Beyond the Breakdown: The Strategic Maintenance Manager's Playbook for Air Compressor Repair & Reliability in 2025
Jul 18, 2025
air compressor repair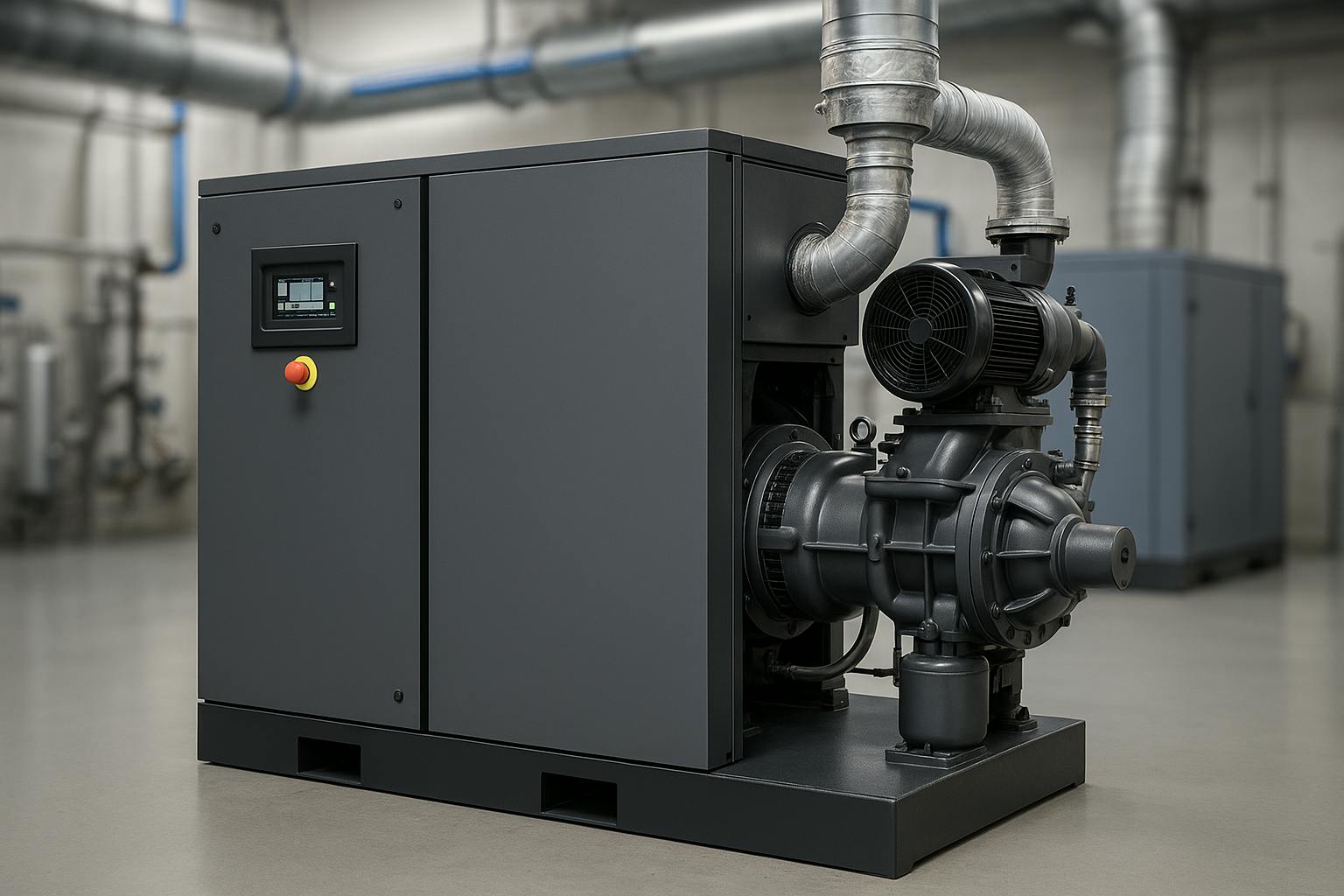
An industrial air compressor isn't just another piece of equipment on the factory floor; it's the heart of your operation, pumping the lifeblood of compressed air that powers tools, actuates cylinders, and drives production. When that heart stops, everything grinds to a halt. The sudden silence is deafening, quickly replaced by the rising panic of calculating downtime costs in real-time.
If you're reading this, you likely fall into one of two camps. You might be in the midst of a crisis, frantically searching for an "air compressor repair" guide to solve an immediate, production-stopping failure. Or, you're a strategic maintenance manager or facility operator looking to get ahead of the curve, seeking to understand how to prevent that crisis from ever happening again.
This is not another generic, five-step troubleshooting list. This is a comprehensive playbook for the modern maintenance leader. We'll address the immediate triage needed during a breakdown, but more importantly, we'll dive deep into the strategies that transform air compressor maintenance from a reactive, unpredictable cost center into a proactive, data-driven function that adds tangible value to the bottom line. We will explore advanced diagnostics, the critical repair-or-replace decision, and how to leverage the technology of 2025 to build a truly resilient compressed air system.
The True Cost of Air Compressor Downtime: Beyond the Repair Bill
A failed compressor costs far more than the sum of its replacement parts and the technician's labor. For a strategic manager, understanding the full financial ripple effect is crucial for justifying investments in better maintenance practices. The true cost of downtime (TDC) is a multi-layered calculation that reveals the profound impact of an unreliable system.
Calculating the Full Financial Impact
When a central compressor fails, the direct repair cost is often the smallest part of the financial damage. A comprehensive analysis must include:
- Lost Production Value: This is the most significant cost. If your plant generates $50,000 in revenue per hour and a compressor failure halts production for four hours, that's a direct $200,000 revenue loss.
- Idle Labor Costs: Your operators, technicians, and assembly line workers are still on the clock, even if their tools are silent. A team of 50 employees with an average loaded labor rate of $45/hour costs you $2,250 every hour they stand idle.
- Expedited Freight & Overtime: To catch up on lost production and meet customer deadlines, you'll likely incur significant costs for overtime labor and expedited shipping for finished goods.
- Brand and Reputation Damage: Failing to meet a delivery deadline for a key customer can have long-term consequences that are harder to quantify but no less damaging.
The Hidden Costs: Energy Inefficiency and Waste
Even when it's "working," a poorly maintained compressor is an energy vampire. Compressed air is one of the most expensive utilities in a plant, often referred to as the "fourth utility." According to the Department of Energy, compressed air systems can account for 10% to 30% of a facility's total electricity consumption.
A system plagued by issues like air leaks, clogged filters, or improper pressure settings works harder than necessary, consuming excess energy every minute it runs. An unaddressed quarter-inch air leak at 100 psi can cost over $12,000 per year in wasted electricity. A strategic approach to compressor repair isn't just about uptime; it's about optimizing one of your largest operational expenses.
Safety and Compliance Risks
Beyond the financial costs, a failing compressor poses significant safety risks. A catastrophic failure of a pressure vessel can be explosive. Oil carryover can create slick, hazardous floors. Overheating components present a fire risk. Adhering to pressure vessel inspection standards, like those from ASME (American Society of Mechanical Engineers), is not just a best practice—it's a legal requirement in many jurisdictions. Neglecting maintenance can lead to failed inspections, fines, and, in the worst-case scenario, preventable accidents.
Immediate Triage: An Industrial Air Compressor Troubleshooting Guide
When a compressor goes down, you need to act fast. This guide is designed for in-house maintenance teams to quickly diagnose the most common failure modes in industrial units, particularly rotary screw compressors.
Safety First: Before performing any checks, follow proper Lockout/Tagout (LOTO) procedures. Disconnect and lock the main power supply. Safely depressurize the system by opening a downstream valve.
Problem: Compressor Fails to Start
This is the most common and often the simplest issue to resolve.
- Possible Causes & Troubleshooting Steps:
- No Power: Start with the obvious. Check if the circuit breaker has tripped or a fuse has blown. Verify voltage at the machine's disconnect switch.
- Emergency Stop Engaged: Check if an E-stop button on the machine or a remote panel has been pressed.
- Controller Fault: Modern compressors have sophisticated controllers. Check the display for any active fault codes (e.g., "High Sump Temperature," "Low Oil Level"). Consult the manual for the specific code.
- Low Oil Level Shutdown: Most compressors have a sensor that prevents startup if the oil level in the sump is too low. Visually inspect the sight glass and top off with the manufacturer-specified oil if needed.
- High-Pressure Shutdown: The compressor won't start if the system pressure is already above the cut-in pressure setting. This could indicate a faulty pressure switch or a check valve that is allowing backflow from the air receiver.
- Motor or Starter Failure: If you hear a humming or buzzing sound but the motor doesn't turn, you may have a failed starter contactor, capacitor (on smaller units), or a seized motor/airend.
Problem: Low or No Air Pressure
The compressor is running, but you're not getting the pressure or flow (CFM) you need.
- Possible Causes & Troubleshooting Steps:
- Massive Air Leaks: The compressor may be producing air, but it's escaping before it can be used. A system-wide leak survey is the first step.
- Clogged Intake Filter: A dirty air filter restricts the amount of air the compressor can draw in. This is a simple but often overlooked cause. Inspect and replace if necessary.
- Inlet Valve Malfunction: The inlet or "load/unload" valve may be stuck in a partially closed or "unloaded" position, preventing the compressor from building pressure. Check for mechanical binding or issues with the controlling solenoid.
- Worn Seals (Rotary Screw) or Rings (Reciprocating): Internal wear and tear can reduce the compressor's efficiency. This is a more serious issue that often requires a partial or full airend rebuild.
- Belt Slippage: On belt-driven units, loose or worn belts can slip, preventing the motor from effectively turning the compressor pump or airend at the required RPM.
Problem: Excessive Oil in the Compressed Air (Oil Carryover)
Oil in your airlines can damage pneumatic tools, contaminate processes, and ruin product finishes.
- Possible Causes & Troubleshooting Steps:
- Failed Air-Oil Separator: This is the most common culprit. The separator element is a consumable filter that coalesces oil mist and returns it to the sump. Over time, it becomes saturated or can rupture. It must be replaced as part of routine maintenance.
- Overfilled Oil Sump: Too much oil in the reservoir can overwhelm the separator. Drain the oil to the correct level indicated on the sight glass.
- Scavenge Line Clogged: The scavenge line is a small tube that returns the collected oil from the separator back to the sump. If it's clogged, the oil has nowhere to go but downstream.
- Excessive Operating Temperature: High heat can cause the oil to break down and vaporize, making it much harder for the separator to capture. Address the root cause of the overheating.
Problem: Compressor Overheating and Shutting Down
High-temperature shutdowns are a clear warning sign that needs immediate attention to prevent catastrophic damage.
- Possible Causes & Troubleshooting Steps:
- Poor Ventilation: The compressor needs to breathe. Ensure there is adequate clearance around the unit (typically 3-5 feet) and that the room's ambient temperature is within the manufacturer's specified limits.
- Clogged Oil Cooler / Aftercooler: The radiator-like coolers are magnets for dust and debris. Use compressed air (at low pressure) to blow out the fins. For heavy, oily buildup, a chemical cleaning may be necessary.
- Low Oil Level: Oil is not just a lubricant; it's the primary cooling medium in a rotary screw compressor. Low oil means less capacity to remove heat.
- Incorrect Oil Type: Using the wrong oil (e.g., a non-synthetic oil in a high-duty-cycle machine) can lead to premature thermal breakdown and poor heat transfer.
- Thermostatic Valve Failure: This valve controls the flow of oil to the cooler. If it fails in the closed position, the oil will never be cooled, leading to a rapid temperature rise.
From Reactive to Proactive: Building a World-Class Compressor Maintenance Strategy
Fixing a broken compressor is reactive. A world-class maintenance organization makes breakdowns the rare exception, not the rule. This requires a strategic shift from a "fix-it-when-it-breaks" mentality to a structured, multi-tiered maintenance approach.
Step 1: Foundational Preventive Maintenance (PM)
Preventive maintenance (PM) is the bedrock of reliability. It involves performing scheduled tasks to prevent the most common causes of failure. A robust PM program is non-negotiable for any critical asset. Automating the scheduling, execution, and documentation of these tasks is simple with a modern CMMS for pneumatic systems, which eliminates guesswork and ensures compliance.
Comprehensive Air Compressor PM Checklist:
-
Daily Tasks:
- Check and log the sump oil level.
- Check and log the discharge air pressure and temperature on the controller.
- Drain condensate from air receivers and drip legs (if using manual drains).
- Listen for any unusual noises or vibrations.
-
Weekly Tasks:
- Clean the intake air filter. In very dirty environments, this may need to be done daily.
- Wipe down the exterior of the unit and clean the cooler fins with compressed air.
- Check automatic condensate drains for proper operation.
-
Monthly Tasks:
- Check drive belts for proper tension and signs of cracking or wear.
- Perform an ultrasonic leak detection survey around the compressor and in the main distribution lines.
- Check all safety relief valves to ensure they are not stuck.
-
Quarterly / 2,000-Hour Tasks:
- Take an oil sample for analysis (see Predictive Maintenance section).
- Change the oil and oil filter (or follow manufacturer's specific interval).
-
Annual / 8,000-Hour Tasks:
- Replace the air-oil separator element.
- Replace the intake air filter element.
- Replace all drive belts.
- Have a certified technician inspect and test all safety controls, calibrate sensors, and lubricate motor bearings.
Step 2: Advanced Diagnostics & Root Cause Failure Analysis (RCFA)
When a failure does occur, simply replacing the broken part is a missed opportunity. The goal of Root Cause Failure Analysis (RCFA) is to dig deeper and understand the why behind the failure to prevent it from recurring.
For example, a motor bearing fails.
- The Reactive Fix: Replace the bearing.
- The RCFA Approach: Ask "Why did the bearing fail?"
- Why? It was overloaded.
- Why? The drive belts were over-tensioned.
- Why? The PM procedure for belt tensioning was unclear.
- Why? The technician who wrote it was not properly trained on the new tensioning tool.
- Why? The company lacks a formal training and procedure validation process.
The RCFA process, using methods like the 5 Whys or Fishbone Diagrams, moves the solution from "buy a new bearing" to "improve our training and PM procedures," a much more valuable, long-term fix. For a deeper dive into structured problem-solving methodologies, resources from organizations like iSixSigma provide excellent frameworks.
Step 3: The Leap to Predictive Maintenance (PdM)
Predictive Maintenance (PdM) is the highest level of maintenance maturity. Instead of changing parts on a schedule (PM), you use condition-monitoring technologies to predict exactly when a component is likely to fail, allowing you to schedule repairs before a breakdown occurs. This maximizes component life, minimizes downtime, and optimizes labor. Implementing a robust predictive maintenance for air compressors strategy is the hallmark of a leading-edge operation in 2025.
Key PdM technologies for air compressors include:
- Vibration Analysis: Sensors mounted on the motor and airend detect subtle changes in vibration signatures that indicate developing faults like bearing wear, misalignment, imbalance, or gear tooth defects long before they become catastrophic.
- Oil Analysis: Just like a blood test for a human, a lab analysis of a compressor oil sample reveals a wealth of information about the machine's internal health. It can detect metal particles from wearing components, contamination from dirt or water, and chemical breakdown of the oil itself.
- Thermal Imaging: Using an infrared camera, technicians can quickly scan for "hot spots" on coolers, electrical connections, motor casings, and bearings, identifying areas of high resistance or insufficient cooling.
- Ultrasonic Analysis: High-frequency sound detectors are invaluable for finding costly compressed air leaks that are completely inaudible to the human ear. They can also be used to detect early-stage bearing faults and electrical arcing.
The Critical Decision: Repair vs. Replace Air Compressor Calculator
For a major failure, like a seized airend or a failed main motor, you face a critical decision with significant financial implications. Do you invest in a costly repair, or is it time to replace the entire unit? A purely emotional or gut-feel decision is a mistake. A data-driven approach is essential.
Key Factors in the Calculation
- Total Repair Cost: Get a firm quote for all parts, labor, and any necessary rental compressor costs during the downtime.
- Age and Reliability History: How old is the unit? Check your maintenance logs. Is this its first major failure, or is it one of a series of mounting problems? A 12-year-old compressor with recurring issues is a poor candidate for a major repair.
- Energy Efficiency of Old vs. New: This is often the deciding factor. A new, modern compressor—especially a Variable Speed Drive (VSD) model—can be 35% to 50% more energy-efficient than a decade-old, fixed-speed unit.
- Changes in Air Demand: Has your plant's air demand grown or become more variable? Your old compressor may now be undersized, or a fixed-speed unit may be highly inefficient for a fluctuating load profile. A new, properly sized VSD compressor can provide massive savings.
A Simplified Payback Calculation Framework
Let's run a sample scenario:
- Your Current Unit: 15-year-old, 100 HP fixed-speed compressor.
- The Failure: Seized airend. Repair cost is quoted at $18,000.
- The Replacement Option: A new 100 HP VSD compressor. Cost is $45,000.
Step 1: Calculate Annual Energy Cost of the OLD Unit.
100 HP * 0.746 kW/HP = 74.6 kW
- Assume it runs loaded 6,000 hours/year at an average 80% load:
74.6 kW * 0.80 * 6,000 hrs = 358,080 kWh
- At an electricity rate of $0.12/kWh:
358,080 kWh * $0.12/kWh =
$42,970/year
Step 2: Calculate Annual Energy Cost of the NEW VSD Unit.
- A new VSD can match the variable load precisely. Let's assume a conservative 30% energy savings.
$42,970 * 0.70 =
$30,079/year- Annual Energy Savings = $12,891
Step 3: Calculate the Payback Period.
Payback Period = (Cost of New Unit - Cost of Repair) / Annual Energy Savings
Payback Period = ($45,000 - $18,000) / $12,891
Payback Period = $27,000 / $12,891 =
2.1 years
In this scenario, by investing an additional $27,000 upfront, you get a brand new, reliable asset that pays for that extra investment in just over two years through energy savings alone. For most financial decision-makers, a payback period under three years is an excellent investment.
Optimizing Your Entire Compressed Air System: Beyond the Compressor
A perfectly maintained, highly efficient compressor can still waste enormous amounts of energy if the rest of the system—the "demand side"—is neglected. True optimization requires looking at the entire system, from the compressor intake to the point of use.
The War on Leaks: How to Reduce Compressed Air Energy Cost
Leaks are the single greatest source of wasted energy in most compressed air systems. The U.S. Department of Energy estimates that, on average, 20-30% of a compressor's output is lost to leaks. A formal leak management program is essential:
- Detect: Use an ultrasonic leak detector to survey the entire plant. Human hearing can't detect the high-frequency hiss of most leaks.
- Tag: When a leak is found, attach a numbered tag that details its location and estimated severity (CFM loss).
- Log: Enter the tagged leak into your work order system. A modern work order software integrated with your CMMS is perfect for this.
- Repair: Schedule and execute the repair. Most leaks occur at threaded fittings, quick-couplers, and old hoses and are simple to fix.
- Verify: After the repair, use the ultrasonic detector again to confirm the leak has been eliminated.
Right-Sizing Pressure and Storage
Many plants operate at a much higher pressure than necessary "just to be safe." This is incredibly wasteful. A common rule of thumb is that for every 2 PSI reduction in system pressure, energy consumption drops by approximately 1%. Conduct a system audit to find the minimum pressure required by your most sensitive equipment and set your compressor controls accordingly.
Additionally, adequate storage in the form of air receivers (tanks) is critical. Tanks act as a buffer, allowing the system to handle sudden, large demands without forcing the compressor to turn on or ramp up. This reduces cycling, saves energy, and lessens wear and tear on the compressor's motor and controls.
Leveraging Technology for Next-Generation Air Compressor Reliability
The future of maintenance is intelligent and interconnected. In 2025, leveraging technology is no longer optional for top-performing facilities.
The Central Nervous System: Your CMMS
A Computerized Maintenance Management System (CMMS) is the foundation. It's the single source of truth for your entire maintenance operation. For your compressed air system, a CMMS allows you to:
- Automate and track all PM schedules and work orders.
- Build a detailed asset history for every compressor, including all repairs, costs, and downtime.
- Manage spare parts inventory to ensure critical components like filters and separators are always in stock.
- Generate reports on Mean Time Between Failure (MTBF) and other KPIs to measure reliability improvements.
The Power of AI and Prescriptive Maintenance
The next evolution is here. While predictive maintenance tells you what will fail and when, prescriptive maintenance tells you why it will fail and what to do about it. By integrating real-time sensor data (vibration, temperature, pressure) with your CMMS asset history, AI algorithms can identify complex patterns that precede failure.
The system doesn't just send an alert saying, "Motor bearing #2 vibration is high." It sends a prescriptive work order: "Vibration data on Compressor C-101 indicates a 95% probability of an inner race bearing fault within the next 250 operating hours, likely caused by lubrication contamination detected in the last oil analysis. Recommend scheduling a bearing replacement and a full sump flush/refill using part #XYZ from inventory. Click here to approve the work order." This is the power of true prescriptive maintenance.
Conclusion: From Firefighter to Strategist
Managing industrial air compressor repair in 2025 is about a fundamental shift in mindset. It's about moving from being a reactive firefighter, constantly battling the consequences of failure, to becoming a proactive strategist, using data and technology to eliminate failure before it happens.
By understanding the true cost of downtime, implementing a tiered maintenance strategy from basic PMs to advanced PdM, making data-driven repair-or-replace decisions, and optimizing your entire compressed air system, you can transform this critical asset from a source of unpredictable costs and stress into a pillar of operational excellence and a tangible competitive advantage.
Ready to transform your air compressor maintenance from a liability to an asset? Explore how our AI-powered predictive maintenance platform can help you achieve unprecedented levels of reliability and efficiency.
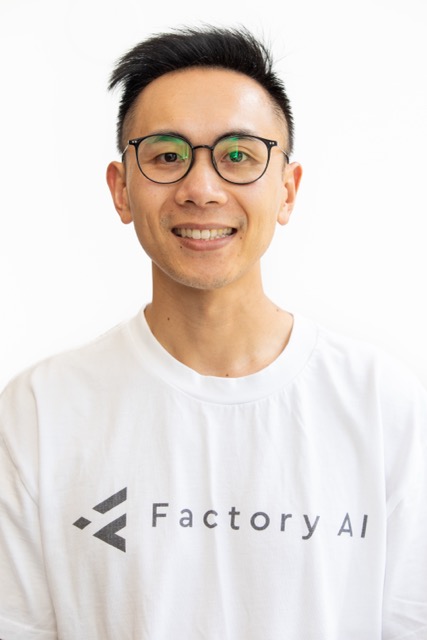