelines and overall expenses.5
Wireless Systems
Wireless vibration sensors offer a modern alternative that prioritizes flexibility, scalability, and ease of installation. They are significantly simpler and less expensive to deploy than their wired counterparts, reducing labor and upfront costs.4 This ease of installation makes them highly scalable, allowing businesses to expand their monitoring capabilities by simply adding new sensors without the need for extensive re-cabling.4 Wireless sensors are particularly advantageous for hazardous environments where frequent manual checks are infeasible, or for meeting long-distance communication needs across geographically dispersed manufacturing plants.25 They provide the power to monitor asset condition 24/7, sending measurements at specified intervals, and are ideal for triggering alarms when readings exceed normal levels.4
Despite these benefits, wireless systems do have considerations. Their data transfer speeds can be impacted by factors such as connectivity and location.4 While significant advancements have been made, wireless sensors historically exhibited a larger noise floor and more limited full-scale (g-level) and upper frequency ranges compared to high-fidelity wired IEPE sensors.23 For instance, most wireless sensors operate within a measurement range of 10 g to 100 g, making them generally adequate for rotating machines, turbines, and gearboxes, but less suitable for shock-related high-g testing or micro-vibration measurements.23 Similarly, their upper frequency range is typically limited to around 2 kHz while maintaining acceptable accuracy.24
The strategic imperative for wireless adoption is largely driven by a favorable Total Cost of Ownership (TCO) and superior scalability. While wired systems may offer marginally better raw performance in highly specialized niches, the overarching economic and practical advantages of wireless solutions are compelling for the vast majority of industrial applications. The reduced installation complexity and cost, coupled with the ability to deploy sensors rapidly and widely, significantly lower the overall expenditure over the system's lifecycle. Furthermore, the capacity to monitor assets in hazardous or remote environments without human intervention dramatically reduces safety costs and risks. The strong market growth projections for wireless sensors directly reflect this economic and practical advantage, indicating that their value proposition extends far beyond mere technical specifications.
In practice, a well-rounded vibration monitoring system often incorporates a hybrid approach, combining both wired and wireless sensors. This strategy allows organizations to leverage the continuous, high-resolution data provided by wired systems for their most critical, production-dependent assets, while utilizing the scalability, ease of deployment, and cost-effectiveness of wireless sensors for semi-critical machines or those in hard-to-reach locations.4 This nuanced approach ensures optimal coverage and data quality tailored to the specific needs of each asset.
Market Dynamics and Projections for Wireless Sensors in 2025
The market for wireless vibration sensors is experiencing a period of robust expansion, reflecting a broader industry shift towards more agile, data-driven maintenance strategies. In 2025, the global Wireless Vibration Sensor Market is projected to reach a valuation of USD 1.50 billion. This segment is anticipated to grow further, reaching USD 2.37 billion by 2034, demonstrating a Compound Annual Growth Rate (CAGR) of 5.2% from 2025 to 2034.1 This growth outpaces the overall vibration monitoring market in terms of CAGR for wireless networks specifically (10.5% CAGR for wireless networks between 2025 and 2030, compared to 6.3% for the overall market).26 The broader global vibration sensor market, encompassing both wired and wireless solutions, is projected to grow from USD 7.05 billion in 2025 to USD 13.25 billion by 2034, with a CAGR of 7.27%.2
The primary drivers for this market expansion are the escalating demand for predictive maintenance and the increasing imperative for real-time condition monitoring across a multitude of environments, including manufacturing, automotive, aerospace, and energy sectors.1 Traditional wired systems are increasingly being replaced by wireless alternatives due to their inherent ease of installation, superior scalability, and the significant reduction in overall costs they offer.1
The market is further propelled by the widespread adoption of enabling technologies such as the Industrial Internet of Things (IIoT), Industry 4.0 initiatives, and the integration of AI-powered analytics. These technologies collectively facilitate automated fault detection and remote monitoring capabilities, which are essential for modern industrial operations.1 Energy efficiency programs and stringent regulatory requirements also contribute to the heightened adoption of these advanced monitoring solutions.1
The growth of the wireless vibration sensor market is a clear demonstration of a powerful market dynamic: the "pull" of predictive maintenance needs being met by the "push" of technological enablement. Industries are increasingly recognizing the critical need to avoid costly unplanned downtime and optimize equipment efficiency. This demand creates a strong "pull" for solutions that can provide accurate, real-time insights into asset health. Simultaneously, advancements in low-power wireless communication technologies, miniaturization (e.g., MEMS sensors), and embedded processing capabilities are providing the "push" by making wireless vibration monitoring solutions increasingly viable, cost-effective, and easy to deploy on a large scale.1 The observed collaborations among companies to develop new wireless vibration sensors further underscore a collective industry effort to capitalize on this convergence of demand and technological capability.25 This indicates that the market is not simply growing; it is maturing into a sophisticated ecosystem where sensor hardware, communication protocols, and analytics platforms are co-evolving to meet complex industrial demands, firmly positioning wireless sensors as the central data collection point for this integrated ecosystem.
IV. Vibration Data Acquisition and Advanced Analytics
Effective vibration monitoring hinges on the quality of data acquisition and the sophistication of its subsequent analysis. The selection of appropriate sensors and the application of advanced signal processing techniques are paramount to extracting actionable intelligence from the complex vibrational signatures of industrial machinery.
Types of Vibration Sensors and Their Industrial Applications
The diverse requirements of industrial vibration monitoring necessitate a range of specialized sensor types, each optimized for particular measurement parameters and applications. While wireless solutions are gaining prominence, the fundamental principles governing sensor selection remain crucial.
- Accelerometers: These are among the most popular vibration sensors, designed to measure acceleration, which is the rate of change in velocity over time. They are particularly effective for detecting very high frequencies.11 In industrial settings, accelerometers are crucial for identifying abnormal vibrations in machinery, serving as an early warning system for potential mechanical failures. They can be configured as single-axis for simpler movements or tri-axis for comprehensive, complex motion analysis, providing more information about a machine's condition.21 Piezoelectric accelerometers, in particular, are known for their high sensitivity and precision, making them suitable for demanding applications in aerospace, medical equipment, and laboratory settings.12
- Velocity Transducers (Geophones): These electromagnetic devices are widely utilized for structural vibration measurements and are best suited for measuring mid-range frequencies.11 They track vibrations in relation to their speed, generating electrical signals proportional to the vibration velocity. These sensors are commonly employed in critical industrial machinery such as turbines, pumps, and motors, where early detection of excessive vibrations is vital to prevent escalating problems.21
- Displacement Sensors: Used when precision in measuring the movement of objects over time is paramount, these sensors are ideal for low-frequency measurements.11 In industrial vibration monitoring, displacement sensors are critical for assessing the stability of large structures like bridges, buildings, and railway tracks, detecting even slight movements that could indicate structural integrity issues. They also play a crucial role in machine alignment within manufacturing processes.21
- MEMS Vibration Sensors: Micro-Electro-Mechanical Systems (MEMS) sensors are tiny, yet powerful, devices characterized by their small size, low power consumption, and cost-effectiveness. While prevalent in consumer electronics (e.g., smartphones, smartwatches), their applicability in industrial contexts is growing, especially where compact and economical solutions are required for small-scale applications and industrial IoT setups.1 However, their current technology often limits their use for shock-related high-g testing or micro-vibration measurements, as their g-level ranges (typically 10-100g) and noise floors are not as refined as high-end IEPE sensors.23
- Seismic Vibration Sensors: These sensors are specifically designed to detect large-scale vibrations in the ground, typically caused by events such as earthquakes, volcanic eruptions, or significant structural shifts. While primarily used for natural disaster early warnings and monitoring seismic activity, they also play a role in monitoring the stability of large industrial infrastructures like dams, tunnels, and skyscrapers.21
The specialization and complementarity of these sensor types are crucial in a wireless-dominated landscape. While wireless technology is achieving widespread adoption due to its pervasiveness and convenience for general applications, the choice of sensor type remains highly application-specific, dictated by the frequency range and amplitude level of the operations being monitored.12 For instance, while wireless accelerometers are becoming ubiquitous, applications requiring extreme precision, very high-g measurements, or the detection of subtle micro-vibrations may still necessitate specialized wired IEPE sensors.23 This indicates that the "dominance" of wireless is more about its widespread applicability and ease of deployment for the majority of industrial needs, rather than a single sensor type or connectivity method replacing all others. A comprehensive vibration monitoring strategy in 2025 will therefore likely involve a judicious mix of sensor types, predominantly wireless for scalability and flexibility, but retaining wired or highly specialized sensors where critical performance parameters demand it.
Optimizing Data Collection: Sampling Rates and Multi-Axis Measurement
The efficacy of any vibration monitoring program is directly proportional to the quality and relevance of the data collected. Two critical parameters in optimizing data acquisition are the sampling rate and the use of multi-axis measurements.
The sampling rate, also known as sampling frequency, defines the number of data points collected per second by a data acquisition system. It plays a pivotal role in accurately capturing the vibration signal, directly influencing the resolution and fidelity of the collected data.27 A higher sampling rate captures more data points, providing a more detailed and accurate representation of the vibration signal, and is crucial for capturing a wider range of frequencies, including high-frequency components that often indicate specific faults or defects.27 Conversely, an insufficient sampling rate can lead to aliasing, a phenomenon where a high-frequency signal is misinterpreted as a lower frequency signal, resulting in a loss of critical information and potentially inaccurate diagnoses.27 To prevent aliasing, the Nyquist-Shannon theorem dictates that the sampling rate should be at least twice the highest frequency component of interest; a general rule of thumb suggests a rate 2.5 to 3 times this highest frequency.28
However, the notion that a higher sampling rate is always superior is a common misconception. While it provides more detailed data, it also significantly increases the volume of data collected, posing substantial challenges for storage, transmission, and processing.27 Therefore, the ideal sampling rate is not simply the highest possible, but rather one that is sufficient to capture the frequency range of interest and achieve the desired resolution for the specific application.27 Industry standards and guidelines often dictate appropriate sampling rates: for instance, power generation typically uses 2-5 kHz, petrochemical industries 1-3 kHz, and aerospace applications, particularly for high-speed machinery like gearboxes, require higher rates of 5-10 kHz or more.27 The selection must consider the equipment type, its operational speed, and the specific frequency content expected from potential faults.27
Multi-axis measurement is equally essential for comprehensive vibration analysis. For accurate measurements, particularly in structural monitoring or machine condition assessment, vibrations should be measured along three axes: the vertical (z) axis and two horizontal (x and y) axes, perpendicular to each other.12 The horizontal axes should ideally align with the building's or machine's main axis, with one pointing towards the vibration source.12 Modern wireless vibration sensors increasingly offer 3-axis measurement capabilities, providing a more complete picture of machine movement and condition, which is vital for diagnosing complex faults.23
The trade-off between data granularity and processing burden in real-time systems is a critical engineering challenge. While high sampling rates are necessary for detailed fault detection, the resulting massive data volumes can overwhelm cloud infrastructure and introduce latency, hindering real-time decision-making. This necessitates that advanced data acquisition systems employ intelligent strategies, potentially at the edge of the network, to dynamically adjust sampling rates based on operational states or detected anomalies. Such adaptive sampling ensures that high-resolution data is captured precisely when critical events occur, while minimizing unnecessary data transmission and storage during normal operation. This approach directly aligns with the broader trend towards edge computing, where initial data processing occurs closer to the source, optimizing data flow and enhancing responsiveness.29
Signal Processing Techniques: Time Domain, Frequency Domain, FFT, Wavelet, and Envelope Analysis
Once vibration data is acquired, sophisticated signal processing techniques are employed to transform raw measurements into actionable insights. These methods allow for the identification, diagnosis, and even prediction of machinery faults.
Time Domain Analysis provides a direct representation of how a vibration signal changes over time.30 This approach is useful for assessing the overall condition of components and detecting gross changes in vibration levels.25 However, raw time-domain data can be extremely dense and complex, making it challenging to discern specific fault signatures or relate them directly to operational parameters.10 A single time-instant value of vibration is often not instructive because it changes rapidly.10
Frequency Domain Analysis is a more powerful approach, revealing how a signal's energy is distributed over a range of frequencies.30 This transformation is crucial because specific frequencies in a vibration signal can be directly correlated with the rotational speeds of machine components or other operational parameters, allowing for precise fault identification.10 In this domain, amplitude indicates the severity of a problem, frequency identifies its nature, and phase provides insight into how different vibration signals relate to one another.31
The Fast Fourier Transform (FFT) is the cornerstone mathematical technique for converting time-domain signals into the frequency domain.10 FFT is computationally efficient and indispensable for isolating specific frequency components, which can then be linked to machine elements (e.g., a high amplitude at 100 Hz corresponding to a motor running at 6000 rpm, or 100 revolutions per second).10 This capability is fundamental for diagnosing issues such as imbalance, misalignment, or bearing wear.10 The significance of the FFT algorithm is so profound that it was listed among the top 10 algorithms of the 20th century.10
Beyond basic FFT, more advanced techniques further enhance diagnostic capabilities:
- Wavelet Analysis: This powerful signal processing technique allows for the decomposition of vibration signals into different frequency bands, making it particularly useful for analyzing non-stationary signals where the frequency content changes over time.34 Wavelet analysis has proven effective in detecting faults in rolling element bearings, where traditional FFT might struggle due to the transient nature of the fault signals.34
- Envelope Analysis: This technique extracts the amplitude modulation of a high-frequency vibration signal, effectively demodulating it to reveal lower-frequency patterns that are characteristic of specific faults, particularly in bearings and gearboxes.33 It typically involves demodulation methods like the Hilbert transform and filtering to isolate the relevant frequency range.35 By analyzing the envelope spectrum, maintenance personnel can identify wear, misalignment, or damage to gear teeth.36
- Phase Analysis: Often underutilized, phase analysis is a powerful technique for diagnosing 1X frequency issues such as unbalance and misalignment.32 It examines the phase difference (measured in degrees) between vibration signals at two different points on a machine or between a vibration signal and a reference signal (e.g., a tachometer pulse).32 Modern vibration analyzers often include cross-channel phase functions, simplifying the process compared to older methods. For example, a loose or cracked machine base will produce readings approximately 180 degrees out of phase across the defect, indicating opposing movements.32 Phase analysis can also identify angular or parallel misalignment in coupled machines by comparing readings in vertical, horizontal, and axial directions.32
The evolution of these signal processing techniques marks a critical progression from merely diagnostic tools to components of predictive intelligence. Initially, techniques like FFT primarily served a diagnostic purpose, informing what was wrong with a machine. Advanced methods such as Wavelet and Envelope analysis significantly improved the accuracy and earliness of fault detection, particularly for complex and subtle faults like bearing wear. The integration of these sophisticated signal processing techniques with Artificial Intelligence and Machine Learning models transforms them from standalone analytical tools into integral components of a comprehensive predictive system. This allows the system to not only identify what is wrong but also forecast when a failure is likely to occur, enabling proactive and optimized maintenance actions.6 The sophistication of signal processing directly correlates with the accuracy and lead time of predictive maintenance, making automated, multi-modal signal processing pipelines that feed directly into AI models a key focus for achieving highly precise and early fault detection in the future.
V. AI and Machine Learning in Predictive Maintenance
The integration of Artificial Intelligence (AI) and Machine Learning (ML) has fundamentally reshaped predictive maintenance, driving a paradigm shift from reactive and rule-based approaches to sophisticated, data-driven strategies.
The Shift from Rule-Based to Data-Driven Predictive Maintenance
Historically, maintenance practices were largely reactive, addressing equipment failures only after they occurred, or preventive, based on fixed schedules regardless of the actual condition of the machinery. These traditional methods often relied heavily on human expertise to interpret data and predict potential failures, or on static rules and predefined thresholds.13 This frequently led to inefficient outcomes, such as unnecessary maintenance on healthy equipment or, more critically, missed opportunities to address developing issues before they escalated into costly breakdowns.37
The advent of the Industrial Internet of Things (IIoT) has ushered in a data-driven revolution in maintenance. IIoT sensors now continuously collect vast amounts of real-time data on various operational parameters, including vibration, temperature, pressure, and current.13 This constant stream of data provides an unprecedented level of insight into equipment health and performance. AI and ML are central to this transformation, as they possess the capability to process these massive datasets, identify intricate patterns, detect subtle anomalies, and accurately predict potential failures.6 This proactive, data-driven approach minimizes unplanned downtime, optimizes maintenance schedules, and significantly enhances overall operational efficiency.6
This transition represents a profound shift from human interpretation to automated, self-improving intelligence. Traditional systems were limited by their reliance on human operators to manually interpret data and by static rules that struggled to account for the myriad of variables and complex interactions in real-world industrial environments.37 AI/ML-based systems, in contrast, are designed to learn and adapt over time by continuously analyzing data streams. They excel at detecting subtle anomalies that might go unnoticed by human operators or conventional monitoring tools, predicting failures with far greater accuracy.19 This capability enables a significant reduction in human cognitive load, allowing maintenance professionals to shift their focus from routine data interpretation to more complex problem-solving and strategic initiatives. The ultimate goal is the automation of decision-making and, eventually, the realization of "autonomous maintenance," where AI systems can analyze, diagnose, and even initiate repairs without direct human intervention.13 This shift democratizes advanced diagnostics, making sophisticated predictive capabilities accessible to a broader range of industrial users beyond a small cadre of specialized vibration experts.
Key AI/ML Algorithms for Anomaly Detection, Fault Diagnosis, and RUL Prediction
AI and Machine Learning algorithms form the analytical core of modern predictive maintenance systems, leveraging real-time data from IoT sensors to provide deep insights into machine health. These algorithms are specifically designed to address three critical aspects of equipment monitoring: anomaly detection, fault diagnosis, and Remaining Useful Life (RUL) prediction.
Anomaly Detection: AI algorithms are adept at establishing baselines of normal operating parameters and then identifying deviations or unusual patterns in vibration data, temperature fluctuations, or other performance metrics.6 These subtle anomalies often precede equipment failure, providing early warnings that human observation or traditional threshold-based systems might miss.40 The ability to detect these early indicators is crucial for proactive intervention.
Fault Diagnosis: Machine learning algorithms can be trained on labeled datasets, where the data is tagged with the known condition of the equipment (e.g., normal, imbalanced, misaligned, bearing wear, loose components).11 By analyzing these large datasets, the algorithms learn to recognize characteristic vibration patterns associated with specific faults. This allows them to automatically diagnose the nature of a problem, providing maintenance teams with precise information about the issue.33
Remaining Useful Life (RUL) Prediction: Beyond merely detecting and diagnosing faults, advanced ML algorithms can predict the remaining useful life of equipment. By analyzing historical performance data, current operational parameters, and identified degradation patterns, these algorithms can forecast when a component is likely to fail.6 This predictive capability enables maintenance teams to schedule interventions precisely when needed, optimizing resource allocation and minimizing unnecessary downtime.6
The development of Deep Learning Architectures has significantly advanced these capabilities:
- Convolutional Neural Networks (CNNs): Originally developed for image processing, CNNs are highly effective for analyzing vibration data when it is transformed into two-dimensional representations, such as time-frequency images (e.g., spectrograms or scalograms from Continuous Wavelet Transform). CNNs excel at extracting spatial features, such as peaks, cliffs, and waveforms, from these images, which are indicative of specific fault characteristics.41 They can achieve high classification accuracy for fault detection, often outperforming traditional engineering-based approaches.43
- Recurrent Neural Networks (RNNs), particularly Long Short-Term Memory (LSTM) and Gated Recurrent Units (GRUs): These networks are specifically designed for sequence modeling and are highly effective at capturing temporal dependencies and long-term variations in time-series data, such as continuous vibration signals.41 LSTMs, for instance, possess a "memory" function that allows them to retain information from previous time steps, which is crucial for predicting future vibration values and overcoming challenges like vanishing or exploding gradients encountered in traditional RNNs.44
- Hybrid Models: The most advanced and effective solutions often combine different deep learning architectures to leverage their respective strengths. For example, hybrid CNN-LSTM-GRU models integrate CNNs for spatial feature extraction from time-frequency domains with LSTMs and GRUs for analyzing long-sequence temporal characteristics.41 This combined approach allows for comprehensive spatio-temporal feature extraction, resulting in superior performance. Studies have shown that such hybrid models can achieve very high accuracy (e.g., over 99% for bearing fault diagnosis) even in noisy industrial environments.41 A novel hybrid model, RoughLSTM, integrates rough set theory with LSTM to enhance anomaly detection, particularly in handling uncertainty in vibration data, achieving a classification accuracy of 94.3%.46
The synergy of different data types and AI architectures is a crucial aspect of developing comprehensive diagnostics. The effectiveness of a predictive maintenance system is greatly enhanced by employing AI models that are best suited for the specific characteristics of the vibration data. CNNs excel when data is represented visually (e.g., time-frequency plots), while LSTMs and GRUs are superior for sequential, time-series data. The most effective solutions therefore integrate these different approaches, creating hybrid models that can simultaneously analyze both temporal and spatial features of the vibration signals. This complex, multi-faceted approach is necessary to accurately diagnose the wide variety of real-world machine faults. The implication is that future research and development will continue to focus on optimizing these hybrid models and integrating them with domain expertise to push prediction accuracy even higher, potentially leading to near-perfect fault diagnosis and RUL prediction.
Impact on Accuracy, Efficiency, and Reduction of False Positives
The transformative power of AI and ML in predictive maintenance is most evident in their impact on diagnostic accuracy, operational efficiency, and the crucial reduction of false positives. These advancements are critical for building confidence in automated systems and ensuring their widespread adoption.
AI/ML-based systems excel at detecting subtle anomalies and complex patterns in vibration data that are often imperceptible to human operators or beyond the capabilities of traditional rule-based monitoring tools.37 This enhanced detection capability translates directly into significantly higher prediction accuracy. Some modern predictive maintenance systems, leveraging these advanced algorithms, can achieve up to 99% prediction accuracy.19 This precision allows for proactive interventions long before issues escalate into critical failures, thereby preventing costly unplanned downtime and extensive damage.6
A critical advantage of AI/ML algorithms is their ability to significantly reduce false positives. Traditional condition monitoring systems, often limited by predefined rules and fixed thresholds, frequently generated false alarms or, conversely, missed actual developing issues. This limitation stemmed from their inability to account for the myriad of dynamic variables and complex interactions present in real-world industrial environments.37 AI/ML algorithms, however, are designed to handle this inherent complexity. By continuously analyzing vast amounts of data from multiple sensors, they can identify nuanced patterns and correlations that are beyond the reach of conventional methods.37 For instance, novel hybrid models like RoughLSTM specifically improve uncertainty handling in vibration data, leading to more reliable anomaly detection and fewer erroneous alerts.46
Beyond accuracy, AI-powered predictive maintenance dramatically enhances operational efficiency. By streamlining the analysis of equipment data and automating fault diagnosis, these systems reduce human error and optimize maintenance workflows.13 This allows for more precise planning of maintenance activities, ensuring resources are allocated effectively and interventions occur at the most opportune time, leading to substantial savings in time and resources.6
The continuous refinement of AI/ML models to improve accuracy and robustness is not merely a technical objective but a commercial and operational necessity. The success of widespread predictive maintenance adoption hinges on the trust that maintenance teams place in the system's predictions. If systems frequently generate false alarms or miss critical issues, they will be disregarded, undermining the entire PdM program. The focus on improving model transparency, handling non-stationary signals, and reducing noise in data directly addresses these reliability concerns.46 The implication is that the ongoing development of AI/ML in vibration monitoring is driven by the need to consistently deliver reliable, actionable intelligence, thereby fostering confidence among industrial users and accelerating the transition to truly intelligent, proactive maintenance strategies.
VI. Factory AI: A Leader in Predictive Maintenance Software
In the rapidly evolving landscape of industrial predictive maintenance, software platforms play a pivotal role in translating raw sensor data into actionable intelligence. Factory AI’s Predictive Maintenance software platform stands out as a notable example, embodying many of the advanced features and benefits sought by modern industries.
Platform Features and Core Technological Approach
Factory AI’s flagship offering, "Predict," is an Anomaly Detection Platform built on "advanced machine learning" principles to identify potential equipment failures before they manifest.7 This platform is designed to simplify the complex process of vibration analysis, diagnosis, and asset availability improvement, aiming to make proactive maintenance the most straightforward course of action for industrial teams.7
Key features of the Factory AI platform include:
- Real-time Monitoring and Actionable Alerts: The system continuously monitors critical assets, providing real-time insights and generating actionable alerts when anomalies are detected. This immediate notification capability allows teams to respond quickly to emerging issues.7
- Versatile Data Source Integration: Factory AI demonstrates a flexible data ingestion capability, working seamlessly with various data sources, including vibration sensors, historical operational data from plant historians, and Programmable Logic Controllers (PLCs).7 This broad compatibility is crucial for integrating into existing industrial IT/OT infrastructures.
- User-Centric Visualization: The platform emphasizes "straightforward visuals" to empower maintenance and reliability teams. This approach translates complex vibration data and analytical outputs into easily understandable formats, enabling proactive identification of potential failure risks and clear notification for issues requiring immediate attention.7
- Integrated Maintenance Management (CMMS): A significant value proposition of Factory AI is the inclusion of "Prevent CMMS" at no additional cost with their Predict platform. This AI-powered Computerized Maintenance Management System streamlines maintenance operations by automating work order generation, facilitating asset management, and optimizing maintenance schedules.7
- Root Cause Analysis and Knowledge Management: Beyond mere detection, the platform assists in analyzing the root causes of identified issues. It also supports the creation of a centralized knowledge base, allowing teams to capture and leverage past maintenance experiences and insights.7
The core technological approach of Factory AI, while not explicitly detailed in terms of specific algorithms, can be inferred from its capabilities and the broader industry trends. Its reliance on "advanced machine learning" for anomaly detection and its ability to process diverse time-series and operational data strongly suggest the employment of sophisticated deep learning architectures. This likely includes combinations of Convolutional Neural Networks (CNNs) for extracting spatial features from transformed vibration signals, and Recurrent Neural Networks (RNNs) like Long Short-Term Memory (LSTM) and Gated Recurrent Units (GRUs) for analyzing temporal dependencies in continuous data streams.33 The emphasis on "unlocking the hidden potential in existing data" further indicates robust data preprocessing, feature engineering, and model training capabilities that can derive value from both new and legacy data sources.7
Factory AI serves as an exemplar of the integrated predictive maintenance ecosystem that is becoming standard in 2025. It is not merely a sensor provider or an isolated analytics tool; rather, it offers a comprehensive platform that seamlessly integrates data acquisition, advanced analytical capabilities, and maintenance management functionalities. This holistic, end-to-end approach reflects the industry's movement away from fragmented solutions towards unified platforms that can manage the entire PdM workflow. The platform's focus on "straightforward visuals" and "actionable alerts" highlights a strong user-centric design, ensuring that complex data insights are translated into practical, digestible information that empowers maintenance and reliability teams. This integration is crucial for realizing the full benefits of predictive maintenance, making it accessible and effective for organizations regardless of their current stage of digitalization.
Quantifiable Benefits and Illustrative Use Cases
Factory AI's platform delivers tangible benefits by enabling organizations to transition from reactive to proactive maintenance, thereby optimizing operational efficiency and reducing costs.
A primary quantifiable benefit is the mitigation of unplanned downtime. Factory AI explicitly states its role in helping clients "mitigate unplanned downtime and prevent asset failures".7 This directly aligns with the core value proposition of predictive maintenance, which aims to reduce unexpected outages by anticipating equipment issues.6 While specific percentage reductions in downtime for Factory AI are not provided in the available information, the general industry benefits of AI-powered PdM include significant reductions, with studies showing decreases of 35-45% in downtime and 70-75% in breakdowns.20
The platform also aims for enhanced asset availability, ensuring that critical machinery is operational when needed.7 This contributes to increased productivity and throughput across industrial operations. Although direct cost savings figures for Factory AI are not specified, the broader impact of AI-powered predictive maintenance includes substantial reductions in maintenance costs and the prevention of expensive emergency repairs.6
A compelling testament to Factory AI's efficacy comes from a client, Michael Riches, Site Leader at Bega. He expressed being "impressed by their ability to unlock the hidden potential in our existing data" and found the process of working with Factory AI "incredibly pleasant and easy".7 This testimonial underscores two critical aspects of the platform's value: its capacity to derive meaningful insights from pre-existing, potentially underutilized data infrastructure, and its user-friendliness, which lowers the barrier to adoption for companies embarking on their digitalization journey.
Illustrative use cases for Factory AI's platform include "in-depth monitoring" for a range of common industrial equipment such as pumps, fans, and conveyors.7 The system identifies "potential failure risks" within these assets, providing targeted notifications that demand immediate attention.7 These applications are consistent with the widespread industrial uses of vibration monitoring, which are critical for diagnosing issues like imbalance, misalignment, looseness, and bearing wear in rotating machinery.8
The value proposition of platforms like Factory AI extends beyond mere technological capability to encompass ease of adoption and the monetization of existing data. Many organizations possess vast amounts of operational data but lack the sophisticated tools or specialized expertise required to extract actionable insights. Factory AI addresses this by providing an accessible and intuitive platform that can leverage existing data to deliver advanced analytics. The availability of a "free plan for small teams" and "volume discounts" further indicates a strategy aimed at broad market penetration, making advanced predictive maintenance capabilities accessible to a wider range of industrial users.7 This suggests that the future success of PdM software platforms will increasingly depend not only on their analytical power but also on their user experience, seamless integration with current systems, and a clear, demonstrable path to return on investment, particularly for organizations in the early stages of their digital transformation.
VII. Industrial Applications and Quantifiable Benefits of Vibration Monitoring
Vibration monitoring has transcended its origins as a specialized diagnostic tool to become a ubiquitous and indispensable component of industrial operations across various sectors. Its widespread adoption is driven by its proven ability to deliver significant quantifiable benefits, transforming maintenance from a cost center into a strategic value generator.
Impact Across Key Industries: Manufacturing, Oil & Gas, and Power Generation
The application of vibration monitoring and predictive maintenance (PdM) yields substantial improvements in efficiency, safety, and profitability across diverse heavy industries.
Manufacturing: In the manufacturing sector, vibration analysis is crucial for maintaining the health of rotating machinery, which forms the backbone of most production lines. It effectively detects critical issues such as misalignment, bearing defects, and imbalances in motors, pumps, fans, compressors, and gearboxes.8 By identifying these problems early, vibration monitoring helps prevent mechanical failures, reduces operating costs, and ensures smooth, uninterrupted production.21 Real-world case studies underscore these benefits: General Motors, for example, adopted predictive maintenance using IoT sensors and AI to monitor assembly line robots, resulting in a 15% reduction in unexpected downtime and annual savings of $20 million in maintenance expenses.15 Similarly, Frito-Lay implemented a predictive system that minimized planned downtime to just 0.75% and limited unplanned disruptions to 2.88%, preventing critical component failures that could have significantly impacted production.15
Oil & Gas: The oil and gas industry, characterized by high-value assets operating in often hazardous and remote environments, relies heavily on vibration monitoring to ensure operational continuity and safety. Vibration sensors play a vital role in keeping production machinery, including motors, critical pumps, fans, gearboxes, and compressors, operational while minimizing downtime and reducing operating costs.8 These sensors enable robust predictive maintenance strategies, optimize asset performance, enhance safety standards, and ensure compliance with stringent regulatory requirements.50 Early detection of issues such as pump cavitation 49 or potential leaks in pipelines through pressure monitoring 50 prevents catastrophic failures. A leading company in this sector leveraged digital workflow tools to anticipate failures and optimize technician scheduling, significantly improving overall operational efficiency.15 By monitoring vibrations, oil and gas companies can continuously assess asset performance, identify operational inefficiencies like misalignment, and address them promptly to optimize energy efficiency and minimize wear and tear.50
Power Generation: In the power industry, where continuous supply at low costs is paramount, vibration sensors are crucial for tracking rotor imbalances, aerodynamic asymmetry, surface roughness, and overall performance in turbines and generators.8 They facilitate both offline and online measurements of stress and strain, contributing to the reliability of power generation assets.8 The benefits are substantial: one energy provider reported a 23% reduction in unplanned outages, $25 million in annual maintenance cost savings, and a 3.7% increase in turbine availability through advanced predictive maintenance.20 A specific case involved the early identification of a subtle change in vibration signature indicating an impending bearing failure in a critical turbine, which saved millions in potential repair costs and avoided significant downtime.17
The strategic shift enabled by advanced vibration monitoring moves beyond simple cost-reduction to comprehensive value-creation. While reduced maintenance costs and minimized downtime remain prominent benefits, the broader implications include "increased output" 17, "improved safety" 17, "enhanced productivity" 16, and "compliance confidence".51 This signifies that vibration monitoring, particularly when integrated with PdM, is no longer solely about cutting expenses but about generating competitive advantages, ensuring business continuity, and contributing to Environmental, Social, and Governance (ESG) goals through improved energy efficiency and extended asset lifecycles.6 In 2025, investing in advanced vibration monitoring is viewed as a strategic imperative for operational resilience, sustainability, and market leadership, rather than merely a maintenance expenditure.
Broader Applications: Construction, Automotive, Aerospace, and Data Centers
Beyond the core heavy industries, vibration monitoring has found critical applications in a diverse array of sectors, highlighting the ubiquitous nature and versatility of this technology. The widespread adoption of wireless sensors has significantly facilitated this expansion by making deployment easier and more cost-effective in non-traditional environments.
In construction, vibration monitoring is essential for assessing and mitigating the impact of construction-related vibrations on surrounding structures and human comfort.12 This involves employing advanced equipment and methodologies, such as Peak Particle Velocity (PPV) and Root Mean Square (RMS) analysis, to ensure the safety and integrity of projects. Real-time analysis is a critical capability, allowing for the immediate halting of construction activities if vibration amplitudes approach damaging levels, thereby preventing potential harm to nearby buildings, pipes, gas lines, and power lines.12 Remote monitoring and sophisticated alarming functions further enhance safety and structural integrity.12
The automotive industry increasingly leverages vibration sensors for vehicle health monitoring and infrastructure safety.1 These sensors detect subtle issues with tires, engines, or suspension components that might otherwise go unnoticed until they escalate into severe problems.21 In modern vehicles, these tiny devices provide early warnings, enabling mechanics to diagnose problems faster and perform more targeted repairs, ultimately leading to safer and more reliable driving experiences.21
In aerospace, where even minor vibrations can have catastrophic consequences, vibration sensors are indispensable. They are critical for monitoring engine and structural integrity, detecting loose panels, or identifying problems with landing gear.21 In space applications, where the margin for error is virtually nonexistent, the precision and reliability of vibration monitoring are even more critical.21
Data centers, which demand exceptionally high uptime, compliance, and efficiency, are also adopting vibration monitoring as a foundational tool for smarter operations. These systems help in documenting asset and repair histories across sites, facilitating faster commissioning of new equipment, and ensuring audit-ready records for compliance confidence.51 By capturing and tracking vibration trends over time, data centers can build a comprehensive picture of equipment performance, identify recurring issues, and make data-driven decisions regarding purchasing and repairs.51
Beyond industrial and infrastructure applications, vibration sensors have permeated consumer electronics. They are responsible for the buzzing alerts in smartphones, enable movement tracking and fall detection in smartwatches, and enhance user experience in gaming controllers and virtual reality headsets.21 Furthermore, vibration testing is utilized in laboratories to uphold high quality standards for products, and even in novel applications such as improving bus user comfort by measuring vibrations and sudden movements experienced by passengers.25
The ubiquitous nature of vibration monitoring, extending beyond traditional industrial settings, highlights that the underlying technology for sensing and analyzing vibrations is highly versatile. This broad applicability is significantly facilitated by the dominance of wireless capabilities and the miniaturization of sensors, which make deployment easier and more feasible in a wide range of environments. The implication is that the vibration monitoring market will continue to expand beyond heavy industry, driven by the increasing integration of these sensors into everyday devices and critical infrastructure for enhanced safety, comfort, and operational efficiency.
VIII. Challenges and Future Outlook
While the state of vibration monitoring in 2025 is characterized by significant advancements and widespread adoption, several challenges remain. Addressing these, alongside the continuous emergence of new technologies, will define the trajectory of the field beyond the current year.
Cybersecurity Risks and Mitigation Strategies for IIoT Vibration Monitoring
The increasing interconnectedness of industrial systems through IIoT, while offering immense benefits, simultaneously introduces a complex web of cybersecurity risks. IIoT vibration monitoring systems, by their very nature, expand the attack surface, making them potential targets for malicious actors.53 Signals transmitted wirelessly, particularly over widely used channels like Wi-Fi and Zigbee, are inherently more susceptible to interception than traditional wired connections.5
A significant challenge arises from the extended operational lifespan of industrial equipment. Unlike consumer IT devices that are frequently replaced, industrial IoT devices often remain in operation for decades with minimal or no security updates, creating long-lived vulnerabilities that can be exploited over time.53 Legacy devices, prevalent in many industrial environments, further complicate the security landscape due to their outdated hardware and software, which can hinder network visibility and make it difficult to implement modern security controls.53 Common vulnerabilities include inadequate access controls, the use of default credentials, and poor network segmentation, which can allow attackers to move laterally within industrial networks once initial access is gained.53
The threat landscape is escalating, with the financial impact of industrial cybersecurity incidents reaching millions of dollars per data breach, not including regulatory fines and reputational damage.53 Critical infrastructure, including power generation and transportation systems, is increasingly targeted by nation-state actors, with geopolitical tensions manifesting as cyberattacks.53 This elevates cybersecurity from a business risk to a national security concern.
To combat these escalating threats, robust mitigation strategies and best practices are imperative for IIoT vibration monitoring systems in 2025:
- Comprehensive Device Discovery and Classification: Organizations must implement passive discovery methods, such as network traffic analysis (Deep Packet Inspection), correlated with DHCP, DNS, and ARP logs, to build dynamic asset maps. Machine learning can be used to identify device types based on their behavioral signatures, providing essential visibility into the entire device landscape.55
- Enforce Logical Segmentation and Network Isolation: Implementing firewalls with east-west control and deploying Software-Defined Networking (SDN) for dynamic segmentation is crucial to restrict lateral access within networks. In Industrial Control Systems (ICS)/Operational Technology (OT) environments, applying the Purdue Model segmentation (Levels 0–5) with Demilitarized Zones (DMZs) and data diodes can effectively contain lateral movement and minimize the blast radius in the event of a breach.55
- Secure Device Provisioning and Identity Binding: Leveraging X.509 certificates, Trusted Platform Modules (TPMs), or Hardware Security Module (HSM)-backed identity binding ensures that only authenticated and trusted devices can connect to the network. Secure boot processes and device attestation validate firmware integrity at startup.55
- Harden Device Configurations: This involves disabling unused services and interfaces (e.g., USB, SSH, telnet), enforcing strong password policies, removing factory defaults, and applying host-based firewalls and IP whitelisting where supported. Unnecessary code or debug modes should be removed from firmware.55
- Secure Firmware Management and Patch Governance: Establishing a Firmware Bill of Materials (FBOM) repository and mandating cryptographic signing for firmware updates, along with secure update delivery mechanisms (e.g., over TLS), are critical. Automated patch rollout via management gateways and post-deployment integrity validation are essential, with compensating controls (e.g., firewall ACLs, microsegmentation) applied for legacy devices that cannot be directly updated.55
- Implement Secure Communication Protocols: Enforcing TLS 1.2+ for HTTPS/MQTT communication, using AES-256 for payload encryption, and ensuring mutual authentication between devices and gateways/cloud platforms are vital. Legacy protocols should be replaced with secure alternatives.55
- Monitor IoT-Specific Behavior and Anomalies: Beyond signature-based detection, behavioral monitoring is crucial. Baselines of normal device behavior (e.g., periodic telemetry, update intervals) should be established to detect deviations such as abnormal DNS requests, data exfiltration attempts, or rogue firmware updates. Integrating alerts into centralized Security Information and Event Management (SIEM)/Security Orchestration, Automation, and Response (SOAR) pipelines is recommended.55
- Apply Zero Trust Principles: Assuming no device is inherently trusted, continuous authentication based on context and risk scores, policy-based access controls with device posture checks, and micro-segmentation for each device with restricted permissions are key. Access should be dynamically revoked if abnormal behavior is detected.55
- Continuous Vulnerability Assessment and Penetration Testing: Regular firmware analysis using Static Application Security Testing (SAST)/Dynamic Application Security Testing (DAST), red team exercises to simulate multi-stage IoT compromise scenarios, and physical security assessments for edge deployments (e.g., tamper-resistance) are necessary.55
- Cybersecurity Education: Building strong, flexible cybersecurity education programs focused on IoT defense is paramount. Training should cover device authentication, network segmentation, protocol-specific security measures (e.g., MQTT, CoAP), and robust incident response strategies, fostering open communication and collaboration between IT and OT teams.56
Cybersecurity is not an afterthought but a foundational enabler for IIoT scalability. The sheer volume of security challenges and the detailed mitigation strategies highlight that security must be designed into the system architecture from the ground up. The increasing vulnerability of devices and the financial and operational impact of breaches underscore that robust security is paramount. The implication is that in 2025, adherence to comprehensive cybersecurity frameworks (such as NIST and ISA/IEC 62443) and continuous education will be non-negotiable for any organization deploying IIoT vibration monitoring. The market will increasingly favor solutions that demonstrate secure data transmission protocols and offer end-to-end protection, recognizing that security is a prerequisite for reliable and trustworthy industrial operations.
Data Standardization and Interoperability Challenges
The promise of the Industrial Internet of Things (IIoT) and AI in vibration monitoring lies in achieving holistic visibility and integrated decision-making across industrial operations. However, a significant hurdle to realizing this vision is the challenge of data standardization and interoperability.
Importance of Standardization: Data standardization is the process of converting the enormous volume of incoming information from diverse sources into a common, consistent format. This is crucial because it allows various end-users—from operators and technicians to line supervisors and executives—to effectively utilize the insights revealed in the data.57 The ultimate goal is to automate the collection of disparate data sources and autonomously translate them into a single, common model that can be consumed by both human users and other systems for analysis and actionability.57 Standardized data is essential for advanced analytics, enabling real-time condition status updates and seamless integration with other critical business intelligence software, such as Manufacturing Execution Systems (MES) and Enterprise Resource Planning (ERP) systems.57 This integration provides better insights into production and facilitates sharper decision-making across the organization.57
Challenges: The vibration monitoring market, particularly within the IIoT context, faces "fragmented wireless standards causing interoperability issues".26 This fragmentation means that data from different sensor manufacturers, legacy systems, or even different departments within the same organization may not "speak the same language." This lack of a common data model significantly hinders the ability to aggregate, analyze, and leverage data from diverse sources effectively, creating data silos that impede comprehensive monitoring and integrated decision-making.26
Solutions: To overcome these challenges, several approaches are being adopted. Data-tag mapping software, often implemented on edge devices, can transform raw data into a common model before it is transmitted to the cloud for further analysis.57 This edge-based processing helps to normalize inputs at the source. Furthermore, digital twin implementations contribute to data standardization by providing "contextualized asset models" that help to unify and make sense of diverse data streams from physical assets.20 These solutions are critical for ensuring that the vast amounts of data collected can be effectively utilized to drive predictive maintenance and operational improvements.
The bottleneck of data silos in a connected ecosystem is a fundamental impediment to achieving the full potential of IIoT and AI in industrial settings. If data from different sensors or systems cannot be easily integrated and understood due to fragmented standards, the vision of holistic visibility and integrated decision-making is severely hampered. Data standardization is the critical missing link that enables true "comprehensive monitoring" and prevents the overwhelming volume of data from becoming a source of paralysis rather than power. The implication is that while wireless sensors are dominating data collection, the true value extraction in 2025 and beyond will depend heavily on overcoming these interoperability challenges through industry-wide data standardization efforts and the widespread adoption of platforms capable of ingesting, normalizing, and integrating diverse data streams. This will be a key area of focus for industrial digital transformation.
Emerging Technologies and Trends Beyond 2025: Digital Twins, Edge Computing, 5G/6G, and Self-Powered Sensors
The rapid evolution of technology ensures that the state of vibration monitoring in 2025 is merely a waypoint on a continuous journey of innovation. Beyond the current year, several emerging technologies are poised to further revolutionize industrial operations, pushing the boundaries of predictive maintenance and asset intelligence.
Digital Twins (DTs)
Digital Twins are virtual replicas of physical assets, systems, or processes that are continuously updated with real-time data from their physical counterparts.58 These dynamic models enable real-time monitoring, advanced analytics, and precise forecasting of equipment health.58 By integrating IoT sensors, AI, and Machine Learning, Digital Twins can simulate various maintenance scenarios, optimize maintenance planning, and accurately predict failures.58 They serve as a "virtual testing ground," allowing manufacturers to evaluate different maintenance strategies without disrupting actual operations.58 For instance, in manufacturing, critical assets like motors, turbines, and pumps can be monitored in real-time through their digital twins, enabling proactive interventions.58
Digital Twins are evolving into the "brain" for prescriptive maintenance. While predictive maintenance informs when a failure might occur, Digital Twins, through their simulation and optimization capabilities, move beyond mere prediction to prescription. They can suggest what specific action to take and how to optimize it, effectively closing the loop between data, insight, and actionable intervention.51 The integration of Digital Twins with advanced AI models further enhances their ability to provide highly precise and actionable recommendations, leading to increasingly autonomous and self-optimizing industrial systems. Beyond 2025, Digital Twins will be central to enabling intelligent, simulated-validated decision-making for maintenance and broader operational adjustments.
Edge Computing
Edge computing involves offloading computational and analytical workloads from centralized cloud servers to IoT edge devices, processing data closer to its source.29 This paradigm offers significant advantages for vibration monitoring, including accelerated real-time decision-making, substantial reductions in bandwidth requirements for data transmission (with some methods reducing data by up to 95%), and decreased storage and computation workloads on cloud servers.29 Edge computing is particularly essential for proactive maintenance and real-time fault diagnosis, where immediate action based on sensor data is critical.29
Edge computing acts as a crucial bridge for real-time, secure, and efficient data flow. The immense volume of data generated by continuous vibration monitoring can strain cloud infrastructure and introduce unacceptable latency for time-sensitive applications. Edge computing addresses this by performing initial data processing and analysis at the source, which is critical for immediate responses to detected anomalies.12 Furthermore, processing sensitive data locally at the edge can enhance cybersecurity by reducing the amount of raw data transmitted over networks.53 The implication is that edge computing will become an increasingly vital component of IIoT architectures, enabling faster, more efficient, and more secure vibration monitoring systems, especially for critical, high-frequency data streams.
5G/6G Connectivity
The advent of 5G connectivity, and the anticipated development of 6G, provides the necessary communication backbone for the next generation of industrial IoT and vibration monitoring. 5G offers high bandwidth and ultra-low latency, which are crucial for transmitting rich data streams, including high-definition video feeds and complex sensor data from industrial machinery.64 This capability enables near-instantaneous data analysis and response, removing bottlenecks that previously hindered real-time applications.64 It also reduces restrictions on speed and bandwidth, allowing for the deployment of more sensors and the collection of even greater volumes of data.61 Looking further ahead, 6G is being developed to meet the imperative needs of future network deployments, promising even greater speeds, lower latencies, and massive device support.65
5G and 6G are poised to enable hyper-connected, real-time industrial environments. The effectiveness of advanced vibration monitoring, AI-driven analytics, and Digital Twin simulations relies heavily on seamless, high-speed data transmission. These next-generation communication technologies provide the essential infrastructure to support the massive number of connected devices and the real-time data flows required for truly responsive predictive maintenance.64 The implication is that the widespread availability of 5G and the future development of 6G will significantly accelerate the adoption of advanced vibration monitoring solutions, particularly wireless ones, by eliminating communication bottlenecks and enabling more pervasive and real-time data collection and analysis, thereby unlocking the full potential of IIoT.
Self-Powered Sensors (Energy Harvesting)
A significant operational challenge for widespread wireless sensor deployment is the reliance on batteries and the associated maintenance burden of replacement. Self-powered sensors directly address this by harvesting energy from their surrounding environment, eliminating the need for external power sources or frequent battery changes.67 These sensors can convert various forms of ambient energy, such as mechanical vibrations, thermal gradients, light, or magnetic fields, into usable electrical power.67 This capability enables stable, continuous data acquisition for extended periods, even in hard-to-reach or hazardous locations where manual battery replacement is impractical or dangerous.67
Triboelectric nanogenerators (TENGs) represent a key advancement in this area, enabling the development of self-driven wireless temperature, humidity, and vibration monitoring and alarm systems.68 Researchers are developing innovative designs, such as series-resistor-enhanced TENGs, that can efficiently harvest vibration energy while simultaneously sensing signals, providing high output voltages even at low vibration amplitudes.68 The global energy harvesting system market is projected to reach USD 1.53 billion by 2033, exhibiting a CAGR of 10.45% from 2025-2033, indicating strong commercial interest in these sustainable power solutions.71
Self-powered sensors are emerging as the ultimate enabler for "fit-and-forget" deployments. By eliminating the need for battery maintenance, they remove a major logistical hurdle for continuous, widespread, and long-term asset monitoring. This not only reduces operational costs but also significantly increases the feasibility of deploying sensors in challenging and remote industrial environments. The implication is that beyond 2025, self-powered vibration sensors will be a game-changer, further accelerating the dominance of wireless solutions by making truly ubiquitous and maintenance-free deployments a widespread reality.
IX. Conclusion: Charting the Course for Smarter Operations
In 2025, vibration monitoring stands as an indispensable tool for industrial efficiency and reliability, fundamentally transformed by the pervasive adoption of wireless sensor technologies and the analytical power of AI/ML-driven predictive maintenance. The market trajectory clearly indicates robust growth for these integrated solutions, signifying a profound shift in how industries approach asset management.
The ascendancy of wireless vibration sensors is not merely a transient trend but a strategic evolution. It is driven by their unparalleled scalability, ease of deployment, and favorable total cost of ownership, making them the preferred choice for widespread industrial applications. While specialized wired sensors will retain their niche for extreme precision or high-fidelity requirements, the overall landscape is increasingly dominated by wireless solutions.
The true value derived from vibration monitoring is unlocked through a sophisticated interplay of advanced data acquisition, cutting-edge signal processing techniques, and the transformative capabilities of AI and machine learning. These technologies collectively enable highly accurate anomaly detection, precise fault diagnosis, and reliable Remaining Useful Life (RUL) prediction. Platforms such as Factory AI exemplify this integration, offering comprehensive solutions that translate complex data into actionable insights, directly leading to reduced unplanned downtime, significant cost savings, and enhanced operational safety.
Looking towards the future, the continuous evolution of digital twins, edge computing, and advanced communication networks like 5G and the nascent 6G will further refine and expand the capabilities of vibration monitoring. These technologies will facilitate the transition towards increasingly autonomous and prescriptive maintenance paradigms, where systems not only predict failures but also recommend optimal interventions. The emergence of self-powered sensors, capable of harvesting energy from their environment, promises to overcome the last major logistical hurdle of power management, paving the way for truly ubiquitous and maintenance-free deployments.
For organizations seeking to maintain a competitive edge and ensure operational resilience, several strategic recommendations emerge. Prioritizing investment in integrated wireless vibration monitoring solutions, coupled with robust cybersecurity measures, is paramount. A steadfast commitment to data standardization and interoperability will be crucial to unlock the full potential of interconnected IIoT ecosystems. Furthermore, embracing AI/ML-driven platforms and actively exploring emerging technologies like digital twins and self-powered sensors will be essential for achieving sustainable growth and leadership in the evolving industrial landscape. The future of industrial maintenance is undeniably proactive, intelligent, and deeply integrated with the digital fabric of Industry 4.0.
Works cited
- Global Wireless Vibration Sensor Market Size 2025-2034 - CMI, accessed on July 18, 2025, https://www.custommarketinsights.com/report/wireless-vibration-sensor-market/
- Vibration Sensor Market Size to Reach USD 13.25 Billion by 2034 - Precedence Research, accessed on July 18, 2025, https://www.precedenceresearch.com/vibration-sensor-market
- Future-Forward Strategies for Wireless IoT Vibration Sensor Node Industry, accessed on July 18, 2025, https://www.datainsightsmarket.com/reports/wireless-iot-vibration-sensor-node-1639802
- Enhance your maintenance with vibration monitoring and analysis | Fluke, accessed on July 18, 2025, https://www.fluke.com/en-us/products/condition-monitoring/vibration
- Wired vs. Wireless Monitoring: Why Wireless Is the Future - Packet Power, accessed on July 18, 2025, https://www.packetpower.com/blog/wired-vs-wireless-monitoring-systems
- Future of Predictive Maintenance with AI and Machine Learning - VisionX, accessed on July 18, 2025, https://visionx.io/blog/future-of-predictive-maintenance/
- Factory AI | Predictive Maintenance & AI-Powered CMMS Software, accessed on July 18, 2025, https://f7i.ai/
- Vibration Sensor: Definitions, Applications and How to Use it - ETS Solutions Asia, accessed on July 18, 2025, https://www.etssolution-asia.com/blog/vibration-sensor-definitions-applications-and-how-to-use-it
- A History of Vibration Test Controllers - Crystal Instruments, accessed on July 18, 2025, https://www.crystalinstruments.com/history-of-vibration-test-controllers
- Why Use an FFT to Analyze Vibration Data - enDAQ Blog, accessed on July 18, 2025, https://blog.endaq.com/why-use-an-fft-to-analyze-vibration-data
- Demystifying Vibration Monitoring Part 1: Why Vibration Monitoring Matters—And How It Works | Pruftechnik, accessed on July 18, 2025, https://www.pruftechnik.com/understanding-vibration-monitoring-why-it-matters-part-1/
- Vibration Monitoring, Sensors & Noise: Comprehensive Guide - SVANTEK, accessed on July 18, 2025, https://svantek.com/academy/vibration-monitoring-guide/
- Data-Driven Maintenance Revolution: Insights for Smarter Decision Making, accessed on July 18, 2025, https://www.maintwiz.com/blog/data-driven-maintenance-revolution/
- Top 5 Emerging Trends in Condition Monitoring for 2025 - ConditionMeter, accessed on July 18, 2025, https://conditionmeter.com/en/blog/top-5-emerging-trends-in-condition-monitoring-for-2025
- Predictive Maintenance Case Studies: How Companies Are Saving Millions with AI-Powered Solutions - ProValet, accessed on July 18, 2025, https://www.provalet.io/guides-posts/predictive-maintenance-case-studies
- AI-Driven Predictive Maintenance for Smart Manufacturing and Industry 4.0 - ResearchGate, accessed on July 18, 2025, https://www.researchgate.net/publication/389498658_AI-Driven_Predictive_Maintenance_for_Smart_Manufacturing_and_Industry_40
- Faraday Predictive: Predictive Maintenance Made Simple, accessed on July 18, 2025, https://faradaypredictive.com/
- Vibration Equipment Analysis for Predictive Maintenance Success - Prometheus Group, accessed on July 18, 2025, https://www.prometheusgroup.com/learning-center/what-is-vibration-equipment-analysis
- From Vibrometers to Sensors, Cloud, and AI: How Modern Predictive Maintenance Works, accessed on July 18, 2025, https://www.iotforall.com/how-modern-predictive-maintenance-works
- Proven Advanced Predictive Maintenance for Energy & Utilities, accessed on July 18, 2025, https://www.numberanalytics.com/blog/proven-advanced-predictive-maintenance-energy-utilities
- What is a Vibration Sensor? Application, and its Types (2025) - Blikai, accessed on July 18, 2025, https://www.blikai.com/blog/sensors/what-is-a-vibration-sensor-application-and-its-types-2025
- 2024 product line & sales summary and 2025 roadmap - Broadsens, accessed on July 18, 2025, https://www.broadsens.com/news/2024-summary-and-2025-roadmaps/
- Wireless Vibration Sensor Technology: Benefits, Limitations, and Industrial Applications - Crystal Instruments, accessed on July 18, 2025, https://www.crystalinstruments.com/s/Wireless-Vibration-Sensor.pdf
- Wireless Vibration Sensor Technology: Benefits, Limitations, and ..., accessed on July 18, 2025, https://www.crystalinstruments.com/machine-condition-monitoring-articles/wireless-vibration-sensor-technology
- Revolutionizing Remote Monitoring: The Power of Wireless ..., accessed on July 18, 2025, https://www.iotforall.com/wireless-vibration-sensors
- Vibration Monitoring Market - Size, Report Analysis & Companies - Mordor Intelligence, accessed on July 18, 2025, https://www.mordorintelligence.com/industry-reports/vibration-monitoring-market
- Mastering Sampling Rate in Vibration Analysis - Number Analytics, accessed on July 18, 2025, https://www.numberanalytics.com/blog/ultimate-guide-to-sampling-rate-in-vibration-analysis
- The Impact of Sampling Rate on Vibration Analysis - Number Analytics, accessed on July 18, 2025, https://www.numberanalytics.com/blog/impact-of-sampling-rate-on-vibration-analysis
- IoT Sensor Node with Edge Computing for Efficient Vibration Monitoring of Industrial Motors | Request PDF - ResearchGate, accessed on July 18, 2025, https://www.researchgate.net/publication/391031160_IoT_Sensor_Node_with_Edge_Computing_for_Efficient_Vibration_Monitoring_of_Industrial_Motors
- Practical Introduction to Frequency-Domain Analysis - MATLAB & - MathWorks, accessed on July 18, 2025, https://www.mathworks.com/help/signal/ug/practical-introduction-to-frequency-domain-analysis.html
- acoem.us, accessed on July 18, 2025, https://acoem.us/blog/other-topics/understanding-phase-analysis-in-vibration-diagnostics/#:~:text=Each%20plays%20a%20unique%20role,in%20relation%20to%20one%20another.
- Understanding Phase Analysis in Vibration Diagnostics - Acoem USA, accessed on July 18, 2025, https://acoem.us/blog/other-topics/understanding-phase-analysis-in-vibration-diagnostics/
- Advanced Vibration Signal Processing Techniques - Number Analytics, accessed on July 18, 2025, https://www.numberanalytics.com/blog/advanced-vibration-signal-processing-techniques
- Advanced Vibration Analysis Techniques - Number Analytics, accessed on July 18, 2025, https://www.numberanalytics.com/blog/advanced-vibration-analysis-techniques-predictive-maintenance
- Envelope Analysis: The Vibration Expert's - Number Analytics, accessed on July 18, 2025, https://www.numberanalytics.com/blog/envelope-analysis-vibration-expert-toolbox
- Mastering Envelope Analysis in Vibration - Number Analytics, accessed on July 18, 2025, https://www.numberanalytics.com/blog/ultimate-guide-envelope-analysis-vibration
- Revolutionizing Predictive Maintenance with AI/ML: From High-Tech to Legacy Systems, accessed on July 18, 2025, https://www.automation.com/en-us/articles/january-2025/predictive-maintenance-ai-ml-high-tech-legacy
- The Impact of AI on Predictive Maintenance - MultiSensor AI, accessed on July 18, 2025, https://www.multisensorai.com/blog/the-impact-of-ai-on-predictive-maintenance
- Research Progress on Data-Driven Industrial Fault Diagnosis Methods - PMC, accessed on July 18, 2025, https://pmc.ncbi.nlm.nih.gov/articles/PMC12074220/
- Technologies Driving Predictive Maintenance - WorkTrek, accessed on July 18, 2025, https://worktrek.com/blog/technologies-driving-predictive-maintenance/
- Research on a Bearing Fault Diagnosis Method Based on a CNN-LSTM-GRU Model - MDPI, accessed on July 18, 2025, https://www.mdpi.com/2075-1702/12/12/927
- Bearing fault diagnosis with parallel CNN and LSTM - AIMS Press, accessed on July 18, 2025, https://www.aimspress.com/article/doi/10.3934/mbe.2024105?viewType=HTML
- Comparative studies of deep learning neural network architectures in fault diagnosis of rubber vibration isolators, accessed on July 18, 2025, https://ceij.ut.ac.ir/article_101447_4d1abf67c67f9360e5b75d4181204ce9.pdf
- Using LSTM Recurrent Neural Networks to Predict Excess Vibration Events in Aircraft Engines, accessed on July 18, 2025, https://www.se.rit.edu/~travis/papers/2016_escience_vibration.pdf
- A Comparative Study of Deep-Learning Autoencoders (DLAEs) for Vibration Anomaly Detection in Manufacturing Equipment - MDPI, accessed on July 18, 2025, https://www.mdpi.com/2079-9292/13/9/1700
- Deep Learning for Anomaly Detection in CNC Machine Vibration Data: A RoughLSTM-Based Approach - MDPI, accessed on July 18, 2025, https://www.mdpi.com/2076-3417/15/6/3179
- Sensors, Volume 25, Issue 14 (July-2 2025) – 181 articles, accessed on July 18, 2025, https://www.mdpi.com/1424-8220/25/14
- What are some industry use cases for vibration analysis? - UpKeep, accessed on July 18, 2025, https://upkeep.com/learning/vibration-analysis-use-cases/
- Vibration monitoring applications and case studies - Wilcoxon Sensing Technologies, accessed on July 18, 2025, https://wilcoxon.com/resources/applications-and-case-studies/
- Harnessing the Power of Vibration Sensors in the Oil and Gas Industry - NCD.io, accessed on July 18, 2025, https://ncd.io/blog/harnessing-the-power-of-vibration-sensors-in-the-oil-and-gas-industry/
- Why Vibration Monitoring Matters in Data Centers - Pruftechnik, accessed on July 18, 2025, https://www.pruftechnik.com/why-vibration-monitoring-matters-in-data-centers/
- Predictive Maintenance in the Oil and Gas Industry | LLumin, accessed on July 18, 2025, https://llumin.com/predictive-maintenance-oil-and-gas/
- Industrial IoT Security Threats: Top Risks and Mitigation Strategies 2025 - Device Authority, accessed on July 18, 2025, https://deviceauthority.com/industrial-iot-security-threats-top-risks-and-mitigation-strategies-2025/
- The Industrial Internet of Things: What You Need To Know in 2025 - BizTech Magazine, accessed on July 18, 2025, https://biztechmagazine.com/article/2025/07/industrial-internet-things-what-you-need-know-2025-perfcon
- Best Practices to Secure IoT Devices in 2025 - Sattrix, accessed on July 18, 2025, https://www.sattrix.com/blog/iot-security-best-practices-2025/
- Industry News 2025 Mastering IoT Defense Strategies With Cybersecurity Education, accessed on July 18, 2025, https://www.isaca.org/resources/news-and-trends/industry-news/2025/mastering-iot-defense-strategies-with-cybersecurity-education
- The Importance of Data Standardization in Manufacturing - Machine Metrics, accessed on July 18, 2025, https://www.machinemetrics.com/blog/data-standardization-in-manufacturing
- Digital Twins for Predictive Maintenance - Acuvate, accessed on July 18, 2025, https://acuvate.com/blog/digital-twin-for-predictive-maintenance/
- (PDF) Applications of Digital Twins in Predictive Maintenance of Mechanical Systems, accessed on July 18, 2025, https://www.researchgate.net/publication/388414391_Applications_of_Digital_Twins_in_Predictive_Maintenance_of_Mechanical_Systems
- Digital Twin in Manufacturing: 10 Key Benefits & Use Cases - Litslink, accessed on July 18, 2025, https://litslink.com/blog/what-is-digital-twin-in-manufacturing-inspiring-industry-examples
- IIoT Trends 2025 | ATS - Advanced Technology Services, accessed on July 18, 2025, https://www.advancedtech.com/blog/iiot-trends/
- Machine Condition Monitoring | Edge Computing - ADLINK Technology, accessed on July 18, 2025, https://www.adlinktech.com/en/machine_condition_monitoring
- Forescout's 2025 report reveals surge in device vulnerabilities across IT, IoT, OT, and IoMT, accessed on July 18, 2025, https://industrialcyber.co/reports/forescouts-2025-report-reveals-surge-in-device-vulnerabilities-across-it-iot-ot-and-iomt/
- The Impact of 5G on Real-Time Data and Business Responsiveness | Dehongi Blog, accessed on July 18, 2025, https://dehongi.com/blog/post/the-impact-of-5g-on-real-time-data-and-business-responsiveness/
- (PDF) Future Wireless Communication Technology towards 6G IoT: An Application-Based Analysis of IoT in Real-Time Location Monitoring of Employees Inside Underground Mines by Using BLE - ResearchGate, accessed on July 18, 2025, https://www.researchgate.net/publication/360327151_Future_Wireless_Communication_Technology_towards_6G_IoT_An_Application-Based_Analysis_of_IoT_in_Real-Time_Location_Monitoring_of_Employees_Inside_Underground_Mines_by_Using_BLE
- Future Wireless Communication Technology towards 6G IoT: An Application-Based Analysis of IoT in Real-Time Location Monitoring of Employees Inside Underground Mines by Using BLE - MDPI, accessed on July 18, 2025, https://www.mdpi.com/1424-8220/22/9/3438
- Self-powered sensor automatically harvests magnetic energy | MIT News, accessed on July 18, 2025, https://news.mit.edu/2024/self-powered-sensor-harvests-magnetic-energy-0118
- Self‐Powered Vibration Sensing and Energy Harvesting via Series‐Resistor‐Enhanced Triboelectric Nanogenerators with Charge Compensation for Autonomous Alarm Systems | Request PDF - ResearchGate, accessed on July 18, 2025, https://www.researchgate.net/publication/388842001_Self-Powered_Vibration_Sensing_and_Energy_Harvesting_via_Series-Resistor-Enhanced_Triboelectric_Nanogenerators_with_Charge_Compensation_for_Autonomous_Alarm_Systems
- Self-powered sensing for health monitoring and robotics - OAE Publishing Inc., accessed on July 18, 2025, https://www.oaepublish.com/articles/ss.2024.65
- Self‐Powered Vibration Sensing and Energy Harvesting via Series‐Resistor‐Enhanced Triboelectric Nanogenerators with Charge Compensation for Autonomous Alarm Systems - DOI, accessed on July 18, 2025, https://doi.org/10.1002/ente.202402284
- Energy Harvesting Systems Market Report 2025-2033 - - GlobeNewswire, accessed on July 18, 2025, https://www.globenewswire.com/news-release/2025/02/25/3031767/28124/en/Energy-Harvesting-Systems-Market-Report-2025-2033-Increasing-Focus-on-Green-Energy-Solutions-and-Reducing-Greenhouse-Gas-Emissions-Driving-Market-Revenues-to-1-53-Billion-by-2033.html
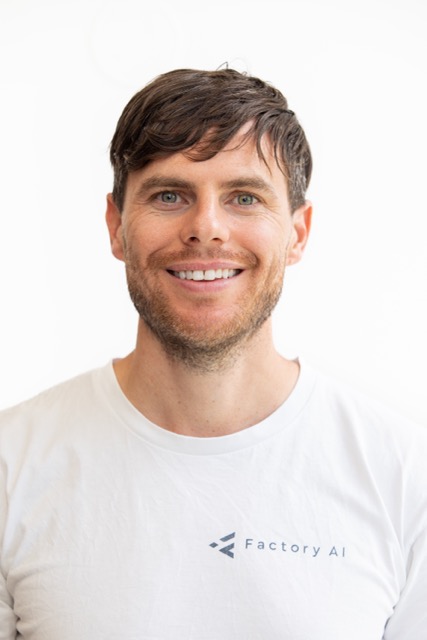