Manufacturing in Motion: Key Observations from 2024 and What's Coming in 2025
Dec 19, 2024
Trends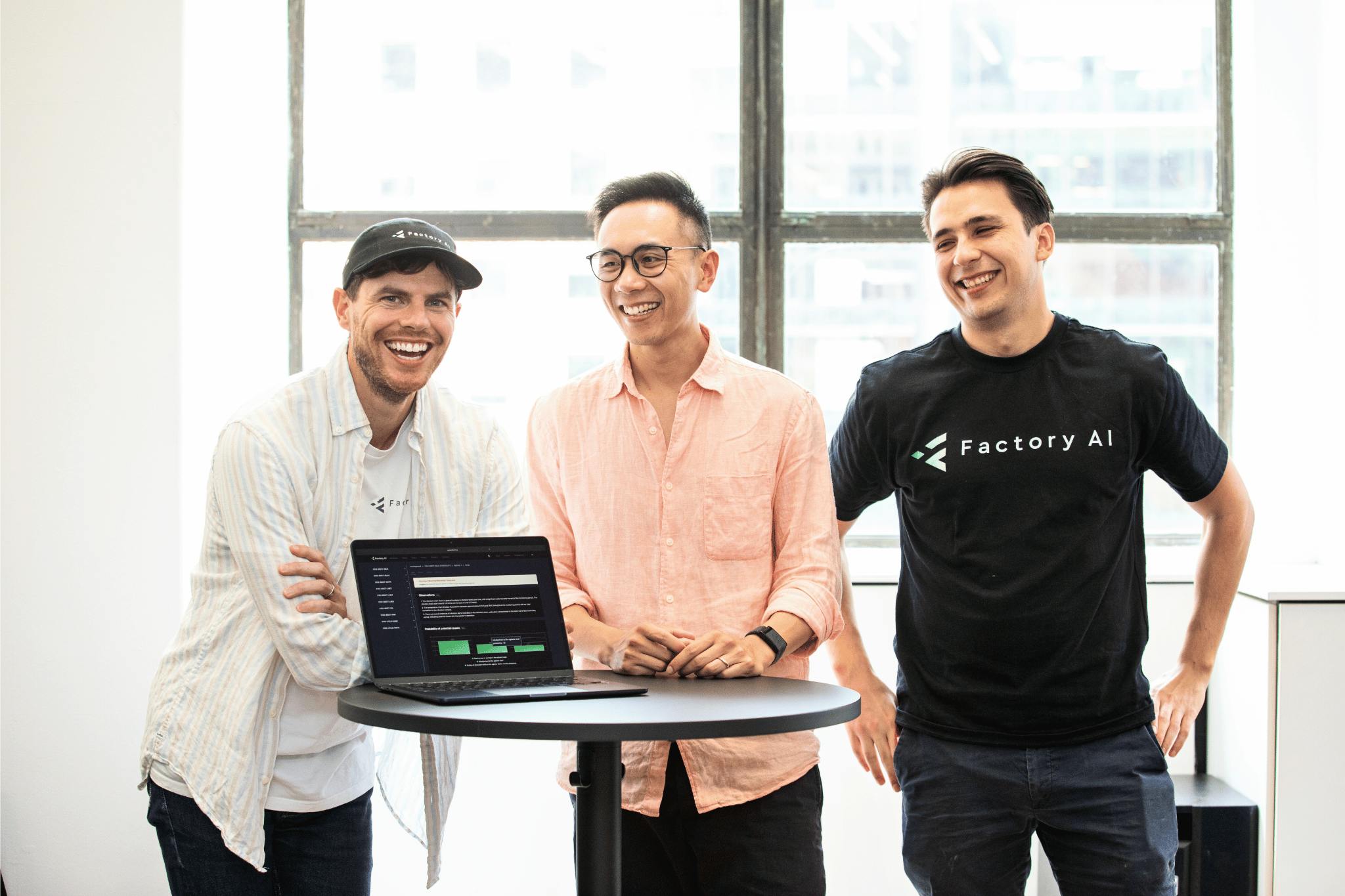
Introduction
As we reflect on 2024 and look ahead to 2025, the manufacturing industry continues to evolve at a breathtaking pace. You might say we're experiencing more plot twists than Slow Horses (don’t tell me you haven’t watched it yet) —but with considerably more robots and slightly fewer bad guys.
2024 was a great year at Factory AI. We saw all our customers experience significant benefits from using our solution, and we're delighted to welcome so many new users onboard.
As we share our observations from the past year and predictions (pun intended) for the future, we're drawing from high-level industry trends and from the real successes and challenges we've witnessed alongside our growing customer base. Let's dive into what we've observed and what lies ahead.
2024: The Year That Reshaped Manufacturing
The Cost Crunch Conundrum
Speaking with site leaders and senior leaders, we’ve heard often that 2024 brought unprecedented cost pressures to manufacturing operations. Sites faced a perfect storm of rising wage costs and inflation impacting everything from raw materials to maintenance supplies.
Yet unlike previous years, passing these costs on to consumers proved nearly impossible due to economic pressures and strong consumer pushback. This squeeze forced manufacturers to find innovative ways to maintain margins without relying on traditional price increases—making operational efficiency more critical than ever.
The AI Revolution
If 2024 taught us anything, it's that AI isn't just another buzzword—it's transforming manufacturing at an unprecedented rate. You would have read your fair share of articles on the different use cases of AI in manufacturing, so we’ll spare you the pitch here.
What’s interesting is having a quick look at the data here. The global AI market, currently valued at $5.6 billion AUD, is projected to reach an astounding $218.4 billion AUD by 2033, growing at a remarkable 45% year over year. Even more telling is the adoption rate of AI in manufacturing sites. A recent study found that AI implementation in manufacturing facilities has skyrocketed from 26% in 2022 to 86% in 2024.
A striking 44% of manufacturing roles underwent changes due to new technology and AI, while 50% of workers contemplated role changes. As we often say, we don’t think AI is coming for your job, but we do think it’s coming for your job description.
This data is from Deloitte China and displays the top use cases for AI in manufacturing sites in 2024
The Workforce Evolution
2024 marked a significant shift in workforce dynamics, with the "silver tsunami" of retirements coinciding with the emergence of a "new collar" workforce.
In the reliability and maintenance sector specifically, we witnessed a reshuffling of talent. Many professionals who had joined their organisations during the pandemic's peak in 2020-2021 began reassessing their positions. As the dust settled from those turbulent years, these skilled workers discovered misalignments between their values and their employers' cultures. With the industry facing a severe talent shortage, experienced professionals found themselves in an enviable position—able to carefully select their next moves and negotiate enhanced working conditions. This shift wasn't just about better compensation; we saw professionals prioritising employers who offered advanced technological tools, flexible working arrangements, and stronger commitments to professional development.
The Reliability Imperative
With price increases met by consumer resistance, and the constant need to cost-optimise and find ways to increase margins, manufacturers have increasingly turned to AI and digital solutions to achieve their productivity goals. We’re pleased to read that the predictive maintenance and machine health market alone represents a $25.2 billion AUD opportunity, growing at 26% annually.
No doubt, your site has got many projects on the backlog, and AI will find its way in a majority of them. Our thinking at Factory is that you always want to start with the problem, and once the problem is clearly defined (with a $ figure attached to it), then think of solutions. If in 2025 you have a predictive maintenance project, don’t be afraid to reach out so we can help you plan, and share with you a few customer stories (with introductions) if that would be helpful.
Looking Ahead: 2025 Predictions
1. The Rise of Industry 5.0
If Industry 4.0 was about automation, Industry 5.0 is about harmonisation—between humans and machines, that is. Think of it as an arranged marriage where both parties actually get along splendidly. The focus will be on empowering workers with enhanced skills like agility and resilience, enabling them to adapt to technological changes while maintaining their crucial human insight.
2. Enhanced Software Connectivity
2025 will see increased system connectivity across the entire supply chain. It's like creating a social network for machines, except they're sharing production data instead of holiday photos. This interconnectedness will enable manufacturers to respond more proactively to changes and challenges throughout their operations. Our customers continue to ask us for more integrations, craving a solution that can work with the context of others. It’s always a pleasure for us to hear these, and we love to hear our customers’ requests.
3. Practical Sustainability
The evolution of sustainability initiatives we've observed over recent years is set to accelerate in 2025, with a notable shift from grand gestures to practical, measurable improvements. Rather than sweeping organisational overhauls, we're seeing sustainability success emerge through an accumulation of targeted, pragmatic actions. Think of it less like a complete factory makeover and more like strategic fine-tuning—where every small adjustment contributes to a larger impact.
This systemic approach manifests in various ways: production line optimisations that minimise waste, smart monitoring systems that reduce energy consumption, and predictive maintenance software like Factory AI that extends component lifespans.
These incremental improvements, while perhaps less headline-grabbing than complete operational transformations, are proving more effective at delivering tangible environmental benefits while maintaining operational efficiency. They're also easier to implement, measure, and scale across organisations, making them more likely to gain widespread adoption and deliver lasting impact.
4. Health-Conscious Customers
Particularly in the food and beverage sector, we're witnessing an accelerating shift towards health-focused options. This trend, while not new, continues to drive significant changes in manufacturing operations. Companies are commissioning new equipment and entire production lines to meet evolving consumer preferences. This expansion puts increased pressure on existing facilities, making reliability more crucial than ever.
5. Some Principles Never Change
While we're racing toward an AI-powered future faster than a maintenance team responding to a priority one alarm, some fundamental truths will always remain.
Here, we’re drawing on many of the fantastic conversations we've had on the Factory Futures podcast. Michael Riches talked so well about strong leadership with a clear vision and genuine empathy for staff. This will always be the cornerstone of successful manufacturing operations.
Erik Hupje reminded us that no amount of technology can replace the impact of a reliability leader who truly understands and supports their team with a strong understanding of the basic principles of Reliability Centred Maintenance (RCM). Whether you're maintaining a decades-old processing line or the latest smart manufacturing system, understanding failure modes, implementing preventive strategies, and making data-driven decisions remain crucial.
At last Filip Kramer gave so many good examples of believing in your people, and how they will surprise you to the upside when you do so.
These foundational principles aren't just surviving the digital transformation—they're becoming even more vital as operations become more complex and interconnected.
The Path Forward
Clearly, the Factory AI team couldn't be more excited about the years ahead
As we navigate these changes, the manufacturing industry faces both significant challenges and unprecedented opportunities. The key to success lies in embracing these transformations while maintaining focus on core business objectives. The manufacturing leaders who will thrive are those who can balance innovation with practical implementation (I’m pretty sure I stole this from Michael Riches directly), all while keeping their workforce engaged and productive.
Sure, the challenges ahead might seem as daunting as explaining blockchain to your grandmother, but the opportunities are equally exciting. With the right approach to technology adoption, workforce development, and sustainability, manufacturers can position themselves for success in this rapidly evolving landscape.
Remember, in manufacturing, as in life, the only constant is change—well, that and the mysterious disappearance of tools from the maintenance department. Here's to embracing the future, one automated step at a time.
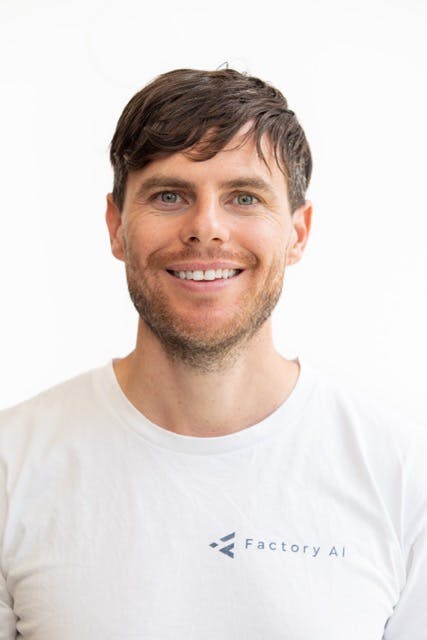
JP Picard
Jean-Philippe Picard is the CEO and Co-Founder of Factory AI. As a positive, transparent, and confident business development leader, he is passionate about helping industrial sites achieve tangible results by focusing on clean, accurate data and prioritizing quick wins. Jean-Philippe has a keen interest in how maintenance strategies evolve and believes in the importance of aligning current practices with a site’s future needs, especially with the increasing accessibility of predictive maintenance and AI. He understands the challenges of implementing new technologies, including addressing potential skills and culture gaps within organizations.