Say hello to Factory AI
Jun 7, 2024
Our Story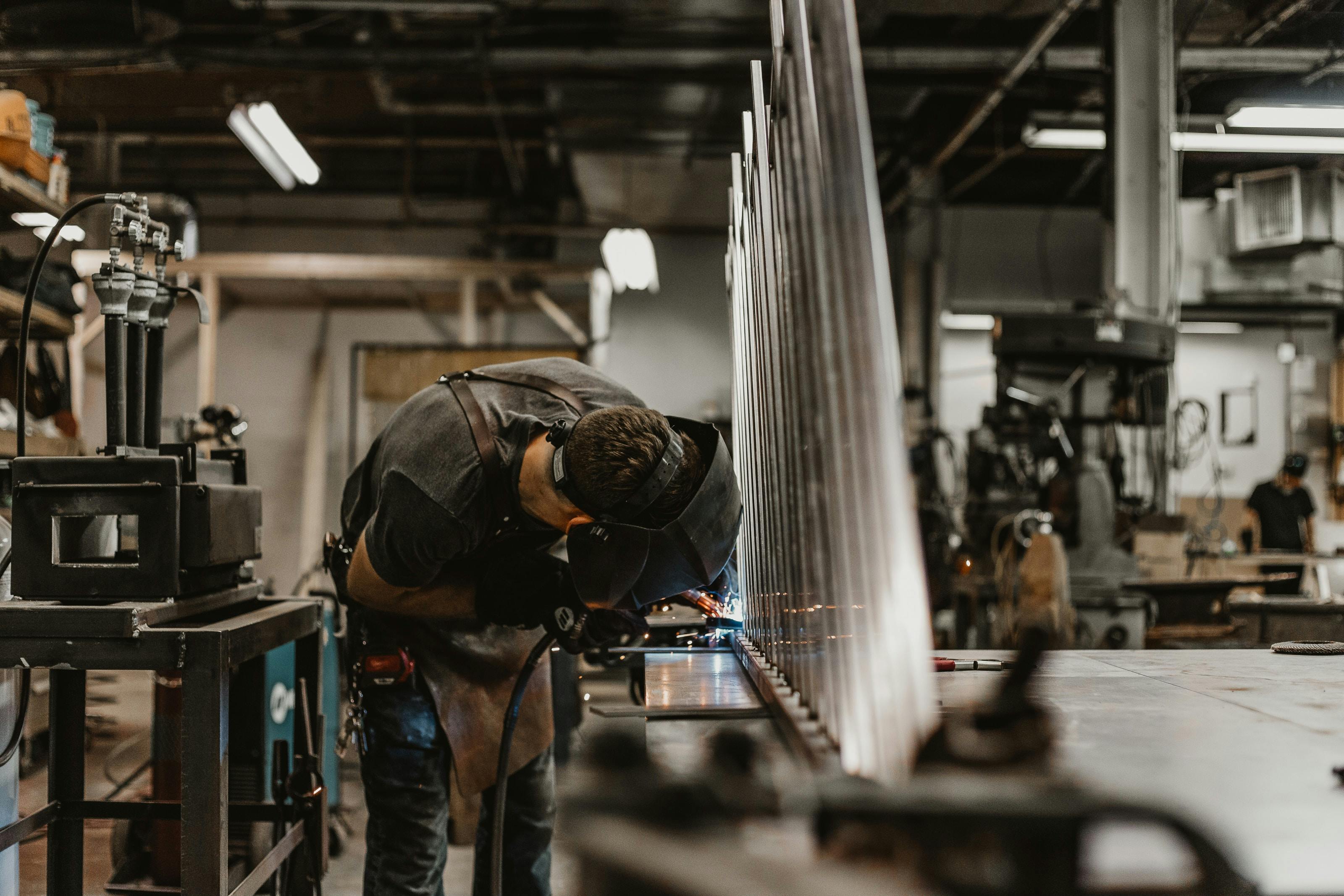
Explore our origin story, discover our distinctive qualities, and delve into our perspective on the pivotal juncture facing the manufacturing industry
Introduction
Five years ago, on a cold and wet British morning, I made my way to the site of one of our clients, where we were working on digital transformation project. After spending the morning talking to the team, we were invited to tour the factory. During the tour, I observed that the factory noise had ceased, and production had come to a halt.
What had happened? Operators and engineers and managers, who had appeared focused and collected just moments ago, now displayed looks of concern and immediately sprang into action. This specific client, one of the world’s largest automobile manufacturers, estimated that this brief period of downtime would cost them millions.
Following this painful experience, our team shifted our efforts from the ongoing project to help them mitigate the likelihood of such a distressing event occurring again in the future.
Our Journey So Far
Factory AI was established with a clear mission: to make innovation accessible to all in the manufacturing sector.
While working on the project I mentioned in the introduction, along with dozens of others during my time at AWS, I observed various ironies within the realm of manufacturing.
One such irony is that few industries amass as much operational data as manufacturers, yet only the top 1% seem capable of unlocking the transformative potential residing within this data. Others lack the internal resources, whether in terms of time or skillset, to harness their data effectively. With slim margins constantly under pressure, most manufacturers understandably hesitate to invest significant sums upfront without a proven return on investment (ROI).
These challenges faced by our customers were the driving force behind our inception.
Why now?
The concept of condition monitoring (CM) is not new. The use of condition monitoring to enhance productivity and minimise downtime has been feasible for quite some time.
There is evidence that as far back as the 1960s, European facilities were already implementing CM (Hoogovens, 1961, Maintenance in a new light).
What has changed in the last decade is the incredible advancement in artificial intelligence, which can elevate the benefits of condition monitoring to an entirely new level. AI enables vastly superior anomaly detection, fault classification, prediction of useful life, integration, and significantly extends the window for failure forecasting.
What excites us at Factory AI the most is the democratization of other tools within the tech stack, enabling integrations with other facets of manufacturing operations that were previously unattainable. This positions us uniquely to facilitate a genuine digital transformation in manufacturing.
On the human side of the equation, manufacturers are grappling with the challenge of an aging workforce. As the younger demographic becomes more interested in emerging industries, hiring for engineering and maintenance roles has become more challenging than ever before.
Whether manufacturers embrace it or not, this reality will act as a catalyst for digital adoption across the manufacturing sector in the coming decades.
How we’re unique
The potential future of Industry 4.0 remains out of reach for most, accessible only to the top 1%.
Evidence of this lies in the fact that many readers going through this article are likely rolling their eyes, considering all the reasons why these digital advancement concepts, theoretically, might be too difficult to implement in practice.
Traditionally, providers of such solutions needed to embark on complex custom developments for each new client. The result was high upfront costs, extended development and deployment timelines, and a significant risk of failing to achieve a satisfactory ROI.
At Factory AI, our distinct expertise and approach set us apart. We are now demonstrating that artificial intelligence can be harnessed by manufacturers in the food and beverage industry to reduce downtime, alleviate workloads, and offer unprecedented benefits to reliability and maintenance teams.
This time it’s different
The manufacturing industry finds itself at a pivotal juncture. Choosing the status quo in a rapidly evolving digital landscape can lead some to fall behind. At the same time, it provides others a chance to establish a strong competitive advantage.
Embracing Innovation: Your Ideas Welcome
If you have audacious and unconventional ideas aimed at enhancing the reliability of your operations, we would love a conversation. Our doors are wide open, ready to receive your ideas and engage in discussions on how we can collaborate to assist you.
Persisting in the Pursuit
In the meantime, continue to tackle complex challenges head-on. By persistently solving intricate problems, you contribute to the advancement of our industry. Here’s to solving difficult problems.
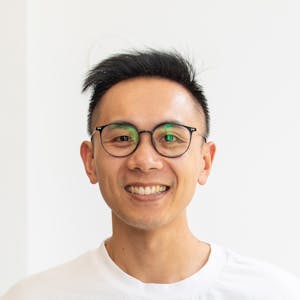
Tim Cheung
Tim is the Co-Founder and CTO of Factory AI. Previously, he served as a Solutions Architect at AWS, guiding CxOs at PE firms, UK-based Digital Native scale-ups, and Enterprises across Energy, Utilities, Automotive, Manufacturing, and Construction throughout their cloud adoption journey.