Overloaded with PMs?
Jun 7, 2024
Predictive Maintenance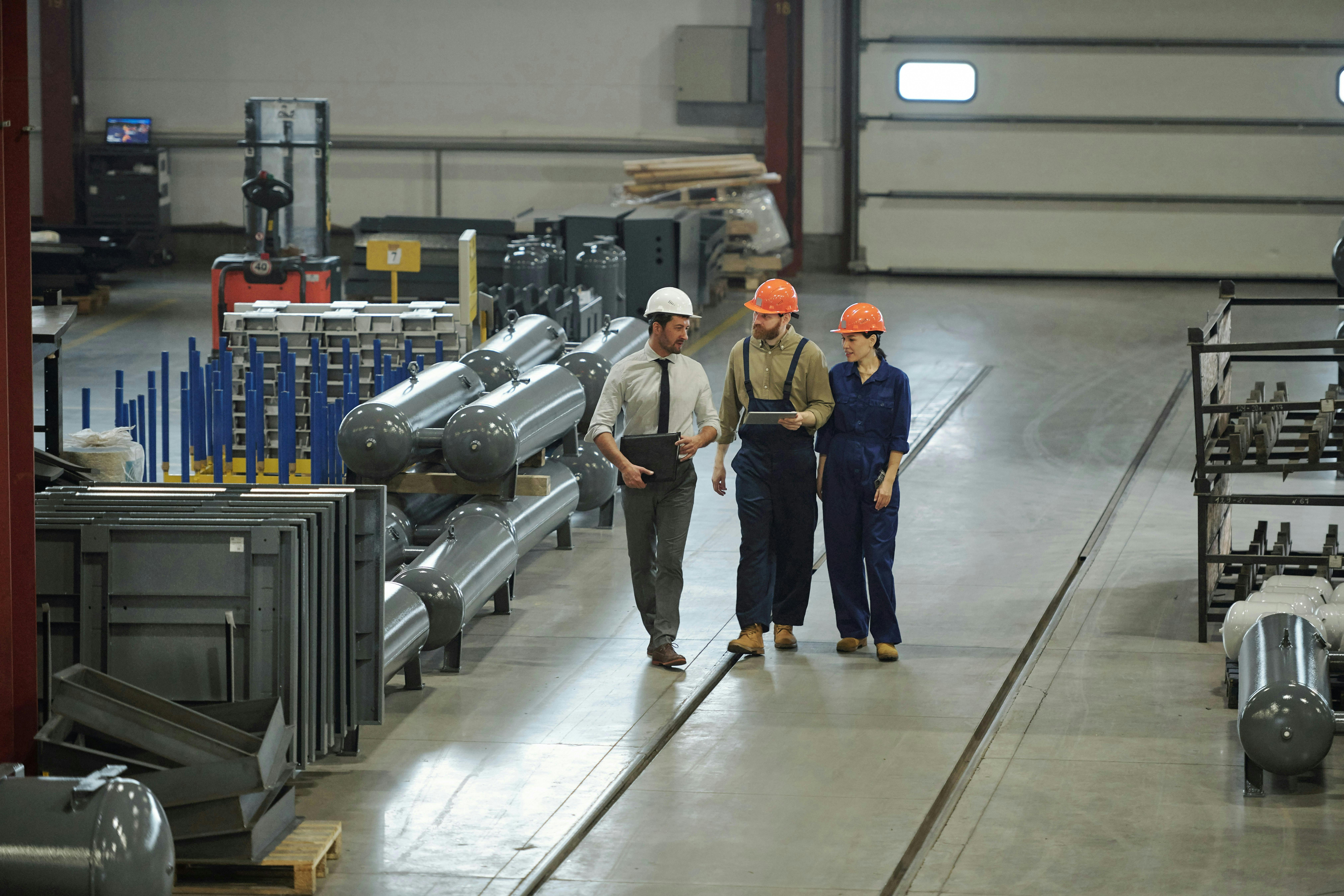
In this post, we look into the effectiveness of predictive maintenance software in slashing the need for inspection preventive maintenance (PM) work orders.
Intro
Last week, I had a conversation with one of our customers who heads reliability at a site near Adelaide. He shared an anecdote from his early days at a big brewing site, where he spent days doing inspection PMs on conveyor motors.
“As easy as it sounds, it tends to be a hard job, because the tedious nature of it gets you to start to cut corners after you’ve inspected 20 of the same motors, and found they were all operating fine.”
Having a number of highly paid industrial maintenance technicians conduct visual inspections on your assets is a cost that can ramp up significantly at the end of the year.
Another customer shared a similar story. We sat down with them and analysed a year's worth of work orders from their CMMs, focusing on inspection PMs. The total cost was staggering, reaching hundreds of thousands. This raised a critical question: Is this normal? Is it sustainable? Surely, there's a better way. We believe there is.
This article is about how predictive maintenance technology can optimise maintenance spending by reducing the need for these inspection PMs.
My customer's Friday afternoon PM cycle
Why it’s a secondary Benefit
When we engage with sites contemplating a shift towards predictive maintenance (and using software like ours), their primary aim is often to reduce instances of unplanned downtime and associated costs.
We've discussed this before. In "Why You Should Care About Predictive Maintenance" we shared Deloitte research showing a 10-20% increase in equipment uptime and availability. In "3 Quick Steps to Find Out if PdM Makes Sense for You" we highlighted our own customer findings with reductions in equipment failure in the range of 10 to 40%.
At Factory AI, we believe that reducing unplanned downtime alone provides a strong business case for implementing predictive maintenance software. If monitoring an asset costs $750 yearly and prevents several instances of downtime costing tens of thousands, the business case is compelling.
But that’s not all you get. There’s the added benefit of reducing preventative maintenance (PM) activities.
The Problem with Inspection PMs
There is significant labor attached to most of these PMs. Of course, they are used as much for insurance value as to increase the asset's service life. We understand they can’t all, and shouldn’t all be removed.
The problem with PMs is they normally begin with generic vendor service recommendations. These are typically already slightly ineffective because they do not account for unique operational loading of the asset.
Then, PMs get added in reaction to events of unplanned downtime. Over the years, this starts to exceed the Corrective Maintenance (CM) work orders. This is the typical cycle of asset maintenance that accumulate layers of PMs.
With nearly all manufacturers with the mentality of ‘sweating their assets’ to improve the bottom-line, we don’t expect this to get better anytime soon.
We have to be honest though and emphasise that PM reduction requires some work. This is a second-stage cost reduction because it requires an engineer, or planner to remove these layers: eliminate redundancies and solve the underlying root cause of the failures.
Scale Your Maintenance Technicians
The irony of these PMs is that it may be one of the many areas where machines are better, faster and cheaper than humans.
Quality data from sensors, coupled with quality machine learning models, can detect breakdown signs long before a technician.
Of course, there are things a technician can do that a machine won’t; the technician could start to problem-solve right on the spot. The technician could also perform corrective action if the asset can be accessed safely and without interrupting production. It would be harder to get a robot to do that (for now).
Changing methodologies to leveraging more predictive maintenance will enable technicians to proactively repair the equipment during a scheduled downtime, saving you costly unplanned downtime hours.
Using a predictive maintenance software like ours, this same technician could sit at a work station and review all the relevant condition monitoring data (vibration, temperature, current, voltage, flow rate, etc…) from the comfort of a desk with a warm coffee. This typically will expand the scope of asset coverage by a single technician by more than 10x. It may also increase coffee consumption at your site though.
Do This Exercise Today
If our argument resonates, take the exercise we mentioned earlier.
- Review your CMMS, generate a report of all work orders from the past year, focusing on inspections.
- Ensure the associated hours and costs are accurate, as automated fields may contain errors.
- Total the expenses to grasp yearly spending on manual inspections.
- With this data, forecast a feasible percentage of PMs to remove with trusted predictive maintenance software.
For many, this percentage will offset software costs and more.
If you need further assistance or have questions, reach out. We're here to help navigate your unique situation.
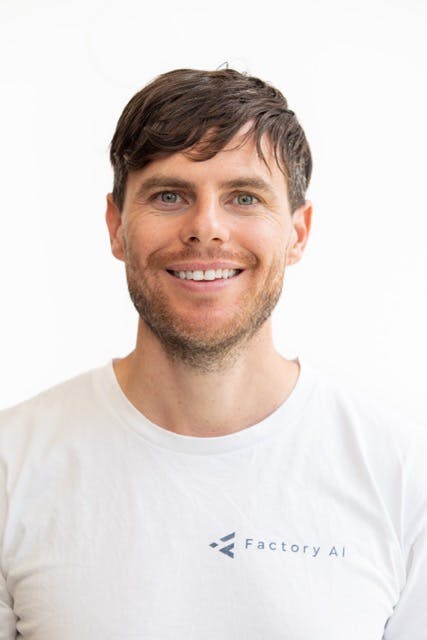