How Reliability Engineers Can Benefit from Software
Jun 7, 2024
Predictive Maintenance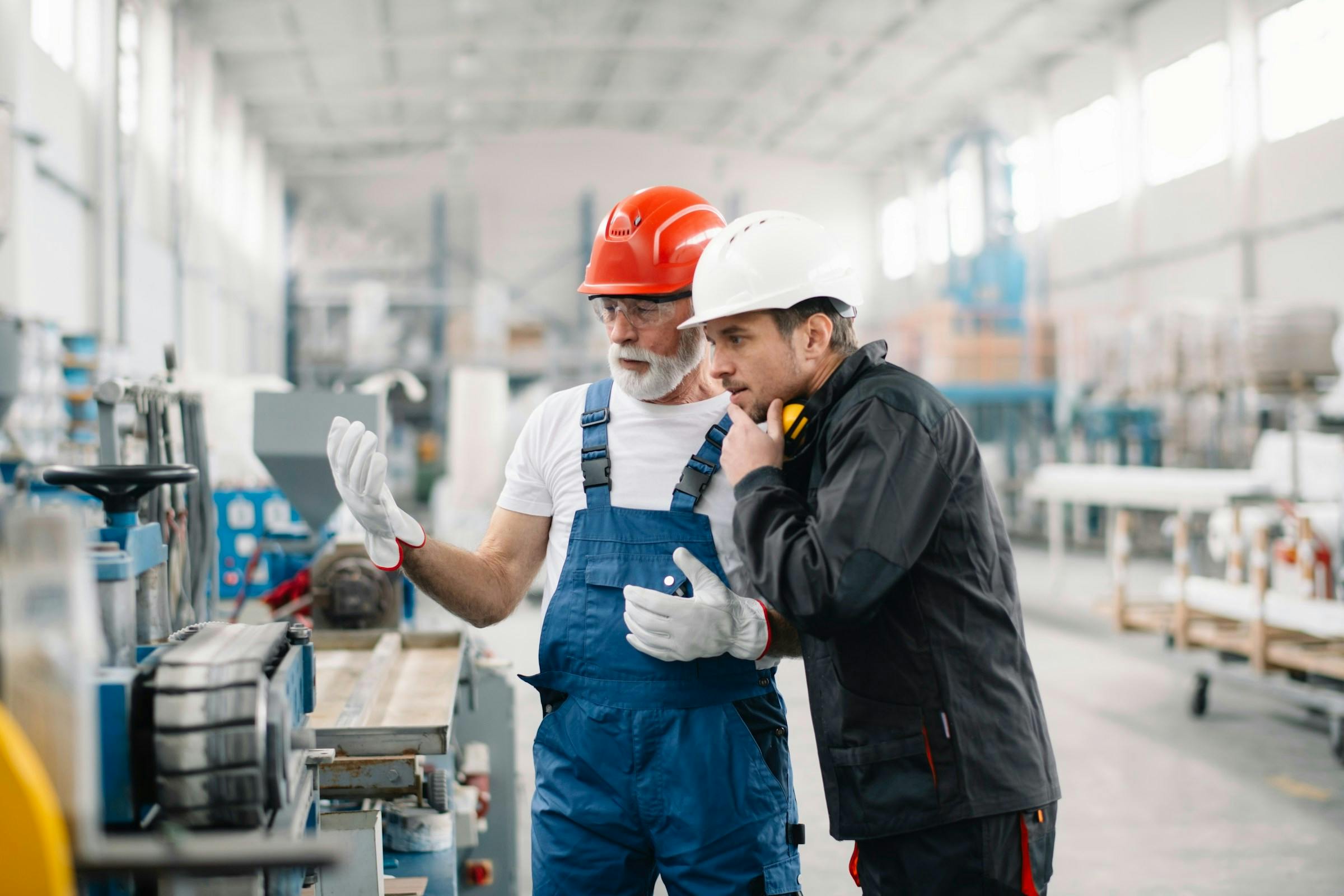
Introduction
In her book ‘Free Time’, author Jenny Blake addresses one of the biggest problems for modern workers: the burden of busywork. The average knowledge worker today spends so much time on admin tasks, meetings, and emails that the feeling of ‘truly getting things done that matter’ can be elusive.
Although Blake's book was written with small business owners in mind, its principles are just as relevant to site leaders, managers, and engineers. At Factory AI, we often discuss work productivity with our customers. We ask reliability engineers how much time they spend behind a desk versus on the factory floor, and if they could, how they would change this proportion.
A common answer is that they would prefer to spend more time at their desks working on future projects with a broad impact, rather than dealing with today’s emergencies or responding to emails about maintenance store labels.
Enter: Slow Productivity
Jenny Blake’s book is part of the wider Slow Productivity movement, which I’m a big fan of. Currently, I’m reading Cal Newport’s book on the topic. The strategies offered in these books can make a significant difference over time.
Cal Newport offers strategies such as:
- Putting tasks on autopilot: This involves booking recurring calendar slots weekly to do the same tasks at the same time. Newport suggests combining these with a ritual you enjoy, such as getting coffee from the same shop each time.
- Synchro meetings: These are weekly recurring meetings with your team to handle admin tasks, potentially eliminating many asynchronous emails and Slack messages. During these sessions, your team works through tasks requiring collaboration or clarification, using a shared document to keep track.
- Avoid task engines: Choose projects based on the admin work they generate. Newport shares a story about a sales leader choosing between organizing a conference and writing a detailed report. While the conference seems like the easier choice, the report generates fewer follow-up tasks.
Perhaps this worker is already onboard with creating a nice ritual associated to deep work
Enter: Software
One surprising strategy in Newport’s book is spending money on software. He references Jenny Blake’s $2,400 monthly spend on premium productivity software like Calendly, Docusign, and Zoom.
“From the context of slow productivity, investments of this type make a lot of sense. The more you can tame the small commitments pulling at your attention, the more sustainably and effectively you can work on things that matter.”
In engineering, spending on software is sometimes undervalued. There's a mentality that hiring staff is always more productive than leveraging software. However, in an industry with a staff shortage and continuously improving software, this mentality might need to change.
What Does This Have to Do with Reliability?
Here’s an exercise to determine the value you're getting (or not getting) from software:
- Open an empty Excel spreadsheet.
- List the 5-10 pieces of software you use weekly.
- Create two columns: one for the time you spend using each software, and the second for the time the alternative option would take.For example, instead of using a CMMS, some sites use a shared Excel file for maintenance planning.For predictive maintenance software like Factory AI, the alternative might be quarterly visual asset inspections, taking 5-30 minutes per asset versus 2 minutes with the software.
- Calculate the time difference between the two columns. This number shows how much time you're saving with the software.
This exercise is a rough estimate but can help decide what’s worth keeping and what might need more investment. Some software benefits might not directly translate to time saved, requiring a different evaluation approach.
Conclusion
Today's reliability engineers likely spend too much time on tasks that don’t directly improve site reliability. This sentiment is shared by many of our customers and other reliability leaders.
We’re not claiming that our predictive maintenance software will solve all these problems. However, using software aligned with your core responsibilities—like equipment uptime, OEE, and availability—makes sense. Also, it might be easier to implement a predictive maintenance software (which helps you shift from reactive to proactive maintenance, saving time and improving equipment uptime) than many reliability engineers think.
If you want to learn more about predictive maintenance, here are some of our previous articles that might help:
- The Failure History Method for Predictive Maintenance ROI Calculation: A quick way to estimate the value of predictive maintenance software.
- 3 Quick Steps to Find Out if PdM Makes Sense for You: Another strategy to evaluate the potential ROI of predictive maintenance software.
- Overloaded with PMs?: Insights into visual inspection PMs and how smart condition monitoring software can help.
- The First 10 Steps Roadmap of a Predictive Maintenance Pilot: A comprehensive guide to setting up a predictive maintenance pilot, often achievable without all 10 steps.
As always, we welcome your feedback.
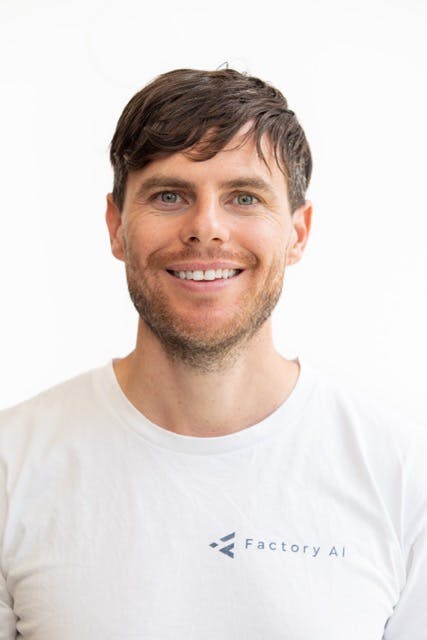
JP Picard
Jean-Philippe Picard is the CEO and Co-Founder of Factory AI. As a positive, transparent, and confident business development leader, he is passionate about helping industrial sites achieve tangible results by focusing on clean, accurate data and prioritizing quick wins. Jean-Philippe has a keen interest in how maintenance strategies evolve and believes in the importance of aligning current practices with a site’s future needs, especially with the increasing accessibility of predictive maintenance and AI. He understands the challenges of implementing new technologies, including addressing potential skills and culture gaps within organizations. Jean-Philippe is based in Sydney, New South Wales, Australia.