The Costly Impact of Unplanned Downtime in Animal Feed Production
Apr 3, 2025
Predictive Maintenance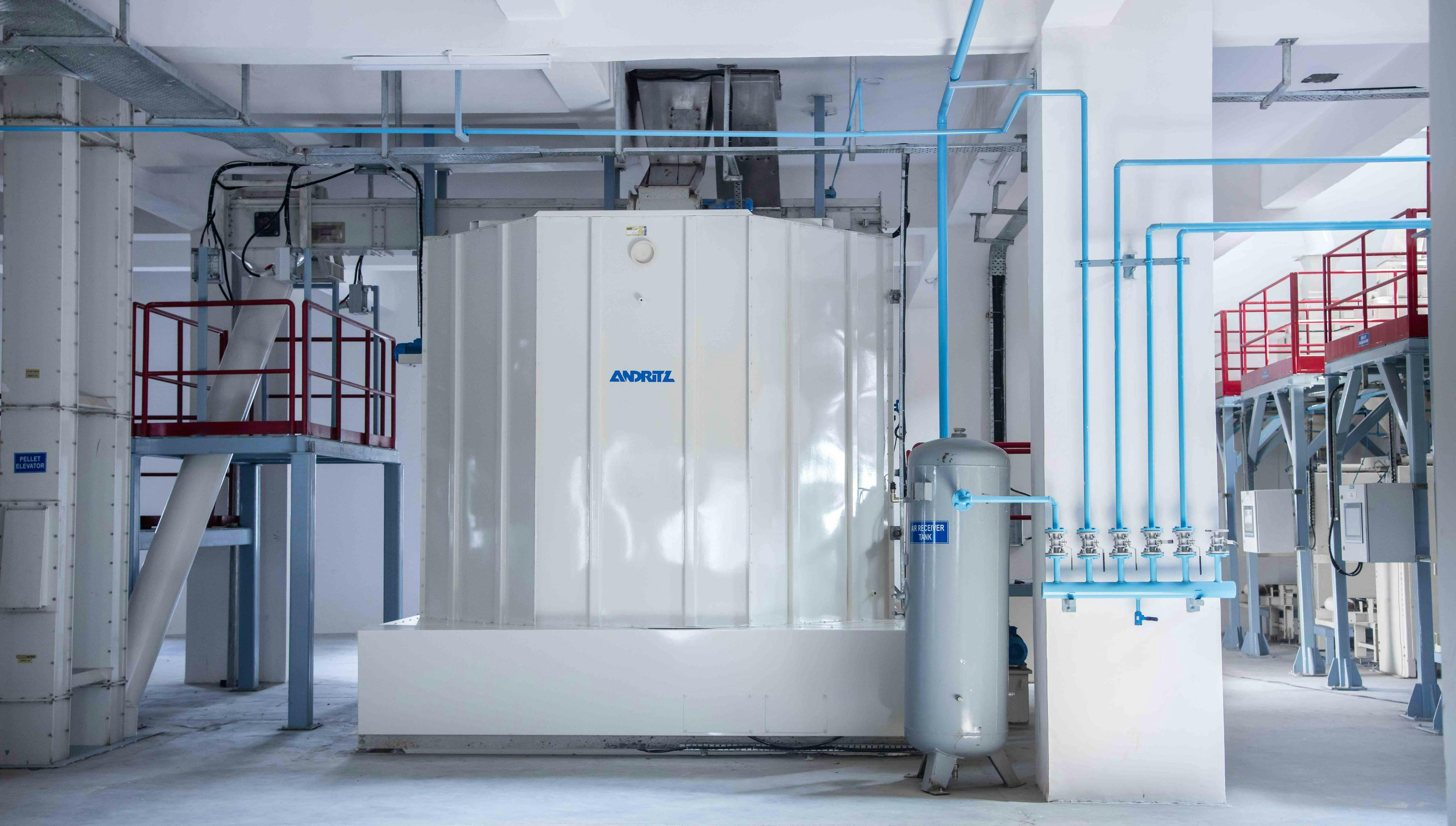
Animal feed production is a cornerstone of the global agricultural value chain, with companies worldwide relying on efficient operations to meet demand. However, like any manufacturing environment, unplanned equipment breakdowns can bring production to a screeching halt. These interruptions don't just cost time and money; they risk crucial supply chain commitments to farmers and partners.
This post will delve into the often-hidden costs of downtime specific to animal feed production. We'll identify the critical assets most prone to causing these disruptions and explore how leveraging predictive maintenance strategies can significantly reduce breakdowns, ensuring your feed mill operates smoothly and reliably.
The Costly Impact of Unplanned Downtime in Milk & Yogurt Production
Animal feed production is a critical part of Australia’s and the world’s agricultural value chain. Companies like Ridley, Reid Stockfeeds, Harwood Grains, Cargill, New Hope Liuhe, Muyuan Foodstuff, BRF, ForFarmers, Tyson Foods, and Nutreco and others in the industry rely on smooth production to meet demand and maintain quality. But like any production environment, unplanned equipment breakdowns can bring everything to a halt, costing time, money, and risking supply chain commitments to farmers and partners.
In this post, we break down the hidden costs of downtime in animal feed production, look at some of the assets most likely to cause issues, and explore how predictive maintenance can reduce breakdowns and keep feed mills running smoothly.
What Causes Downtime in Animal Feed Production?
Manufacturing animal feed involves a complex, continuous process, including grinding, mixing, pelleting, cooling, and packaging. This means a variety of rotating and processing equipment is constantly at work. Some of the most common culprits of downtime include the below.
Hammer Mills (Grinding Systems)
Hammer mills are critical to breaking down grain, proteins, and additives into fine particles for animal feed. They rely on high-speed rotating shafts with hammers or blades.
Common Failures:
- Bearing wear or failure from constant high-speed rotation
- Imbalance or misalignment of hammers, leading to shaft vibration
- Motor or gearbox overheating under excessive load
How Vibration & Temperature Sensors Help:
- Vibration sensors detect early bearing faults, misalignment, or imbalance that increase vibration as they worsen.
- Temperature sensors catch bearing overheating or motor stress long before failure.
- Together, these sensors give weeks of warning before breakdown, allowing scheduled bearing replacements or hammer adjustments, preventing mill stoppages.
Hammer mills, found in various shapes and sizes, often emerge as a frequent cause of unplanned downtime at sites, often lacking redundancy to mitigate disruptions when issues arise.
Mixers (Horizontal/Vertical Feed Blenders)
Mixers are essential for homogeneously blending nutrients, minerals, and proteins into feed. They use rotating shafts with paddles or ribbons inside large chambers.
Common Failures:
- Bearing and gearbox failure due to heavy torque loads and material buildup
- Coupling misalignment between motor and mixer shaft
- Motor overload from compacted material or foreign objects
How Vibration & Temperature Sensors Help:
- Vibration sensors detect gearbox wear, shaft misalignment, and coupling issues.
- Temperature sensors pick up overheated bearings and motor strain, often due to material blockages.
- Early detection means avoiding catastrophic gearbox failure or snapped shafts, saving tens of thousands in repair costs.
Mixer motors may be reliable, but given their critical role in the production process, they often lead to an "oh shit" moment when something goes wrong. Sites want these motors covered to ensure peace of mind.
Pellet Mills and Presses
Pellet mills compress mixed feed into pellets using roller dies under high pressure. These are high-torque, high-pressure machines prone to mechanical stress.
Common Failures:
- Roller and die bearing failures from extreme pressure
- Gearbox and drive motor wear due to sustained high loads
- Roller misalignment or slippage, creating uneven pellets and internal stress
How Vibration & Temperature Sensors Help:
- Vibration sensors detect roller and die bearing wear, as well as gearbox damage.
- Temperature sensors highlight overheating bearings—a sign of lubrication issues or imminent failure.
- Early warnings prevent entire roller die assemblies seizing, which can take days to repair and cost heavily in lost production.
Bucket Elevators and Screw Conveyors
These systems move raw materials and finished feed through various production stages. Constantly in motion, they suffer from wear and misalignment.
Common Failures:
- Motor and gearbox failures from high torque
- Belt misalignment or slippage on bucket elevators
- Bearing wear on rotating shafts and pulleys
How Vibration & Temperature Sensors Help:
- Vibration sensors pick up early-stage gearbox wear, misalignment, and belt tension problems.
- Temperature sensors monitor motor and bearing heat rise, catching strain before failure.
- This allows planned repairs before conveyors stop moving feed, avoiding full-line stoppages.
Packaging Conveyors
This isn’t one you would have thought about at first. In fact you’re probably raising your eyebrows now. Here’s the thing; the small motors driving conveyors are particularly susceptible to being missed if you have very short maintenance windows. Add to this that some of these conveyors will be overhead and therefore hard to access, and you are prone to missing the classic belt wear and bearing issues on them.
For this reason, leveraging consistent vibration and temperature condition monitoring will do a great job here to prevent unexpected failures that could halt production. Here, you will be able to detect early signs of bearing degradation and belt wear, allowing maintenance teams to schedule repairs during planned downtime.
Some sites will have multiple dozens of these motors, and with some experiencing a MTBF that’s quite low, these can form a great part of a pilot program to prove the technology will work well at your site. We wrote more about how specifically we have a history of preventing failures on them in this article : From Preventive to Predictive Conveyor Maintenance in the food and beverage industry.
The small, humble and reliable conveyor motor that can halt production at anytime and often gets missed in maintenance windows given it's too hard to access.
Coolers and Dryers
Coolers and dryers are used to remove heat and moisture from feed pellets, a critical step for quality and storage life. They involve rotating fans, conveyors, and blowers.
Common Failures:
- Fan and blower bearing failures due to high-speed rotation and heat exposure
- Motor overheating on fans and conveyors
- Gearbox wear driving rotary coolers or belts
How Vibration & Temperature Sensors Help:
- Vibration sensors detect bearing issues and balance problems in fans and rotary parts.
- Temperature sensors warn of motor overheating—often the first sign of an impending failure.
- Preventing a failure in coolers/dryers maintains feed quality and throughput, avoiding costly product waste or rework.
Coolers and dryers are another potential showstopper when things go wrong. While generally reliable, their installation on many sites makes repairs inconvenient and time-consuming.
How Much Does Downtime Really Cost?
While every site is different, downtime costs for a large animal feed mill can quickly add up. Let's break it down:
Of course, this largely depends on your company's financial profile and the specifics of your site. However, based on numerous industry conversations, we estimate that, conservatively, a 4-hour unexpected breakdown could cost between $35,000 and $50,000—excluding the downstream impacts on supply chain and customer satisfaction.
The Bottom Line: Why It Matters
Across Ridley, Reid Stockfeeds, Harwood Grains, Cargill, New Hope Liuhe, Muyuan Foodstuff, BRF, ForFarmers, Tyson Foods, Nutreco, and others in the animal feed industry, using indicators like continuous vibration and temperature monitoring will give a crucial early warning system, allowing maintenance teams to fix issues before they become breakdowns.
Instead of reacting to failures and scrambling for parts, predictive maintenance allows planned, cost-effective maintenance, keeping production lines moving and customers happy.
Challenges of Maintenance in a 24/7 Production Environment
Whilst this certainly isn't the case for everyone, a number of animal feed production facilities we’ve spoken with will operate around the clock to meet consumer demand for their popular products. This 24/7 manufacturing schedule presents unique challenges when it comes to equipment maintenance. With limited downtime available, maintenance teams have extremely tight windows to inspect, repair, or replace critical assets.
Any unplanned failure that occurs during active production can be catastrophic. As one reliability manager noted, the costs of such incidents go far beyond maintenance - unplanned downtime is considered a "marketing cost" that impacts the entire business.
For such sites, continuous, online condition monitoring is especially helpful for maintenance planning. If you have planned maintenance work orders on all of your conveyor motors, but your limited time window won't allow you to cover all of them, then having critical asset data on these will be the best way to help you coordinate your efforts.
The Power of Condition Monitoring
As we’ve suggested above when going over some key pieces of equipment, we’re seeing that implementing comprehensive vibration condition monitoring across critical assets has proven particularly effective for preventing unexpected failures in yogurt production. As a quick overview to dive deeper into some common failure modes, for filling machine motors, vibration analysis can detect:
- Early-stage bearing wear
- Belt misalignment
- Mounting looseness
- Shaft imbalance
In fermentation tank agitators, condition monitoring software can identify:
- Seal degradation patterns
- Bearing temperature anomalies
- Unusual vibration signatures
- Shaft alignment issues
Using AI to Predict Equipment Failures
The key to preventing costly failures lies in the ability to detect subtle anomalies that precede such events. By harnessing the power of artificial intelligence (AI) and machine learning, modern predictive maintenance software can analyse vast amounts of data from equipment sensors to pinpoint patterns indicative of impending failures.
At the core of this AI-driven solution is a sophisticated algorithm that continuously monitors data streams from critical components. This data encompasses a wide range of parameters, including temperature, pressure, vibration, and electrical signals. The AI model is trained to recognise normal operating patterns and identify deviations that may signal potential issues.
Why is AI better than thresholds?
Here’s another common question; Why is AI better than thresholds that are traditionally used in SCADA systems?
AI-powered predictive maintenance models offer significant advantages over traditional threshold-based monitoring systems. While conventional systems rely on pre-set thresholds based on generic motor classifications, AI models learn from your specific equipment's actual operating patterns. This contextual learning is crucial because each production facility operates its assets differently, making standardised thresholds less effective. This is especially true for production related equipment; if you run multiple different products on the same lines (a common occurrence for brands that market many different flavours, and with marketing departments that like to create punchy temporary products), than thresholds will fire off lots of false positives when a new product that is more demanding on your equipment starts to get produced.
For equipment that operate with a more consistent operational profile, AI's more sophisticated pattern recognition capabilities can detect subtle changes in equipment behaviour long before they would trigger traditional thresholds. This enhanced sensitivity provides maintenance teams with greater lead time to plan and execute repairs, shifting from reactive maintenance to truly predictive interventions. The AI approach also eliminates the complicated and often imprecise process of manually setting and adjusting threshold values, resulting in more accurate and site-specific early warning detection.
For Sites Already doing Manual Inspections: What’s The Value of Online Condition Monitoring?
While manual vibration inspections have traditionally been a cornerstone of maintenance programs, online condition monitoring offers significant advantages for yogurt producers. Manual inspections, typically performed monthly or quarterly, can miss critical developments that occur between measurements. Here's why continuous online monitoring represents a crucial upgrade for modern production facilities:
Catching Rapid Deterioration
Some equipment failures can develop rapidly, especially in high-speed production environments. A bearing might show normal readings during a monthly inspection but fail catastrophically just days later. Online condition monitoring software provides continuous oversight, catching sudden changes in equipment health that manual inspections might miss.
Comprehensive Data Analysis
Manual inspections provide only periodic snapshots of machine health, making it difficult to identify subtle trends or patterns. Online monitoring captures continuous data streams, enabling advanced analysis of:
- Long-term deterioration patterns
- Correlation between operating conditions and equipment stress
- Impact of process changes on machine health
- Early warning signs that might be invisible in monthly readings
Real-World Production Context
Online monitoring systems can correlate equipment behaviour with actual production conditions. This context is invaluable for understanding how different product types, speeds, and operating parameters affect machine health - insights that are impossible to gather from periodic manual measurements.
Cost-Effective Resource Allocation
While manual inspections require significant time and labour investment, online condition monitoring software can monitor hundreds of assets simultaneously. This allows maintenance teams to:
- Focus their efforts on genuinely problematic equipment
- Eliminate unnecessary routine inspections
- Reduce travel time between sites
- Deploy specialist resources more effectively
24/7 Protection
In round-the-clock production environments, equipment failures don't wait for scheduled inspection times. Online monitoring provides constant vigilance, ensuring that potential issues are flagged immediately, regardless of the time of day or day of the week.
Enhanced Predictive Capabilities
By combining continuous monitoring with machine learning algorithms, modern predictive maintenance software can:
- Learn normal behaviour patterns for specific equipment
- Detect subtle deviations that might indicate emerging problems
- Predict potential failures weeks or months in advance
- Provide increasingly accurate remaining useful life estimates
Integration with Production Systems
Online monitoring systems can integrate with broader production management software, enabling:
- Automatic production adjustments based on equipment health
- Coordination of maintenance activities with production schedules
- Real-time alerts to operators and maintenance teams
- Comprehensive reporting and trend analysis
Conclusion : Getting Started with Predictive Maintenance
Taking the first step towards implementing an AI-powered predictive maintenance program can seem daunting. However, with the right approach and a trusted partner, you can unlock significant cost savings, increase asset reliability, and optimise your maintenance operations.
Key considerations include:
- #1 - Conducting an initial asset survey : Begin with a structured assessment of your critical equipment. Our proven 8-step evaluation matrix helps identify the assets that will provide the highest return on your predictive maintenance investment. This systematic approach ensures your program starts with clear objectives and measurable outcomes.
- #2 - Establishing data integration protocols : Prioritise your integration needs by distinguishing between essential integrations and nice to have. This helps avoid scope creep while ensuring your core maintenance objectives are met effectively and efficiently.
- #3 - Implementing comprehensive condition monitoring software vs. running pilot programs : Starting with predictive maintenance doesn't require a full-scale deployment. Many successful programs begin with targeted pilot projects focused on critical assets combined with other assets with a lower MTBF. We can connect you with customers who have successfully scaled from modest pilots to comprehensive programs, demonstrating the value of starting small and growing strategically.
- #4 - Training maintenance teams : So much of transitioning to predictive maintenance is about behaviour and culture change. Anytime a workflow we’ve used for years becomes different, we all need a hand to get enabled, and support along the way.
- #5 - Continuously optimising and expanding the program : The majority of our successful customers have adopted a layered approach to their predictive maintenance journey. Start small, build on the wins, and continue to improve.
By following these steps and partnering with an experienced predictive maintenance provider, you can unlock the full potential of AI-driven maintenance, reducing downtime, minimising product loss, and maximising the lifespan of your critical assets.
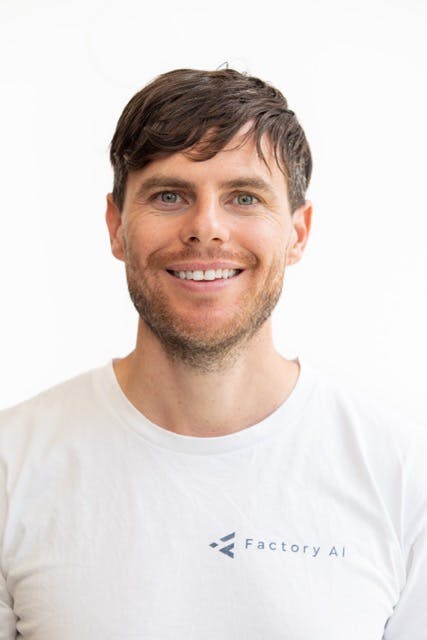
JP Picard
Jean-Philippe Picard is the CEO and Co-Founder of Factory AI. As a positive, transparent, and confident business development leader, he is passionate about helping industrial sites achieve tangible results by focusing on clean, accurate data and prioritizing quick wins. Jean-Philippe has a keen interest in how maintenance strategies evolve and believes in the importance of aligning current practices with a site’s future needs, especially with the increasing accessibility of predictive maintenance and AI. He understands the challenges of implementing new technologies, including addressing potential skills and culture gaps within organizations.