Process vs. Procedure: The Billion-Dollar Difference Your Maintenance Team Can’t Afford to Ignore
Jul 16, 2025
process vs procedure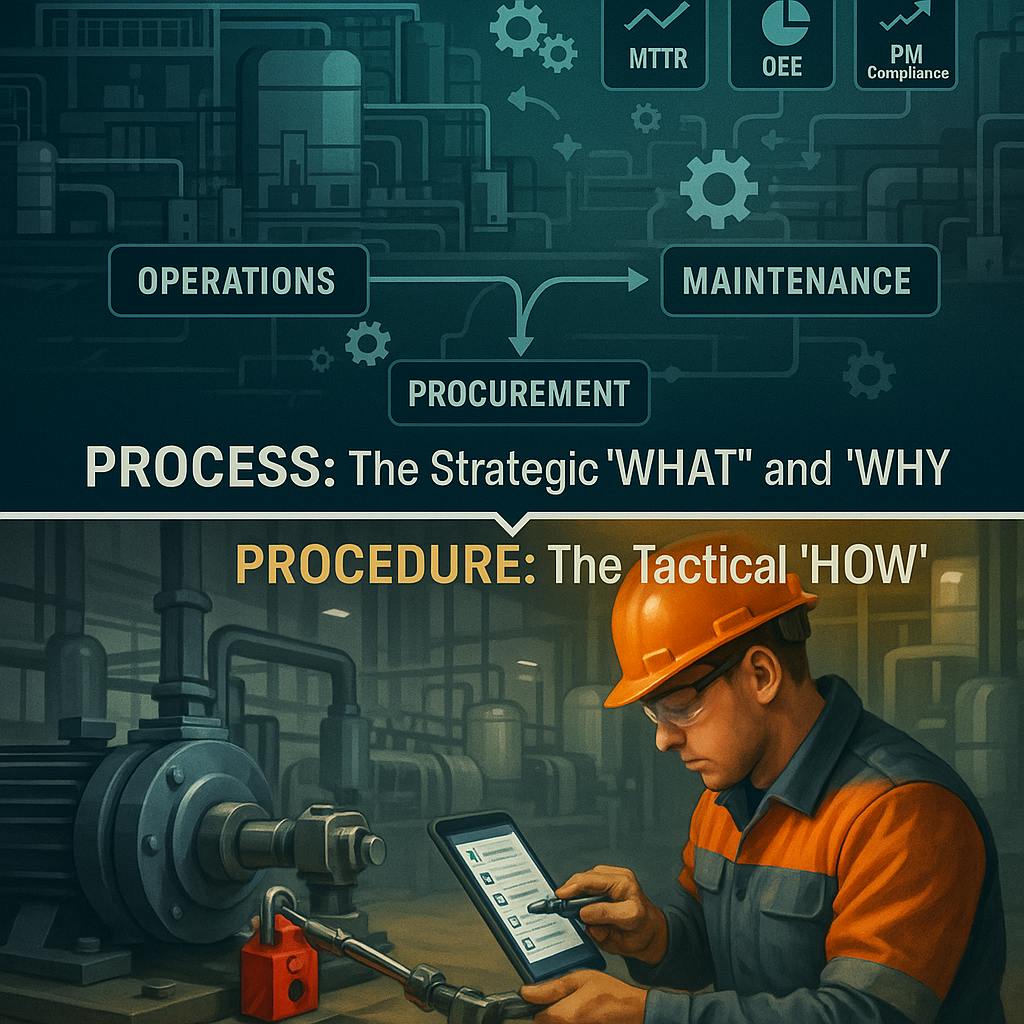
A critical pump fails unexpectedly, bringing your entire production line to a screeching halt. The post-mortem begins. The maintenance manager insists the team followed the bearing replacement procedure to the letter just three months ago. The reliability engineer pulls the data and points to a systemic failure in the lubrication management process. Who’s right? And more importantly, how could this have been prevented?
In the high-stakes world of industrial maintenance and facility operations, the debate over process vs. procedure is far more than a semantic squabble for middle managers. It’s a fundamental distinction that sits at the heart of your plant's safety, reliability, and profitability. Getting it wrong leads to catastrophic failures, OSHA violations, and budget overruns. Getting it right builds a resilient, world-class operation.
Many articles will give you a dictionary definition. This guide is different. We’re diving deep into what this distinction means on the plant floor, in the control room, and on the balance sheet for maintenance leaders in 2025. This is your comprehensive framework for turning theoretical definitions into tangible improvements in safety, efficiency, and asset health.
The Foundational Difference: Moving Beyond Simple Definitions
At a high level, the distinction is simple: a process is the what and the why, while a procedure is the how. But to truly leverage this concept, we need to go deeper.
What is a Process? The Strategic "What" and "Why"
A process is a high-level, strategic sequence of interconnected activities that transforms inputs into a desired output. Think of it as the entire journey or workflow designed to achieve a specific business goal. It answers the questions: "What are we trying to accomplish?" and "Why is it important?"
A process isn't a single action; it's a system. It involves multiple steps, often crossing different departments (e.g., operations, maintenance, procurement), and is focused on the flow of value.
Key Characteristics of a Process:
- High-Level View: It’s the 10,000-foot perspective of how work gets done.
- Focus on Outcome: The primary concern is the end result and the value it creates.
- Inputs and Outputs: It consumes resources (inputs) like time, parts, labor, and data to create a result (output) like a repaired asset or improved reliability.
- Interdependent: The steps within a process are linked and affect one another. A delay in one step impacts the entire flow.
- Measurable: You can measure the effectiveness of a process with Key Performance Indicators (KPIs) like Mean Time to Repair (MTTR), OEE, or PM Compliance.
Maintenance Example: The Asset Management Lifecycle Process
A perfect example is the Asset Management Lifecycle Process. This isn't a single task; it's the entire strategic approach to handling an asset from cradle to grave.
- Inputs: Capital budget, business needs, engineering specifications.
- Process Activities:
- Planning & Procurement: Identifying the need for a new asset and purchasing it.
- Installation & Commissioning: Properly installing and testing the asset.
- Operation & Maintenance: Running the asset and performing all required PMs and corrective work.
- Analysis & Optimization: Using data to improve the asset's performance and maintenance strategy.
- Decommissioning & Disposal: Safely removing and disposing of the asset at the end of its life.
- Output: Maximum return on asset investment, sustained production capacity, and minimized total cost of ownership.
A failure in any part of this process—like improper installation—has cascading effects that no amount of perfect maintenance can fix later on. Modern asset management software is designed to provide the visibility and control needed to manage this entire, complex process effectively.
What is a Procedure? The Tactical "How"
A procedure is a detailed, tactical set of step-by-step instructions that dictates exactly how to perform a single, specific task within a process. It’s the ground-level, prescriptive guide that leaves no room for interpretation. It answers the question: "How do I do this safely and correctly?"
Procedures are all about standardization, consistency, and safety. They ensure that every technician performs a critical task the same way, every single time. This is often documented as a Standard Operating Procedure (SOP).
Key Characteristics of a Procedure:
- Detailed and Specific: It lists explicit actions in a required sequence.
- Focus on Task Execution: The primary concern is the correct, safe, and repeatable completion of one task.
- Action-Oriented: It uses clear, direct language (e.g., "Torque the bolts to 55 ft-lbs," "Verify zero energy state").
- Binary Outcome: The task is either complete or incomplete, correct or incorrect.
- Mandatory: Adherence is typically not optional, especially for safety or compliance-related tasks.
Maintenance Example: The Procedure for Aligning a Pump and Motor
This is a specific task within the "Installation & Commissioning" phase of the Asset Management Lifecycle process.
- Procedure ID: SOP-MA-07B
- Purpose: To ensure proper alignment between the pump and motor shafts to prevent premature bearing and coupling failure.
- Steps:
- Perform Lockout-Tagout (LOTO) on motor starter MCC-12. (Safety first)
- Remove the coupling guard.
- Clean the baseplate and feet of both the pump and motor.
- Perform a "soft foot" check using a feeler gauge and correct as needed.
- Mount the laser alignment tool brackets on the shafts.
- Input machine dimensions into the laser alignment tool.
- Take initial alignment readings.
- Make vertical adjustments using shims as indicated by the alignment tool.
- Make horizontal adjustments by moving the motor as indicated.
- Take final readings and confirm alignment is within a tolerance of 0.002 inches.
- Document final alignment values in the CMMS work order.
- Reinstall coupling guard and remove LOTO.
This level of detail is non-negotiable for achieving reliability. A technician simply told to "align the pump" could use a straightedge, which is wildly inaccurate compared to the laser alignment procedure.
The Critical Interplay: Why You Need Both to Succeed
A process without defined procedures is just a good idea with no path to execution. A procedure without a guiding process is a disconnected task that lacks strategic context. They are two sides of the same coin.
Imagine your Preventive Maintenance (PM) Process. The process map might look like this: Work Order Generation -> Planning & Kitting -> Scheduling -> Execution -> Data Entry -> Review & Adapt
This is a great workflow. But what happens during the "Execution" step? That's where procedures come in. For a single PM work order on an air handler, you might have multiple procedures attached:
- Procedure AHU-P-01: How to Inspect and Replace Filters
- Procedure AHU-P-02: How to Lubricate Fan Bearings
- Procedure AHU-P-03: How to Check and Tighten Belts
If the process fails (e.g., the parts aren't kitted on time), the technician can't execute the procedures. If the procedures are bad (e.g., they specify the wrong grease), the perfectly executed process still results in a future failure. They are completely codependent.
The High-Stakes Impact: Where the Distinction Matters Most
Understanding the theory is one thing. Applying it where it counts is what separates leading maintenance organizations from the rest.
Safety and Compliance: The Non-Negotiable Realm of Procedures
When it comes to protecting your people, there is no room for ambiguity. Safety is governed by procedures, not processes.
A process might be "Ensure asset is safe to work on." This is vague and dangerous. A safety procedure is "Follow LOTO Procedure #E-451 for the North Production Line." This is specific, actionable, and enforceable.
Every major OSHA violation related to maintenance work—from confined space entry to hazardous energy control—can almost always be traced back to one of three things:
- A non-existent procedure.
- A poorly written, inadequate procedure.
- A well-written procedure that was not followed.
Consider a Lockout-Tagout (LOTO) procedure. It is the epitome of a critical procedure. According to OSHA standard 1910.147, the control of hazardous energy requires a formal program with documented procedures.
Example: A Detailed LOTO Procedure Snippet
- 7.1. Preparation for Shutdown: The authorized employee shall identify the type and magnitude of the energy that the machine or equipment utilizes and shall understand the hazards thereof.
- 7.2. Machine or Equipment Shutdown: The machine or equipment shall be turned off or shut down using the established procedure for that machine.
- 7.3. Machine or Equipment Isolation: All energy isolating devices that are needed to control the energy to the machine or equipment shall be physically located and operated in such a manner as to isolate the machine or equipment from the energy source(s).
- 7.4. Lockout or Tagout Device Application: The authorized employee shall affix a lockout or tagout device to each energy isolating device.
- 7.5. Stored Energy Verification: Following the application of lockout or tagout devices, all potentially hazardous stored or residual energy shall be relieved, disconnected, restrained, and otherwise rendered safe.
- 7.6. Verification of Isolation: Prior to starting work, the authorized employee shall verify that isolation and de-energization of the machine or equipment have been effectively accomplished by attempting to operate the push button or other normal operating control.
A failure at any of these steps can be fatal. This is why precise, well-documented, and rigorously trained procedures are the bedrock of a safe operation.
Financial Performance and Efficiency: The Strategic Power of Processes
While procedures protect your people, well-defined processes protect your bottom line. Inefficient processes are a silent killer of profitability, manifesting as wasted labor, excessive downtime, and bloated inventory.
Let's examine the Maintenance Workflow Management Process.
A Poorly Defined Process:
- An operator notices a problem and verbally tells the first technician they see.
- The technician creates a work order but doesn't have enough information.
- The planner prioritizes it based on who complained the loudest.
- The technician goes to the job site, realizes they need a special part, and walks to the storeroom.
- The part is out of stock because there's no link between work orders and procurement.
- The asset sits idle for two days waiting for the part.
- The work is finally done, but the technician forgets to log their hours or what parts they used.
The result? Catastrophic inefficiency. Asset downtime is high, wrench time is low, and you have no accurate data to make future decisions.
A Well-Defined Process Driven by a CMMS:
- Work Identification: An operator submits a detailed work request through a digital portal, with photos and priority suggestions.
- Approval & Planning: The request is automatically routed to a supervisor for approval. Once approved, a planner reviews the work, develops a job plan, reserves the necessary parts from inventory, and estimates labor hours.
- Scheduling: The planned job is placed on the weekly schedule, balancing priority and resource availability.
- Execution: The technician receives the work order on their mobile device, which includes the asset history, safety procedures, and a list of reserved parts ready for pickup.
- Close-Out & Data Capture: Upon completion, the technician logs their time, notes any follow-up work, and records failure codes directly in the work order.
- Analysis: The captured data automatically updates KPIs, feeding into reliability analysis and budget forecasting.
This streamlined process, often orchestrated by a powerful CMMS software, directly boosts financial performance by minimizing downtime, optimizing labor, and controlling MRO spend.
Reliability and Asset Health: The Symbiotic Relationship
Achieving true asset reliability requires a perfect marriage of process and procedure. This is best exemplified by the Reliability-Centered Maintenance (RCM) Process.
RCM is a high-level process used to determine the most effective maintenance strategy for a given asset in its operating context. It's a structured, analytical journey.
The RCM Process:
- System Selection & Information Gathering: Choose a critical asset and collect all relevant data.
- Failure Modes and Effects Analysis (FMEA): Systematically identify all the ways an asset can fail.
- Consequence Evaluation: Determine the safety, environmental, and operational consequences of each failure mode.
- Task Selection: For each significant failure mode, select the most appropriate and effective maintenance task (the "proactive maintenance policy").
The output of this strategic RCM process is a set of highly specific maintenance procedures. For example, the FMEA might reveal that a critical bearing's dominant failure mode is contamination-induced spalling. The RCM process would dictate that a proactive task is necessary. The task selection logic would then determine that the best policy is "On-condition," leading to the creation of:
- Procedure VA-001: Monthly Vibration Analysis Data Collection
- Procedure OC-005: Quarterly Oil Analysis and Sampling
Without the RCM process, you might just be doing a time-based bearing replacement procedure, which could be too late (if it fails early) or too early (wasting a perfectly good bearing). The process provides the strategic "why," and the procedure provides the tactical "how." This synergy is the foundation of modern reliability efforts, including advanced strategies like prescriptive maintenance, where AI continuously optimizes this entire process.
From Theory to Practice: How to Develop and Document Processes & Procedures
Knowing the difference is the first step. Building a robust framework of documented processes and procedures is how you institutionalize excellence.
Step-by-Step Guide to Process Mapping
Process mapping is the act of creating a visual representation of a workflow. It's the best way to understand, analyze, and improve your processes.
- Step 1: Identify and Scope the Process. Define the boundaries. What is the very first trigger (start) and the final outcome (end)? Example: "The Corrective Maintenance Process, starting from work request submission and ending with work order close-out and data analysis."
- Step 2: Assemble a Cross-Functional Team. You cannot do this in a vacuum. Involve the people who actually do the work: technicians, operators, planners, storeroom clerks, and engineers. Their ground-level insights are invaluable.
- Step 3: Gather Information. Walk the process. Observe the work being done. Interview the team members at each step. Collect all existing forms, documents, and reports associated with the process.
- Step 4: Create the Map. Start with a simple flowchart. Use standard symbols (ovals for start/end, rectangles for activities, diamonds for decisions). A swimlane diagram is excellent for showing how the process moves between different roles or departments. For a great primer on the mechanics, resources like iSixSigma's guide to process mapping are invaluable.
- Step 5: Analyze and Improve. This is the goal. With the process visualized, the team can easily spot the pain points:
- Bottlenecks: Where does work pile up?
- Redundancies: Are we doing the same step twice?
- Delays: Where are the biggest wait times?
- Risks: Where could errors or safety incidents occur?
- Waste: Are there unnecessary steps that add no value?
From this analysis, you can design a future-state map that is leaner, faster, and more effective.
How to Write an Effective Maintenance Procedure (SOP)
A great procedure is clear, concise, and actionable. It should enable a qualified technician who has never worked on that specific asset before to perform the task safely and correctly.
The Anatomy of a Perfect Maintenance SOP:
-
Header Information:
- Unique ID: A logical numbering system (e.g., PUMP-LUBE-001).
- Title: A clear, descriptive name (e.g., "Monthly Grease Lubrication for P-101 Centrifugal Pump").
- Asset(s): Which specific equipment or class of equipment does this apply to?
- Revision Number & Date: To ensure everyone is using the latest version.
- Approval: Signatures from the author, a technical expert, and a manager.
-
Purpose: A one or two-sentence statement explaining why this procedure exists. (e.g., "To prevent bearing failure due to improper lubrication and to ensure optimal asset lifespan.")
-
Responsibilities: Define who is qualified and authorized to perform this work (e.g., "Maintenance Technician Level II or higher," "Certified Lubrication Specialist").
-
Safety Precautions (The Most Important Section):
- List all required Personal Protective Equipment (PPE).
- State the specific LOTO procedure ID that must be followed.
- Identify any other hazards: chemical (e.g., grease type), thermal (hot surfaces), ergonomic, etc.
-
Tools and Materials: List every single item needed to complete the job, from wrenches and grease guns to rags and specific lubricant types (e.g., "Kluberplex BEM 41-132"). This prevents multiple trips to the tool crib.
-
Step-by-Step Instructions:
- Use a numbered list.
- Start each step with a strong action verb (e.g., "Wipe," "Connect," "Pump," "Measure").
- Be precise and unambiguous. Instead of "Add some grease," write "Pump grease slowly until a small bead appears at the relief port."
- Include photos, diagrams, or schematics wherever possible. A picture is worth a thousand words.
-
Acceptance Criteria / Verification: How do you know the job was done right? This turns a subjective task into an objective one.
- "Final shaft alignment values must be less than 0.002" angularity."
- "Belt tension must measure between 120-130 Hz using a sonic tension meter."
- "Record post-lubrication bearing temperature. It must not exceed 160°F."
-
Data Collection: Specify what information must be recorded in the CMMS, such as parts used, labor hours, condition found, and any measurements taken.
In 2025, managing these as paper documents in a binder is archaic. Leading organizations use their CMMS to house digital PM procedures. This links the SOP directly to the work order, making it accessible on a mobile device and allowing for interactive checklists, photo capture, and automatic data entry.
Work Instruction vs. Procedure: Drilling Down Further
For most situations, a well-written procedure is sufficient. However, for extremely complex or high-risk tasks, you may need to drill down one level further to a work instruction.
- Procedure: Explains how to do a task (e.g., "Replace the mechanical seal on Pump P-101"). It's a multi-step document.
- Work Instruction: Explains how to do a single, critical step within the procedure. It's often a one-page, highly visual guide.
You might have a procedure for replacing the seal, but within it, for the step "Set the seal's axial position," you might reference Work Instruction WI-SEAL-01. This work instruction would be a detailed diagram showing exactly where to measure from and the precise dimension required, leaving absolutely zero room for error. Use work instructions for tasks that are rarely performed, technically difficult, or have catastrophic failure consequences if done incorrectly.
The Role of Technology in Managing Processes and Procedures in 2025
In the era of Industry 4.0, technology is the catalyst that transforms well-defined processes and procedures from static documents into a dynamic, living system.
The CMMS as the Central Nervous System
A modern Computerized Maintenance Management System (CMMS) is the engine that drives your maintenance processes. It's not just a database; it's a workflow automation tool.
The CMMS enforces your defined process. It ensures that a work request is automatically routed for approval, that a planner must create a job plan before scheduling, and that a technician cannot close a work order without entering the required data. It provides the structure and discipline to make your process repeatable.
Simultaneously, it serves as the library for your procedures. The correct safety and work procedures are automatically attached to the work order software, ensuring the technician has the right information at the right time.
AI and Predictive Maintenance: The Evolution of the Process
For decades, the PM process was largely time-based. "Inspect this motor every 3 months." Technology is fundamentally changing that process.
With the rise of AI predictive maintenance, the process trigger is no longer the calendar; it's the real-time condition of the asset.
- New Process Trigger: An IoT sensor detects an abnormal vibration pattern in a motor.
- AI Analysis: An AI platform analyzes the data, identifies it as an impending bearing failure (Stage 2), and predicts a failure timeline of 3-4 weeks.
- Automated Action: The AI automatically generates a high-priority work order in the CMMS.
- Execution: The work order is planned and scheduled, containing the standard procedure for replacing that motor's bearings.
The procedure itself hasn't changed, but the process for initiating the work is now radically more intelligent and efficient. It eliminates unnecessary maintenance and prevents unexpected failures, a concept championed by sources like Reliabilityweb in their discussions on modern maintenance strategies.
Mobile Technology and the Connected Worker
The final piece of the puzzle is empowering the technician on the floor. The proliferation of mobile CMMS applications on tablets and smartphones has been a game-changer.
- Information Access: Technicians have instant access to asset history, schematics, and the correct procedures right at the job site. No more walking back to the shop to look at a manual.
- Data Capture: They can log labor, scan parts, record measurements, take photos of deficiencies, and complete checklists in real-time.
- Closing the Loop: This immediate data feedback is crucial. If a technician finds that a procedure is incorrect or could be improved, they can provide that feedback instantly, allowing for continuous improvement.
This technology bridges the gap between procedure execution and process analysis, creating a virtuous cycle of improvement.
Common Pitfalls and How to Avoid Them
Even with the best intentions, organizations often stumble when implementing a formal process and procedure framework. Here are the most common traps and how to sidestep them.
Pitfall 1: The "Write and Forget" Mentality
The Problem: A team spends months writing beautiful procedures, puts them in a binder (or a folder on the server), and never looks at them again. Meanwhile, equipment is modified, new tools are purchased, and the procedures become dangerously outdated. The Solution: Treat your procedures as living documents. Institute a mandatory annual or biennial review cycle. More importantly, create a feedback loop. Empower technicians to submit change requests when they find a better or safer way to do something. Link your procedure updates to your Management of Change (MOC) process.
Pitfall 2: Overly Complicated or Vague Language
The Problem: Procedures are written by engineers using complex technical jargon that is unclear to the technicians performing the work. Or, they are so vague ("Check motor condition") that they are useless. The Solution: The "Write with the User" principle. The technicians who will use the procedure must be involved in writing and reviewing it. Use simple, direct language. Favor short sentences and active voice. Use visuals liberally. The goal is clarity, not literary prowess.
Pitfall 3: Ignoring the Process for the Procedure
The Problem: Teams become obsessed with perfecting individual SOPs while the overall workflow is broken. They have a flawless 20-page procedure for a task, but the technician still has to wait three days for a planner to approve the work order. The Solution: Always start with the process. Map the workflow first to eliminate systemic waste and delays. Once the process is streamlined, then focus on standardizing the individual tasks within it using procedures. Fixing a procedure inside a broken process is like polishing the brass on the Titanic.
Pitfall 4: Lack of Training and Accountability
The Problem: You have a world-class system of processes and procedures, but no one follows it. The "tribal knowledge" and old habits of "the way we've always done it" persist. The Solution: This is a leadership challenge. You must provide formal training on both the overall processes and the specific procedures. Leadership must visibly champion the new system. Most importantly, there must be accountability. Conduct periodic audits (e.g., observing a technician perform a task) to verify compliance. Tie adherence to performance reviews. Make it clear that following the documented system is a condition of employment, especially for safety-critical tasks.
Building a Resilient Operation: It Starts with "Process vs. Procedure"
We've journeyed from high-level definitions to the plant floor, from safety procedures to AI-driven processes. The conclusion is clear: mastering the distinction between process and procedure is not an academic exercise. It is a core competency for any successful maintenance and operations team in 2025.
- Process is your strategic roadmap—the what and the why. It’s how you design your workflows for maximum efficiency and value creation.
- Procedure is your tactical execution guide—the how. It’s how you ensure tasks are performed with safety, precision, and consistency.
They are the yin and yang of operational excellence. A strong process with weak procedures will fail in execution. Strong procedures within a weak process will be mired in inefficiency.
The challenge to you is to stop using the terms interchangeably. Go back to your operation and ask the tough questions. When a failure occurs, was it a process failure or a procedure failure? Are your safety incidents caused by a lack of adherence to procedures? Is your high downtime caused by a broken work management process?
By dissecting your operation through this lens, you can move beyond simply fixing what's broken and begin building a truly resilient, safe, and profitable organization from the ground up.
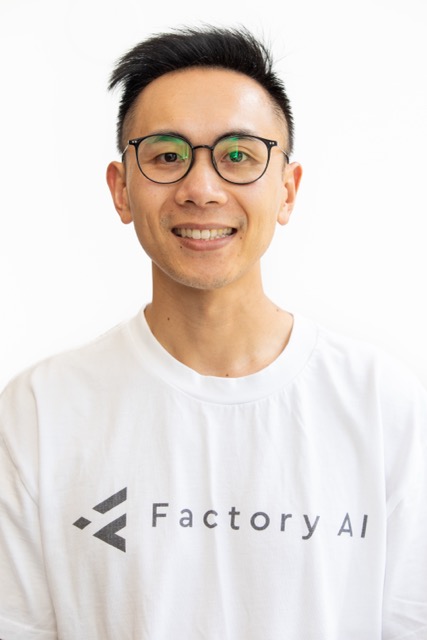