How to Use Data to Guide Your Predictive Maintenance Rollout Plan
Mar 18, 2025
Predictive Maintenance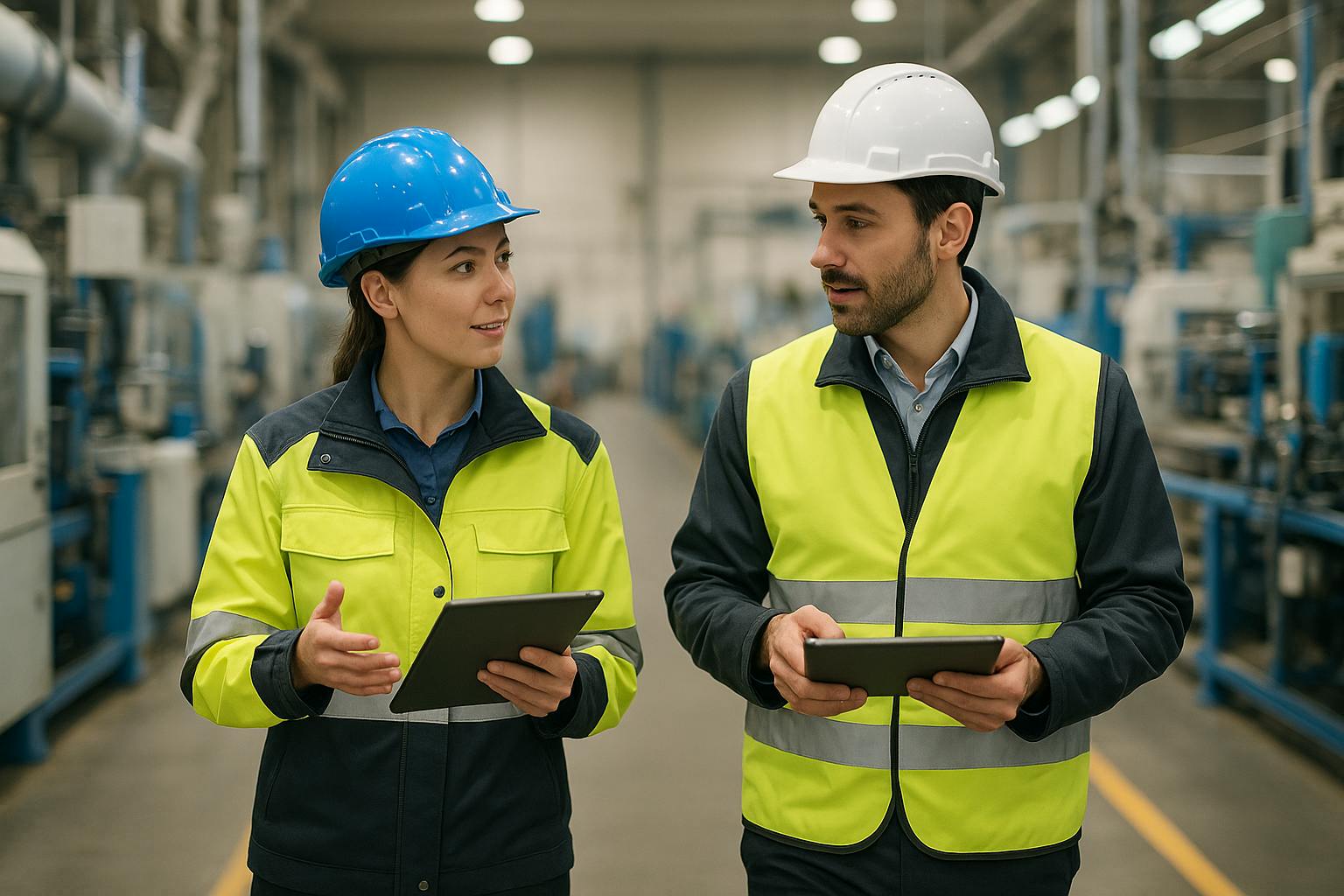
Predictive maintenance is transforming how manufacturers operate, promising less downtime, reduced costs, and optimized asset performance. But how do you ensure your predictive maintenance initiative delivers on these promises? The answer lies in your data.
A common question we hear is: 'What data should we examine to determine if predictive maintenance is right for us and to guide our rollout?' This post provides that answer. We'll explore the essential data sources—ranging from your CMMS records and process control systems to the invaluable insights of your on-site teams and industry peers—that should form the foundation of your predictive maintenance implementation plan, ensuring you target the right assets, at the right time, for maximum impact.
How to Use Data to Guide Your Predictive Maintenance Rollout Plan
Predictive maintenance is revolutionising industrial operations, helping manufacturers minimise unplanned downtime, reduce maintenance costs, and optimise asset performance. However, the success of a predictive maintenance strategy depends on the availability, accuracy, and analysis of data.
One of the most common questions we receive is: What data sources should we examine as a site considering predictive maintenance to determine if it's the right fit for us?
Well, here's our answer.
Rolling out predictive maintenance requires a structured approach—one that leverages various data sources to ensure that maintenance efforts are targeted at the right assets, at the right time, with the right actions. In this guide, we’ll explore the critical data sources that should inform your predictive maintenance rollout and how to use them to maximise the return on your investment.
1. CMMS Data: The Foundation of Maintenance Insights
A Computerised Maintenance Management System (CMMS) is the backbone of maintenance data in most industrial facilities. It contains historical records of maintenance activities, asset health, and work orders. Here’s how to leverage CMMS data:
Asset Criticality Matrix
Not all assets require predictive maintenance—some are more critical than others. Use your CMMS to create an asset criticality matrix, which ranks equipment based on factors such as:
- Production impact (does failure cause line stoppage?)
- Repair costs and lead times for spare parts
- Health and safety risks
- Frequency and severity of past failures
Downtime Hours per Asset
Your CMMS logs downtime for each asset. By analysing this data, you can:
- Identify the assets responsible for the most lost production time
- Quantify downtime costs (e.g., $ per hour of lost production)
- Prioritise predictive maintenance efforts where it will have the biggest ROI
Failure Modes and Trends
Understanding which failure modes occur most often enables you to focus predictive maintenance efforts on solving recurring issues. CMMS data can help answer:
- What are the most common failure types for each asset?
- Do failures follow a seasonal or operational pattern?
- Are certain failure modes more likely to occur in specific conditions (e.g., humidity, temperature fluctuations)?
Work Order History
A deep dive into historical work orders can reveal inefficiencies in your current maintenance strategy. Look for:
- Reactive vs. preventive maintenance ratios (how often are you fixing breakdowns vs. performing scheduled PMs?)
- Time between failures (Mean Time Between Failures - MTBF)
- Mean Time to Repair (MTTR)
- Frequent failure causes and whether past fixes have been effective
2. Capturing Anecdotal Data from Site Conversations
While digital records are valuable, the insights from site personnel—engineers, operators, and maintenance staff—are just as critical in shaping a predictive maintenance strategy.
Conversations with Operators and Technicians
Operators and technicians interact with the equipment daily. Engaging them in structured conversations can uncover:
- Repeated adjustments they make to keep equipment running smoothly
- Unusual noises, vibrations, or performance dips they have observed
- Workarounds they rely on when equipment isn’t functioning correctly
- Situations where past maintenance actions did not resolve the issue long-term
Investigating Past Near-Misses and Failures
By speaking with maintenance teams, you can build a richer understanding of past failures and near-misses that might not be well-documented in CMMS data:
- Was there an early warning sign before the failure that was ignored or unrecognised?
- How often have teams replaced the same component before realising the root cause was elsewhere?
- Have certain failures always happened after specific production conditions?
Identifying Manual Data Logging Gaps
Many sites still rely on paper-based logs or informal reporting, which means some failure patterns are not captured digitally. Work with teams to:
- Encourage systematic logging of manual observations
- Digitise important handwritten records where feasible
- Train operators on what failure symptoms to report consistently
Confirming Maintenance Work Effectiveness
Maintenance teams have hands-on experience with past repairs. Their insights can help determine:
- Whether prior repairs solved the root cause or just the symptoms
- Which assets frequently require rework or additional adjustments
- Where maintenance activities could be optimised to prevent recurring breakdowns
3. SCADA, PLC & Historian Data: Leveraging Process Control Systems
Most industrial sites have Supervisory Control and Data Acquisition (SCADA) systems, Programmable Logic Controllers (PLCs), and Data Historians that store vast amounts of operational data.
Process Variables for Predictive Maintenance
SCADA and PLCs track key process variables that can be used for predictive insights:
- Pressure anomalies in hydraulic and pneumatic systems
- Flow rates indicating pump or valve blockages
- Temperature profiles for heat exchangers and cooling systems
Combining Process Data with Manual Insights
By integrating SCADA/PLC data with anecdotal feedback from operators, you can:
- Detect process conditions that contribute to wear and tear
- Identify correlations between operating conditions and asset failures
- Optimise predictive maintenance models using a combination of structured and unstructured data
4. Operator & Maintenance Team Feedback
Not all failure patterns are captured in digital data—some are best understood by those closest to the equipment.
Capturing Tribal Knowledge
Operators and maintenance personnel often notice early warning signs of failure that may not be recorded in data systems. This could include:
- Unusual smells (burning, overheating insulation)
- Changes in machine behaviour (increased noise, slower operation)
- Frequent manual adjustments required to keep equipment running
Digital Logs & Mobile Apps
Encouraging operators to log observations in a mobile app or digital system ensures valuable insights are recorded for predictive analysis.
5. Building Meaningful Connections Beyond Your Site
Predictive maintenance insights don’t just come from internal data—they can also be enriched by learning from industry peers and experts outside of your site.
Networking with Site Leaders & Reliability Professionals
Engaging with maintenance and reliability professionals at other facilities can provide new perspectives on:
- Best practices in predictive maintenance implementation
- Lessons learned from successful and unsuccessful rollout strategies
- Innovative technologies and methodologies being adopted in the industry
Attending Industry Conferences & Webinars
Industry events and online forums offer valuable opportunities to:
- Hear real-world case studies from maintenance leaders
- Discover emerging trends in predictive maintenance technology
- Engage in discussions on maintenance challenges and solutions
Benchmarking Against Similar Sites
Comparing your maintenance performance with similar sites can help identify:
- Areas where your predictive maintenance efforts can improve
- Key performance indicators (KPIs) that are leading indicators of success
- Strategies to enhance collaboration across different sites within your organisation
Leveraging Online Communities & Forums
Online platforms dedicated to industrial maintenance, such as LinkedIn groups and specialised forums, provide an accessible way to:
- Exchange knowledge with industry peers
- Stay updated on technological advancements
- Seek advice on predictive maintenance challenges
Specific Questions to Ask someone already doing PdM
When you have found someone in your network that uses predictive maintenance, here are examples of questions you might want to cover with them:
Getting Started with Predictive Maintenance
- What motivated your site to implement predictive maintenance?
- How did you decide which assets to monitor first?
- What were your biggest concerns before starting?
- How long did it take to see tangible benefits?
- What challenges did you face during implementation?
Performance & Impact
- How has predictive maintenance changed your maintenance strategy?
- Have you reduced unplanned downtime? By how much?
- Can you share an example where predictive maintenance prevented a major failure?
- How have maintenance costs changed since using predictive maintenance?
- What has been the impact on production efficiency and OEE (Overall Equipment Effectiveness)?
Reliability & Accuracy
- How accurate are the predictions? Have there been any false positives or missed failures?
- How much confidence do operators and maintenance teams have in the system?
- What type of alerts or insights have been most valuable?
Integration & Usability
- How easy was it to integrate predictive maintenance into your existing processes?
- What training or onboarding was required for your team?
- How user-friendly is the system? Do your teams actively engage with it?
- How well does the system integrate with your existing CMMS (Computerised Maintenance Management System) or ERP?
ROI & Future Plans
- How long did it take to achieve ROI on predictive maintenance?
- If you were to start again, what would you do differently?
- What are your next steps with predictive maintenance—scaling, refining, or exploring new technologies?
Bringing It All Together: Your Predictive Maintenance Roadmap
To effectively roll out predictive maintenance, follow these steps:
- Audit Your Data Sources – Identify gaps in data collection and areas for improvement.
- Prioritise Critical Assets – Use an asset criticality matrix to focus efforts where impact is highest.
- Engage Site Personnel – Gather anecdotal insights to complement structured data sources.
- Expand Your Network – Learn from industry professionals and external sources.
- Refine & Optimise – Continuously adjust based on feedback and system performance.
Conclusion
At Factory AI, we would be more than happy to speak to any site that is going through, or considering going through this process. We can help guide them, offer expertise from having done dozens of rollouts, provide introductions to current customers, and much more.
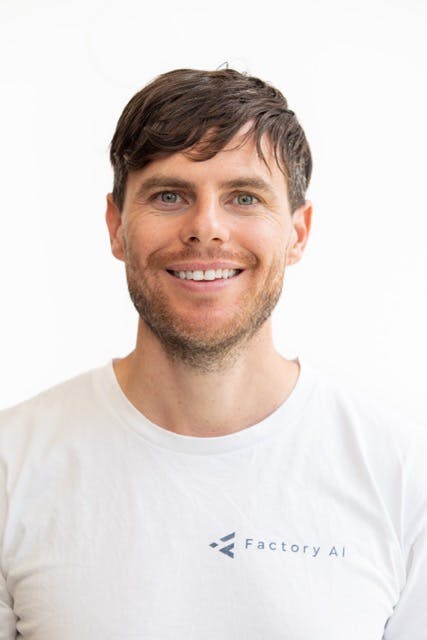
JP Picard
Jean-Philippe Picard is the CEO and Co-Founder of Factory AI. As a positive, transparent, and confident business development leader, he is passionate about helping industrial sites achieve tangible results by focusing on clean, accurate data and prioritizing quick wins. Jean-Philippe has a keen interest in how maintenance strategies evolve and believes in the importance of aligning current practices with a site’s future needs, especially with the increasing accessibility of predictive maintenance and AI. He understands the challenges of implementing new technologies, including addressing potential skills and culture gaps within organizations.