Beyond Wrenches and Work Orders: Building the High-Performance Maintenance Team of 2025
Jul 16, 2025
maintenance team
The clanging alarm of a critical asset failure at 2 AM. The frantic scramble for parts. The cascading production delays. For too long, this has been the defining image of a maintenance department—a reactive, high-stress unit perpetually caught in a cycle of breakdown and repair. They were the firefighters, the fix-it crew, a necessary but often overlooked cost center.
But in 2025, that image is not just outdated; it's a liability.
The industrial landscape has fundamentally shifted. Industry 4.0 isn't a buzzword anymore; it's the operational reality. In this new era of interconnected devices, artificial intelligence, and data-driven decision-making, the most successful organizations have recognized a powerful truth: the maintenance team is no longer a cost center. It is a strategic value driver, a hub of innovation, and the frontline champion of your most critical business goal: reliability.
Welcome to the age of the High-Performance Reliability Team. This isn't just a new name for the same department. It's a complete paradigm shift in mindset, structure, skills, and purpose. This guide is your comprehensive blueprint for moving beyond the reactive "fix-it" model and building a modern maintenance team that actively boosts your bottom line, enhances safety, and secures your competitive edge.
The Evolution of the Maintenance Team: From Firefighters to Reliability Champions
To build the team of the future, we must first understand its past. The journey of the maintenance team mirrors the evolution of industrial technology itself, moving from simple reaction to complex prediction and strategic optimization.
The Reactive Era: The "Fix-It" Crew
This is the classic, and unfortunately still common, model. The philosophy is simple: "If it ain't broke, don't fix it." The team’s entire existence revolves around responding to failures after they occur.
- Characteristics: Dominated by emergency work orders, minimal planning, high levels of overtime, and a constant sense of chaos.
- Metrics of Failure: High Mean Time To Repair (MTTR) because every job is an unplanned scramble. Low Mean Time Between Failures (MTBF) because underlying issues are never addressed.
- Business Impact: Unpredictable production schedules, significant downtime costs, higher safety risks, and rapid burnout of skilled technicians. This model treats maintenance as a pure expense to be minimized, rather than an investment.
The Proactive Shift: The Preventive Planners
The first major leap forward was the adoption of Preventive Maintenance (PM). The philosophy shifted to: "Fix it before it breaks." This involved performing routine maintenance tasks (lubrication, inspections, parts replacement) on a time-based or usage-based schedule.
- Characteristics: Introduction of scheduled work, the first appearance of maintenance planners, and the use of a Computerized Maintenance Management System (CMMS) to track schedules.
- Improvement: This model brought a degree of order and predictability. It successfully prevented many common failure modes.
- Limitations: PM is often inefficient. It can lead to over-maintenance (replacing parts that are still perfectly good) or under-maintenance (a part failing before its scheduled replacement). It's a one-size-fits-all approach that doesn't account for the actual operating condition of the asset.
The Predictive Leap: The Data-Driven Analysts
The next evolution was powered by technology. Predictive Maintenance (PdM) changed the philosophy to: "Fix it when it shows signs of breaking." Instead of relying on a calendar, teams began using condition-monitoring tools to listen to what their assets were telling them.
- Characteristics: Use of technologies like vibration analysis, infrared thermography, oil analysis, and ultrasonic testing. The team becomes more analytical, interpreting data to predict failures.
- Improvement: Maintenance is performed only when necessary, maximizing asset life and minimizing maintenance costs. This is a huge step towards efficiency.
- The Challenge: PdM requires a higher skill level, investment in technology, and a robust system for managing and analyzing the data.
The Reliability-Centered Future: The Strategic Partners of 2025
This is where we are today. The most advanced organizations have embraced a holistic, strategic approach known as Reliability-Centered Maintenance (RCM). The philosophy is profound: "Understand why things fail and systematically eliminate the causes of failure."
A high-performance reliability team doesn't just fix or predict breakdowns; it engineers them out of existence. This team is deeply integrated with operations, engineering, and procurement. They are data scientists, problem solvers, and strategic partners in the business's success. As defined by experts at Reliabilityweb, RCM is a corporate-level strategy for preserving asset function. This team owns asset performance and drives profitability by maximizing uptime, throughput, and safety.
Blueprint for a High-Performance Maintenance Team Structure in 2025
An evolved philosophy requires an evolved structure. The old model of a manager and a group of generalist technicians is no longer sufficient. A modern reliability team is a carefully orchestrated ensemble of specialized roles, each contributing a unique skill set.
Foundational Roles: The Bedrock of Execution
These are the hands-on roles that form the core of the team's ability to execute work safely and efficiently.
Maintenance Technicians (Specialists, not Generalists)
In 2025, the "wrench-turner" is a highly skilled, tech-savvy professional. The demand is for multi-skilled technicians who are as comfortable with a tablet and diagnostic software as they are with a torque wrench.
- Responsibilities:
- Execute planned and scheduled work with precision, following detailed procedures.
- Perform complex troubleshooting on mechanical, electrical, and instrumentation systems.
- Gather high-quality data from PdM tools (e.g., taking vibration readings, thermal images).
- Provide detailed feedback on work orders, suggesting improvements to job plans and procedures.
- Participate in Root Cause Analysis (RCA) sessions, providing invaluable frontline insight.
- The Modern Skillset: Beyond core mechanical/electrical skills, they need data literacy, critical thinking, and strong communication skills. They are the eyes and ears of the entire reliability program.
Maintenance Supervisor / Team Lead
The modern supervisor is a coach and a leader, not a taskmaster. Their primary function is to empower their team to succeed.
- Responsibilities:
- Ensure absolute safety compliance on every job.
- Manage the day-to-day execution of the weekly schedule.
- Remove roadblocks for technicians (e.g., clarifying procedures, resolving parts issues).
- Conduct performance coaching and support individual development plans.
- Champion the reliability culture on the floor, celebrating proactive "finds" and successful PMs.
- Act as the key communication link between the technicians and the planning/engineering functions.
Strategic Roles: The Brains of the Operation
These roles focus on the "what," "why," "how," and "when" of maintenance work. They transform the team from reactive to proactive.
Maintenance Planner
The Planner is arguably one of the most critical roles for achieving maintenance efficiency. A great planner can double the "wrench time" of a technician by ensuring every second of their day is spent on value-added work.
- Core Duty: To create high-quality, detailed work packages for future work. The Planner focuses on the "what" and "how."
- Detailed Responsibilities:
- Scope the Job: Visit the job site, assess the requirements, and create a detailed sequence of tasks.
- Identify Resources: List all necessary parts, tools, and special equipment.
- Procure Materials: Create purchase requisitions for non-stock parts and confirm availability of all materials before the job is scheduled.
- Develop Procedures: Write or attach detailed work procedures, safety checklists (LOTO), and technical drawings.
- Estimate Labor: Accurately estimate the hours and number of technicians required for each craft.
- Coordinate: Arrange for any necessary support from other departments (e.g., production shutdown, scaffolding, cranes).
- The Goal: A planner's work is done when a "ready-to-schedule" work package is handed off, containing everything a technician needs to execute the job without delay or interruption. This entire process is managed within a robust CMMS software that acts as the central repository for all planning information.
Maintenance Scheduler
While often combined with the Planner role in smaller organizations, separating them creates a powerful focus. If the Planner handles the "what" and "how," the Scheduler owns the "when" and "who."
- Core Duty: To build and manage the weekly maintenance schedule in tight coordination with production.
- Responsibilities:
- Manage the backlog of "ready-to-schedule" work packages created by the Planner.
- Negotiate equipment availability windows with operations leaders.
- Allocate technicians to jobs based on skill set and availability.
- Build the weekly schedule, balancing PMs, PdM work, and corrective jobs.
- Publish the schedule and track its compliance, analyzing reasons for any deviations.
Reliability Engineer: The Linchpin of Proactivity
This is the role that truly separates a traditional maintenance team from a high-performance reliability team. The Reliability Engineer is a data-driven strategist focused on eliminating failure.
- Core Duty: To improve asset reliability and reduce maintenance costs through analysis and engineering solutions.
- Key Responsibilities:
- Bad Actor Analysis: Analyze maintenance data to identify the assets causing the most downtime and cost.
- Root Cause Analysis (RCA): Lead formal investigations into significant failures to understand the true physical, human, and latent root causes.
- PM/PdM Optimization: Use data and analysis (like Failure Mode and Effects Analysis - FMEA) to ensure the right maintenance is being done on the right assets at the right frequency. Eliminate non-value-added tasks.
- Manage PdM Program: Oversee the condition-monitoring technologies, set alarm limits, and interpret complex data to generate predictive work orders.
- Lifecycle Asset Management: Provide input on new equipment purchases to ensure reliability and maintainability are considered from the design phase.
- Continuous Improvement: Champion projects to redesign components, improve operating procedures, or upgrade materials to prevent failures from recurring.
Supporting & Integrated Roles
These roles provide the critical infrastructure and support that enable the entire team to function at a high level.
MRO Storeroom Manager / Coordinator
A disorganized storeroom can bring the most well-planned maintenance operation to its knees. This role is about strategic materials management, not just handing out parts.
- Responsibilities:
- Optimize inventory levels to balance carrying costs against the risk of stockouts.
- Ensure critical spares are identified, preserved, and readily available.
- Implement robust processes for receiving, issuing, and cycle counting.
- Organize the storeroom for efficiency (e.g., 5S, kitting).
- Manage vendor relationships and performance.
- Strategic Impact: Excellent inventory management directly reduces maintenance delays and lowers overall MRO (Maintenance, Repair, and Operations) spend.
Data Analyst / CMMS Administrator
In 2025, maintenance data is a goldmine. This role is the miner. As teams rely more on AI and advanced analytics, the quality and integrity of the underlying data become paramount.
- Responsibilities:
- Ensure data integrity within the CMMS (e.g., correct asset hierarchy, failure codes, work order completion data).
- Develop and maintain dashboards for key performance indicators (KPIs).
- Generate reports for planners, supervisors, and reliability engineers.
- Train team members on how to use the CMMS and other technologies effectively.
- Support the Reliability Engineer with data extraction and analysis for complex projects.
Building Your Team: From Recruitment to Retention
Having the right structure is only half the battle. You need to populate it with the right people and create an environment where they can thrive.
Hiring for the Future: Skills and Mindset Over Experience Alone
When recruiting for a modern maintenance team, look beyond a simple list of past jobs.
- Technical Aptitude & Multi-Skilling: Look for candidates with a foundation in one discipline (mechanical/electrical) but a demonstrated ability and curiosity to learn others.
- Data Literacy: Are they comfortable using a smartphone or tablet? Can they interpret a simple chart? In an interview, show them a sample work order on a mobile device and ask them to walk you through it.
- Problem-Solving Mindset: Use behavioral questions. Instead of "Can you troubleshoot a pump?" ask, "Tell me about a time a pump failed repeatedly. What steps did you take to find the real cause?" You're looking for a thought process that goes beyond the immediate fix.
- Soft Skills: Communication, teamwork, and a collaborative spirit are non-negotiable. A brilliant but abrasive technician can poison a team's culture and hinder the collaborative work required for reliability.
The Onboarding Blueprint: Setting New Hires Up for Success
A new hire's first 90 days are critical. A structured onboarding process ensures they become a contributing member of the team quickly and safely.
- Week 1: Culture and Safety. Immerse them in your safety-first culture. This includes LOTO procedures, permit-to-work systems, and hazard identification. Introduce them to the team and the facility.
- Weeks 2-4: Systems and Technology. Provide dedicated training on your work order software and any mobile devices they'll be using. Don't just show them how to close a work order; explain why accurate data entry is critical for the Reliability Engineer.
- Days 30-90: Mentorship and Application. Pair the new hire with a senior technician or mentor. This allows them to apply their skills in a supervised environment, learn tribal knowledge, and build relationships. Set clear performance expectations and check in regularly.
Continuous Development: The Key to Retention and Performance
The best people want to grow. Investing in your team's development is the single most effective retention strategy.
- Create a Skills Matrix: Map out the required skills for your facility (e.g., pump alignment, VFD troubleshooting, welding) and assess each technician against it. This visually identifies gaps and creates a clear roadmap for training.
- Invest in Certifications: Support technicians and engineers in achieving recognized certifications like Certified Maintenance & Reliability Professional (CMRP) or Certified Reliability Leader (CRL). This professionalizes their role and brings new knowledge into the organization.
- Cross-Training Programs: Intentionally schedule technicians to work with team members from other disciplines. An electrician who understands the mechanical impact of a motor failure is infinitely more valuable.
- Leadership Development: Identify potential future leaders and invest in their soft skills. Send a promising supervisor to a course on coaching, conflict resolution, or financial basics.
The Modern Maintenance Toolkit: Empowering Your Team with Technology
A high-performance team needs high-performance tools. In 2025, technology is the great enabler, amplifying the skills and effectiveness of every role on the team.
The Central Nervous System: The CMMS/EAM
A modern, cloud-based, mobile-first CMMS or Enterprise Asset Management (EAM) system is the non-negotiable foundation. It's the single source of truth for assets, work orders, inventory, and performance data. Old, clunky, server-based systems are a relic. Today's teams need instant access to information in the field.
Seeing the Future: Predictive Maintenance (PdM) & AI
PdM tools are the stethoscopes of the maintenance team, allowing them to diagnose problems before they become catastrophic failures.
- Vibration Analysis: Wireless sensors attached to rotating equipment like motors and pumps detect subtle changes in vibration that indicate bearing wear, misalignment, or imbalance.
- Infrared Thermography: Thermal cameras spot overheating electrical connections, faulty motor windings, or refractory breakdown—problems invisible to the naked eye.
- Ultrasonic Testing: Detects high-frequency sounds associated with compressed air leaks, steam trap failures, and early-stage bearing faults.
- Oil Analysis: Lab analysis of lubricant samples can reveal machine wear, contamination, and fluid degradation, much like a blood test for your equipment.
The next frontier is layering artificial intelligence on top of this data. Powerful algorithms can analyze millions of data points from multiple sources, identifying complex patterns that no human could ever detect. This is the power of AI predictive maintenance, which moves from predicting a failure to prescribing a specific action to prevent it.
Mobility and Connectivity: The Technician's Best Friend
Untether your technicians from the desk and the paper file.
- Tablets and Smartphones: Equipped with a mobile CMMS, a technician can access asset history, view digital schematics, order parts, and close out work orders right at the job site. This dramatically improves data accuracy and wrench time.
- Augmented Reality (AR): While still emerging, AR is gaining traction. A technician wearing smart glasses can see a digital overlay of instructions, schematics, or key data points on the equipment they are working on. It also allows a remote expert to see what the technician sees and guide them through a complex repair in real-time.
Measuring Success: The KPIs That Truly Matter
"What gets measured gets improved." But a high-performance team focuses on a balanced set of metrics that tell the whole story of reliability, not just activity. These KPIs should be used for learning and improvement, not as a stick to punish people.
Lagging Indicators: Measuring Past Performance
These metrics tell you how you've done. They are the result of your processes and actions.
- Mean Time Between Failures (MTBF):
- Formula:
Total Operational Uptime / Number of Breakdowns
- What it means: A measure of asset reliability. A higher MTBF means your assets are failing less often. This is the primary KPI for the Reliability Engineer.
- Formula:
- Mean Time To Repair (MTTR):
- Formula:
Total Maintenance Downtime / Number of Breakdowns
- What it means: A measure of maintainability and efficiency. A lower MTTR means your team can diagnose and repair failures faster. This is a key KPI for Planners and Supervisors.
- Formula:
- Overall Equipment Effectiveness (OEE):
- Formula:
Availability x Performance x Quality
- What it means: The gold standard for measuring manufacturing productivity. As explained by authorities like iSixSigma, it's a holistic metric that shows how maintenance, operations, and quality are all interconnected. Maintenance directly owns the "Availability" component.
- Formula:
Leading Indicators: Predicting Future Success
These metrics measure the health of your maintenance processes. Excelling at these will lead to better lagging indicators.
- Preventive Maintenance (PM) Compliance:
- Formula:
(Completed PMs / Scheduled PMs) x 100
- What it means: Measures discipline and proactivity. A score consistently above 90% shows the team is executing its proactive strategy.
- Formula:
- Schedule Compliance:
- Formula:
(Completed Scheduled Work Hours / Total Scheduled Hours) x 100
- What it means: The single best measure of a Planning and Scheduling function's effectiveness. A high score (85%+) means the team is working on pre-planned, efficient jobs rather than being diverted by reactive work.
- Formula:
- Work Order Backlog (in weeks):
- What it means: A measure of the total planned and ready-to-schedule work available. A healthy backlog of 2-4 weeks is a good sign; it means the Planner has a good queue of work ready to go. A backlog of zero means you're living hand-to-mouth, and a backlog of 12 weeks means you're not getting enough work done.
Case Study: Transforming a Reactive Team into a Reliability Powerhouse
Company: "Astra Components," a mid-sized automotive parts manufacturer.
The Problem (Before): Astra's stamping press line was the heart of their plant but also their biggest headache. Unplanned downtime was rampant, averaging 20 hours per month. The maintenance team, led by a long-tenured but overwhelmed manager, was in constant firefighting mode. MTBF was low, MTTR was high, and overtime costs were through the roof. Technician morale was at an all-time low; they felt like they could never get ahead.
The Transformation (The Process): A new Plant Manager, with a background in reliability, initiated a complete overhaul.
- Leadership & Structure: They hired a dedicated Reliability Engineer and formally split the Planner and Scheduler roles. The existing manager was moved into the Supervisor role, where his hands-on knowledge could be leveraged for coaching.
- Process & Technology: They implemented a modern, mobile-first CMMS. The first major project was for the Planner and Reliability Engineer to build a proper asset hierarchy and bill of materials for the entire press line.
- PM Optimization: The Reliability Engineer conducted an FMEA on the press line's most common failures. They discovered that 30% of their PM tasks were non-value-added and eliminated them. They also identified the critical hydraulic pumps as "bad actors."
- PdM Pilot Program: They installed wireless vibration and temperature sensors on the hydraulic pumps. This was a targeted investment in a solution for predictive maintenance on motors and pumps. The data was fed directly into the new CMMS.
- Team Empowerment: All technicians were trained on the new mobile CMMS and on basic RCA principles. The weekly schedule and key KPIs were displayed on a large monitor in the maintenance shop, creating transparency and ownership.
The Results (After 12 Months):
- MTBF for the press line increased by 300% as predictive and optimized PM work caught issues early.
- MTTR decreased by 50%. When failures did occur, the team had planned work packages and kitted parts ready, thanks to the Planner.
- Unplanned Downtime dropped from 20 hours/month to less than 4 hours/month.
- Maintenance Costs were reduced by 18%, primarily through reduced overtime and eliminating emergency parts freight.
- Technician Morale soared. The team was no longer fighting fires; they were preventing them. They felt like skilled professionals contributing to the plant's success.
Your Journey to a High-Performance Team Starts Now
Building the maintenance team of 2025 is not a quick fix; it's a strategic journey. It requires a fundamental shift in how your organization views maintenance—not as a necessary evil, but as a core driver of operational excellence and profitability.
The blueprint is clear:
- Evolve your philosophy from reactive to reliability-centered.
- Build a modern structure with specialized strategic and foundational roles.
- Hire and develop people with a blend of technical, analytical, and soft skills.
- Empower your team with the right technology, from a mobile CMMS to AI-driven predictive tools.
- Measure what matters with a balanced scorecard of leading and lagging KPIs.
The world of firefighting maintenance is fading. The future belongs to the data-driven, proactive, and strategic High-Performance Reliability Team. Start building yours today.
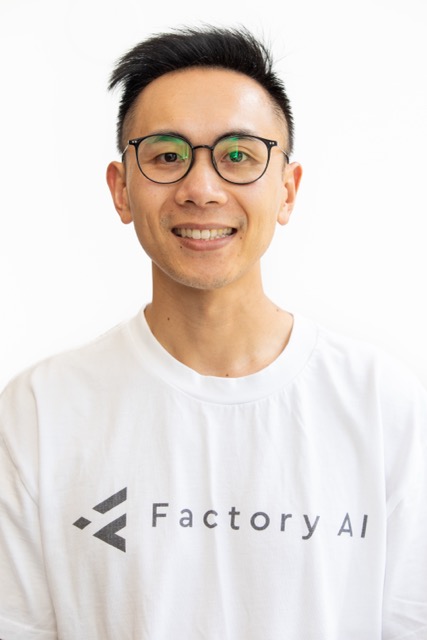