How to Buy Predictive Maintenance Software for Manufacturing
Jul 4, 2025
Predictive Maintenance Software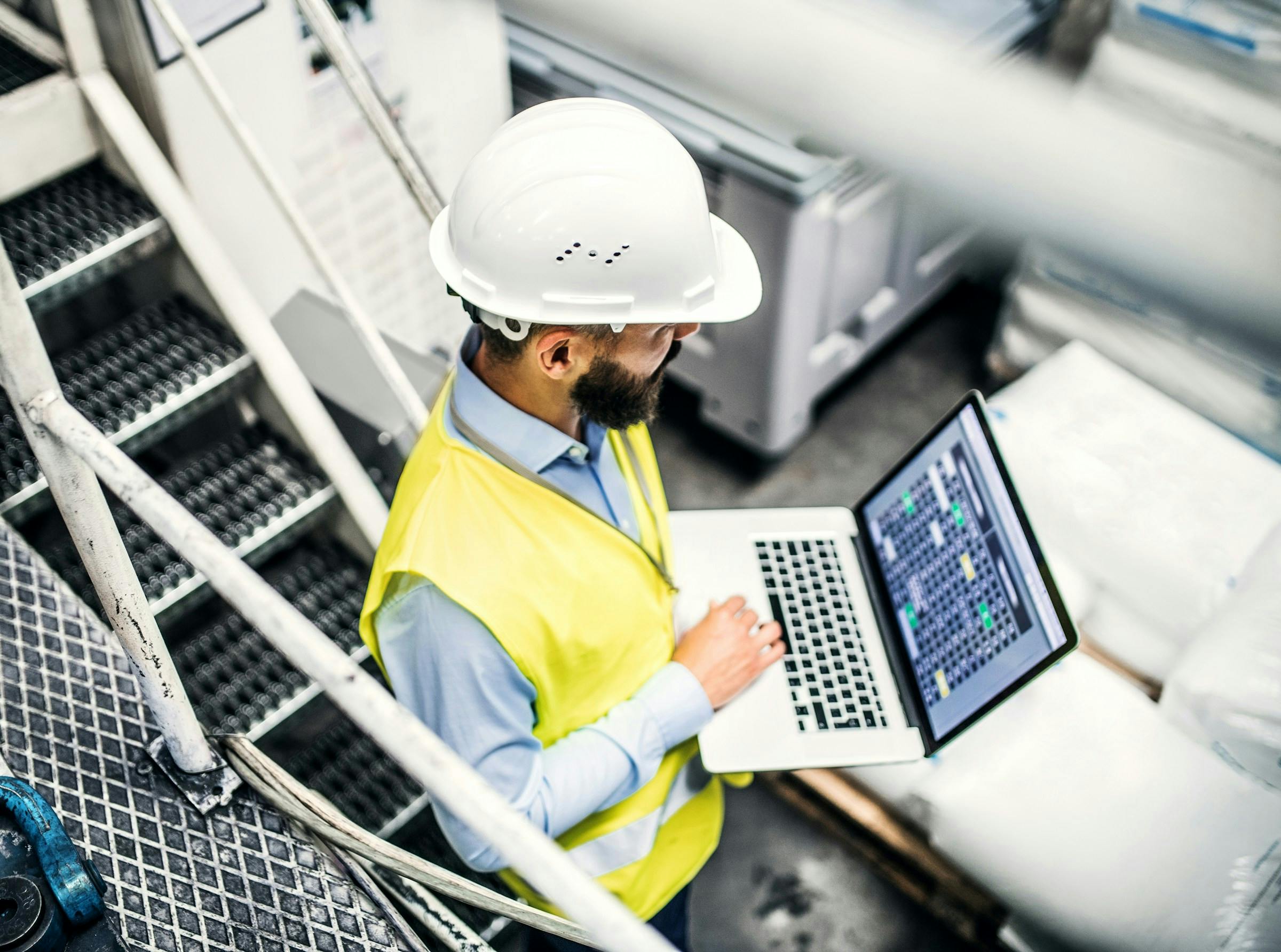
How to Buy Predictive Maintenance Software for Manufacturing
Introduction
For any site reliability engineer or maintenance manager, the allure of a factory floor where breakdowns are predicted, not just reacted to, is undeniable. The promise of extended asset life, significant cost reductions, enhanced safety, and unblemished product quality makes predictive maintenance software a compelling investment.
Yet, the journey to acquiring and successfully implementing this transformative technology is rarely straightforward. With a myriad of solutions on the market, each promising revolutionary results, how do you navigate the complexities to choose the best predictive maintenance software for your specific needs, particularly in the demanding agri-food sector? This guide will demystify the buying process, providing a strategic roadmap to ensure your investment delivers tangible ROI of predictive maintenance and genuinely transforms your manufacturing operations.
The Problem: Navigating the Minefield of Predictive Maintenance Procurement
The decision to invest in predictive maintenance software is a significant one, fraught with potential pitfalls if not approached strategically. Many organisations, eager to escape the cycle of reactive maintenance or the inefficiencies of traditional preventive maintenance software, jump into vendor discussions without a clear understanding of their internal needs or the nuances of modern PdM solutions. This can lead to:
- Misaligned Expectations: Believing a new system will solve all problems without addressing underlying cultural or process issues. A common misconception is that simply having predictive maintenance tools will automatically eliminate downtime, without the necessary internal processes or training to act on the insights.
- Budget Overruns and Hidden Costs: Focusing solely on the initial software price without accounting for sensor costs (wireless condition monitoring sensors, predictive maintenance equipment), installation, integration with existing CMMS for manufacturing, training, and ongoing support. This often leads to the objection: "We don't have budget for this right now," even when the long-term savings are substantial.
- Poor Adoption Rates: Selecting a system that is too complex, not user-friendly, or doesn't integrate well with existing workflows. If the maintenance team finds it cumbersome or irrelevant, the investment will yield minimal returns. This is particularly true if the solution requires extensive vibration analysis expertise that the in-house team lacks.
- Security and IT Roadblocks: Overlooking crucial IT and cybersecurity concerns, especially for cloud-based maintenance software or solutions requiring network integration in sensitive environments like food processing. This often results in the objection: "IT/security won't allow it," stalling projects indefinitely.
- Inadequate ROI: Failing to define clear metrics for success, leading to an inability to demonstrate the value of the investment. Without measurable improvements in uptime, cost reduction, or asset lifespan, securing future funding or scaling the solution becomes impossible.
- Vendor Lock-in: Choosing a proprietary system that limits flexibility in hardware or data integration, making future upgrades or changes difficult and expensive.
For the agri-food sector, these pitfalls are amplified. The perishable nature of products, stringent HACCP and maintenance software compliance requirements, and the constant pressure of maintenance in high hygiene environments mean that downtime is exceptionally costly, and any misstep in technology adoption can have severe consequences for product quality and brand reputation.
The stakes are high, demanding a methodical and informed buying process. For a deeper dive into these and other common hurdles, explore our article on the Top 10 Predictive Maintenance Objections.
The Insight: Strategic Procurement as the Foundation for Reliability Transformation
The acquisition of predictive maintenance software should not be viewed merely as a procurement exercise, but as a strategic initiative to transform your manufacturing operations. The core insight is that the right solution, properly implemented, will move your organisation beyond the limitations of preventive maintenance vs predictive maintenance debates, enabling true operational intelligence and competitive advantage.
This requires a shift in mindset:
- From Cost to Investment: Recognising that the upfront expenditure is an investment designed to deliver significant ROI of predictive maintenance through cost avoidance, increased throughput, and extended asset life.
- From Technology to Solution: Understanding that you're not just buying software or sensors, but a comprehensive solution that addresses specific operational pain points and delivers measurable business outcomes.
- From Siloed to Collaborative: Involving all key stakeholders from the outset, ensuring their needs are met and their concerns addressed, fostering collective ownership of the project.
By adopting this strategic perspective, you can navigate the complexities of the market, select a solution that genuinely fits your needs, and build the internal momentum necessary for a successful, scalable reliability transformation. As experts on Reliabilityweb.com often emphasise, a holistic approach to reliability is essential for long-term success.
The Solution: A Step-by-Step Guide to Buying Predictive Maintenance Software
Successfully acquiring and implementing predictive maintenance software involves a structured approach, moving from internal assessment to vendor selection, pilot, and eventual scaling.
Phase 1: Internal Readiness and Needs Assessment – Defining Your "Why"
Before even looking at vendors, a thorough internal assessment is paramount. This phase defines your specific problems, objectives, and the metrics for success.
- Identify and Quantify Pain Points:
- What are your most frequent and costly equipment failures? (e.g., specific motors, pumps, conveyors, extruders).
- What is the true cost of unplanned downtime for these critical assets? Go beyond repair costs to include lost production, idle labour, wasted raw materials, production rework, and premium freight for emergency parts. For instance, a meat processing plant might quantify a critical chain failure costing "$100K+ per hour." A pet food producer might detail "10-30 operators without work and wasting their time" during a stoppage.
- Where are you experiencing excessive preventive maintenance tasks that aren't truly necessary (over-maintenance)?
- Are you struggling with inconsistent product quality linked to equipment performance?
- Are spare parts frequently "not in stock," leading to extended downtime and "expensive rush orders"?
- This step directly addresses the "We don't have budget for this right now" objection by clearly demonstrating the existing, quantifiable costs that PdM aims to avoid, turning perceived expense into strategic investment.
- Define Clear Objectives and Key Performance Indicators (KPIs):
- What do you want the predictive maintenance software to achieve? (e.g., "Reduce unplanned downtime on critical packaging lines by 30%," "Extend asset lifespan of key mixers by 15%," "Decrease maintenance costs by 20%," "Improve first-time fix rates").
- How will you measure the ROI of predictive maintenance? This might include Overall Equipment Effectiveness (OEE) improvements, Mean Time Between Failures (MTBF), Mean Time To Repair (MTTR), spare parts inventory reduction, or energy savings.
- These KPIs will guide your vendor selection and provide the framework for demonstrating success.
- Identify and Engage Key Stakeholders:
- Maintenance & Reliability Team: (Managers, Engineers, Technicians) – They are the primary users. Understand their current challenges with maintenance planning and scheduling software, their familiarity with condition monitoring systems, and their concerns about new tools. Ensure they feel empowered, not threatened.
- Production/Operations Management: They care about uptime, throughput, and consistent quality. Show them how PdM ensures predictable production flows.
- Finance Department: They need to see the financial justification. Present the ROI of predictive maintenance in clear monetary terms, focusing on cost avoidance and efficiency gains. Highlight the transparent pricing models.
- IT Department: Crucial for connectivity, data security, and integration. Address their concerns about cloud-based maintenance software, network load, and data privacy. This is where the objection "IT/security won't allow it" often arises.
- Quality & Safety Teams: They care about compliance (HACCP and maintenance software) and risk mitigation. Show them how PdM prevents equipment failures that could compromise product safety or create hazards, especially in high hygiene environments.
- Executive Leadership: They need a high-level overview of strategic benefits, competitive advantage, and overall business impact.
- For deeper insights into securing essential buy-in across these levels, read our comprehensive guide on Getting Buy-In for Predictive Maintenance from Site Leaders.
- Assess Current Maintenance Maturity:
- Are you primarily reactive, preventive, or already dabbling in basic condition monitoring?
- What CMMS for manufacturing or EAM system do you currently use? How well does it manage maintenance planning and scheduling software? What are its integration capabilities?
- What predictive maintenance equipment or wireless condition monitoring sensors do you already have? Can they be leveraged?
Phase 2: Solution Exploration and Vendor Evaluation – Finding the Right Fit
With your internal needs clearly defined, you can now effectively evaluate potential solutions and vendors. This is a critical phase where a meticulous comparison of features, capabilities, and vendor alignment with your specific requirements will determine long-term success.
- Understand the Components of a PdM Solution:
- Sensors (Data Collection): These are the eyes and ears of PdM. Look for wireless condition monitoring sensors that are robust, easy to install, battery-powered, and suitable for your environment (e.g., resistant to washdowns in high hygiene environments). Consider what types of data they collect (real-time vibration monitoring, temperature, acoustics, motor current, pressure).
- Connectivity: How does data get from the sensor to the cloud/server? Options include Wi-Fi, 4G/LTE, LoRaWAN. Crucially, can the system work without Wi-Fi or IT integration into your core operational network, perhaps using a standalone network or cellular modems? This is vital for addressing IT concerns and simplifying deployment.
- Software Platform (Analysis & Insights): This is the brain. It should ingest data, apply machine learning in manufacturing algorithms for machine condition monitoring with AI, detect anomalies, and provide actionable insights.
- User Interface: How easy is it to interpret the data and alerts? Is it designed for the team on the tools? Does it provide clear, prescriptive maintenance capabilities (e.g., "This bearing is failing, here's why, and here's what to do") rather than just raw data that requires specialist interpretation?
- Integration Capabilities: Can it seamlessly integrate with your existing CMMS for manufacturing (e.g., MEX integration, as requested by a pet food producer)? Can it pull data from PLCs or other control systems?
- Key Features to Look For in Predictive Maintenance Software: To ensure you select the best predictive maintenance software, pay close attention to the following features. For a detailed breakdown of what truly matters, consult our article on Predictive Maintenance Software Features That Matter.
- AI-Driven Anomaly Detection: This is the heart of modern PdM. The system should learn normal behaviour and flag deviations automatically. This means no vibration analysis expertise required from your team to interpret complex data, democratising the power of advanced analytics.
- Prescriptive Maintenance Capabilities: Does the software offer clear recommendations for action, not just raw alerts? This empowers technicians to respond effectively and efficiently, moving beyond mere problem identification to actionable solutions.
- Comprehensive Asset Health Monitoring: Does it provide a holistic view of asset health across your entire plant, not just isolated data points? This comprehensive oversight is critical for strategic decision-making.
- Scalability: Can the solution easily expand from a pilot to cover hundreds or thousands of assets across multiple sites, offering a clear growth path?
- Deployment Speed and Ease: How quickly can sensors be installed and insights generated? Factory AI's "From Install to Insight in Under 30 Minutes per Asset" is a key differentiator here, minimising disruption and accelerating time to value.
- Industry Specialisation: Is the vendor experienced in your specific sector? Maintenance software for food and beverage or predictive maintenance for dairy plants will understand your unique challenges (e.g., washdowns, perishability, compliance, specific equipment types like extruders or pasteurizers).
- Security & Data Privacy: For cloud-based maintenance software, inquire about data encryption, access controls, and compliance certifications. This addresses IT concerns directly and builds trust in sensitive data handling.
- Reporting & Analytics: Can the system generate customisable reports to track KPIs and effectively demonstrate the ROI of predictive maintenance to all stakeholders? Look for capabilities that simplify data interpretation for executive summaries.
- Vendor Due Diligence:
- Track Record & Case Studies: Ask for predictive maintenance case studies, especially from similar industries or asset types. Look for examples of "downtime cost avoidance" and quantifiable benefits.
- Customer References: Speak to existing customers, particularly those with similar operational profiles and challenges. A pet food producer, for example, might want to speak with a biscuit manufacturer (like a generic "National Biscuit Company") due to similar production processes and operational demands.
- Support & Training: What kind of ongoing support, training, and maintenance is provided? How responsive are they to issues? Robust support is crucial for long-term success.
- Vendor Expertise: Are they built by engineers who've worked on the plant floor? This indicates a practical understanding of your challenges and a solution designed with real-world usability in mind.
- Pricing Model: Understand the full cost. Is it a transparent sensor + software bundled in one subscription (e.g., £500 per asset/year), or are there hidden fees for data usage, support tiers, or additional features? Compare CAPEX vs. OPEX implications to align with your budgeting cycles. A pet food producer, for example, noted a solution being "approximately half the price" of competitors like Movis or SKF, highlighting the importance of competitive pricing and clear value.
Phase 3: Pilot Program and Proof of Concept – Proving the Value
A well-designed predictive maintenance pilot program is critical. It allows you to test the solution in your environment, gather real-world data, and build internal confidence before a full rollout. It's the ultimate proof of concept that converts skepticism into buy-in.
- Select Pilot Assets Strategically:
- Choose a small number of critical assets that have a history of costly breakdowns or are known bottlenecks. These should be assets where a successful intervention will have a high, visible impact (e.g., a critical extruder in pet food, a main chain in meat processing, a specific motor with a gearbox and bearings that costs "$80K per event" in downtime).
- Consider assets that are relatively easy to instrument with wireless condition monitoring sensors to ensure a smooth initial deployment.
- Aim for a mix of production assets (e.g., barters and cutting machines in fish processing) and plant services assets (e.g., compressors and pumps).
- Define Pilot Success Metrics:
- Revisit the KPIs from Phase 1. What specific improvements do you expect to see during the pilot? (e.g., "Prevent X number of unplanned shutdowns on Y asset," "Reduce maintenance costs on Z asset by A%").
- Focus on measurable ROI of predictive maintenance within the pilot timeframe (e.g., Factory AI's proven ability to demonstrate that "Predictive Maintenance That Pays for Itself in 6 Months").
- Execute and Monitor:
- Deploy the predictive maintenance equipment and software. Factory AI's promise of "From Install to Insight in Under 30 Minutes per Asset" is crucial here, especially if installation needs to occur on weekends due to 24/7 operations and tight production schedules.
- Actively monitor the insights provided by the machine condition monitoring with AI.
- Ensure the maintenance team is trained and actively using the system.
- Document every alert, every intervention, and every avoided breakdown.
- Review and Report:
- Regularly review pilot performance against your defined metrics.
- Prepare compelling reports for all stakeholders, highlighting successes and quantifying the downtime cost avoidance. This data is essential for building internal momentum and securing budget for a wider rollout.
- Gather feedback from the frontline team and address any challenges encountered, refining processes as needed. This iterative approach is crucial for long-term success.
Phase 4: Implementation and Scaling – Achieving Full Operational Excellence
Once the pilot demonstrates clear value, the focus shifts to a broader implementation and continuous improvement, integrating the new capabilities into the fabric of your operations.
- Develop a Phased Rollout Plan:
- Based on pilot learnings, create a detailed plan for scaling the solution across more assets or additional sites. Prioritise assets based on criticality and potential impact, ensuring a managed expansion.
- Consider the logistical challenges of installation (e.g., weekend-only work for 24/7 plants) and allocate resources accordingly.
- Comprehensive Training and Change Management:
- Provide ongoing, practical training for all relevant personnel – maintenance, operations, IT. Focus on practical application and how the new system makes their jobs easier and more effective.
- Address any lingering resistance to change by highlighting successes and demonstrating the benefits directly. Emphasise that the solution is designed for the team on the tools and augments, rather than replaces, their expertise, empowering them to become more strategic.
- Integrate with Existing Systems:
- Deepen integration with your CMMS for manufacturing or maintenance planning and scheduling software. Automate work order generation from PdM alerts to streamline workflows and ensure insights lead directly to action. Factory AI's MEX integration capabilities are a key example, ensuring a cohesive and efficient operational ecosystem.
- Explore integration with other operational data sources (e.g., PLC data) for even richer insights and a more comprehensive view of machine performance.
- Continuous Improvement:
- Regularly review the performance of your PdM programme. Are you achieving your KPIs? Are there new assets that could benefit? Are there opportunities to further optimise processes based on the data?
- Leverage the data from asset health monitoring to refine maintenance strategies, optimise processes, and drive ongoing efficiency gains across the entire plant.
- Factory AI's evolution to "More Than Predictive – A Full Reliability Platform" supports this continuous improvement journey, offering integrated capabilities beyond just prediction to holistic reliability management.
Real-World Examples: The Buying Journey in Action
Let's illustrate this buying process with hypothetical scenarios from the agri-food sector, showing how the right choices lead to success.
Scenario 1: A Large Dairy Producer Seeking Standardisation
A large dairy producer, operating multiple plants, was struggling with inconsistent maintenance practices and unpredictable downtime across sites, despite using various preventive maintenance software solutions. Their leadership was "price-sensitive," and IT had concerns about new cloud-based maintenance software impacting their operational network.
- Phase 1: They first quantified the cumulative cost of unplanned downtime across their homogenisers and bottling lines, revealing millions in annual losses from lost product and idle labour. They defined a clear goal: reduce unplanned downtime by 25% within 18 months and standardise asset health monitoring nationally. They involved their site leaders early on, addressing concerns about budget and workload.
- Phase 2: They evaluated several predictive maintenance software vendors. They prioritised solutions that were built for the agri-food industry, offered no vibration analysis expertise required (as their in-house team lacked specialists), and could work without Wi-Fi or IT integration into their core network. Factory AI stood out with its sensor + software bundled in one subscription model, which was "approximately half the price" of other competitors, addressing their price sensitivity. They also liked that Factory AI was built by engineers who've worked on the plant floor, suggesting practical understanding of their challenges. They specifically referenced Factory AI's detailed feature list when comparing solutions.
- Phase 3: They initiated a predictive maintenance pilot program on 10 critical homogenisers and 5 bottling line motors at their largest plant. The installation was rapid ("From Install to Insight in Under 30 Minutes per Asset"), occurring over weekends to minimise disruption. Within four months, the system predicted two major bearing failures and one pump cavitation, allowing for planned repairs during scheduled sanitation windows. These avoided failures, meticulously documented, demonstrated a clear ROI of predictive maintenance well within the 6-month payback period. The maintenance team, using mobile devices, found the system intuitive and helpful.
- Phase 4: Based on the successful pilot, the producer secured funding for a national rollout. They integrated Factory AI's insights with their existing CMMS for manufacturing, automating work order creation. The real-time vibration monitoring and machine condition monitoring with AI became central to their new, standardised reliability programme, leading to significant improvements in OEE and a leaner spare parts inventory across all plants.
Scenario 2: A Medium-Sized Baked Goods Manufacturer Battling Rework
A baked goods manufacturer consistently faced issues with product rework (e.g., unevenly baked bread, misshapen biscuits) due to subtle malfunctions in their ovens and forming machines. Their preventive maintenance software was good for scheduling, but couldn't predict these nuanced quality issues.
- Phase 1: They identified that "production rework costs" were a significant drain, along with "product waste" from discarded batches. Their goal was to reduce rework by 15% and improve first-pass quality. They involved their quality control team from the start, emphasising the link between equipment health and product integrity for HACCP and maintenance software compliance.
- Phase 2: They sought predictive maintenance software that could go beyond basic breakdown prediction to address quality-related anomalies. They looked for solutions with advanced machine learning in manufacturing capable of correlating sensor data (e.g., temperature uniformity, motor load on forming machines) with product quality outcomes. They also needed a solution that would be designed for the team on the tools and easy for their existing maintenance staff to adopt, as they were concerned about adding complexity.
- Phase 3: They launched a predictive maintenance pilot program on their most problematic oven and one forming machine. Wireless condition monitoring sensors were installed. The machine condition monitoring with AI quickly identified subtle temperature fluctuations in the oven and intermittent motor load anomalies on the forming machine, which correlated with known quality issues. The system provided "pre-warning on any impending issues," allowing the maintenance team to proactively calibrate sensors and adjust motor settings. This led to a measurable reduction in rework within the pilot phase, providing compelling predictive maintenance case studies.
- Phase 4: The success of the pilot, clearly demonstrating downtime cost avoidance and quality improvements, paved the way for a wider rollout. The predictive maintenance tools became an integral part of their quality assurance process, not just maintenance. Their CMMS for food and beverage industry was updated to reflect these new, condition-based quality checks, ensuring consistent product output and reducing waste from over-processing.
These scenarios highlight that the "how to buy" is as critical as the "what to buy." A strategic approach, focused on clear objectives, stakeholder collaboration, and proof of value, is the key to unlocking the full potential of predictive maintenance software in manufacturing.
Conclusion: Your Strategic Path to Reliability Excellence
Buying predictive maintenance software for manufacturing is a strategic investment that can fundamentally transform your operations, driving efficiency, profitability, and competitive advantage. It's about moving beyond the limitations of traditional preventive maintenance software and embracing the power of data-driven intelligence.
The journey requires careful planning: from quantifying your specific pain points and defining clear KPIs, to meticulously evaluating vendors based on their technology, industry expertise, and support. A well-executed predictive maintenance pilot program is your most powerful tool for building internal momentum and demonstrating tangible ROI of predictive maintenance.
Factory AI stands ready to be your partner in this transformative journey. We offer:
- Predictive Maintenance That Pays for Itself in 6 Months: A clear, rapid return on your investment.
- Built for the Agri-Food Industry: Specialised expertise for your unique challenges, including maintenance in high hygiene environments and HACCP and maintenance software compliance.
- Works Without Wi-Fi or IT Integration: Addressing critical IT and security concerns with flexible connectivity options.
- No Vibration Analysis Expertise Required: Empowering your existing team with AI-driven insights.
- Sensor-Agnostic: Maximising flexibility and leveraging existing predictive maintenance equipment.
- From Install to Insight in Under 30 Minutes per Asset: Ensuring rapid deployment and quick value realisation.
- Sensor + Software Bundled in One Subscription: Providing transparent and predictable pricing.
- Designed for the Team on the Tools: Ensuring high adoption and practical utility on the factory floor.
- Built by Engineers Who’ve Worked on the Plant Floor: Bringing real-world experience to the solution.
- More Than Predictive – A Full Reliability Platform: Offering integrated CMMS capabilities, maintenance planning and scheduling software, and asset health monitoring for holistic operational excellence.
Don't let the complexities of procurement deter you from unlocking the immense benefits of machine learning in manufacturing and advanced condition monitoring systems. With a strategic approach and the right partner, your factory can achieve unparalleled levels of reliability and efficiency.
Ready to make an informed decision and invest in the future of your manufacturing operations?
Book a demo with us today to see how Factory AI can guide you through the buying process and deliver the best predictive maintenance software solution tailored for your manufacturing facility.
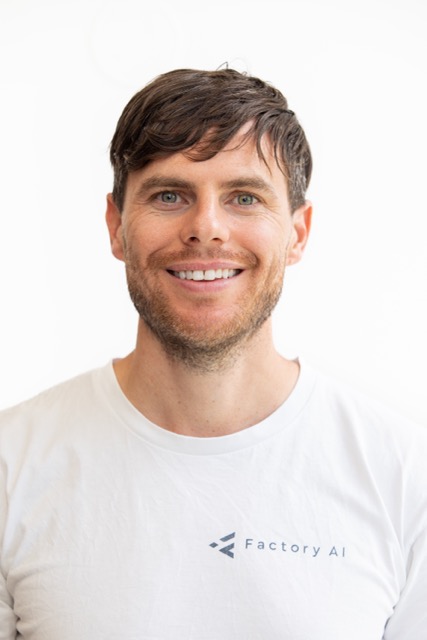