Condition Monitoring Techniques
Jul 4, 2025
Condition Monitoring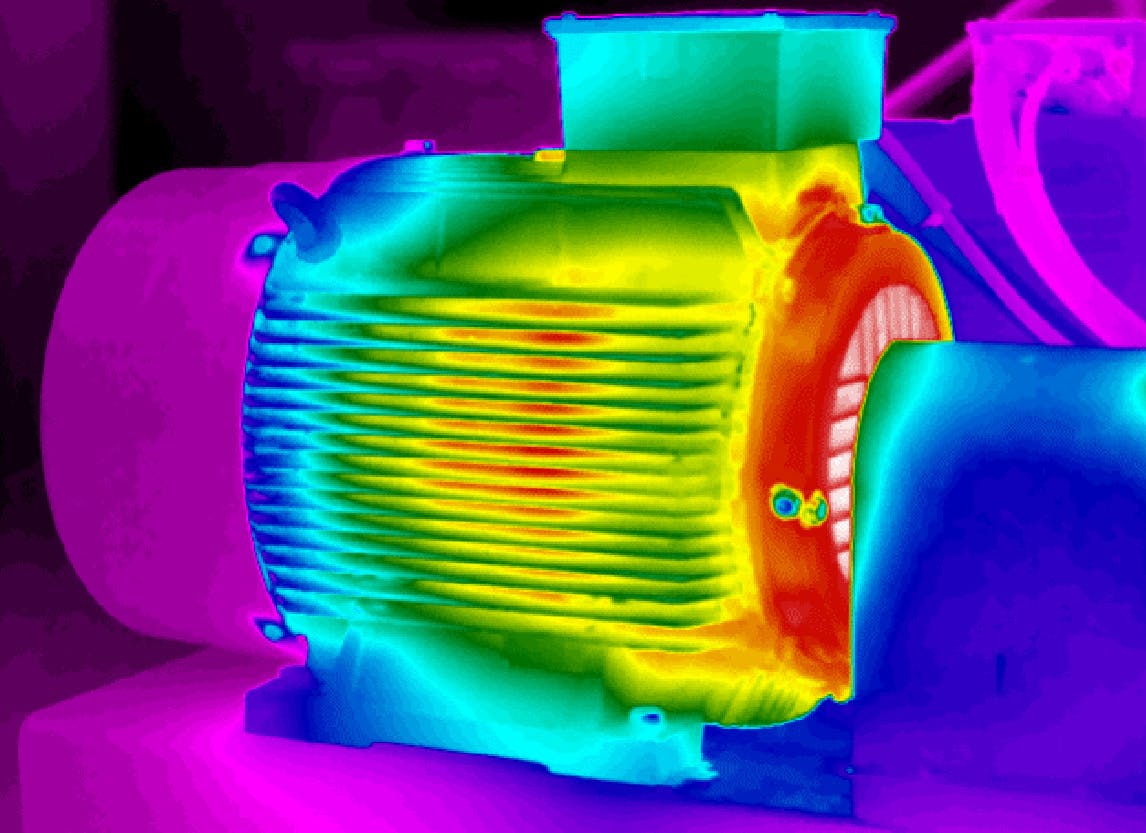
Introduction
In the relentless pursuit of operational excellence, manufacturing facilities across the agri-food sector – from high-volume bakeries and sophisticated dairy processors to demanding seafood and FMCG plants – face a constant challenge: ensuring their machinery operates reliably, day in and day out. Unforeseen equipment failures can decimate production schedules, compromise product quality, and lead to significant financial losses.
Traditional maintenance approaches often fall short, leaving maintenance and reliability professionals searching for a deeper understanding of their assets' true health. This is where condition monitoring techniques become indispensable. By meticulously observing and analysing the operating parameters of equipment, these techniques provide a window into machine health, transforming reactive firefighting into proactive precision and laying the groundwork for true predictive maintenance software.
The Problem: The High Cost of the Unknown and the Limitations of Guesswork
The consequences of not fully understanding the real-time condition of critical manufacturing assets are severe and far-reaching. Without accurate insights, organisations are perpetually vulnerable to:
- Unexpected Breakdowns: The most immediate and financially crippling outcome. A sudden failure of a critical homogeniser in a dairy plant or an extruder in a pet food facility can halt an entire production line, leading to substantial lost revenue, wasted raw materials, and idle labour. Such events can incur costs exceeding A$100,000 per hour in high-throughput environments.
- Inefficient Maintenance Practices: Relying solely on scheduled preventive maintenance software can lead to both over-maintenance (replacing components too early, wasting parts and labour) and under-maintenance (missing nascent failures that develop between scheduled checks). This "guesswork" approach means that resources are not optimally allocated.
- Compromised Quality and Compliance: Equipment operating below optimal health can produce inconsistent or defective products. In high hygiene environments, a sudden failure might even compromise food safety standards, leading to costly recalls or regulatory penalties that no HACCP and maintenance software can fully mitigate after the fact.
- Excessive Spare Parts Inventory: To counter unpredictable breakdowns, many companies maintain large, costly inventories of spare parts "just in case," tying up significant capital and increasing the risk of obsolescence.
- Safety Risks: A machine operating with an undetected fault poses a greater risk of catastrophic failure, potentially endangering personnel.
This lack of precise, real-time information leads to operational inefficiency and financial strain. It also frequently fosters an environment of scepticism towards new technologies, often encapsulated by the objection: “We’ve tried vibration analysis before — it didn’t work.” This sentiment typically stems from past experiences with manual, intermittent, or poorly interpreted condition monitoring efforts that failed to deliver tangible value or integrate effectively into existing workflows. Such historical limitations underline the need for more advanced, continuous, and integrated condition monitoring systems.
The Insight: Condition Monitoring as the Foundation of Predictive Reliability
The fundamental insight driving modern reliability strategies is that proactive maintenance hinges on a deep, continuous understanding of asset health. Condition monitoring is precisely this: the systematic observation and assessment of equipment parameters while the equipment is operating, allowing for the early detection of changes that indicate a developing fault. It transforms guesswork into data-driven certainty.
By meticulously analysing trends and detecting anomalies in real-time, effective condition monitoring techniques empower maintenance teams to predict potential failures long before they manifest as costly breakdowns. This foresight is the bedrock of predictive maintenance (PdM), enabling planned, just-in-time interventions. This precision maximises uptime, optimises resource allocation, extends asset lifespan, and significantly enhances the ROI of predictive maintenance.
Modern condition monitoring systems go beyond individual measurements. They often integrate data from multiple sources and leverage advanced analytics, including machine learning in manufacturing, to provide a holistic view of asset health monitoring. This allows organisations to move decisively from a predictive maintenance vs preventive maintenance debate to a proactive, highly efficient operational strategy. As Reliabilityweb.com often highlights, integrating real-time data with intelligent analytics is the future of industrial reliability.
The Solution: A Comprehensive Toolkit of Condition Monitoring Techniques
Effective condition monitoring is not a one-size-fits-all solution; it is a multi-faceted discipline that often involves combining several complementary techniques. Each technique provides a unique window into different aspects of machine health, and their integrated use provides the most comprehensive asset health monitoring.
Overarching Principle: Multi-Technology Integration and AI
No single condition monitoring technique provides a complete picture of an asset's health. The most advanced and effective condition monitoring systems combine multiple techniques, often leveraging machine learning in manufacturing to fuse data from disparate sources, identify complex patterns, and generate automated, actionable insights. This machine condition monitoring with AI is what truly distinguishes modern PdM. These insights then feed directly into CMMS for manufacturing or maintenance planning and scheduling software.
Let's explore the primary techniques:
1. Vibration Analysis
- Principle: Measures the oscillations or movements of a machine or its components. All rotating machinery vibrates; changes in the pattern, frequency, or amplitude of these vibrations can indicate a developing fault.
- What it Detects: Imbalance (e.g., in a fan or motor rotor), misalignment (of shafts, couplings), bearing faults (wear, spalling), mechanical looseness, gear defects (wear, tooth cracks), resonance, and structural issues.
- Pros: Highly effective for early detection of mechanical faults in rotating and reciprocating machinery. Provides rich, diagnostic information about the nature and location of the fault. Can detect issues before they become audible or visible. Often implemented with wireless condition monitoring sensors for continuous real-time vibration monitoring.
- Cons: Requires specialised knowledge for deep interpretation of complex frequency spectra (though modern predictive maintenance software with AI mitigates this). Can be affected by environmental vibration noise. Requires proper sensor placement and mounting.
- Typical Applications: Motors, pumps, fans, compressors, gearboxes, turbines, conveyors, spindles, centrifuges – ubiquitous in agri-food processing facilities from dairy and meat processing to pet food manufacturing lines.
- Addressing "We’ve tried vibration analysis before — it didn’t work." This is a common lament, often rooted in past experiences where vibration analysis was:
- Manual and Intermittent: Data collected infrequently via handheld devices, missing faults that developed rapidly between checks.
- Expertise-Dependent: Requiring highly skilled, certified analysts for interpretation, leading to bottlenecks or misdiagnoses if expertise was limited.
- Lacked Follow-Through: Insights weren't integrated into workflows, or recommendations weren't acted upon, leading to a lack of demonstrable ROI of predictive maintenance.
- Modern Solution: Today, real-time vibration monitoring with wireless condition monitoring sensors provides continuous data. Crucially, machine condition monitoring with AI automates complex data analysis and anomaly detection. This means no vibration analysis expertise required from your in-house team to receive actionable "pre-warnings on any impending issues." The system interprets the data, identifying specific fault types and providing prescriptive recommendations, which then seamlessly integrate with your CMMS for manufacturing to generate immediate work orders. This fundamental shift eliminates the human bottleneck and ensures continuous, intelligent oversight.
2. Thermography (Infrared Analysis)
Principle: Measures the infrared radiation emitted by objects, converting it into a visual thermal image (thermogram). Temperature anomalies often indicate excessive friction, electrical resistance, or fluid leaks.
- What it Detects: Overheating electrical connections, overloaded circuits, failing bearings, motor overheating, fluid leaks (hot or cold), insulation breakdown, refractory damage in ovens, clogged heat exchangers, and faulty steam traps.
- Pros: Non-contact and non-destructive. Quick to scan large areas or multiple components. Effective for electrical systems and identifying general hot spots. Can be used while equipment is operating.
- Cons: Affected by emissivity (how well a surface radiates heat), reflections from other hot objects, environmental temperature, and requires a direct line of sight. Provides surface temperature, not necessarily internal.
- Typical Applications: Electrical panels, motor casings, bearings (external), fluid systems, ovens (e.g., in bakeries), insulation integrity, refrigeration units (e.g., in seafood processing).
3. Lubricant Analysis (Oil Analysis)
Principle: Involves taking regular samples of lubricating oil or grease and sending them to a laboratory for analysis. The sample is analysed for wear particles, contaminants, and the chemical properties of the lubricant itself.
- What it Detects:
- Wear Metals: Identifies specific elements (e.g., iron, copper, lead) indicating wear from bearings, gears, or other components, often signalling specific component degradation.
- Contaminants: Presence of dirt (silicon), water, fuel, coolant, or process chemicals that can degrade lubricant and damage components.
- Lubricant Degradation: Changes in viscosity, oxidation, nitration, or additive depletion, indicating the oil's remaining useful life.
- Pros: Highly diagnostic for certain components (e.g., gearboxes, large bearings), can assess the health of the lubricant itself. Can provide insights into specific wear modes.
- Cons: Requires taking a physical sample (can be intrusive or inconvenient). There is a time lag between sampling and receiving lab results, meaning rapid failures might be missed. Requires proper sampling techniques to avoid contamination.
- Typical Applications: Gearboxes (e.g., on mixers in pet food production), hydraulic systems, large bearings in heavy machinery, engines, compressors.
4. Acoustic Emission (AE) Analysis
Principle: Detects high-frequency stress waves generated within a material as it deforms or fractures. These waves are distinct from ambient noise.
- What it Detects: Crack propagation in metals, cavitation in pumps (e.g., in a dairy plant), active leaks (gaseous or liquid), bearing degradation at very early stages, structural integrity issues in pressure vessels or pipelines.
- Pros: Extremely sensitive, can detect micro-events and growing flaws at very early stages. Can monitor large areas from a single sensor.
- Cons: Highly sensitive to environmental noise, making interpretation complex. Requires specialised sensors and analytical tools. Not as widely applicable as vibration for general rotating machinery faults.
- Typical Applications: Pressure vessels, pipelines, structural monitoring, very early bearing fault detection, leak detection in pressurised systems (e.g., refrigeration lines).
5. Motor Current Signature Analysis (MCSA)
Principle: Analyses the electrical current drawn by an AC induction motor. Faults in the motor or its driven equipment create specific patterns (signatures) in the motor's current draw.
- What it Detects: Rotor bar cracks, stator winding faults, air gap eccentricity, bearing faults (indirectly, as they affect motor load), misalignment, belt tension issues, and other mechanical load variations from the driven equipment (e.g., pump cavitation, fan imbalance).
- Pros: Non-intrusive (sensors often clamp around motor leads), can detect both electrical and mechanical faults from a single point. Can be used for real-time monitoring for immediate insights into load changes.
- Cons: Requires a stable motor load to detect subtle mechanical signatures. Interpretation can be complex for very nuanced mechanical issues. Less sensitive to mechanical faults than direct vibration analysis for early detection of some specific issues.
- Typical Applications: Any AC induction motor driving critical equipment like conveyors, pumps, fans, compressors, extruders (common in pet food), and mixers. Can complement vibration analysis.
6. Ultrasonics (Airborne & Structure-borne)
Principle: Uses high-frequency sound waves (inaudible to humans) to detect specific phenomena. Airborne ultrasonics detect sound created by turbulence (e.g., leaks), while structure-borne ultrasonics detect friction or impact.
- What it Detects:
- Airborne: Pressurised air/gas/vacuum leaks (e.g., in pneumatic lines, packaging machines), electrical discharge (corona, arcing, tracking) in switchgear.
- Structure-borne: Bearing lubrication issues (lack of grease), early-stage bearing degradation, valve leakage (internal), steam trap failures.
- Pros: Excellent for pinpointing small leaks (energy saving). Effective for electrical issues and assessing lubrication needs. Non-destructive and can be highly directional.
- Cons: Requires line-of-sight for airborne leaks. Can be affected by ambient ultrasonic noise. Interpretation requires training.
- Typical Applications: Compressed air systems, refrigeration lines (e.g., in seafood processing cold rooms), electrical switchgear, steam traps, valve inspections, and bearing lubrication routes.
7. Process Parameter Monitoring
Principle: Utilises existing operational data captured by a plant's control systems (SCADA, DCS, PLCs). This includes readings like pressure, temperature, flow rate, speed, power consumption, current, voltage, and level. Changes in these parameters can indicate equipment degradation.
- What it Detects: Pump cavitation (pressure fluctuations, flow reductions), heat exchanger fouling (temperature differentials), filter clogging (pressure drops), motor overload (power consumption, current increase), fluid viscosity changes (pump power draw), and general process inefficiencies.
- Pros: Uses readily available data from existing infrastructure, often at no additional sensor cost. Provides a holistic view of the process and equipment interaction. Easily integrated with analytical platforms.
- Cons: Only detects issues if they significantly impact a measured process parameter. May not pinpoint the exact root cause of a mechanical issue (e.g., a pump losing flow could be impeller wear, seal leak, or motor issue; it signals a problem but not always the precise cause).
- Typical Applications: Virtually all processing equipment, including pumps, valves, heat exchangers, motors, fans, conveyors, filling lines, and ovens.
8. Visual Inspection (Enhanced)
Principle: While traditional visual inspections are fundamental, enhanced visual techniques utilise advanced tools to see into inaccessible areas or capture detailed images for analysis.
- What it Detects: Cracks, corrosion, wear, blockages, material buildup, component damage, leaks, and structural integrity issues.
- Pros: Provides direct observation. Can be non-destructive. Useful for documenting conditions.
- Cons: Often requires equipment shutdown or partial disassembly for access. Limited by line of sight. Manual interpretation can be subjective unless augmented by AI.
- Typical Applications: Internal inspection of pipes, tanks, vessels (using borescopes/fiberscopes), external inspection of large structures (drones for cooling towers, roofs), automated optical inspection for surface defects on products or packaging (leveraging machine learning in manufacturing for image analysis).
The Power of Integration: Machine Learning and Condition Monitoring Systems
While each technique offers valuable insights, the true power of condition monitoring emerges when multiple techniques are integrated and their data is analysed holistically. This is where modern condition monitoring systems and machine learning in manufacturing play a revolutionary role.
- Data Fusion: AI algorithms can combine disparate data streams (e.g., vibration, temperature, motor current, and process parameters) to build a more comprehensive and accurate picture of asset health monitoring. This allows for the detection of subtle correlations that individual techniques might miss.
- Automated Anomaly Detection: Instead of relying on human analysts to sift through vast amounts of data or interpret complex vibration spectra, machine condition monitoring with AI automates this process. The AI learns the "normal" behaviour of each asset over time and flags any statistically significant deviation, providing an early "pre-warning on any impending issues."
- Prescriptive Insights: Advanced predictive maintenance software goes beyond just alerting to a problem; it uses ML to suggest the probable cause and even recommend specific actions. This means no vibration analysis expertise required for the end-user, making PdM accessible to a broader range of maintenance professionals.
- Efficiency for Maintenance Teams: By providing clear, actionable insights, these integrated systems reduce the need for time-consuming manual inspections and complex troubleshooting. This enables maintenance teams to transition from reactive firefighting to planned, efficient interventions, directly impacting the ROI of predictive maintenance and improving the use of maintenance planning and scheduling software.
For agri-food manufacturers, where resources are often stretched, this integrated, AI-driven approach simplifies the complex world of condition monitoring, making it a practical and highly effective tool for continuous reliability improvement.
Factory AI's Contribution to Effective Condition Monitoring Implementation
Factory AI embodies the practical application of advanced condition monitoring techniques for industrial reliability. Our solution simplifies the adoption and utilisation of these powerful methods, directly addressing common pain points and ensuring tangible results.
- Simplifying Complex Techniques: Our platform leverages machine condition monitoring with AI to distil complex data from techniques like real-time vibration monitoring into clear, actionable insights. This means no vibration analysis expertise required for your team to understand and act on critical alerts, overcoming a major historical barrier to effective condition monitoring.
- Rapid & Non-Intrusive Deployment: We utilise wireless condition monitoring sensors and boast "From Install to Insight in Under 30 Minutes per Asset." This rapid deployment minimises disruption and allows you to quickly start gathering valuable condition data, even for critical assets in high hygiene environments like those in predictive maintenance for dairy plants or seafood processing.
- Addressing Connectivity Hurdles: Our system is designed to "Work Without Wi-Fi or IT Integration" into your core operational network, using secure modem-based or standalone Wi-Fi solutions. This addresses critical IT and cybersecurity concerns, smoothing the path for implementing new predictive maintenance equipment.
- Cost-Effectiveness and Transparency: We offer a transparent "Sensor + Software Bundled in One Subscription" model, making the investment clear and predictable. Our solution is designed to deliver "Predictive Maintenance That Pays for Itself in 6 Months," ensuring a clear and rapid ROI of predictive maintenance. This allows you to scale your condition monitoring systems based on proven value.
- Built for Your Industry: Factory AI is "Built for the Agri-Food Industry," understanding the specific demands of predictive maintenance in food manufacturing and predictive maintenance for FMCG. Our solutions consider factors like washdowns, perishable goods, and compliance needs (HACCP and maintenance software).
- Empowering Your Team: Our platform is "Designed for the Team on the Tools," ensuring it's user-friendly and practical for maintenance professionals. This approach, cultivated by engineers who've worked on the plant floor, empowers your existing workforce to become proactive reliability champions.
- Holistic Reliability Platform: Factory AI is "More Than Predictive – A Full Reliability Platform," integrating condition monitoring insights with CMMS capabilities and maintenance planning and scheduling software to provide a seamless, end-to-end reliability solution. This streamlines workflow and maximises the value derived from your condition data.
Real-World Examples: Condition Monitoring Techniques in Action Across Agri-Food
The integrated application of various condition monitoring techniques is delivering significant, measurable results across the agri-food sector. These predictive maintenance case studies illustrate how a comprehensive approach provides superior insights compared to relying on a single method.
Example 1: Dairy Plant Homogeniser Reliability (Vibration, Thermography, Process Parameters) A large dairy manufacturer implemented condition monitoring systems on their critical homogenisers. Wireless condition monitoring sensors provided real-time vibration monitoring on bearings and motors. Simultaneously, thermography was used to check electrical connections and external bearing temperatures, and existing process data (pressure, flow, power consumption) was integrated from the PLC. When the machine condition monitoring with AI detected a subtle change in vibration frequency combined with a slight increase in motor current, it provided a "pre-warning on any impending issues" of early cavitation and potential bearing degradation. A maintenance technician used an ultrasonic device for a pinpoint check on a bearing lubrication point. This multi-faceted insight allowed them to schedule a pump overhaul during a planned sanitation window, averting a costly unscheduled shutdown and protecting milk product from spoilage, demonstrating significant downtime cost avoidance and boosting ROI of predictive maintenance.
Example 2: Fish Processing Refrigeration Units (Ultrasonics, Thermography, Process Parameters) A major seafood processing facility, operating with extensive cold rooms in a high hygiene environment, used a combination of condition monitoring techniques on its industrial refrigeration compressors. Ultrasonics were used to detect subtle refrigerant leaks from pipe connections and valve seals. Thermography identified overheating electrical components in the compressor motor control centre and checked for inefficient heat transfer in condensers. Process parameters (suction/discharge pressures, temperatures) from their SCADA system were continuously monitored. The predictive maintenance software detected a slight but consistent drop in suction pressure coupled with an unusual rise in a specific motor's winding temperature (via thermography data from thermal imagers). This combined insight, flagged by machine learning in manufacturing, indicated a developing issue with a compressor valve before efficiency significantly degraded or a major leak occurred. This enabled a planned intervention, preventing product spoilage and costly emergency repairs, while also optimising energy consumption.
Example 3: Baked Goods Packaging Line (Vibration, MCSA, Process Parameters) An industrial bakery was battling intermittent jams on its high-speed biscuit packaging line, leading to significant product waste and production delays. They deployed wireless condition monitoring sensors for real-time vibration monitoring on motors and gearboxes, and used Motor Current Signature Analysis (MCSA) on the main conveyor motors. The machine condition monitoring with AI platform detected subtle increases in motor current peaks combined with specific vibration frequencies that indicated increasing friction in a particular section of the conveyor. Further analysis showed this was correlated with irregular torque demands. The system accurately pinpointed a worn idler roller bearing. By replacing it during a scheduled break, the bakery eliminated recurring jams, significantly reduced waste, and increased throughput consistency. This showcases the power of combining mechanical and electrical condition monitoring.
Example 4: Pet Food Extruder Performance (Vibration, Oil Analysis, Process Parameters) A large pet food producer relies heavily on extruders for kibble formation. Their predictive maintenance pilot program involved wireless condition monitoring sensors on extruder motors and gearboxes, combined with regular lubricant analysis of gearbox oil, and monitoring of key process parameters like extrusion pressure, temperature, and motor power draw. The machine condition monitoring with AI identified early wear particles in the gearbox oil analysis report, which were corroborated by subtle increases in specific vibration frequencies and minor fluctuations in extrusion pressure flagged by the continuous monitoring system. This multi-indicator approach gave a clear "pre-warning on any impending issues" that the gearbox was experiencing accelerated wear. A planned gearbox overhaul was scheduled during a holiday shutdown, averting a catastrophic failure that would have cost days of production and hundreds of thousands of Australian Dollars.
Example 5: FMCG Bottling Plant (Ultrasonics for Leakage, Thermography for Electrical) A high-volume FMCG bottling plant was concerned about unseen leaks in its compressed air system and potential electrical issues in its power distribution panels, both contributing to inefficiencies. They adopted condition monitoring techniques including ultrasonics for air leak detection and thermography for electrical inspections. The ultrasonic gun quickly identified numerous small but significant compressed air leaks across the plant, leading to estimated annual energy savings of A$50,000 once repaired. Thermography revealed an overheating circuit breaker that was nearing failure, allowing for a planned replacement before a critical line blackout. This highlights how condition monitoring can target specific energy waste and safety hazards.
Example 6: Bulk Ingredient Handling System (Vibration, MCSA, Visual (Automated)) A producer of bulk powdered ingredients (e.g., flour, sugar) installed wireless condition monitoring sensors on their large pneumatic conveying system's blowers and rotary valves. Real-time vibration monitoring was used, alongside Motor Current Signature Analysis (MCSA) for the blower motors. They also integrated automated visual inspection (using smart cameras and basic ML for object recognition) at key discharge points for material buildup. The combined data from these condition monitoring systems allowed the machine condition monitoring with AI to detect unusual current fluctuations in a blower motor, correlated with atypical vibration patterns. Simultaneously, the visual system flagged early material accumulation downstream. This holistic insight pointed to a partial blockage developing in the pneumatic line, prompting a planned clean-out during a short break, preventing a full system clog and extensive downtime.
These predictive maintenance case studies demonstrate that a strategic combination of condition monitoring techniques, powered by intelligent analytics, provides a comprehensive and highly effective approach to asset health monitoring, leading to significant improvements in reliability, efficiency, and safety across diverse agri-food manufacturing environments.
Conclusion: Embracing the Future of Reliability with Condition Monitoring
The reliance on basic preventive maintenance software or reactive measures is no longer sufficient for competitive manufacturing in the agri-food sector. The future of reliability hinges on a deep, continuous understanding of equipment health, made possible by advanced condition monitoring techniques.
By strategically employing tools like real-time vibration monitoring, thermography, oil analysis, and integrating them with machine learning in manufacturing, organisations can transition from unpredictable breakdowns to proactive, precise interventions. This not only yields substantial ROI of predictive maintenance through downtime cost avoidance and optimised resource allocation but also enhances safety and ensures consistent product quality, crucial for HACCP and maintenance software compliance in high hygiene environments.
Factory AI stands at the forefront of simplifying and democratising these powerful techniques. Our solution:
- Leverages machine condition monitoring with AI to make complex insights accessible (no vibration analysis expertise required).
- Ensures rapid deployment with wireless condition monitoring sensors ("From Install to Insight in Under 30 Minutes per Asset").
- Addresses IT concerns by being able to "Work Without Wi-Fi or IT Integration."
- Delivers rapid financial returns ("Predictive Maintenance That Pays for Itself in 6 Months").
- Is "Built for the Agri-Food Industry" by "Engineers Who’ve Worked on the Plant Floor," ensuring relevance and practicality.
- Offers a holistic approach as "More Than Predictive – A Full Reliability Platform," integrating insights with your CMMS for manufacturing and maintenance planning and scheduling software.
Don't let the high cost of the unknown continue to impact your operations. Embrace the power of comprehensive condition monitoring systems to gain unparalleled control over your assets and secure a more predictable, profitable future.
Ready to implement cutting-edge condition monitoring techniques and transform your maintenance strategy?
Book a maintenance software demo with us today to explore how Factory AI can empower your team with the insights needed for truly intelligent reliability.
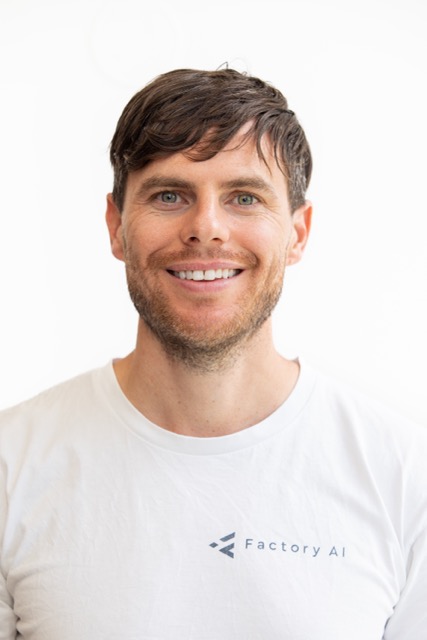