Building Maintenance Is No Longer a Cost Center. It's Your Biggest Competitive Advantage.
Jul 16, 2025
building maintenance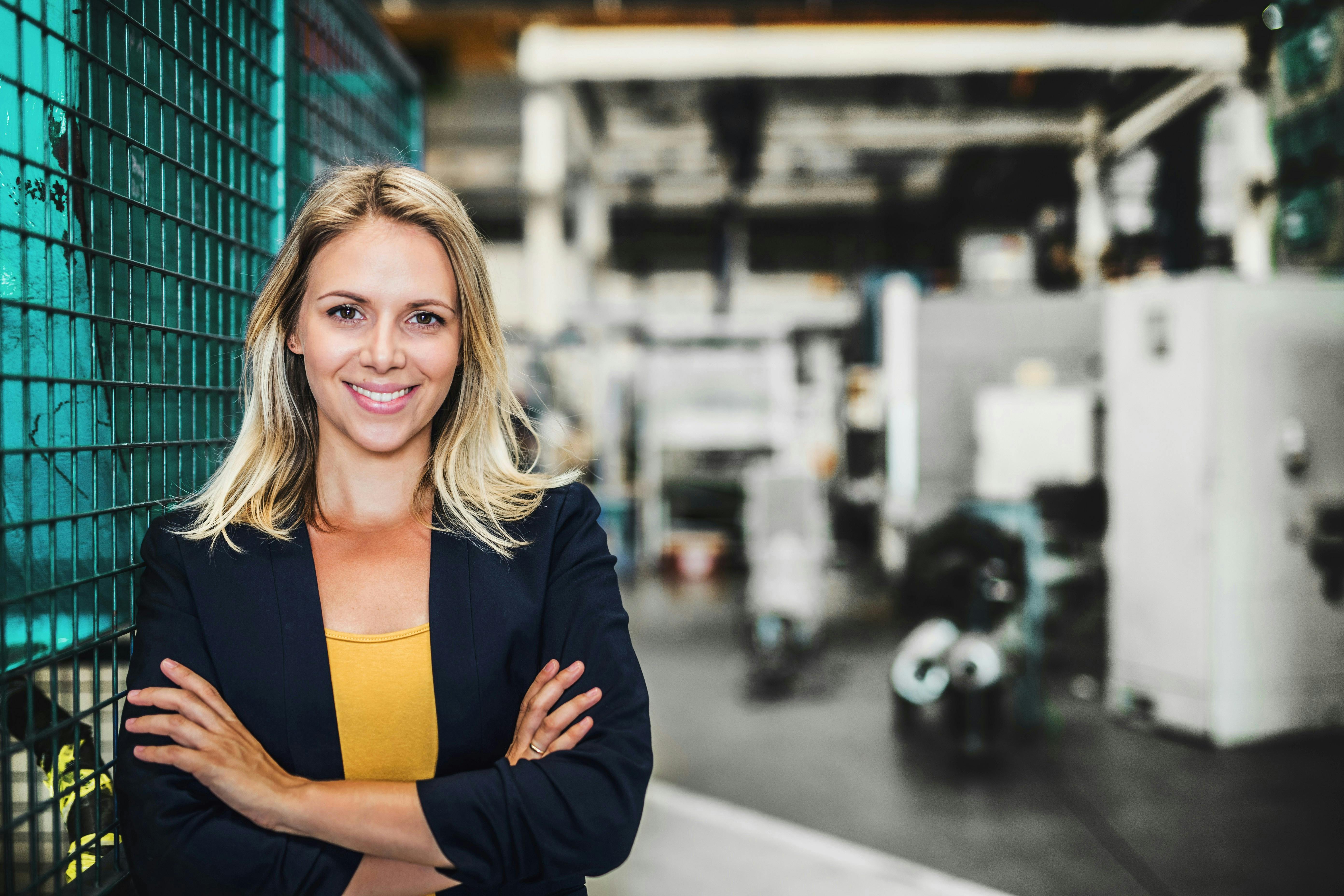
For decades, the hum of an HVAC unit, the flicker of a fluorescent light, or the silence of a production line was only noticed when it broke. Building maintenance was a reactive function—a cost center populated by heroes who rushed in to fix what was already broken. It was a necessary expense, a line item on a budget to be minimized.
In 2025, that mindset is not just outdated; it's a direct threat to your profitability, safety, and competitive standing.
The most forward-thinking organizations have undergone a radical paradigm shift. They no longer see building maintenance as a drain on resources. They see it for what it truly is: a powerful engine for strategic value creation. It's about transforming your physical assets from potential liabilities into high-performing drivers of operational excellence and financial return.
This is not another generic "What is building maintenance?" guide. This is a strategic playbook for facility operators, maintenance managers, and industrial decision-makers who are ready to stop fighting fires and start building a resilient, efficient, and profitable future. We will dissect the financial and strategic imperatives of modern maintenance, explore the technologies powering this revolution, and provide a concrete roadmap to implement a world-class program in your facility.
Beyond the Basics: Redefining Building Maintenance in 2025
The term "building maintenance" itself feels inadequate for the modern reality. It conjures images of janitorial services and simple repairs. While those are components, the true scope is far broader and more strategic.
From "Fixing Things" to "Strategic Asset Management"
The old model was simple: wait for an asset to fail, then dispatch a technician to fix it. The primary metric was speed of repair. The new model, Strategic Asset Management, is about maximizing the value of an asset throughout its entire lifecycle.
This means shifting focus from reactive metrics to proactive, value-driven Key Performance Indicators (KPIs):
- Overall Equipment Effectiveness (OEE): How much of your planned production time is truly productive?
- Asset Uptime: What percentage of time are your critical systems operational?
- Mean Time Between Failures (MTBF): Are your assets lasting longer between breakdowns?
- PM Compliance: Are you completing your scheduled preventive tasks on time?
- Total Cost of Ownership (TCO): What is the true cost of an asset from acquisition to disposal, including energy, maintenance, and downtime?
When you manage buildings through this lens, maintenance stops being an isolated department and becomes an integral partner to operations, finance, and executive leadership. Its success is directly tied to the overall success of the business.
The True Cost of Neglect: The Financial Iceberg of Deferred Maintenance
Deferred maintenance is the practice of postponing necessary repairs and maintenance tasks to save costs in the short term. It’s one of the most insidious financial traps a facility can fall into. What appears as a small saving on this quarter's budget becomes a catastrophic expense on a future balance sheet.
Think of it as a financial iceberg. The visible cost is the repair you postponed. The massive, hidden costs below the surface include:
- Accelerated Deterioration: A simple, inexpensive fix left undone can cause cascading failures in related components. Industry experts often cite the 1:4 rule of deferred maintenance: for every $1 of maintenance you defer today, you will spend at least $4 on reactive repairs in the future.
- Catastrophic Failure & Downtime: A neglected air handler doesn't just need a new belt; it seizes up entirely during a heatwave, shutting down a critical production area and costing tens of thousands per hour in lost revenue.
- Skyrocketing Energy Costs: A poorly maintained HVAC system can consume 30-50% more energy to achieve the same level of climate control. Dirty coils, clogged filters, and unbalanced systems are silent profit killers.
- Safety and Compliance Risks: A faulty fire suppression system or a corroded structural beam isn't just a maintenance issue; it's a major liability that can lead to fines, lawsuits, and tragic accidents.
- Decreased Asset Value: A well-maintained building commands a higher market value and is more attractive to tenants or buyers. A building with a significant deferred maintenance backlog is a financial albatross.
Deferring maintenance isn't saving money; it's taking out a high-interest loan from your future self, with your facility's operational integrity as collateral.
The Four Pillars of a Modern Building Maintenance Strategy
A successful maintenance strategy isn't about choosing one "best" approach. It's about intelligently blending four distinct types of maintenance, applying the right one to the right asset based on its criticality, cost, and failure impact.
Pillar 1: Reactive Maintenance (The Necessary Evil)
Also known as "run-to-failure," reactive maintenance is the practice of fixing assets only after they have broken down. While it sounds like the antithesis of a modern strategy, it has a limited and intentional place.
- When is it acceptable? For non-critical, low-cost, easily replaceable assets. Think of a lightbulb in a storage closet or a small, non-essential office fan. The cost of performing preventive maintenance on such items would far exceed the cost of simply replacing them when they fail.
- The Danger Zone: The problem arises when reactive maintenance becomes the default strategy for all or most assets. A facility operating in a constant state of reaction suffers from unpredictable downtime, high overtime labor costs, expensive emergency parts procurement, and a perpetually stressed-out workforce. If more than 20% of your maintenance work is reactive, your strategy is fundamentally broken.
Pillar 2: Preventive Maintenance (The Foundation of Stability)
Preventive Maintenance (PM) is the cornerstone of any stable maintenance program. It involves performing scheduled maintenance tasks at regular intervals (time-based) or after a specific amount of usage (usage-based) to reduce the likelihood of failure.
This is where you move from chaos to control. Creating a robust preventive maintenance schedule is a non-negotiable first step toward operational excellence.
How to Build a Preventive Maintenance Program from Scratch:
- Create a Comprehensive Asset Inventory: You can't maintain what you don't know you have. Document every piece of maintainable equipment, from major HVAC chillers to smaller exhaust fans. Use a modern CMMS software to create a digital asset hierarchy.
- Conduct a Criticality Analysis: Not all assets are created equal. Rank each asset based on its impact on production, safety, and operational continuity. A 1-10 scale works well. A critical air compressor for a manufacturing line is a "10," while an office water cooler might be a "2." This analysis dictates where you focus your PM efforts.
- Gather Maintenance Requirements: For each critical asset, consult the Original Equipment Manufacturer (OEM) manuals. They provide the best starting point for PM tasks and frequencies. Supplement this with historical maintenance data and interviews with experienced technicians.
- Define Detailed PM Tasks & Checklists: Don't just write "Check Motor." Create a detailed, step-by-step procedure:
- Tools Required: Multimeter, grease gun, infrared thermometer.
- Safety Procedure: Lockout/Tagout (LOTO) power source.
- Step 1: Visually inspect for debris and corrosion.
- Step 2: Check and tighten electrical connections.
- Step 3: Measure motor amperage draw and record.
- Step 4: Lubricate bearings per specification. These detailed checklists ensure consistency and provide valuable data.
- Schedule and Automate: Input these tasks and their frequencies into your CMMS. The system will then automatically generate and assign work orders to your technicians, ensuring nothing falls through the cracks. The right work order software is crucial for tracking compliance and efficiency.
Pillar 3: Condition-Based Maintenance (CBM) (Listening to Your Assets)
While preventive maintenance is powerful, it can sometimes lead to over-maintenance. You might change a part that still has 50% of its useful life remaining, just because the schedule said so. Condition-Based Maintenance (CBM) is the next level of sophistication.
CBM uses real-time data to trigger maintenance only when it's actually needed. Instead of relying on a calendar, you rely on the actual condition of the asset.
Key CBM Technologies:
- Vibration Analysis: Used on rotating equipment like motors, pumps, and fans. Sensors detect subtle changes in vibration patterns that can indicate imbalances, misalignment, or bearing wear long before they become audible or cause failure.
- Infrared Thermography: Thermal cameras are used to detect hot spots in electrical panels, motors, and steam traps. A hot circuit breaker is a clear sign of a poor connection and an impending failure.
- Oil Analysis: Samples of lubricating oil from gearboxes or engines are sent to a lab. The analysis can reveal the presence of metal particles (indicating wear), coolant, or other contaminants, providing a detailed health report of the machine's internal components.
- Ultrasonic Analysis: High-frequency sound detectors can "hear" compressed air leaks, electrical arcing, and the early stages of bearing failure that are inaudible to the human ear.
CBM allows you to optimize your maintenance resources, performing work only when justified by data, which reduces unnecessary labor and parts costs.
Pillar 4: Predictive Maintenance (PdM) (The Future is Now)
If CBM is about listening to your assets, Predictive Maintenance (PdM) is about forecasting their future. This is the pinnacle of maintenance strategy in 2025, moving from detection to prediction.
PdM uses a continuous stream of data from IoT sensors, feeds it into machine learning algorithms, and predicts when a failure is likely to occur.
CBM vs. PdM: A Simple Analogy
- CBM: Your car's "Check Engine" light comes on. You know there's a problem right now.
- PdM: Your car's onboard computer analyzes engine performance data and tells you, "Based on current trends, your alternator has an 85% probability of failing in the next 500 miles."
This predictive capability is a game-changer. It allows you to schedule repairs with surgical precision, during planned downtime, with all necessary parts and labor ready. It eliminates unplanned downtime almost entirely. The power of AI predictive maintenance is what separates good maintenance teams from elite ones. It transforms the maintenance department from a repair crew into a team of data scientists and reliability engineers.
Building Your High-Performance Maintenance Tech Stack
Strategy is nothing without execution, and in 2025, execution is powered by technology. A modern maintenance tech stack is the central nervous system that enables the four pillars of maintenance.
The Central Nervous System: The Modern CMMS
A Computerized Maintenance Management System (CMMS) is the foundational software for any serious maintenance operation. Forget the clunky, server-based systems of the past. A modern CMMS is a cloud-based, mobile-first platform that serves as your single source of truth.
A robust CMMS should do more than just track work orders. It should be a strategic hub for:
- Asset Management: A complete digital record of every asset, its history, documentation, and cost.
- Work Order Management: Streamlining the entire lifecycle of a work request, from creation and assignment to completion and data capture.
- Preventive Maintenance Scheduling: Automating the generation of PMs to ensure 100% compliance.
- Inventory and Parts Management: Tracking spare parts, managing stock levels, and automating reordering to prevent stockouts for critical components.
- Reporting and Analytics: Providing dashboards and reports on KPIs like MTBF, MTTR, and wrench time, allowing you to make data-driven decisions.
The Eyes and Ears: IoT Sensors and Building Automation Systems (BAS)
To fuel Condition-Based and Predictive Maintenance, you need data. This is where the Internet of Things (IoT) and Building Automation Systems (BAS) come in.
- IoT Sensors: These are small, often wireless sensors that can be attached to almost any asset to monitor conditions like vibration, temperature, humidity, pressure, and current draw. The cost of these sensors has plummeted, making it feasible to deploy them across a wide range of equipment.
- Building Automation System (BAS): A BAS (or BMS - Building Management System) is a centralized system that controls and monitors a building's mechanical and electrical equipment, primarily HVAC, lighting, power, and security systems. Integrating your BAS with your CMMS is a massive force multiplier. When the BAS detects an alarm (e.g., a chiller's pressure is out of spec), it can automatically trigger a high-priority work order in the CMMS, complete with all relevant data, without any human intervention.
The Brain: AI and Machine Learning Platforms
This is the component that enables true Predictive Maintenance. AI and machine learning platforms ingest the massive datasets from your CMMS and IoT sensors. They identify normal operating patterns and detect subtle anomalies that precede failure. Over time, these algorithms learn the unique failure modes of your specific assets and can provide increasingly accurate failure predictions. Some advanced platforms even offer prescriptive maintenance, which not only predicts a failure but also recommends the specific corrective actions to take.
The Financial Case: Calculating the ROI of a Proactive Maintenance Program
To get executive buy-in for investing in a modern maintenance program, you need to speak their language: money. A well-crafted ROI calculation can transform your proposal from a "cost" to an "investment."
Step 1: Establish Your Baseline (The Cost of Doing Nothing)
First, you must quantify the cost of your current, likely reactive, maintenance strategy.
Total Current Maintenance Cost = (Downtime Costs) + (Labor Costs) + (Parts Costs) + (Contractor Costs) + (Excess Energy Costs)
- Downtime Cost: This is often the biggest and most overlooked number.
- Downtime Cost per Hour = Lost Revenue per Hour + Lost Productivity Costs
- Calculate this for your most critical assets.
- Labor Costs: Include straight time, overtime, and benefits for your maintenance staff.
- Parts Costs: Include expedited shipping fees for emergency parts.
- Excess Energy Costs: If possible, benchmark your building's energy use against similar facilities to estimate waste.
Step 2: Project Savings from a Proactive Approach
Using industry benchmarks, project the potential savings. Be conservative with your estimates.
- Reduced Unplanned Downtime: A move to a proactive strategy can realistically reduce unplanned downtime by 50-80%.
- Reduced Reactive Labor: Shifting work from reactive (high overtime) to planned (straight time) can cut labor costs by 20-30%.
- Increased Asset Lifespan: Well-maintained assets last longer. A 15-25% increase in asset life defers major capital expenditures.
- Energy Savings: A tuned HVAC and building system can yield 10-20% in energy savings.
- Improved Productivity: Technicians with clear, planned work orders and available parts can see "wrench time" (the time spent actually working on an asset) increase from a typical 25% to over 40%.
For more detailed benchmarks, resources like Reliabilityweb offer a wealth of data on the financial benefits of reliability-centered maintenance.
Step 3: Calculate the ROI
ROI (%) = [ (Total Projected Annual Savings - Annual Cost of New Program) / Annual Cost of New Program ] * 100
- Annual Cost of New Program: This includes CMMS subscription fees, sensor costs, and training.
Hypothetical Example:
- Baseline Annual Cost (Downtime, Labor, etc.): $1,000,000
- Projected Annual Savings (30% reduction): $300,000
- Annual Cost of New Program (CMMS, Sensors, Training): $50,000
- Net Gain: $300,000 - $50,000 = $250,000
- ROI: ($250,000 / $50,000) * 100 = 500%
A 500% ROI is a number that gets any executive's attention. It reframes the conversation from "Can we afford to do this?" to "Can we afford not to do this?"
Implementing a World-Class Building Maintenance Program: A 5-Step Roadmap
Transforming your maintenance function is a journey, not an overnight switch. Follow this structured roadmap for a successful implementation.
Step 1: Secure Executive Buy-In
Start here. Use the ROI calculation and strategic arguments we've discussed. Frame the initiative not as a maintenance project, but as a business optimization project. Highlight the benefits that matter to the C-suite: risk reduction, profitability, and competitive advantage.
Step 2: Conduct a Comprehensive Asset Audit
You need a clean, accurate foundation. Go through your facility and document every single maintainable asset. Capture its name, location, manufacturer, model number, and serial number. Most importantly, perform the criticality analysis we discussed earlier. This audit will be the backbone of your entire program, populating the asset management module of your CMMS.
Step 3: Choose Your Strategy and Technology
Using your criticality analysis, assign a primary maintenance strategy to each asset.
- Critical Assets (e.g., main chiller, primary air compressor): Predictive or Condition-Based Maintenance.
- Important Assets (e.g., secondary pumps, exhaust fans): Preventive Maintenance.
- Non-Critical Assets (e.g., lighting, small appliances): Reactive Maintenance.
Select a CMMS and any necessary sensor technology that aligns with this strategy and can scale with your needs.
Step 4: Develop and Document Standard Operating Procedures (SOPs)
For your program to be repeatable and scalable, it must be documented. Create clear SOPs for your key maintenance tasks, especially PMs and safety procedures like Lockout/Tagout. This ensures consistency regardless of which technician performs the work. Adhering to international standards for asset management, such as the ISO 55000 series, provides a globally recognized framework for excellence.
Step 5: Train, Launch, and Continuously Improve (The Kaizen Approach)
Technology and processes are useless if your team doesn't know how to use them. Invest in comprehensive training for your technicians, supervisors, and anyone else interacting with the new system.
Once you launch, the work isn't over. Adopt a mindset of Kaizen, or continuous improvement. Regularly review your KPIs. Is your MTBF increasing? Is your PM compliance at 95% or better? Is your maintenance backlog shrinking? Use the data from your CMMS to identify bottlenecks, refine your PM frequencies, and constantly optimize your strategy.
Conclusion: Your Facility's Future is Proactive
The landscape of building maintenance has irrevocably changed. The old, reactive model is a recipe for escalating costs, unpredictable failures, and strategic disadvantage.
The future belongs to those who embrace a proactive, data-driven, and strategic approach to managing their physical assets. By blending reactive, preventive, condition-based, and predictive strategies—all powered by a modern technology stack—you can transform your maintenance department from a cost center into a formidable source of value.
This transformation reduces risk, enhances safety, slashes operational costs, and extends the life of your most critical assets. It turns your building from a collection of parts that break into a finely tuned system that performs. Stop managing breakdowns and start engineering reliability. The journey begins now.
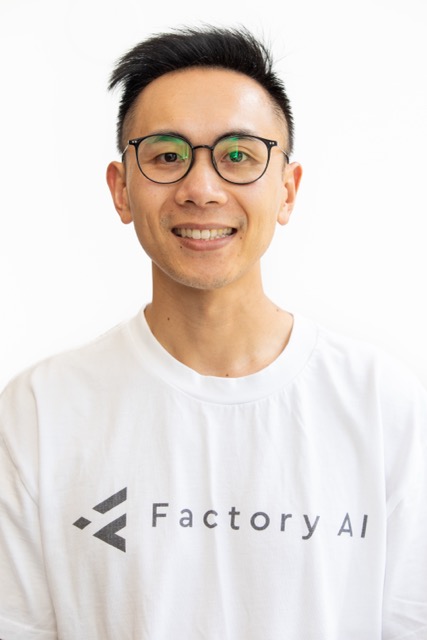