From Preventive to Predictive Conveyor Maintenance in the food and beverage industry
Jun 19, 2024
Predictive Maintenance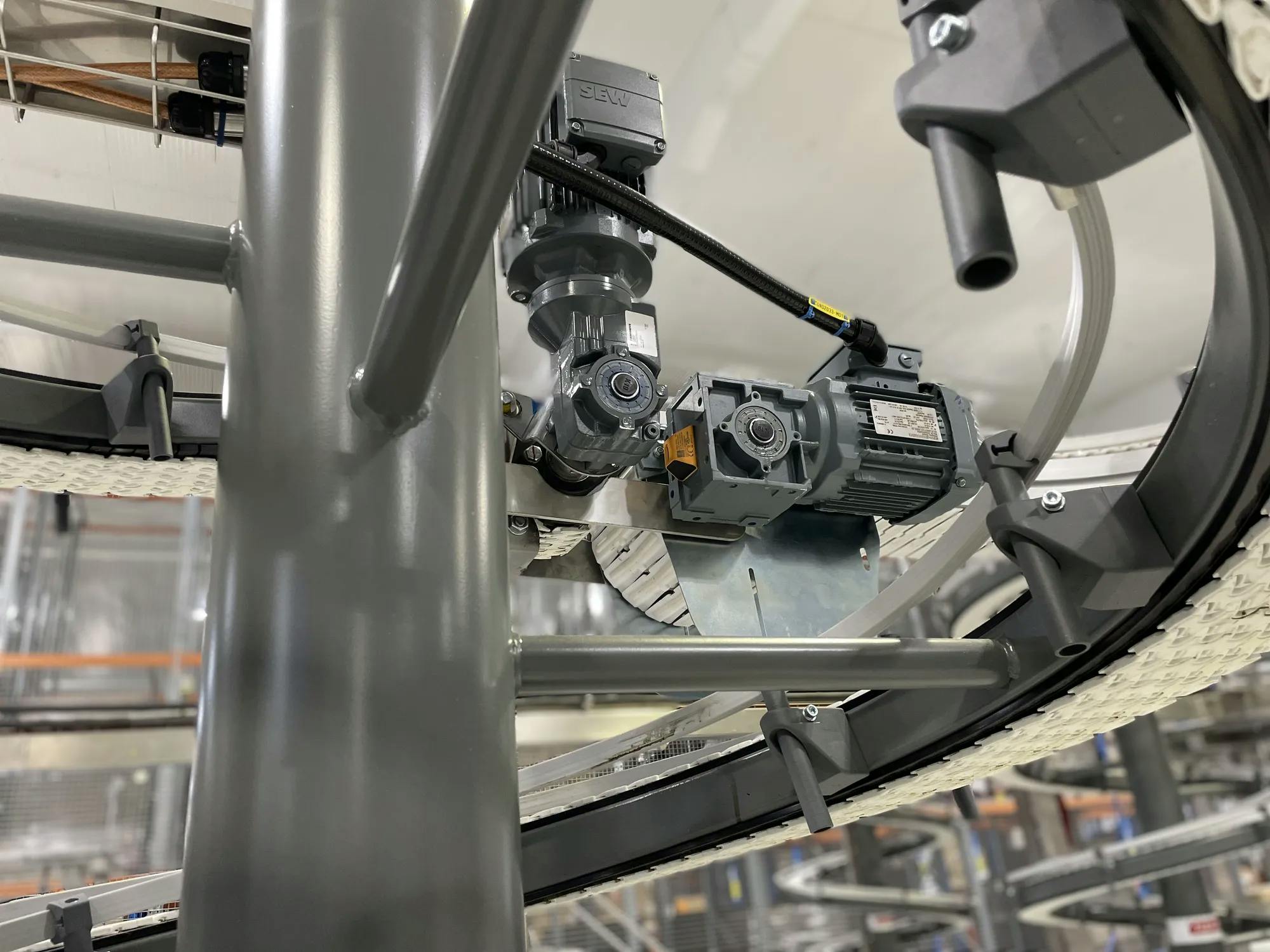
Introduction
While conveyor monitoring is common in heavy industries, it is far less prevalent in the food and beverage manufacturing sectors in Australia and New Zealand. In mining operations, conveyors that replace haul trucks to carry ore or coal to the process plant are critical and often expensive. In food and beverage production, they are often seen as mere transistors.
Typically, when we initiate conversations with prospective customers about transitioning from preventive maintenance to predictive maintenance, their thinking goes to either:
The site’s most critical and expensive assets that already receive a lot of attention.
The typical assets that lend themselves well to vibration and temperature monitoring, such as compressors, pumps, motors, turbines, boilers, heat exchangers, inverters, and mixers.
As we've explained in articles like "Is Asset Price a Good Metric for Predictive Maintenance Feasibility?"; when evaluating predictive maintenance feasibility, you should focus on asset criticality and potential production impact rather than asset price.
In this post, we discuss how smart condition monitoring can add significant value to our customers, particularly in the context of conveyors.
The Humble Conveyor Can Bring the Site to Its Knees
In most food and beverage sites, the conveyor framework is the foundation that moves parts from one expensive asset to the next. Even if your high-value equipment is performing well, a conveyor out of commission can halt operations.
Indeed, in many sites, the conveyor system is a single point of failure and can bring an entire line to unplanned downtime. Worse, some centralised conveyor systems, leading all lines to packaging or warehousing, can cause the entire site to experience unplanned downtime.
Why Do Conveyors Fail?
Conveyors often don’t receive the maintenance attention they deserve due to their very nature. In many sites, parts of the conveyor system are out of sight, out of reach (overhead), making maintenance harder, longer, and more expensive. This means maintenance is less likely to happen as often as it should.
Many sites also remain understaffed in reliability and maintenance, meaning the bigger-ticket assets typically get attention first, rarely focusing on conveyors.
This reality creates susceptibility to failure in conveyor systems. From our experience working with food and beverage sites in Australia, typically in the greater Melbourne, Sydney, or Brisbane regions, failures tend to fall into the following four categories:
- Belt or Chain Stretch: This manifests as fraying, damage, debris buildup, or extra slack in the belt or chain.
- Tracking: This occurs when conveyor belts are off track and become damaged, causing further damage to other parts.
- Bearings: Sometimes you can hear or feel excessive heat from a worn bearing before it fails, but often there are no warnings.
- Gear Motors: Gearbox noise or excessive heat from either the motor or the gearbox often signals trouble.
Where Can Predictive Maintenance Help With These Conveyor Failure Causes?
Predictive maintenance cannot solve all problems but can offer substantial ROI by addressing many issues. Let's examine how predictive maintenance can impact the four types of conveyor failures:
- Belt or Chain Stretch: Causes of chain stretch outside expected wear usually involve the pin. Chain stretch can quickly occur if the pin is bent, losing material due to friction, or too small due to chain hole widening. Recognising chain stretch signs is essential, but this isn't easy to capture with condition monitoring. A common method is to record a chain size measurement of the roller chain.
- Predictive Maintenance Feasibility: Low
- Tracking: If the conveyor belts are off track, they can quickly become damaged, which then causes damage to other parts. When tracking issues begin, the section of the conveyor system may vibrate more due to belt rubbing against the side structure, causing an upward trend in vibration signature. However, this depends on sensor placement and may not always be reliably captured.
- Predictive Maintenance Feasibility: Average
- Bearings: Technology can detect changes in bearings much better than a human can. Early detection of changes in bearing health is crucial as conveyors can go from unhealthy to failure quickly, sometimes in 2 weeks or a month. Vibration and temperature sensors on bearing blocks are effective here.
- Predictive Maintenance Feasibility: High
- Gear Motors: Gearbox noise or excessive heat from the motor or gearbox is a warning sign. In food and beverage production, gearboxes using food-grade lubricants are more susceptible to changes in operating conditions. Vibration and temperature sensors on gearboxes can highlight wear signs long before they cause trouble.
- Predictive Maintenance Feasibility: High
A Customer Story
Now, it’s all well good to talk in theory, and hopefully so far this has helped you categorised more about how predictive maintenance can help with conveyors. But let’s get specific here and share a customer win to make it all more tangible.
On June 12th, 2024, at 00:42 AM, our machine learning models picked up an anomaly on the drive on a conveyor at one of our customer’s sites. On the screenshot below you can see the asset page of this drive. With these smaller conveyor drives, often capturing vibration and temperature data through a single wireless sensor will be enough to help you reach an acceptable level of accuracy with predictive alerts, whilst also providing a low enough cost (~30$ per month of monitoring on many of our plans) to justify a very positive ROI.
A screenshot of what the asset page looks like highlighting the moment when the alert was issued.
As you can see in the picture above, the vibration signature seems healthy, showing the drive operating in line with production cycles. The alert was issued primarily on the back of the temperature. We can see a healthy temperature trend for the previous 2 months, and a sudden unexplained spike sending temperature 34% above healthy range (as indicated in red box).
Higher temperature in on these drives can often indicate bearing wear due. That could be due to increased friction from inadequate lubrication, misalignment, or surface defects. As bearings wear out, friction rises, generating more heat and causing the motor to work harder, reducing its efficiency and potentially leading to failure.
This customer in particular had been very proactive with their alerts, and acted quickly. Below you can read their response back to us. They found rotating looseness in the bearing due to wear. And this instances, and the majority of others, conducting corrective maintenance, whilst the asset is showing signs of wear, but not completely failed, proved to be much faster and much less costly to the site, saving them what they estimate at $11K thousand.
Conclusion
Out of the four common failure causes in conveyors, predictive maintenance is highly effective for two. This means you shouldn’t expect predictive maintenance to capture 100% of failures, but the ability to predict 15% to 50% of failures ahead of time typically outweighs the cost of installing such a system. As we saw in this above customer’s experience, only saving a few headaches every year will provide you with a very appealing ROI, forming part of a business case your leadership team is likely to accept as a great initiative.
We recommend you start your journey cost-effectively by monitoring the most critical components of your conveyors, such as motors, gearboxes, and important roller bearings. It's not necessary to monitor minor components like all idlers in a series configuration.
How You Can Get Started With Predictive Maintenance on Your Conveyors
To get started, identify problematic areas along your conveyor systems. If possible, download historical failure data from your CMMS, focusing on conveyor failures in the past 12 months. Calculate all costs associated with unplanned downtime from conveyors. For more details on this approach, you can read our blog post: The Failure History Method for Predictive Maintenance ROI Calculation.
Once you conclude that a predictive maintenance approach is viable, start by monitoring about 30 motors for a proof of concept. This will help you capture bearing and gearbox failures ahead of time. Monitoring for 90 days is a good starting point to understand the potential impact of predictive maintenance on your site’s conveyors.
If you want more details, feel free to book some time with us. We’ll share customer stories and how they’ve implemented this at their sites.
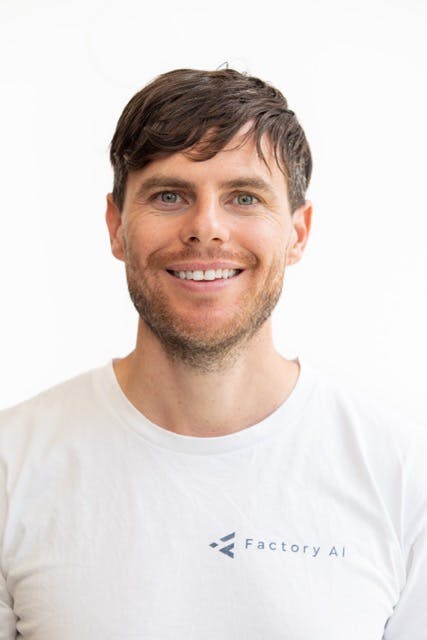
JP Picard
Jean-Philippe Picard is the CEO and Co-Founder of Factory AI. As a positive, transparent, and confident business development leader, he is passionate about helping industrial sites achieve tangible results by focusing on clean, accurate data and prioritizing quick wins. Jean-Philippe has a keen interest in how maintenance strategies evolve and believes in the importance of aligning current practices with a site’s future needs, especially with the increasing accessibility of predictive maintenance and AI. He understands the challenges of implementing new technologies, including addressing potential skills and culture gaps within organizations.