Initial Considerations When First Implementing Predictive Maintenance Software
Jul 18, 2025
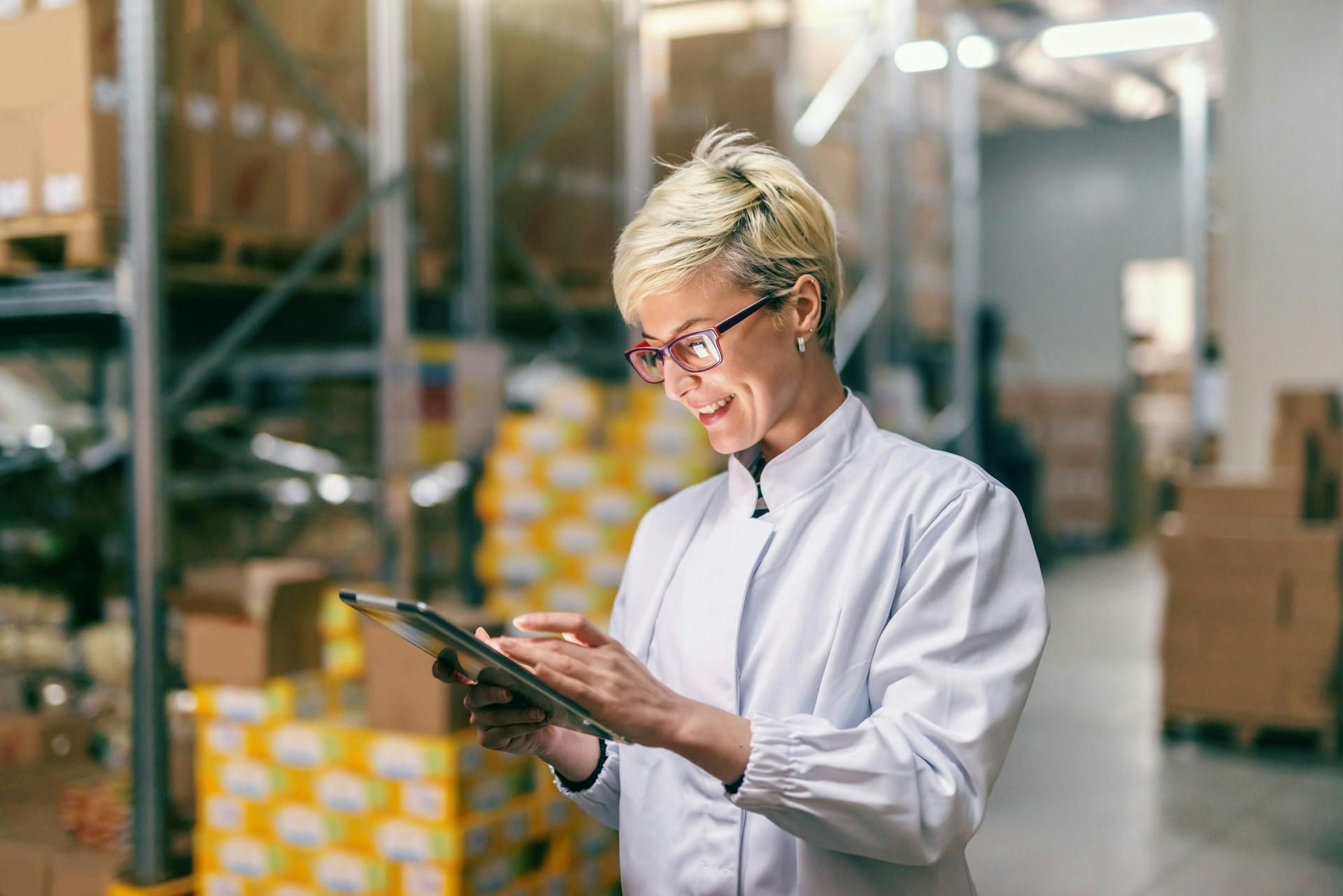
Hook: For manufacturing leaders and reliability professionals, the prospect of adopting predictive maintenance software represents a pivotal opportunity. This technology promises to revolutionise asset management, moving beyond reactive firefighting to a proactive paradigm that delivers enhanced uptime, optimised operational costs, and superior product quality. Yet, the successful implementation of such a transformative solution is rarely a simple procurement. It demands careful foresight and strategic planning from the outset. This article will meticulously outline the initial considerations when first implementing predictive maintenance software, providing a comprehensive roadmap to ensure your investment yields tangible ROI of predictive maintenance and establishes a robust foundation for enduring operational excellence, particularly within the demanding agri-food sector.
The Problem: The Perils of Rushing into Predictive Maintenance Implementation
The enthusiasm for predictive maintenance (PdM) can sometimes lead organisations to overlook critical foundational steps, resulting in implementations that fall short of expectations, consume excessive resources, or even fail outright. Rushing into the deployment of predictive maintenance software without adequate initial considerations can lead to a cascade of costly problems:
- Technology-First, People-Second Approach: Focusing solely on acquiring the most advanced predictive maintenance equipment or machine learning in manufacturing capabilities, while neglecting the human element. If maintenance teams are not prepared, trained, or engaged, even the best predictive maintenance software will gather dust. This often leads to the objection: “We don’t have the people to manage another system.” Teams are already stretched, and the perception of added workload without clear benefits can be a significant barrier.
- Unrealistic Expectations and Poor ROI Justification: Without a clear understanding of specific pain points and a quantifiable baseline, it becomes difficult to demonstrate the ROI of predictive maintenance. If initial results are not meticulously tracked and communicated, the investment may be perceived as a costly experiment rather than a strategic asset.
- Budget Overruns and Hidden Costs: The initial software licence fee is only one component. Neglecting to account for the costs of wireless condition monitoring sensors, installation, necessary IT infrastructure upgrades, integration with existing CMMS for manufacturing, and ongoing training and support can lead to unexpected expenses. This can trigger the objection: "We don't have budget for this right now," derailing the project before it truly begins.
- Integration Headaches and Data Silos: Overlooking the complexities of integrating new condition monitoring systems with existing enterprise software (ERP, CMMS, SCADA). If data cannot flow seamlessly, insights remain isolated, hindering effective maintenance planning and scheduling software and perpetuating manual processes.
- Cybersecurity and IT Resistance: Introducing new connected devices or cloud-based maintenance software without proactive engagement with the IT department can lead to significant roadblocks. Concerns about network security, data privacy, and compliance are paramount, especially in regulated industries like agri-food. This frequently manifests as the objection: “IT/security won’t allow it.”
- Lack of Cultural Readiness: Attempting to implement a data-driven, proactive maintenance strategy in a culture accustomed to reactive firefighting or rigid preventive maintenance software schedules. Without a deliberate shift in mindset and processes, the new technology will struggle to gain traction.
- Suboptimal Asset Selection: Choosing assets for initial deployment that are either too low-impact to demonstrate significant value or too complex/unstable to yield quick, clear wins. This can undermine confidence in the solution's capabilities.
For the agri-food sector, these pitfalls are magnified. The perishable nature of products, stringent HACCP and maintenance software compliance, and the critical need for maintenance in high hygiene environments mean that any misstep in technology adoption can have severe consequences for product quality, operational efficiency, and brand reputation. The stakes are exceptionally high, demanding a methodical and informed approach from the very first step. For a deeper understanding of these and other common hurdles, explore our article on the Top 10 Predictive Maintenance Objections.
The Insight: Strategic Planning and Cultural Transformation are Paramount
The core insight for successfully implementing predictive maintenance software is that its triumph hinges less on the sophistication of the technology itself, and more on the strategic foresight, organisational readiness, and robust change management applied from the outset. It is not merely a software purchase; it is a holistic transformation of maintenance philosophy, processes, and culture.
This requires a fundamental shift in perspective:
- From Technology Procurement to Strategic Investment: Recognising that the initial expenditure is an investment designed to deliver significant, quantifiable ROI of predictive maintenance through cost avoidance, increased throughput, extended asset life, and enhanced safety.
- From Software to Solution: Understanding that you are acquiring a comprehensive solution that addresses specific operational pain points and delivers measurable business outcomes, rather than just a set of features.
- From Siloed to Collaborative: Ensuring all key stakeholders are engaged from the very beginning, their needs understood, and their concerns addressed, fostering collective ownership and accountability for the project's success.
- From Reactive Culture to Proactive Mindset: Prioritising the cultural shift necessary to embrace data-driven decision-making and move away from traditional firefighting.
By adopting this strategic and holistic perspective, organisations can effectively navigate the complexities of the market, select a solution that genuinely fits their unique needs, and build the sustained internal momentum necessary for a successful, scalable reliability transformation. As experts on Reliabilityweb.com often emphasise, true cultural change is as critical as technological adoption in achieving world-class reliability.
The Solution: Initial Considerations When Implementing Predictive Maintenance Software
Successfully implementing predictive maintenance software involves a structured, multi-phased approach that begins long before any purchase order is placed.
Phase 1: Strategic Alignment & Cultural Readiness – The People & Process Foundation
This foundational phase is crucial for ensuring that your organisation is prepared to embrace and leverage the power of PdM. Neglecting these initial considerations is a primary reason why pilots fail.
- Define Your "Why" and Quantify the Problem:
- Identify Specific Pain Points: What are the most frequent and costly equipment failures in your facility? Think beyond just the repair cost. For instance, a meat processing plant might identify a critical chain failure costing A$100,000 per hour, impacting "84 people's jobs at any time." A pet food producer might be battling "unexpected breakdowns causing production line stoppages," leading to "direct labour costs during idle time," "product waste," and "production rework costs."
- Quantify Current Losses: Meticulously calculate the true cost of these issues. Include lost production value, idle labour, wasted raw materials, rework expenses, and "expensive rush orders and premium freight costs" for emergency parts. This rigorous quantification directly addresses the "We don't have budget for this right now" objection by demonstrating the existing, quantifiable costs that PdM aims to avoid.
- Set Clear, Measurable KPIs: Define precisely what success looks like for your initial implementation. Examples include: "Reduce unplanned downtime on critical asset X by Y%," "Increase OEE for line Z by A%," or "Achieve a B% reduction in maintenance costs for monitored assets." These KPIs will be crucial for demonstrating ROI of predictive maintenance.
- Secure Executive Sponsorship & Cross-Functional Buy-in:
- Top-Down Support: Strong executive sponsorship is non-negotiable. Leadership must understand the strategic value of PdM beyond just maintenance, seeing it as a driver for profitability, competitive advantage, and risk mitigation.
- Engage All Key Stakeholders: Involve maintenance, operations, finance, IT, quality, and safety teams from the very beginning. Each department has a unique perspective and potential concerns.
- Tailor the Value Proposition: Articulate the benefits of PdM in terms that resonate with each group. For operations, it's about predictable uptime; for finance, it's about cost avoidance; for IT, it's about secure data management.
- This collaborative approach is vital for building internal momentum and preventing future roadblocks. For a comprehensive guide on securing this crucial support, refer to our article on Getting Buy-In for Predictive Maintenance from Site Leaders.
- Prioritise Culture Change:
- Shift from Reactive to Proactive: This is arguably the most challenging, yet most critical, consideration. Many organisations are deeply ingrained in a reactive "firefighting" culture or a rigid preventive maintenance mindset. Implementing PdM requires a fundamental shift to a proactive, data-driven approach.
- Address Fear of the Unknown: Employees might fear job displacement, new complexities, or a loss of autonomy. Openly communicate that PdM augments, rather than replaces, human expertise. It frees technicians from mundane tasks to focus on higher-value, strategic work.
- Foster a Learning Environment: Encourage curiosity and a willingness to learn new skills. Emphasise that data is a tool to help, not to judge. Build trust in the new system's insights.
- Empowerment: Empower frontline teams to act on insights and contribute to continuous improvement. Recognise and celebrate their role in the transformation.
- Invest Heavily in Training & Skill Development:
- Beyond Software Usage: Training must go beyond simply showing how to click buttons in the predictive maintenance software. It needs to focus on understanding the meaning of the data and alerts.
- For Technicians: Train them on interpreting alerts, performing basic diagnostics based on the insights provided (even if no vibration analysis expertise required for the initial alert), and understanding the new workflow (e.g., how PdM insights generate work orders in the CMMS for manufacturing). They need to trust the "pre-warning on any impending issues."
- For Managers: Train them on leveraging PdM data for strategic maintenance planning and scheduling software, resource allocation, and performance analysis.
- Ongoing Education: PdM is an evolving field. Plan for continuous learning and skill development to keep teams updated with new features and best practices. This ensures the long-term effectiveness of your condition monitoring systems.
Phase 2: Technical & Operational Foundations – The Right Tools & Setup
Once the organisational groundwork is laid, focus shifts to the technical and operational considerations.
- Assess Current Infrastructure & Data Landscape:
- Existing Systems: Catalogue your current CMMS for manufacturing, ERP, SCADA, and other control systems. Understand their capabilities and limitations.
- Connectivity: Evaluate your existing network infrastructure (Wi-Fi coverage, cellular dead zones, wired connections). This is crucial for planning wireless condition monitoring sensors deployment.
- Data Availability: What operational data (e.g., temperatures, pressures, flow rates, motor current) are you already collecting? Can it be integrated with new sensor data for richer insights?
- This step directly addresses the objection: “IT/security won’t allow it.”
- Counter-argument: Proactively engage IT. Highlight solutions that work without Wi-Fi or IT integration into the core operational network (e.g., modem-based systems or standalone networks). Emphasise secure encryption protocols for data transmission and storage. Provide documentation on data privacy and compliance. This transparent approach builds trust and mitigates security concerns, which are paramount in sectors like agri-food.
- Strategic Asset Selection for Initial Rollout:
- Start with Critical "Bad Actors": For your initial predictive maintenance pilot program, focus on a small number of assets that are both critical to production and have a history of frequent, costly breakdowns. This ensures quick, high-impact wins that visibly demonstrate downtime cost avoidance.
- Suitability for Monitoring: Choose assets where wireless condition monitoring sensors can be easily installed and provide clear, actionable data (e.g., rotating machinery like motors, pumps, fans, compressors).
- Manage Expectations: Clearly communicate that the initial rollout is focused and strategic, not an exhaustive plant-wide deployment. This prevents the perception of limited scope as a failure.
- Define Data Collection & Connectivity Strategy:
- Types of Condition Monitoring Techniques: Determine which techniques are most appropriate for your chosen assets (e.g., real-time vibration monitoring, temperature, MCSA, ultrasonics, oil analysis). A comprehensive condition monitoring systems approach often combines several methods.
- Sensor Placement & Frequency: Plan optimal sensor placement for maximum data fidelity. Define data collection frequency based on asset criticality and failure modes.
- Connectivity Solutions: Decide on the most suitable connectivity for your environment – 4G cellular for remote assets, dedicated standalone Wi-Fi for specific areas, or direct wired connections where appropriate. Ensure the chosen predictive maintenance equipment supports these options.
- For a detailed look at selecting the right features, explore our article on Predictive Maintenance Software Features That Matter.
- Plan for Integration with Existing Systems:
- CMMS Integration: This is vital. Plan how predictive maintenance software will integrate with your CMMS for manufacturing to automatically generate work orders from PdM alerts, update asset history, and track maintenance costs. This streamlines the entire workflow.
- Data Flow to Dashboards/Reporting: Ensure data from sensors and PdM insights can flow to centralised dashboards for asset health monitoring and reporting, providing a single source of truth.
- Minimising Manual Data Entry: Aim to automate data transfer as much as possible to reduce human error and workload.
Phase 3: Execution, Measurement & Communication – Proving & Sustaining Value
This phase is where the strategic planning translates into tangible results and where continuous momentum is built.
- Execute a Focused Pilot Program:
- Rapid Deployment: Implement the chosen predictive maintenance software and sensors efficiently. Factory AI's promise of "From Install to Insight in Under 30 Minutes per Asset" is a critical advantage here, allowing for quick setup and data collection.
- Meticulous Data Collection & Anomaly Detection: Ensure the system is actively collecting high-quality data and that machine learning in manufacturing is effectively identifying anomalies.
- Prompt Action on Insights: The most crucial step. When the system issues a "pre-warning on any impending issues," the maintenance team must act swiftly and decisively to validate the alert and perform the necessary intervention. This closes the loop and proves the system's value.
- For a step-by-step guide on executing your pilot, refer to our roadmap: The First 10 Steps: Roadmap of a Predictive Maintenance Pilot.
- Measure and Quantify Results Relentlessly:
- Track KPIs Against Baseline: Continuously monitor the KPIs defined in Phase 1 for your pilot assets. Compare current performance against the established baseline to demonstrate improvements.
- Focus on Downtime Cost Avoidance: This is the most compelling metric. For every predicted failure that is averted by a planned intervention, meticulously calculate the exact cost saved (lost production, idle labour, rework, emergency repair premiums). This quantifies the ROI of predictive maintenance.
- Document Every Success: Keep a detailed log of every alert, every intervention, and the resulting cost savings or efficiency gains. This data forms the backbone of your business case for scaling.
- For a deeper understanding of the realistic outcomes you can expect, consult our article on What Realistic Results Can Be Achieved in a Predictive Maintenance Pilot.
- Communicate Wins Widely and Consistently:
- Share Successes with Leadership: Regularly provide concise, high-level summaries of pilot achievements to executive leadership via simple emails. Focus on the quantifiable ROI of predictive maintenance and the strategic impact.
- Discuss Wins in Daily Huddles/Team Meetings: Crucially, share successes with the frontline maintenance and operations teams in their daily huddles. This reinforces the value of their efforts, builds morale, and fosters a sense of ownership. Celebrate specific instances where a technician acted on an alert and averted a major problem.
- Use Visual Management: Leverage dashboards and visualisations from the predictive maintenance software to make progress and achievements easily understandable across all levels of the organisation.
- This consistent, transparent communication is vital for sustaining cultural change and building unstoppable momentum for broader adoption.
- Plan for Iteration and Scalability:
- Pilot as a Learning Phase: Recognise that the pilot is an opportunity to learn what works best in your specific environment. Refine processes, sensor placements, and alert thresholds based on real-world data.
- Justify Broader Rollout: Use the compelling results from your pilot to build a robust business case for scaling the predictive maintenance software across more assets, production lines, or additional manufacturing sites.
- Continuous Improvement: Embrace a mindset of continuous improvement, leveraging PdM data not just for maintenance, but for optimising overall operational efficiency.
Factory AI's Predictive Maintenance Software Platform: Your Partner in Implementation
Factory AI is purpose-built to address these initial considerations and common pitfalls, ensuring a smooth and successful implementation of predictive maintenance software in your manufacturing facility. Our platform is designed to empower your team and deliver tangible results from day one.
- "Predictive Maintenance That Pays for Itself in 6 Months": Our core promise directly addresses the financial justification, providing rapid ROI of predictive maintenance that makes the business case for investment undeniable. This helps overcome the "We don't have budget for this right now" objection.
- "Built for the Agri-Food Industry": Our deep specialisation means we understand the unique challenges of your sector, including high hygiene environments, perishable goods, and HACCP and maintenance software compliance. This ensures our solution is highly relevant and effective for your specific assets like compressors, heat exchangers, fans, blowers, and pumps.
- "Works Without Wi-Fi or IT Integration": We directly address IT and cybersecurity concerns by offering flexible connectivity options (e.g., modem-based or standalone networks) that bypass your core operational network. This helps overcome the "IT/security won't allow it" objection, simplifying deployment of predictive maintenance equipment.
- "No Vibration Analysis Expertise Required": Our machine learning in manufacturing capabilities distil complex sensor data into clear, actionable insights. This empowers your existing maintenance team, eliminating the need for specialist hires and addressing the "We don’t have the people to manage another system" concern.
- "Sensor-Agnostic – Use the Hardware You Already Have": This flexibility allows you to leverage any existing wireless condition monitoring sensors or choose the most cost-effective hardware, reducing initial investment and vendor lock-in.
- "From Install to Insight in Under 30 Minutes per Asset": Our rapid deployment capability ensures you can quickly set up your pilot, start collecting data, and demonstrate value, crucial for building early momentum.
- "Sensor + Software Bundled in One Subscription": Our transparent, flat-fee model simplifies budgeting and provides predictable costs, appealing to financial stakeholders.
- "Designed for the Team on the Tools": Our user-friendly interface is crafted for frontline maintenance professionals, ensuring high adoption rates and practical utility. This fosters the necessary culture change.
- "Built by Engineers Who’ve Worked on the Plant Floor": Our team's firsthand experience on the factory floor ensures our solution is practical, robust, and truly addresses real-world maintenance challenges.
- "More Than Predictive – A Full Reliability Platform": Beyond just prediction, Factory AI offers integrated CMMS capabilities, maintenance planning and scheduling software, and holistic asset health monitoring, providing a comprehensive solution that streamlines your entire maintenance workflow and supports continuous improvement.
Conclusion: Your Strategic Path to Sustainable Reliability
Implementing predictive maintenance software is a strategic journey that promises significant returns for manufacturing facilities, particularly in the demanding agri-food sector. However, the success of this journey hinges on meticulous initial considerations that extend far beyond simply purchasing technology. It requires a deep understanding of your operational pain points, a commitment to cultural change, robust investment in training, and a clear plan for proving and communicating value.
By prioritising strategic alignment, fostering a proactive culture, empowering your teams with the right training, and meticulously planning your technical implementation, you can overcome common pitfalls and ensure your investment delivers truly transformative results. The transition from reactive or preventive maintenance software to a data-driven, intelligent approach will not only enhance your asset health monitoring but also drive unparalleled efficiency, profitability, and resilience across your entire manufacturing operation.
Don't let the complexities of initial implementation deter you from unlocking the immense benefits of machine learning in manufacturing and advanced condition monitoring systems. With a strategic approach and the right partner, your factory can achieve enduring operational excellence.
Ready to lay a strong foundation for your predictive maintenance journey and unlock its full potential?
Book a maintenance software demo with us today to explore how Factory AI can guide you through these initial considerations and deliver the best predictive maintenance software solution tailored for your manufacturing facility.
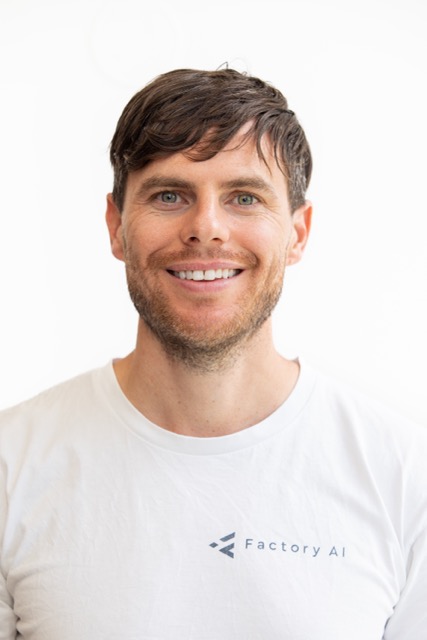